TechnologyApril 25, 2024
HART solution connects plant floor data to higher level systems
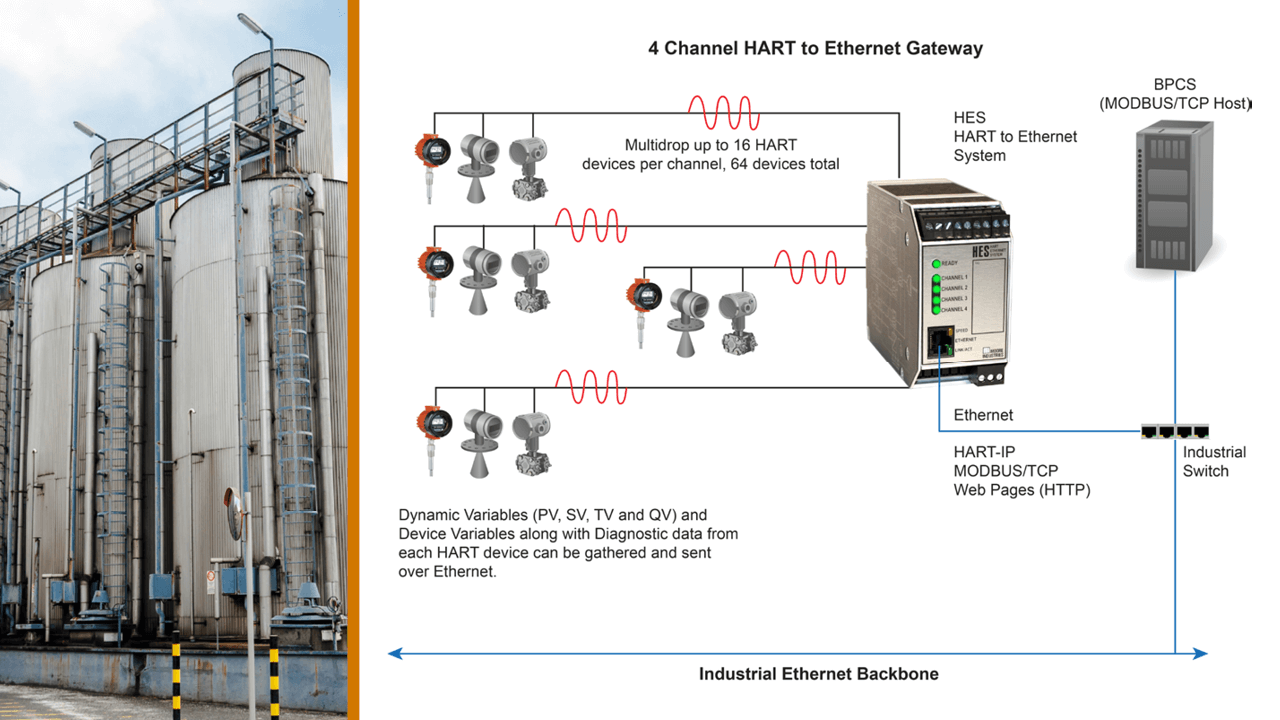
HART - The cost-effective solution to get critical plant floor data up to higher-level information systems.
Over the last few decades, the emergence of industrial Ethernet and wireless networks in process manufacturing plants and automation facilities has made data interchange within a facility and even across global corporate networks more routine. The several information hierarchy levels specified in the ISA 95 model for process data sharing within a manufacturing facility have begun to merge. In previous years, data and information that needed to be exchanged between the lowest plant floor levels 0-2 and the upper ERP (Enterprise Resource Planning) level 4 required expensive MES (Manufacturing Execution Systems) products or custom coding; and oftentimes both. This free flow of information has introduced a new set of widely used terms, standards, and phrases such as IIoT (Industrial Internet of Things), Smart Factory, Cloud Automation, and Industry 4.0.
The typical process control model that involves decision-making for the process at the local or centralized level by PLCs (Programmable Logic Controller) or BPCS (Basic Process Control System) has been changing. Earlier systems were not designed to handle the massive amount of data that would become available in the future. There are newer ERP, MES, and asset management systems that collect some of this data now, but the more critical challenge that local manufacturing facilities face is manpower. Because streamlining of costs and overheads has left many manufacturing facilities with just enough personnel to keep the plant running, facilities no longer have the extra time, personnel, and resources required to analyze data.
For this reason, we are seeing third-party companies, and even some of the larger process control vendors, offer leasing or annual agreements that involve collecting, storing, and analyzing various types of process data. This data is part of a larger predictive analytics strategy that can not only forewarn operators of impending problems to come but is also being used to optimize the process itself. This type of cloud automation looks to gather as much data as possible to reduce operating expenditures and future capital expenditures for future plant builds.
So, the challenge remains: how do existing and new manufacturing facilities find a cost-effective way to get critical plant floor data up to higher-level information systems?
Take advantage of the HART data already installed.
With over 40 million installed HART (Highway Addressable Remote Transducer) devices worldwide, HART is not only here to stay but unlike other protocols, it also continues to get updated revisions that continually enhance data exchange capacity, speed, number of devices on a network, support over Ethernet, and wireless capability. There is no other protocol that has a massive installed base, is open to all vendors, has proven worldwide end-user support, and continues to get updates and unilateral support from nearly all mainstream device manufacturers. For these reasons, HART will continue to retain its leadership role, enabling end users to have unfettered access to process and diagnostic data that can be shared with all areas of the new Smart Factory that supports IIoT endeavors.
