ApplicationsJuly 10, 2018
EtherCAT plug-in modules optimize electronics production
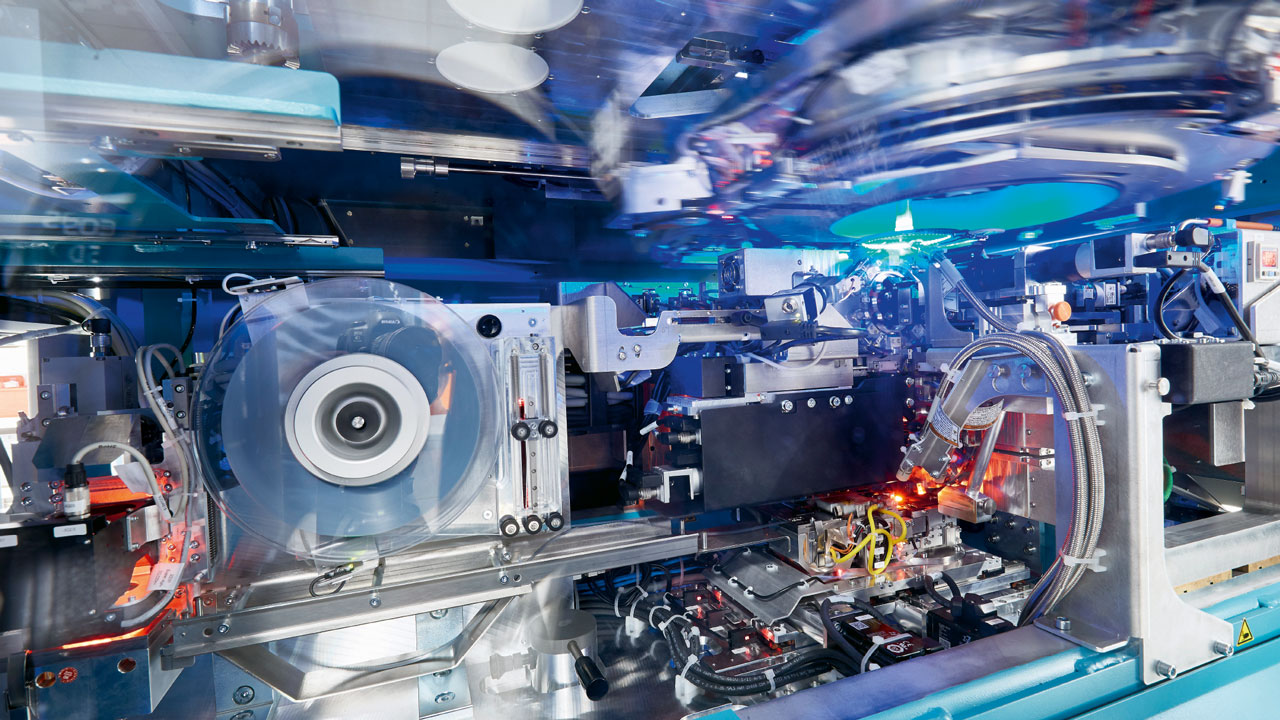
EtherCAT modules, in conjunction with a customer-specific signal distribution board, helped Mühlbauer GmbH increase the throughput of its die-sorting machines from 20,000 to 30,000 chips/hour, simplifying machine setup and operation, and reducing costs by 20 percent compared to previous machine models.
Specialized machines for chip card and passport production, as well as in the semiconductor industry, are built by Mühlbauer GmbH & Co. KG based in Roding, Germany. The company creates a competitive advantage with a high degree of standardization in machine construction. EJ series EtherCAT plug-in modules, in conjunction with a customer-specific signal distribution board, ensured significant reductions in errors and the time required to manufacture these machines. This also resulted in reduced manufacturing costs and accelerated delivery times for the new DS Merlin die-sorting system.
