ApplicationsMarch 9, 2020
Predictive maintenance relies on effective data collection
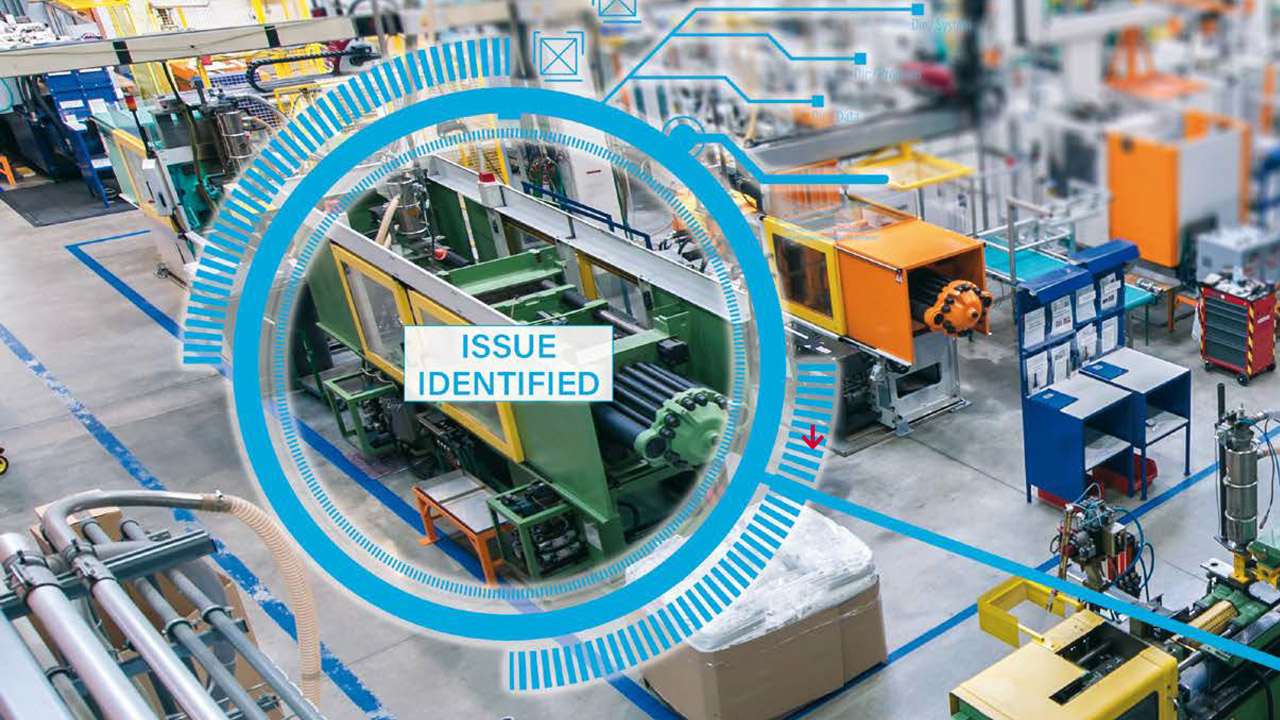
Predictive maintenance has the potential to open up new service models for machine builders. Using machine data, it is possible to more precisely forecast maintenance cycles. Machine builders can offer customers custom tailored service that keeps machines in the field in optimal condition at all times.
When a machine fails or is stopped for maintenance, it comes with a hefty price tag. And that’s not just the cost of repair work and replacement parts, but rather the revenue that is lost every minute that a line is not productive. By helping to detect impending damage before it occurs, an investment in predictive maintenance can really pay off. In addition to preventing revenue loss, predictive maintenance extends the life of the machine and even opens up new business models.
In continuous web machines like those used in printing and packaging, a sheet of material is guided through a labyrinth of rollers. A mechanical imbalance or increased bearing friction in one of those rollers could introduce uncontrolled oscillations that interfere with web tension throughout the machine. This has a negative effect on product quality and could even lead to an outright machine failure.
An effective way to keep this from happening is with a predictive maintenance system, which is able to detect potential faults before they occur. Imbalances or worn bearings are identified in time to plan the necessary repairs before the roller fails and brings the machine to a halt. After all: only if machinery and equipment is functioning properly is it possible to meet financial targets.
