ApplicationsJuly 16, 2024
Motion Control and Measurement Data Acquisition in Perfect Sync
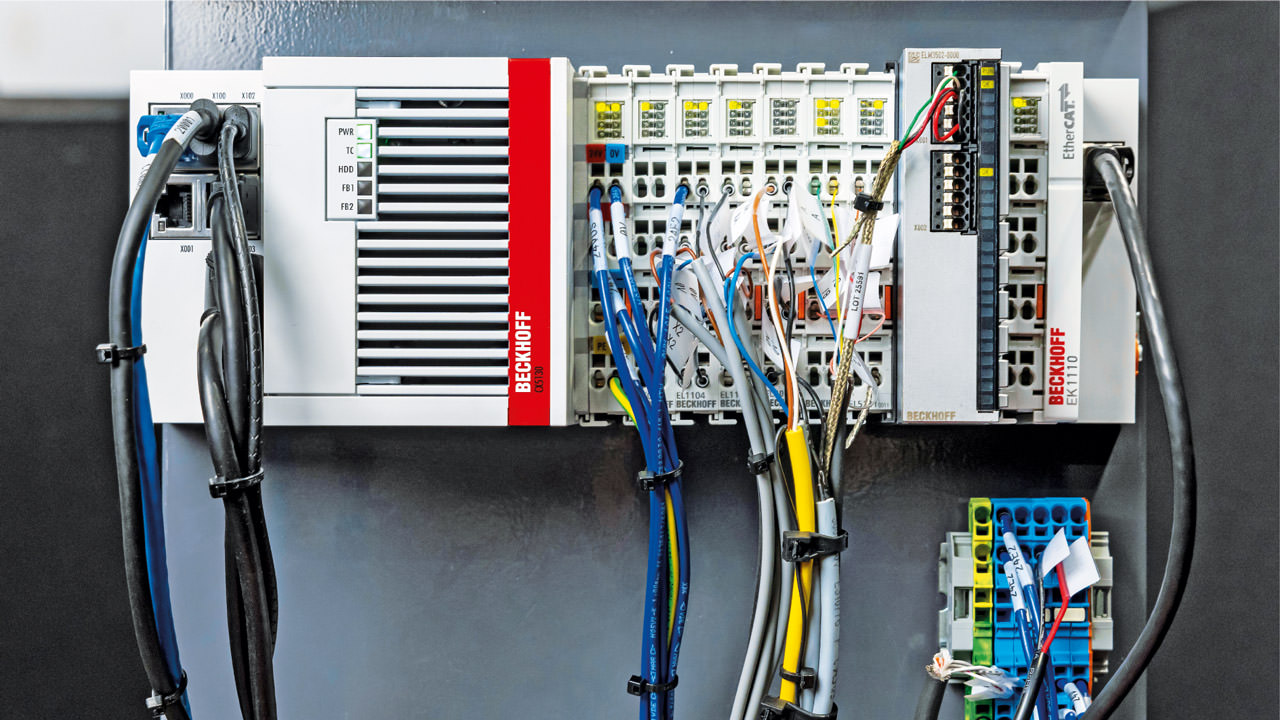
PC-based control and EtherCAT have combined to automate a compact sporting goods test machine. The system delivers precise measurement results using standard components from the automation specialist, and hardware costs were cut by around 4,000 U.S. dollars per machine.
The modernized Impact Tester from Automated Design Corporation (ADC) demonstrates the benefits of seamlessly integrated control and measurement technology from Beckhoff. In the dynamic testing of cushioning elements for sports shoes, the system delivers precise measurement results using standard components from the automation specialist. The hardware costs were cut by around 4,000 U.S. dollars per machine.
ADC’s redesigned Impact Tester shows how well the traditionally disparate disciplines of measurement technology and industrial automation can work together. “The impact testing system, like most others, is more industrial than typical desktop lab-type boxes, but it now offers extended data acquisition (DAQ),” says Thomas Bitsky, Jr., Vice President and Lead Developer at ADC. Founded in 1986 by Thomas Bitsky’s parents, the company based in Romeoville, Illinois, today supplies R&D systems to numerous renowned sporting goods manufacturers.
ADC needed to meet several requirements when upgrading the Impact Tester. Precision motion control, real-time fieldbus communication and fast cycle times were necessary, and a more intuitive HMI was mandatory. Beyond that, ADC wanted the solution to overcome the boundaries between traditional measurement and control technology.
The DAQ industry has remained siloed for far too long, according to Thomas Bitsky. In the past, however, the high sample rates needed to ensure the required measurement quality could only be found in the components from select vendors. But when using a legacy DAQ controller running LabVIEW™ software, automated test handling requires a separate PLC, Thomas Bitsky explains: “These scenarios add cost, communication delays and cabling nightmares.” Also, the motion control and DAQ technologies must synchronize perfectly for accurate, reproducible test results, which creates challenges when using separate solutions. In order to minimize losses at the interfaces, ADC decided to use system-integrated measurement technology in a flexible control platform from Beckhoff.