Mühlbauer is an innovative and globally operating company that covers the entire spectrum of safety applications, ranging from simple production parts to complex production lines and turnkey solutions, including building and safety planning.
“The automation division at Mühlbauer focuses on machines for semiconductor finishing, RFID and tag manufacturing, ID card and passport production, personalization machines for documents and bank cards, as well as complex inspection systems,” said Martin Dimpfl, Head of Electronic Engineering in the automation division. “This includes the new DS Merlin die-sorting system, which can process up to 30,000 dies per hour – including complete vision inspection for possible defects. In addition to the considerable increase in throughput from 20,000 to 30,000 chips/hour, simplified machine setup and operation, as well as improved wafer handling, it was also possible to reduce costs by 20 percent compared to the previous machine model. The standardization of the I/O system with EtherCAT plug-in modules from Beckhoff was a key contributing factor to these achievements.”
The DS Merlin can process microchips up to a size of 0.2 x 0.4 mm and a thickness of 80 μm with maximum precision and speed. The respective wafer is measured, and the placement or size of the individual chips is recorded. The machine then automatically corrects the transfer of the semiconductor devices to the individual pick-and-place units. The advantage, Dimpfl said, is that “up to now, all this had to be implemented by the machine operator via teach-in. This whole effort has been eliminated.”
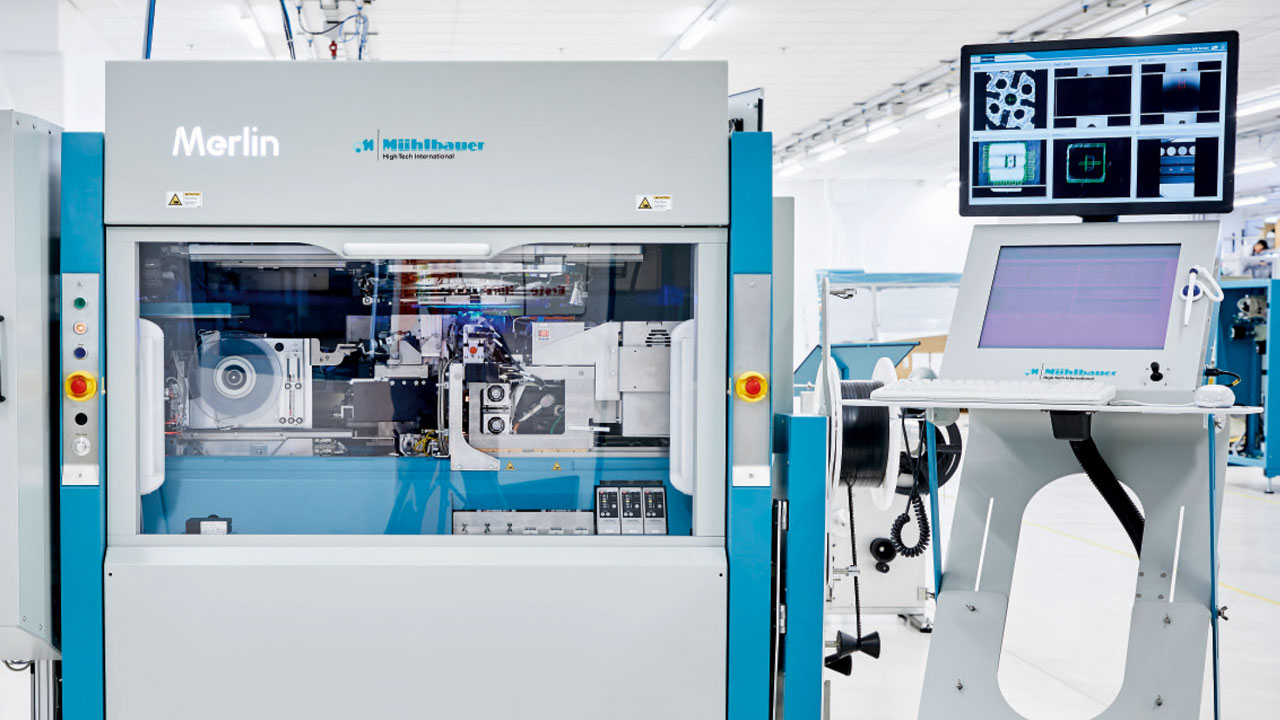
With up to 30,000 dies per hour, the DS Merlin die-sorting system can process significantly more semiconductor components than its predecessor.
