ApplicationsSeptember 10, 2018
Fast changeovers drive high-speed forming machines
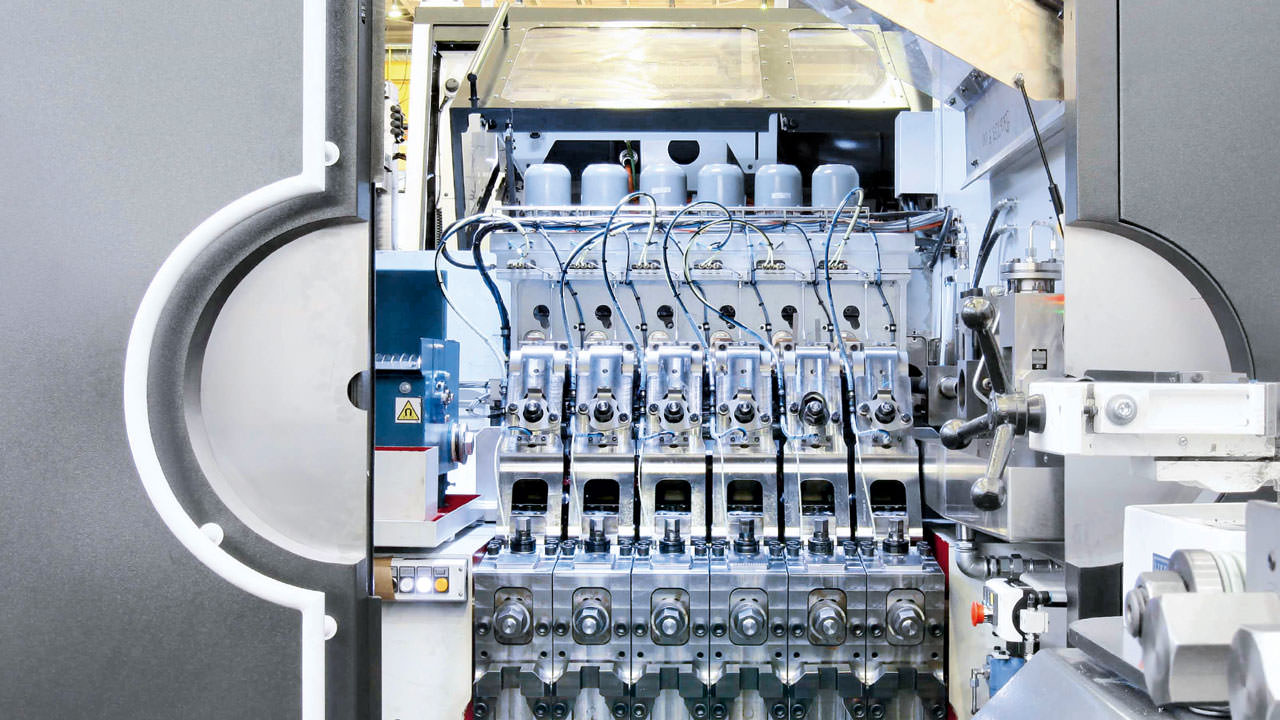
Highly dynamic servo drive technology optimizes forming machine used for precise fastener production. Using this solution, all cam-setting restrictions have been solved. Adjustment of gripping force for fingers, which used to be mechanical, is now done in software, along with receiving feedback from the servo drives.
By switching to servo DRIVE technology, the Belgian company Nedschroef Machinery has greatly reduced the time needed to adapt and set up its metal forming machines used for the production of high-precision fasteners. With an output of up to 240 screws per minute, this places the highest demands on the dynamics and performance of servo drives and motors.
Nedschroef manufactures multi-stage forming machines that produce fasteners and molded parts with complex geometries, such as those used in the automotive industry.
“The requirements for dimensional tolerances and strength are correspondingly high,” said Nedschroef Engineering Manager, Dirk Matheeussen. “In order to guarantee the necessary stability, the screws are pressed from metal rods. Machining inherently reduces the stability between the screw shaft and the screw head, as the material structure is disrupted. That’s not the case with pressing,” he added.
The pressing of the screws is done in individual steps, with each die in the machine carrying out one machining step at a time. After each stroke, the product is transported with grippers until it reaches its final shape.