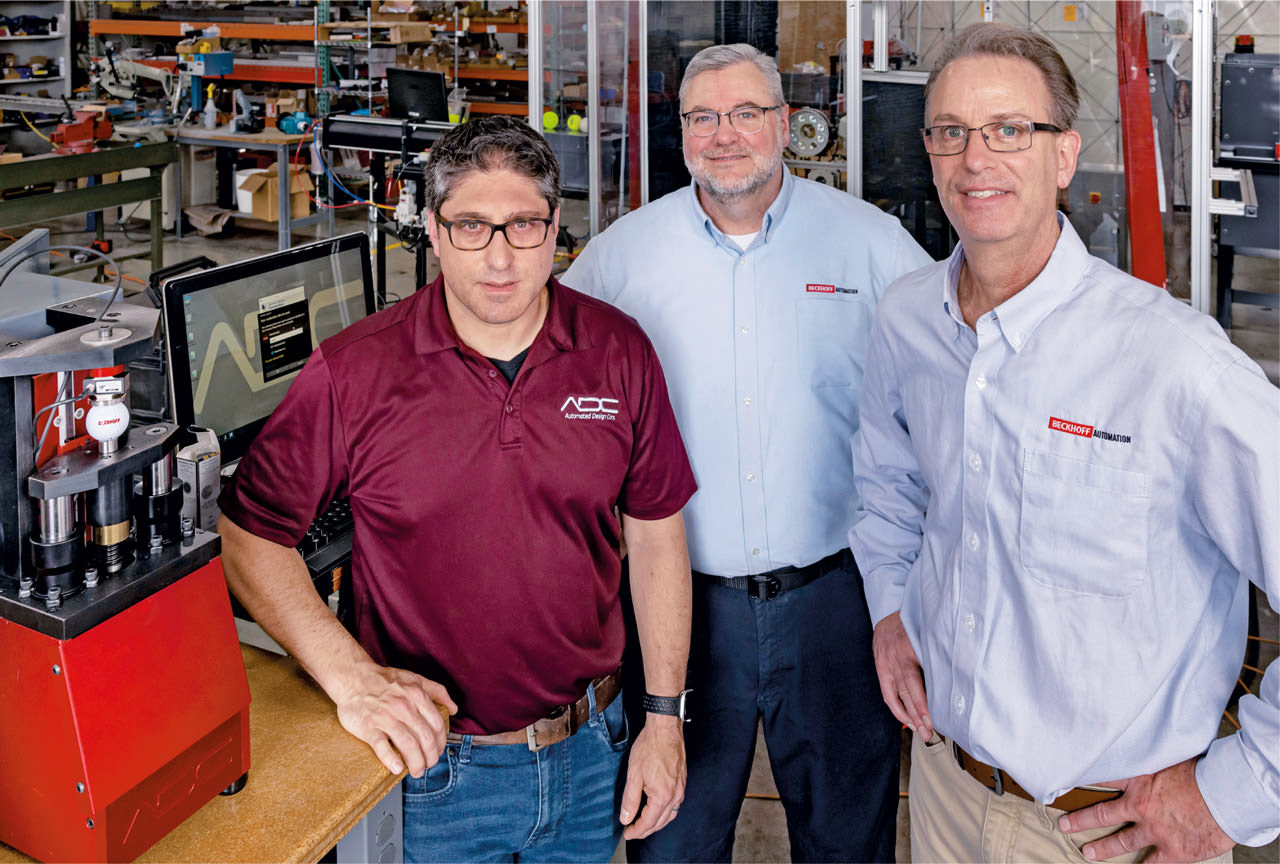
Thomas Bitsky, Jr. (left), Vice President and Lead Developer at ADC, works closely with Dave Zimbrich, Applications Engineering, and Mike Rauch, Regional Sales Engineer, both from the Beckhoff team in the Chicago area.
High-end measurement technology in a standard I/O system
EtherCAT offers many benefits, but the main advantages for ADC are speed and bandwidth. For analog data acquisition during impact testing, EtherCAT measurement terminals from the ELM series with oversampling capabilities are used. Oversampling means reading data multiple times per control cycle for enhanced time resolution of a signal and increased accuracy.
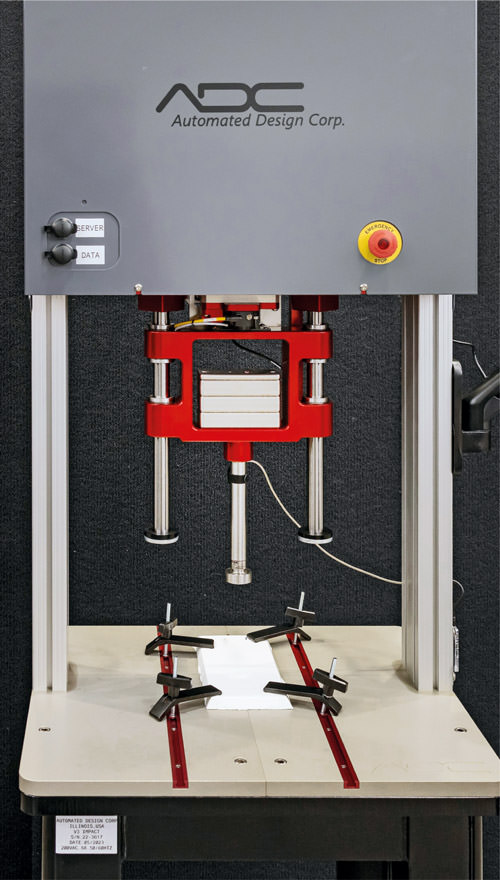
ADC’s redesigned ASTM-compliant Impact Tester combines high-end measurement with intuitive operation.
