ApplicationsSeptember 1, 2020
Industrie 4.0: smart electronics production via PC-based control
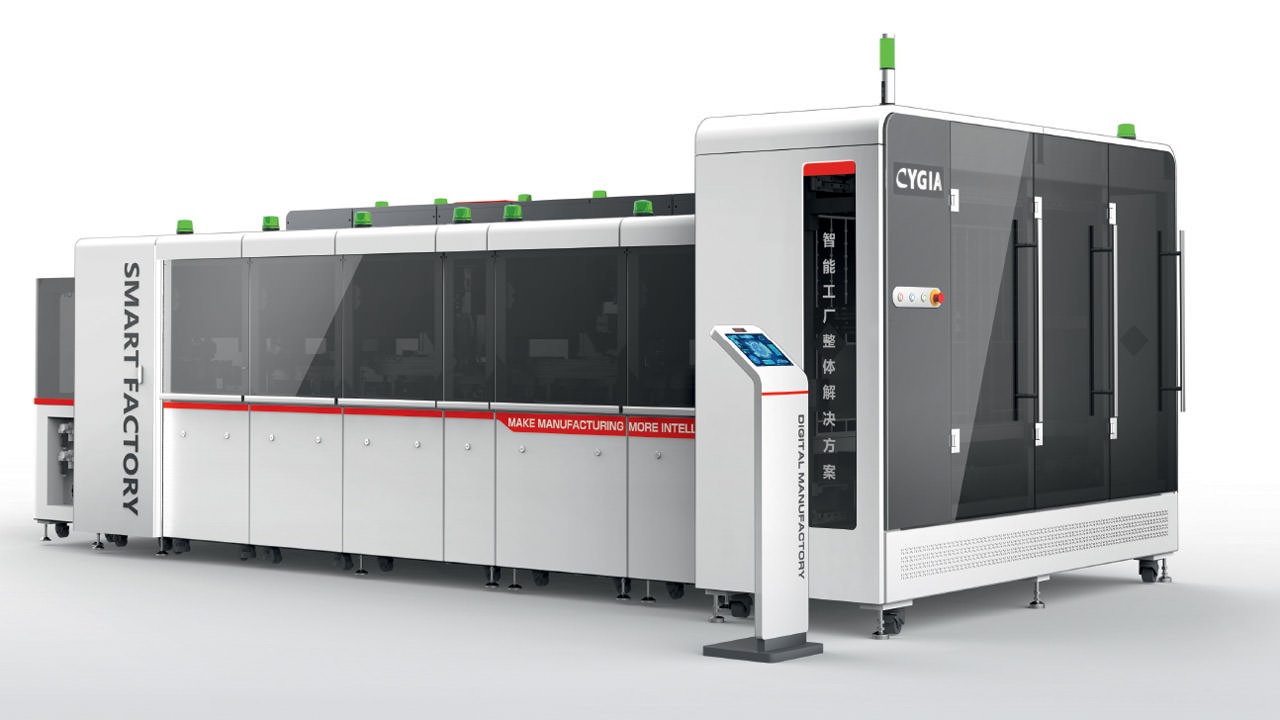
Advancing the smart factory with PC-based control technology, electronics companies are developing platforms with unified interfaces as part of a flexible manufacturing strategy. Intelligent networks combine multiple users and machines with a range of advanced services.
Two companies in China, CYG Intelligent Automation Co., Ltd. (CYGIA) and CYGDM, have used PC-based control technology to develop a smart factory platform with unified interfaces and protocols as part of a new and flexible manufacturing strategy for electronics products. The platform combines sensors, actuators, operator terminals, control systems and communications equipment in an intelligent network that connects multiple users, including humans with machines, and machines with services.
From an Industrie 4.0 perspective, the platform maximizes integration, both at the device level and at the vertical and horizontal production levels.
Formed in 2006, CYGIA is one of China’s foremost high-tech companies. Its business is customer-specific automation and test solutions for industries such as consumer electronics, semiconductors, automotive, energy, medical engineering and lighting technology, among others.