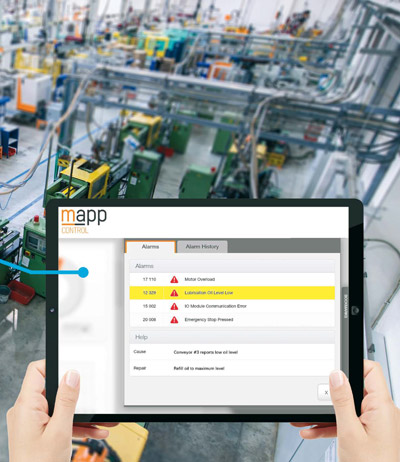
To make a reliable statement about the condition of a machine, the first step is to collect as much data as possible and evaluate it using intelligent analysis algorithms.
Avoid downtime
A predictive maintenance solution relies on a variety of data collected from the machine. This data is collected through a process of continuous condition monitoring, then analyzed and evaluated so that the predictive maintenance system can calculate the precise probability of certain events occurring.
“Not only does predictive maintenance save costs, it also helps maximize productivity – because you’re replacing components before they would begin to impact the machine’s performance,” said Martin Staudecker, software development expert in the area of closed-loop control at B&R.
Predictive maintenance can do much more, however, than simply monitor the behavior of a single roller. It provides comprehensive insight into the health of the entire machine and forecasts the probability of component failure. Motor speed, noise level and temperature can all be recorded, and any unusual vibrations or mechanical imbalances can be detected in their earliest stages. It’s also possible to perform detailed vibration analysis of specific components that are prone to wear.
Intelligent analysis algorithms
To make a reliable statement about the condition of a machine, the first step is to collect as much data as possible and evaluate it using intelligent analysis algorithms.
The more data the system has to work with, the better it is able to detect impending faults before they occur. “That means, however, that you need to find a system that can store and analyze such enormous volumes of data,” Staudecker added.
In addition to condition data from the machine itself, predictive maintenance can also make use of parameters from the surrounding environment, such as temperature and humidity. This data must also be incorporated into the analysis in order to maximize the reliability of its predictions.
B&R’s predictive maintenance utilizes special I/O modules for condition monitoring, paired with sophisticated analysis algorithms from its mapp technology toolkit. The easy-to-configure condition monitoring modules pinpoint areas were service may be needed.
These modules offer unique vibration analysis capabilities. Data received from the condition monitoring modules can easily be prepared and utilized to optimize existing processes. As part of B&R’s X20 controller family, these modules are fully compatible with any machine control topology.
Results-oriented data processing
The collected data is evaluated using the sophisticated analysis algorithms of the mapp Control software package.
“High performance, results-oriented data processing is the key to effective analysis,” noted Staudecker. “And that’s exactly what mapp Control makes possible.” The bulk of the analytics can be performed directly on the controller. That greatly reduces the volume of data to be transferred, since it’s only the results that need to be passed on.
Auto-tuning for fault prediction
Another way to detect faults early is using tuning procedures. Staudecker explained that “mapp Control includes model-based tuning methods that identify system behavior then create a suitable controller on that basis.”
When tuning is performed at regular intervals, not only are the control parameters kept up to date, but any changes in system behavior are brought to light.
Based on deviations in static properties, system dynamics or resonant frequencies, it is possible to draw conclusions about developments in the machine process, leaks or worn components.
Detect wear
Predictive maintenance allows operators to replace worn components when it is most convenient, rather than interrupting ongoing production. Over time, mechanical wear gradually takes its toll on components such as hydraulic valves, which has a negative impact on the control of hydraulic axes.
The mapp Hydraulics package includes a software component for early detection of this type of wear. “The component automatically measures the valve’s characteristic curve, which describes the relationship between valve opening and oil flow rate,” explains Staudecker. “Not only does that let us know when there is wear, it also optimizes control performance.”
Heating current monitoring
Particularly with highly complex machines like those in the plastics industry, the quality of the finished product relies on perfect execution of each step in the process. One sub-process typically involved in plastics production is extrusion. A faulty heating element in an extruder could bring down an entire production line, causing large amounts of waste and immense costs.
“Using software components from B&R to implement predictive maintenance helps keep the machine in optimal condition and maximizes the long-term productivity of the entire system,” said Staudecker. B&R’s mapp Temperature package compares heating currents against reference values at freely configurable intervals. This makes it easy to notice changes in the heating circuit that indicate the first signs of damage in heating elements or relays.
New business models
Predictive maintenance also opens up potential new business models for machine builders, particularly in the area of service. By using machine data collected over longer periods of time, for example, it is possible to more precisely forecast maintenance cycles. Machine builders can offer their customers custom tailored service that keeps machines in the field in optimal condition at all times.
“The data can also be used to optimize the design of the machine itself,” Staudecker said. With predictive maintenance, machine builders can offer a comprehensive service package while at the same time making effectively targeted improvements to their machines.