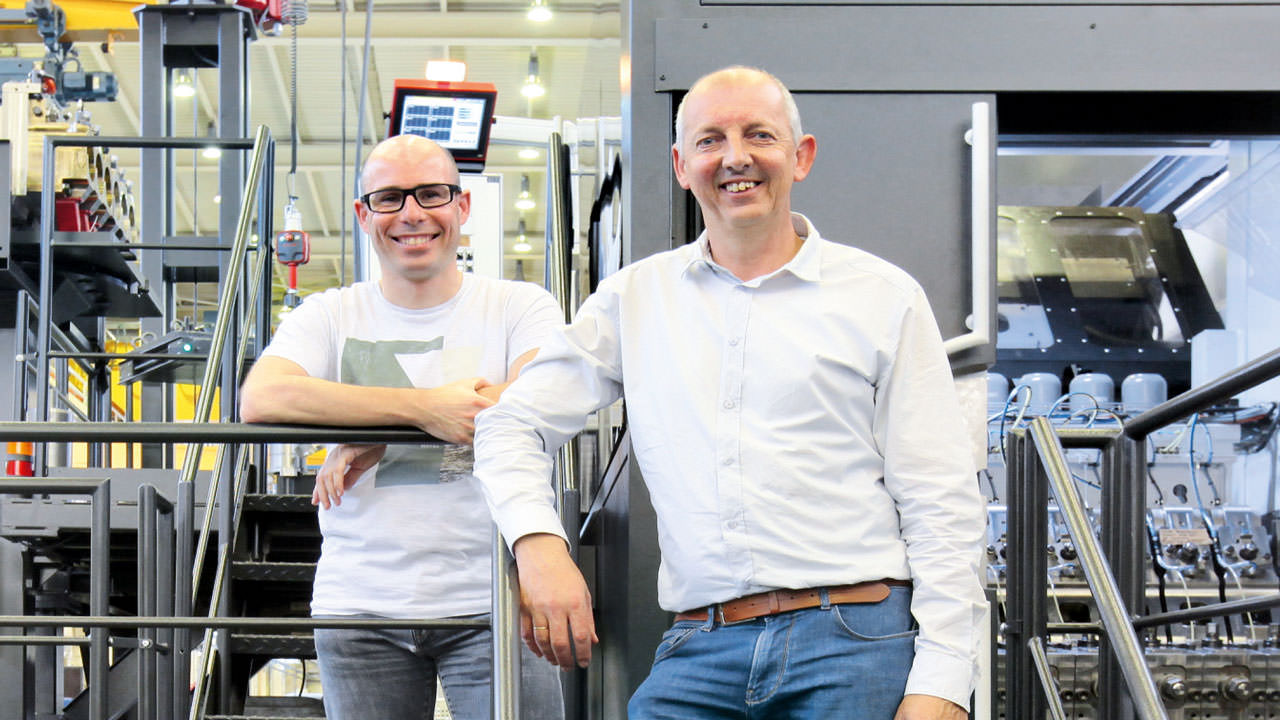
Tom van Weert, Programmer, and Ivo Van Gorp, Coordinator/Developer Automation at Nedschroef, in front of the forming machine (from left to right).
EtherCAT synchronized motion
Nedschroef’s metal forming machines were previously powered by a single motor. A complex mechanical system with gear units and camshafts allowed all functions of the machine, including the gripper finger that transports the products between the individual machining steps, in order to run synchronously.
“The gripper carriage was the first component that we equipped with separate servo drives,” explained Ivo Van Gorp, Coordinator/Developer Automation at Nedschroef.
“In the past, the cams themselves had to be moved in order to adapt the machine when changing production, which was not only time-consuming but also limited the setting range. After equipping each gripper and carriage with its own servomotor, all positioning limitations have been removed,” he added.
“Motion synchronization is now performed in TwinCAT software from Beckhoff,” said Nedschroef Programmer Tom Van Weert. “We use an EtherCAT network with a cycle time of 500 µs. This allows us to precisely synchronize the various machine movements with those of the dies.” The mechanical cam controller has been completely replaced by TwinCAT NC Camming, which enables faster, safer and error-free changeovers while providing more setting options.
The parameters are stored for each product in the controller and can be adapted or retrieved from the graphical user interface, which helps even less experienced machine operators successfully handle rapid changeovers.
However, the transition from a mechanical gear unit to a servo drive system presented Nedschroef with challenges. “Our fastest machines produce 240 screws per minute,” said Van Gorp.
“That means four strokes per second. For each stroke, one-third of the time can be used to grip and advance the screws. The gripping itself must take place within one-twelfth of a stroke. It was not easy to find a drive system that could react so quickly and build up sufficient gripping force in such a short time.”