CYGDM, founded in 2015, is a software and hardware services vendor specialized in developing and implementing smart factory solutions. Examples of projects include the ALC line control system, the iSPC smart data analytics system, and smart warehouse management and logistics systems.
Open control for smart factory
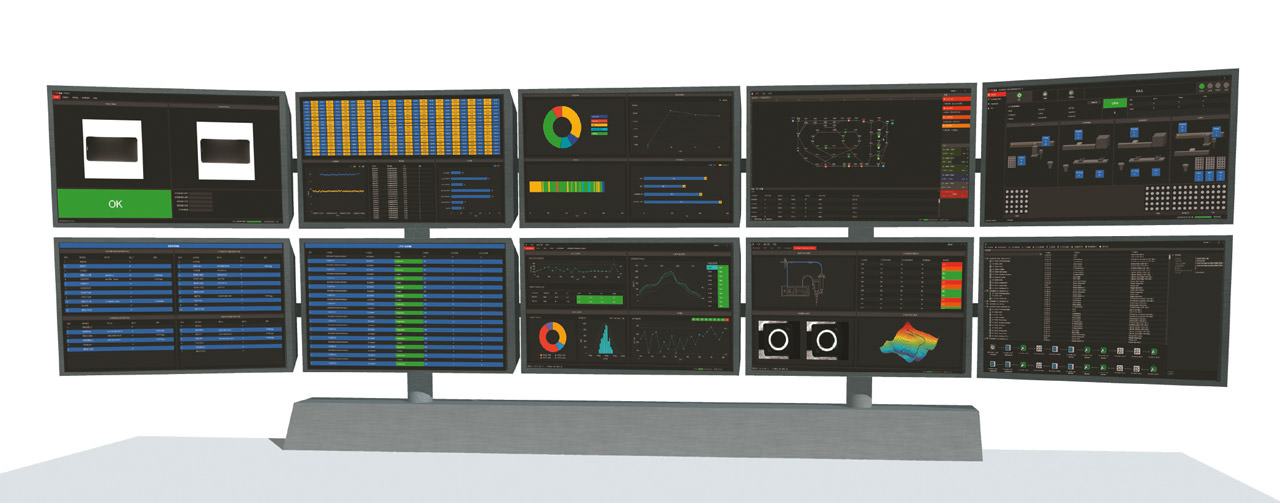
Information displayed on the central control platform’s HMI.
CYGIA’s smart factory solution utilizes IoT and monitoring technology to facilitate information management, to track the production process better, to reduce manual intervention on production lines, and to streamline production planning. Other technologies deployed as part of the solution include simulation, multimedia, and augmented reality.
CYGIA and CYGDM chose powerful CX2030 and CX9020 Embedded PCs from Beckhoff to deliver the requisite computing power.
The CX2030 handles higher-level hub control in the smart factory, while the CX9020 is used as control platform for distributed sub-stations. The open architecture of PC-based control, combined with ultra-fast EtherCAT communication technology, meets all their requirements when it comes to keeping response times as short as possible, while at the same time supporting time-division multiplexing and multitasking, programming in high-level languages, and extensive data storage capacity.
On the software side, the integration of the Beckhoff TwinCAT 3 automation software into Visual Studio is a key benefit for CYGIA’s experts. In their view, the standardized bottom-layer control platform, created in TwinCAT 3’s object-oriented development environment, combined with the upper-layer control platform developed in .NET, has made it easier to integrate a wide variety of devices and to shorten the time required to develop their smart factory solution.
Plus, being able to develop the software on a modular and distributed basis, they say, results in greater software efficiency while minimizing development and maintenance costs.
In the higher-level control system, they use both ADS.Net components and the Dynamic Link Library (DLL) to implement asynchronous communication between the server and multiple clients.