Modular machine designs
The machine is divided into different function modules. The automatic wafer changer first transports the wafer onto a table and then transports the processed semiconductor wafers back into a wafer cassette. The wafer table expands, rotates and moves the wafer during production. It then positions the wafer in such a way that the following die ejector (chip removal unit) can transfer the individual microchips to the upper of two inspection wheels, where the wafer film is held in position by a vacuum around the die ejector needle.
All six microchip sides are 100 percent checked on the two inspection wheels. A counting module then positions, transports and seals the belt with the chips placed in it with the cover band and carries out final inspections. Once the desired quantity has been reached, the belt is cut off. Dimpfl said this advanced machine was designed to be highly modular and compact.
“For this reason, four different signal distribution boards with EtherCAT plug-in modules are used in the DS Merlin, for example. The main reason for introducing the new I/O concept was the significantly reduced wiring effort. This has a very positive effect on error reduction and, above all, on manufacturing time and costs,” he said.
Maximum I/O installation efficiency
Four signal distribution boards are precisely matched to the Mühlbauer machine’s requirements and, according to Dimpfl, go far beyond simple I/O signal distribution. In addition to the EJ modules, EtherCAT servo drives for piezoelectric and piezo-ceramic motors, flashlight controllers and logic for vision applications, as well as the complete 24/48 V voltage distribution are also included. A total of 26 EtherCAT plug-in modules are used, with digital and analog inputs/outputs as well as an incremental encoder interface, stepper motor module and bus power supply unit.
“Our goal was to minimize the wiring effort within the machine and to place the signal distribution board as close to the respective components as possible. This results in an extremely compact design, and the complete wiring and testing of the unit can be carried out in the pre-assembly phase. Thus, the times for testing, production and commissioning are reduced throughout,” Dimpfl pointed out.
Dimpfl also sees a great advantage in the breadth and consistency of PC-based control technology. “With the comprehensive product portfolio from Beckhoff, the right control solution is available for every machine process. In addition, EtherCAT plug-in modules add another advantage to the time savings and error reductions mentioned above. Through consistent support for EtherCAT communication, they can be easily combined with the wide range of available EtherCAT Terminals. This increases our flexibility immensely, as additional customer requirements such as the integration of special sensors or special test systems can be implemented quickly and easily based on the same basic machine,” he added.
The EJ system also offers flexibility with regard to application-specific developments. For example, the signal distribution board can be designed and manufactured in-house by the customer, as a service from Beckhoff or via a third-party company. According to Dimpfl, Mühlbauer decided on the first option.
“Since we have our own electronics development department, this was an easy decision, particularly in view of the fact that Beckhoff provides optimum support, for example with a comprehensive design guide for the EtherCAT plug-in modules,” he said.
Small series production
As a specialized machine manufacturer, the modular system is indispensable because it achieves the standardization needed to use basic assemblies efficiently in different machine types, and to eliminate the need for a complete redesign for each machine.
“According to our calculations, the use of EtherCAT plug-in modules – including the development of the signal distribution board – already returned the investment for a small series of around 10 machines per year. As the functionality of the boards is fully tested in advance, we achieve an enormous reduction of the error rate during assembly, resulting in smooth commissioning,” Dimpfl explained. “In the case of the DS Merlin, this saves approximately 100 hours of installation time, plus additional time saved that was previously spent on troubleshooting and debugging. Accordingly, we will successively convert all relevant machine types in our portfolio in the future, which comprises more than 200 systems with more than 10 machines per year, to the Beckhoff EJ system.”