ApplicationsSeptember 20, 2024
Digital tool life monitoring: making machine data transparent
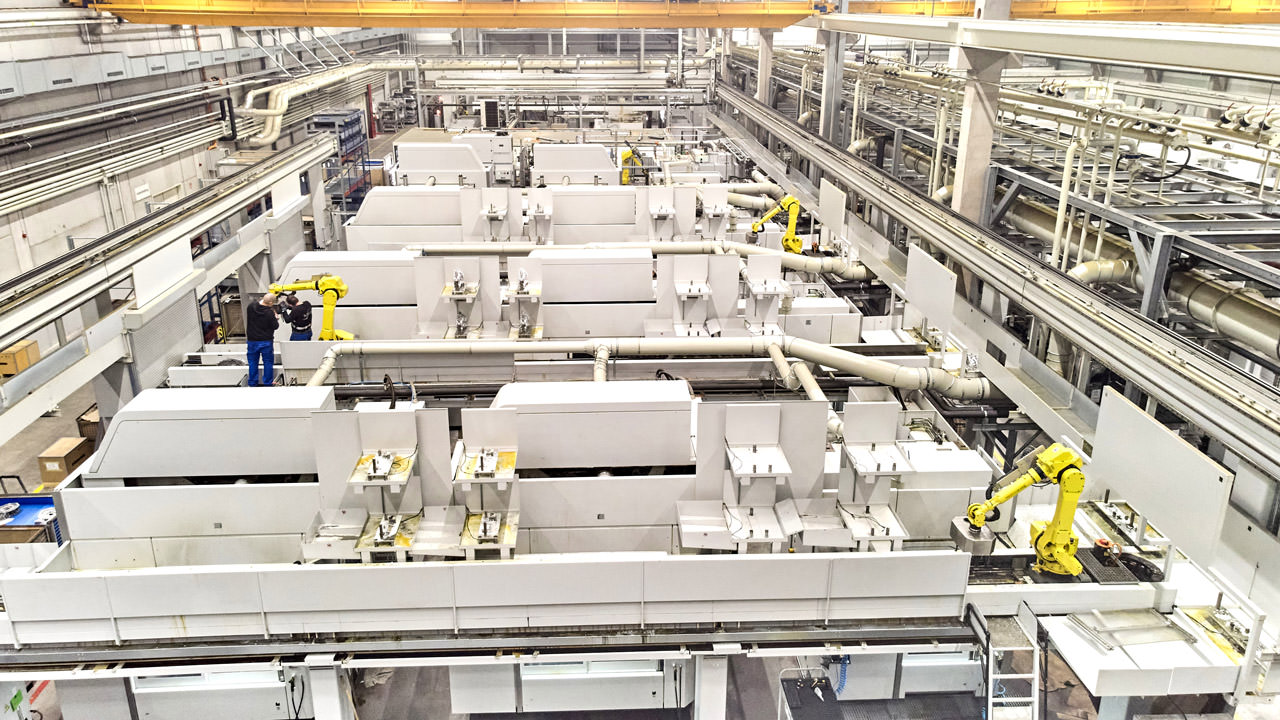
Metal machining is a standard process in the manufacturing of parts for the automotive sector. This is where digitalization in manufacturing can help to optimize process flows and boost efficiency. In its production work, Schlote Group utilizes the edgeConnector 840D from Softing to monitor tool life in its machining centers.
High-volume production of automotive parts often involves the use of machining to further process cast parts. This particular area is a specialty for the midsize enterprise Schlote Group. At nine facilities around the world, the company operates an extensive machine pool for metal processing and other manufacturing processes.
Drilling, turning, milling, and other cutting methods are part of the standard repertoire here for processing engine, transmission and drivetrain components. To secure outstanding quality and high levels of efficiency, advanced CNC machining centers and automated production lines are used.
True to the company slogan “Innovative technology for success,” Schlote Group works continuously towards improving production and optimizing its process flows. “This is where digitalization offers us huge potential,” says Sascha Carell, who is responsible for shopfloor IT as the Group’s MES Team Lead.
Regular tool changes
At Schlote Group’s Harsum facility, the focus is on processing parts made from steel. Tools in the machining centers here are therefore subject to high levels of wear. Depending on the specific circumstances, individual tools may only have a life of a few thousand processing cycles.
On average, employees in production need to change two to three tools every minute at one of the many machining centers in use. For each tool responsible for handling a specific processing step, a maximum number of processing cycles is defined – after this time, the tool must be swapped out. Changing out the tool in time is the most effective way of avoiding unplanned system downtime due to tool breakage.