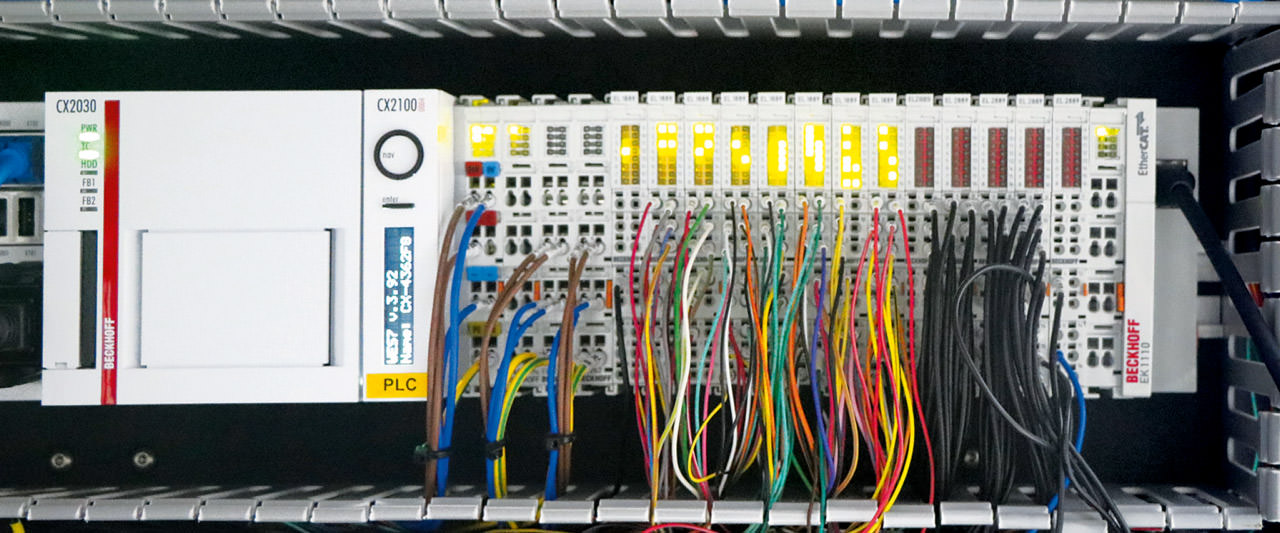
The CX2030 Embedded PC (left) that serves as the main controller for the automated production line.
The entire communication architecture, they claim, not only saves time, it is efficient and compatible, too. In addition, the TwinCAT Automation Interface enables developers to program device interaction using COM technology.
With TwinCAT, CYGIA’s engineers can use a unified, object-oriented, modular program framework, Structured Text, object-oriented programming and customer-specific libraries, all of which help streamline the development of this complex system. Joshua Wang, R&D Director at CYGIA, explained: “We’ve succeeded in improving programming efficiency through modularization and standardization. We only need to modify a few methods when developing new production technologies. The program may be large and complex, but we can reuse the code efficiently, nonetheless. The program has a clear structure, is easy to read, and is highly portable.”
It makes the most of TwinCAT 3’s built-in capabilities for system configuration, PLC code development, motion control configuration, bus and module configuration, and HMI development, as well as its oscilloscope functionality. And the program structure, process control, data structure, alarm release and security control have all been standardized as well.
Smart mobile phone production
The software and hardware fulfilled CYGIA’s requirements for smart solutions in electronics manufacturing.
Compared to a conventional setup with separate production stations, CYGIA’s system can achieve greater manufacturing and supply-chain flexibility and improve capacity utilization. For instance, it enables the ERP, MES and monitoring systems involved in the manufacture of mobile-phone circuit boards to exchange data, resulting in comprehensive process automation that spans everything from order booking and handling, material distribution, product manufacture and inspection to packaging, warehousing, logistics and transportation.