HART-enabled devices superimpose a digital signal upon their 4-20mA process signal. The HART digital signal often contains additional process measurements and other variables that may include instrument status, diagnostic data, alarms, calibration values, and alert messages.
Many HART field transmitters are hard at work measuring process parameters and producing a 4-20mA signal that is being used for process control by a BPCS, PLC, or some other control system. In many cases, HART instruments were installed simply because they could be configured and diagnosed easily with a HART handheld communicator (HHC). There are several reasons that the rest of the HART data often goes unused. One of them is the prohibitive cost of installing a plant-wide HART monitoring system and the lack of familiarity with alternatives. A simple and cost-effective solution for gathering HART information is to use a HART interface device. These HART interface devices make acquiring HART data a simple proposition. This HART data can then be made available to the control system, asset manager, or plant Ethernet backbone where it can then be shared with higher-level systems or corporate WANs (Wide Area Network).
The HES HART to Ethernet Gateway System from Moore Industries converts signals from wired HART devices to Ethernet MODBUS/TCP and HART-IP.
The HES offers a flexible and economical way to gather process data and instrument diagnostics from just one smart HART instrument, or several in HART digital multidrop networks, and share it over an Ethernet infrastructure with MODBUS/TCP or HART-IP hosts. This enables fast and seamless connectivity for the advanced monitoring of critical process variables and parameters.
The rugged HES supports HART 5, 6, and 7 devices with sufficient memory to handle thousands of process variables, and diagnostic data points from up to 64 connected smart HART devices. The HES allows you to further leverage your industrial Ethernet investment by making all of this valuable HART data viewable with any web browser or MODBUS/TCP compliant host. The HES also supports HART-IP, allowing any of the connected HART device variables, HES variables, or diagnostics to be monitored. Support for these open industrial protocols enables you to easily interface with any process control or asset management system while taking advantage of any Industrial Internet of Things (IIoT) initiatives that facilitate the propagation of process data to higher-level corporate or analytical systems.
Leverage Your Existing Network Investment
When monitoring process points, whether dispersed or in small clusters, the HES leverages existing Ethernet network investments by collecting and concentrating process variables from multiple devices onto a single Ethernet communications link. Up to 16 HART instruments can be multidropped on each of the HES’ four channels (4-channel model) onto a low-cost Ethernet communication link allowing up to 64 instruments to be connected using one HES.
The HES communicates with IIoT systems using MODBUS/TCP or HART-IP over Intranet or Internet to historians, control, or higher-level systems. Using the HES to interface with existing HART instruments, as opposed to installing new process instruments and wiring, allows the use of existing Ethernet networks to communicate with a host system, delivering significant savings on upgrade and installation costs.
Diagnostics Help Improve Process Uptime
The HES is capable of collecting and transmitting diagnostics from multiple Smart HART instruments to enable a more timely and effective analysis of your process. The diagnostic data collected by the HES from connected devices are transmitted through MODBUS/TCP or HART-IP over Ethernet to control systems, historians, etc. for predictive analytics that permits scheduled preventative device maintenance, greatly reducing unplanned or emergency process interruptions or shutdowns.
Use the HES to capture up to 128 variables from each of the four devices and deliver the data to an asset management system. HART Revisions HART field devices are compliant to a certain HART revision. Most field devices released within the last twenty years support HART revisions 5, 6, or 7. The HES, acting as a HART host, communicates with all HART field devices with revisions 5, 6, or 7. It is important to verify which revision of HART the field device supports to ensure that the HES is configured correctly.
HES as a HART Host
The HES can be configured as a Primary or Secondary HART Host and polls up to 16 field devices on each of its four channels (total of 64 field devices maximum per HES). As a Primary or Secondary Master, the HES can be configured to communicate in the normal mode or burst mode per channel. The HART standard permits only one device to be in the burst mode per channel. The HES supports HART Commands 3 and 9 for the reading of Dynamic and Device Variables. Additionally, the HES supports Command 48 which reads the field device’s Additional Status data.
HES as a HART Field Device
The HES acts as both a HART host (reading up to 64 field devices across four channels) and a HART field device. As a HART field device, the HES is HART 7 compliant and has both Dynamic and Device Variables which can be read via MODBUS/TCP, HART-IP, or can be viewed on the HES’ web pages.
Quick and Easy Setup
The HES HART to Ethernet gateway system is easily and quickly programmable. Use any FDT-compliant host or download free PACTware software from our website which allows you to set up all HES settings utilizing our DTM. The HES’ IP address is configured with Moore Industries Network Addressing Configuration (NAC) Client Software, which can also be downloaded for free from our website. The HES supports Auto MDIX (Medium Dependent Interface), which means that either a straight-through Ethernet patch cable or crossover cable can be used for commissioning and configuration.
Embedded Web Server
A built-in web server in the HES provides quick and easy read-only viewing of any connected HART devices. The web pages include simple-to-navigate menus and tables that neatly lay out all of the HART Dynamic and Device Variables from each of the connected HART devices. In addition, the HES’ HART variables and diagnostic data are also included within these web pages. To make communication setup with a MODBUS/TCP host easier, the tables within the web pages include MODBUS memory map address referencing so users can more easily configure the MODBUS/TCP host settings.