Carell: “The challenge here is monitoring all of the machining centers at the same time, so that tool changes can be carried out well in advance of any issues. So we were on the lookout for a digitalized solution to handle this task.”
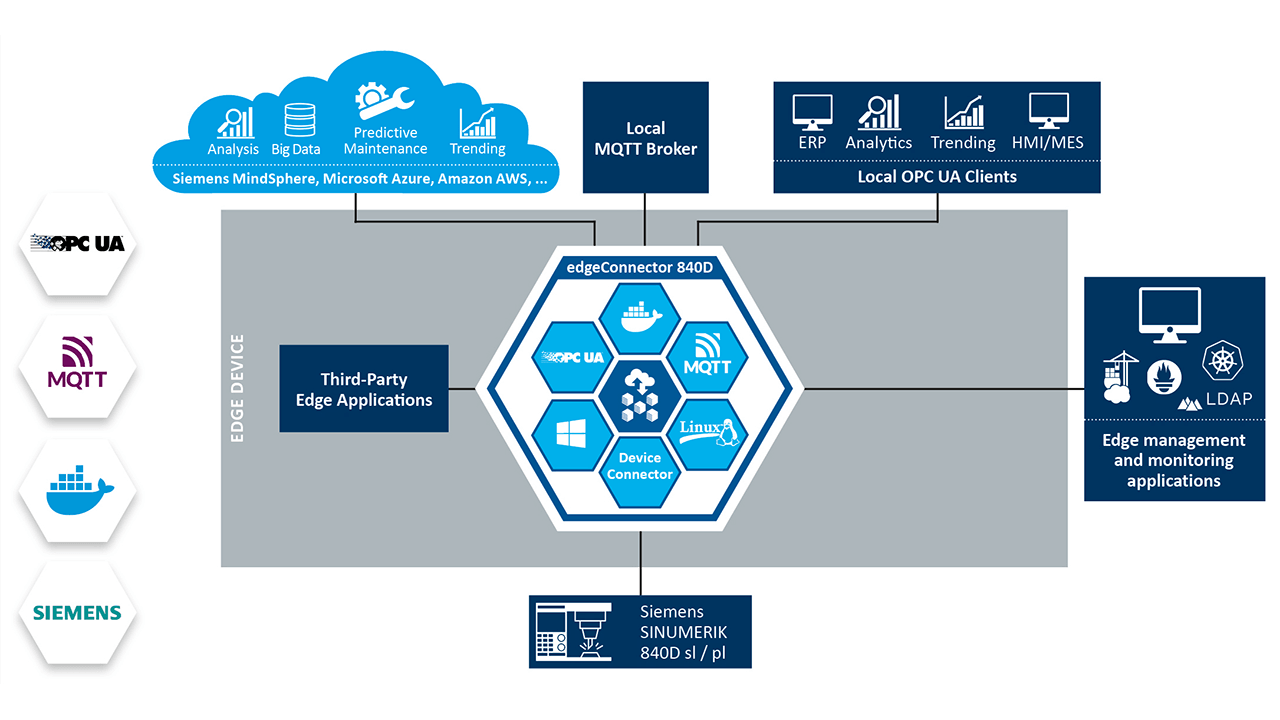
The edgeConnector 840D from Softing accesses data from machine tools and supplies them to data consumers via an OPC/UA server (for example).
Data from the machine tool control
The data needed – in this case, the number of processing cycles since the last tool change – can be found in the CNC control inside the machine tool. However, the challenge here is ensure the right data are extracted from the machines in question and transferred to a higher-level system.
While solutions are also offered by the machine tool makers, these are manufacturer-specific. This makes it impossible to obtain an overview of the data from the overall machine pool, which includes machines from several makers. With the edgeConnector 840D from Softing, Schlote Group has found a solution that can retrieve the data from the Sinumerik controls used in its machining centers.
“We use Windows servers as our standard IT systems,” Carell explains. “These provide a Linux subsystem on which we can install the edgeConnector 840D as a Docker container.” Communication with the machine pool is then easily handled via the company-internal network. For machines featuring a Sinumerik 840D Powerline control without an Ethernet port, Softing offers a compatible adapter for the control’s serial interface.
The software is configured very quickly and easily via a browser-based interface. The variables as well as the control and NC component can be selected in the corresponding tools, which generate the data files that the edgeConnector can import.
Carell: “One thing that we wanted to get right here was to have a solution that can also access data from the NC component and make these data easily available. Softing’s edgeConnector formats these process data into a clean and tidy process data tree.” A key factor for Schlote in this application is the tool monitoring counter, which indicates how many parts can still be processed before the next tool change. As soon as this counter with a stored maximum value approaches zero, an employee has to change the tool.