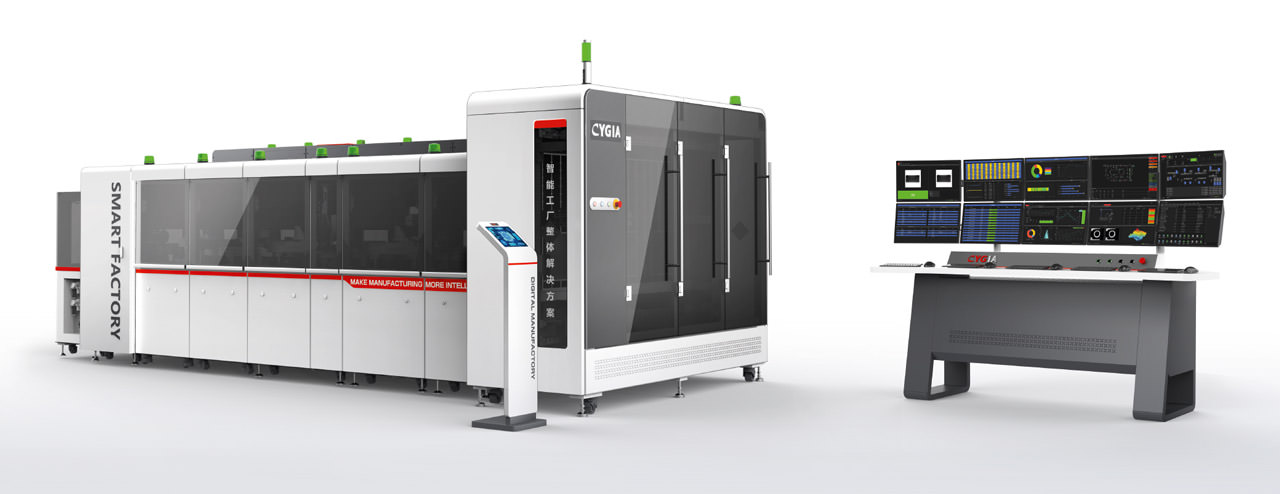
CYGIA’s smart factory solution for electronics manufacturing utilizes IoT and monitoring technology to facilitate information management, to track the production process, reduce manual intervention on production lines, and to streamline production planning.
The smart factory’s system architecture combines order, asset and quality management functions with a management dashboard, inventory control and product traceability.
The intelligent warehouse assigns codes to all goods and creates unified racks and pallets that are carried by forklifts or shuttles into the intended positions. Each storage location is controlled by the warehouse management software. Product locations, inventory levels, open storage locations and storage strategies are all administered through a parameter management system.
The CX9020 Embedded PC is the core element in inventory control, running the PLC program, connecting to the local MES over TCP/IP, and operating as an NC controller for material requirements planning. It also connects with the extended part of the feed and removal mechanism, in a chain topology, via an EK1110 EtherCAT extension.
The main elements in the automated production line include hollow-board printing, surface mounting, reflow welding, dispensing, screw locking, automated optical inspection, integrated and functional circuit testing, and packing and unpacking.
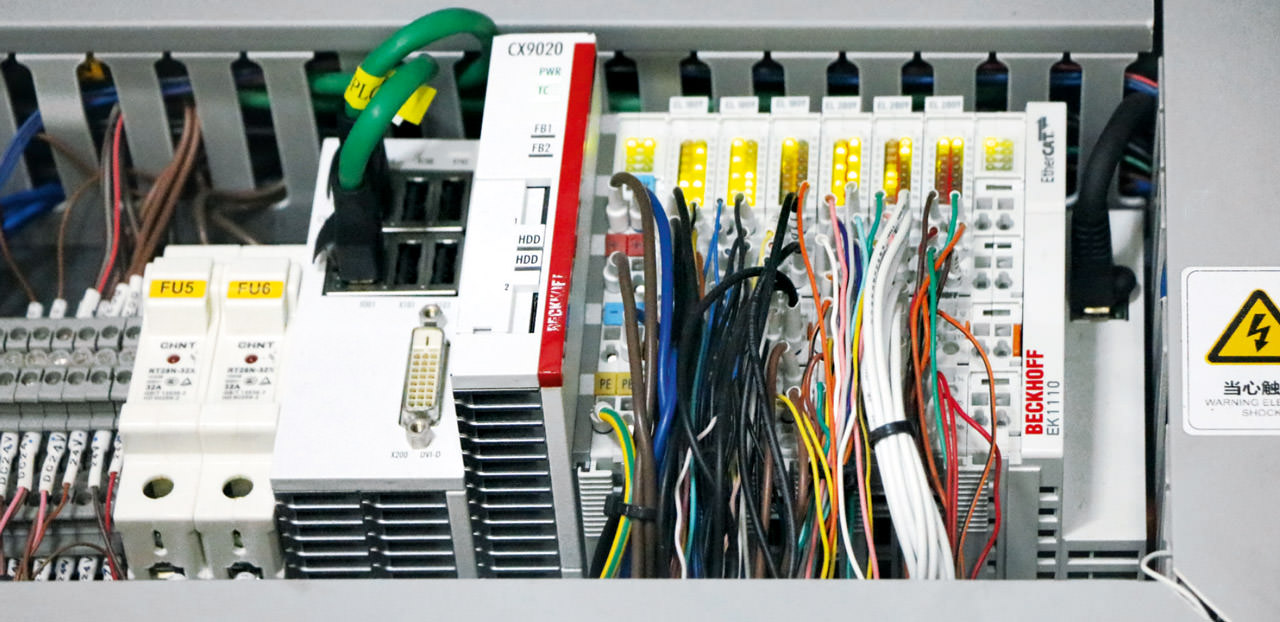
The CX9020 Embedded PC that controls the smart warehouse.