With this high level of performance, ADC was able to use commercial off the shelf (COTS) measurement terminals from Beckhoff to eliminate expensive, specialized hardware. The high-end ELM3502 measurement terminals are fully integrated into the standard Beckhoff I/O system and offer dual-channel measurement in a ruggedized metal housing. With sampling rates up to 20 ksps, the terminal covers most advanced measurement requirements for ADC. However, the scalable ELM series also offers terminals that support sampling rates up to 50 ksps.
“We had been using other Beckhoff measurement terminals – particularly the EL3356 analog input terminal, which works well for industrial applications. But our test and measurement customers needed sampling in the kilohertz range that only legacy DAQ vendors offered previously,” says Thomas Bitsky and adds: “The ELM terminals delivered the sampling rates we needed, along with perfect synchronization to the controller via EtherCAT. Now, the machines can execute a test very quickly. In one scan, I get all motion and load data, and our measurement accuracy and repeatability look as good if not better than what we got with the traditional chassis-style controller.”
Scalable, standard components
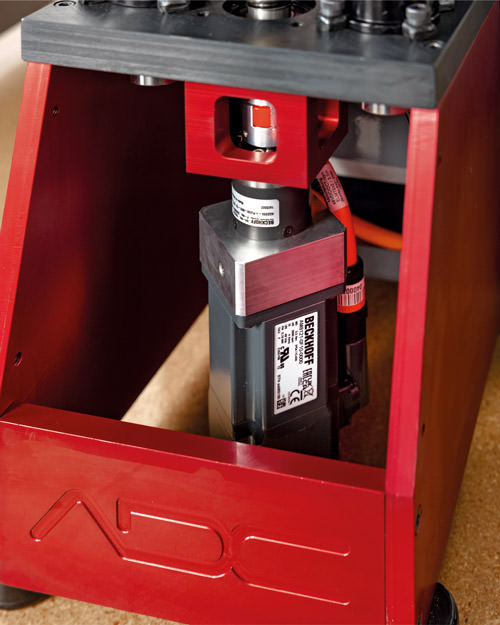
A variety of highly compact servo and stepper motor technologies (here: an AM8121 servomotor) are added advantages of the fully integrated and scalable automation platform from Beckhoff.
TwinCAT 3 delivered a universal engineering environment, which facilitated the implementation, according to Thomas Bitsky, and also easily integrates LabVIEW™ and other third-party software. With TwinCAT, engineers can program in the languages that they are most familiar with or that best fit the project, including the available IEC 61131-3 languages and their object-oriented extensions, function blocks and computer science standards found in Microsoft Visual Studio®. “We lean on TwinCAT to save programming time,” Bitsky explains.
On the controls side, ADC relies on a Beckhoff CX5130 Embedded PC. The DIN-rail-mounted, fanless machine controller saves machine space and delivers ample computing power for data acquisition and motion control in the test systems. The scalability of the Embedded PCs from Beckhoff also allows ADC to increase performance levels when needed, they say.
Compact drive technology from Beckhoff ideally complements the needs of the test systems that usually have to fit in limited lab environments at sporting goods manufacturers. The EL7211 servo terminals (driving the AM8100 servomotors) and EL7041 stepper motor terminals deliver high-performance drive technology in an I/O slice form factor, and are installed in the control cabinet along with the EL5101 encoder interface.
“We can also use third-party motors and drives, and if they’re EtherCAT-based, the integration is incredibly simple. We use the motion control libraries in TwinCAT for all of these devices,” Thomas Bitsky says. “Most of our applications require simple point-to-point motion. We apply a specified load to the material, which requires synchronization between the load cell input and motion controller, and then read the position. If you go past that load, the test will fail to execute.
“The legacy, chassis-style controllers just don’t have the power to support this functionality,” he adds. “But the distributed clocks in EtherCAT ensure synchronization of load versus position. So with the integrated Beckhoff technologies, we’re able to do things that would be impossible otherwise.”
Reduced time and costs
The modernized impact tester machine adheres to the ASTM F1976 and F1614 standards for testing the impact attenuation of cushioning in athletic shoes. The use of standard automation components, including the high-end measurement technology in an I/O module format, led to cost savings of about 4,000 U.S. dollars per machine. The Beckhoff solution also reduced wiring, assembly and programming time. The 24/7 support from Beckhoff proved reliable and efficient when ADC needed assistance.
Since ADC fills a unique gap in testing and automation, it’s important for the company to safeguard its intellectual property. Here, TwinCAT serves up additional value-add, according to Applications Engineer Dave Zimbrich from Beckhoff: “The OEM Certificate feature that we offer allows ADC to encrypt and password-protect its code. This means no matter where their test machine ends up, their code is safe.”