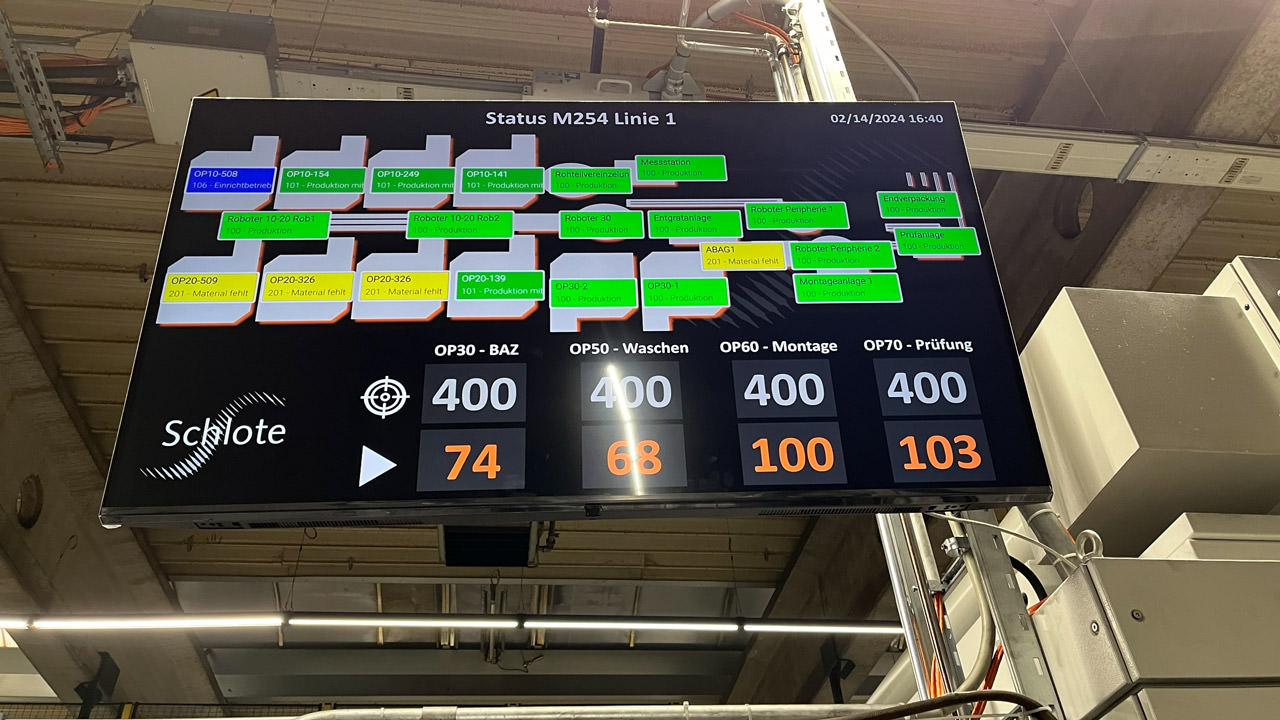
Thanks to the data visualizations provided by Peakboard dashboards, employees can check tool and machine data at any time.
Visualization without programming
Further processing of the data supplied by the edgeConnector is unproblematic, as Softing makes use of open industry standards and protocols such as MQTT and OPC/UA. Schlote uses the Peakboard Designer to visualize the data for employees working in production. This low-code application can be used to create visualizations even without extensive knowledge of coding.
Within the user-friendly interface, users work with building blocks to map out more complex process flows. To process the data from the edgeConnector, the OPC UA server is selected as a data source in Peakboard Designer.
Large screens showing dashboards with the tool data have been installed in several places in the production areas at the Schlote facility. The employees responsible for the machines only need to glance up to see when the tools are due to be changed. Other status data are also visualized alongside the tool data. These screens supplement the traditional “traffic lights” on the machines. And operators are more likely to use the screens and dashboards, as they offer much more information. As one example, the screen tells them why the traffic light has just turned yellow or red. “Being able to skim through all of the key data at a glance is a real help for our production team,” says Carell in conclusion.
Better integration with platforms
Integrating the edgeConnector 840D with the Peakboard solution was also a positive experience for Schlote’s MES Team Lead. “I didn’t have to stop and work out a software networking strategy, because the manufacturers offer solutions that are designed to fit together. This kind of architectural compatibility and collaboratively developed solutions package really offers great value for end users. Carell was also highly impressed by the experience of working with the Softing team. “Softing responded promptly to new requirements, also typically implementing these over a short timeframe. At the end of the day, this project was really like working as part of a single development team.”