The line has three CX2030 Embedded PCs in total, which communicate at extremely high speed with the higher-level central control system and are essential to ensuring efficient production and precise fabrication of semiconductor components.
The master CX2030 runs both the PLC program and the motion control and HMI software. It also sends data bidirectionally at high speed between the control system and the MES over TwinCAT TCP/IP (TF6310), and controls the printing, surface mounting and reflow welding processes.
Here, TwinCAT PLC/NC PTP 10/NC I (TC1260) provides full motion control functionality that can dynamically position 20 EtherCAT servo axes per machine. The NC I interpolation function serves to achieve smooth, steady, coupled movements on two axes and to control the arc-welding process.
The second CX2030 Embedded PC runs PLCs, motion control and HMI software, handles communication over TCP/IP, and exchanges data with the ALC line control system. It also receives instructions from the MES over TCP/IP to run tests and execute packing and unpacking processes.
It can also flexibly configure ten EtherCAT servo axes through a synchronization device that can switch quickly and efficiently between specific test environments for different products. The third CX2030 handles PLCs, motion control and HMI software, and in addition controls a high-resolution TCP/IP camera for optical inspection.
EtherCAT networking performance
CYGIA chose EtherCAT as a high-speed communication system to ensure fast, precise transmission of sensor signals. The company runs master communication on its automated production line over EtherCAT in a star topology. Slave devices are easy to connect, which simplifies management, maintenance and expansion. A line topology is used at sub-station level to keep the wiring as simple as possible.
According to Jianming Huang, a senior electrical engineer at CYGIA: “The EL1809 and EL2809 HD EtherCAT terminals are not just highly compact and inexpensive, they operate on multiple channels and can be configured flexibly for different topologies. They also support offline configuration and Hot Connect groups, which makes them much easier to set up. In addition, EtherCAT provides a wide range of useful information, such as diagnostic codes, diagnostic types, text IDs and time stamps. This helps to locate and fix master-slave communication outages potentially caused by EMC disturbance, cable damage or equipment faults. This makes maintenance much more efficient.”
Future development potential
CYGIA’s aim with its smart factory solution is to integrate assembly and manufacturing units for discrete electronic components within a unified production system. Other goals are to connect production plants, to visualize production data, to make production processes transparent, and to create fully automated production sites.
Given the broader trend toward Industrie 4.0, CYGIA also needed smart factory software that would enable access to a wide range of data resources, including cloud computing, big data, and IoT.
With TwinCAT 3, Joshua Wang has found the right solution and is now looking forward to the new production model the company has lined up: “We’ll gradually incorporate TwinCAT 3 functionality to support big data analysis, IoT advancements, and machine vision in future upgrades. Going forward, this will further enhance the setup of this hybrid control system to fully exploit the benefits of cloud data storage and distributed data interaction.”
Kevin Gao, Technical support engineer, Beckhoff China.