Nedschroef finally found the solution in the AM8000 series servomotors and AX5000 Servo Drives from Beckhoff.
Servo technology has numerous advantages. With this solution, all cam-setting restrictions have been solved. The adjustment of the gripping force of the fingers, which used to be mechanical, is now also done in software. In addition, we receive feedback from the servo drives. If a finger has gripped a product incorrectly or incompletely, this is detected immediately and can be responded to.
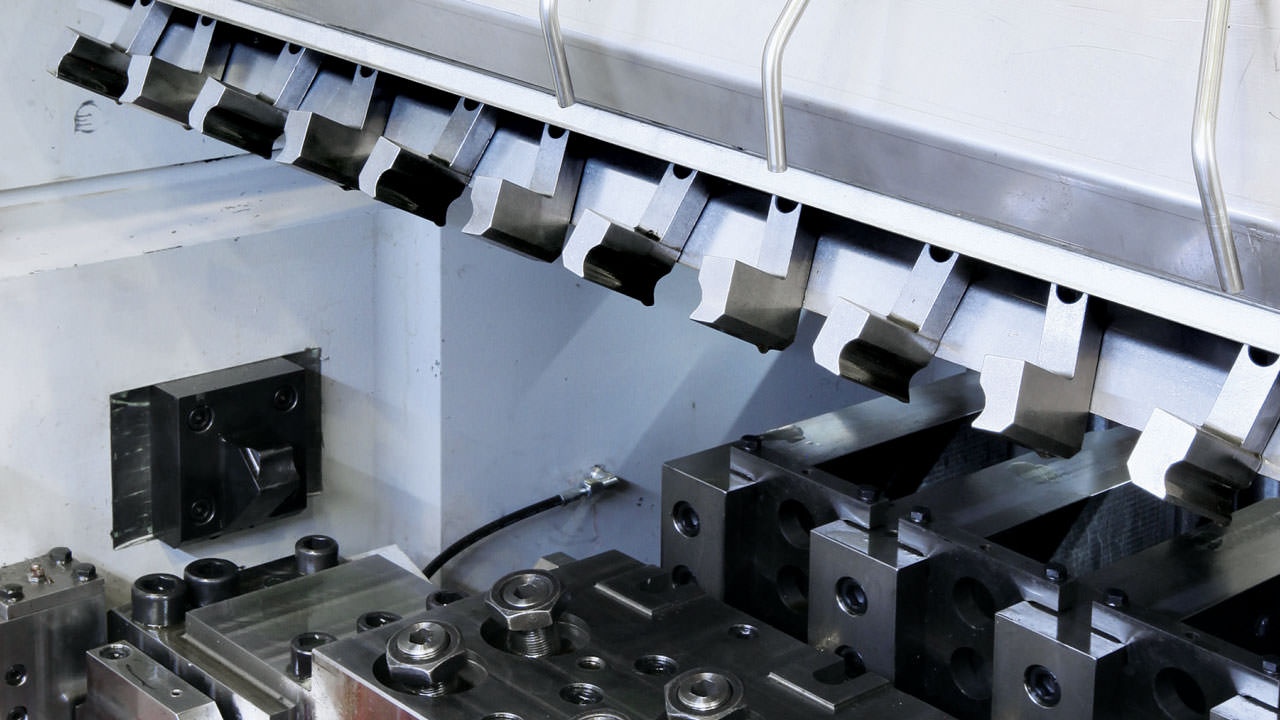
The servo-controlled gripper fingers convey the products with high precision and dynamics between the individual processing steps.
Flexibility and faster changeovers
“Our customers were initially reluctant to use the mechatronic solution because they were used to working with purely mechanical systems. In order to simplify the transition to electronic control, we presented some parameters on the HMI in the same way as in the previous cam control system. The creation of an intuitive interface has made the transition much easier. Once you are familiar with the new technology, you can quickly see the advantages. Many of our customers have to change over their machines several times a day. This is now much faster and the error rate has been significantly reduced,” explained Van Gorp.
Nedschroef now uses servo technology for the material feed axis, and a Beckhoff linear motor handles the rod feed. The complete machine control runs on a C6930 Industrial PC, which integrates both PLC and drive control.
“The NC tasks are also implemented in software modules,” added Van Weert. “This makes it easy to adapt all profiles for motion synchronization.”