ApplicationsSeptember 22, 2019
Variable frequency drive design simplifies smart manufacturing
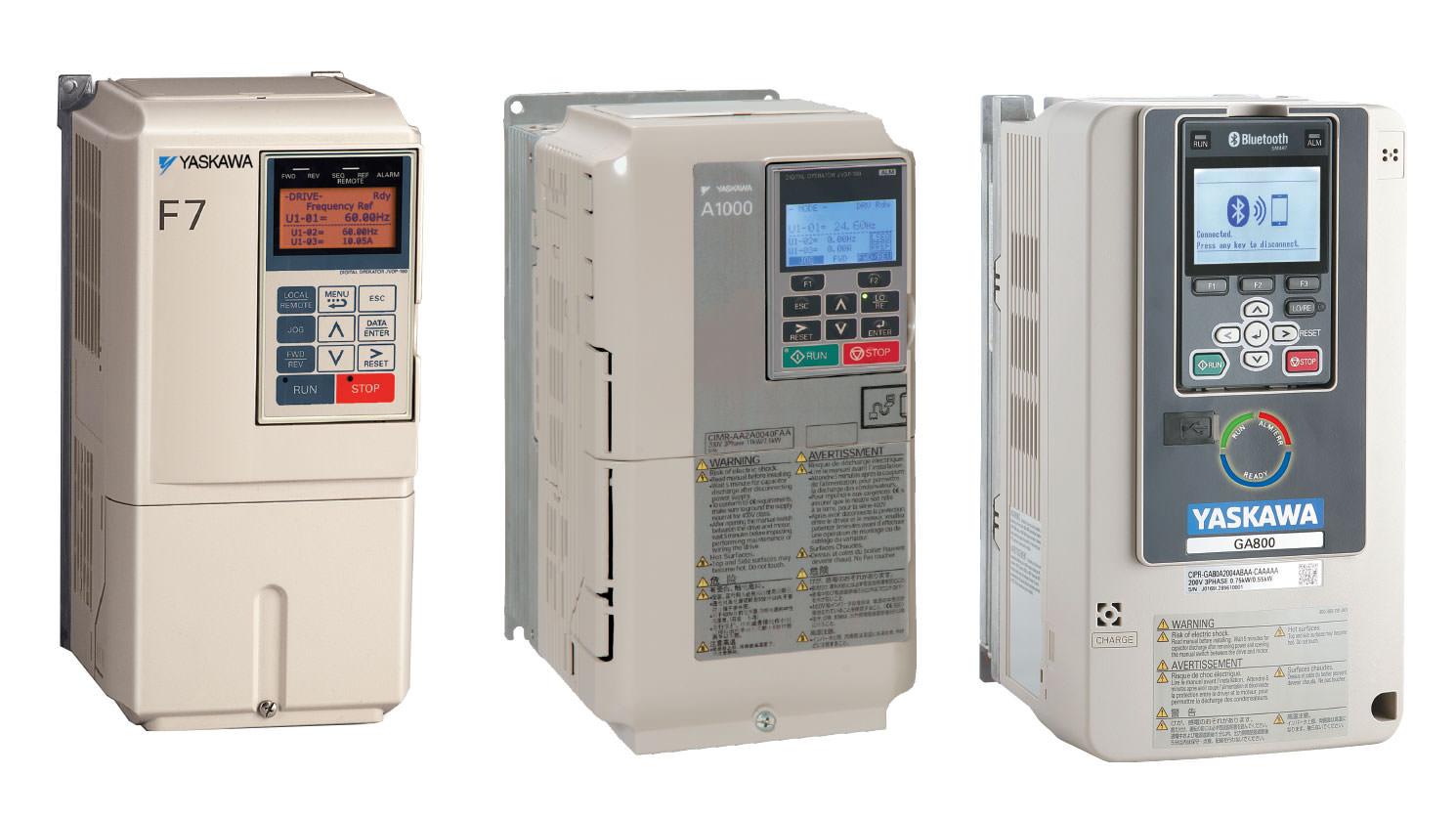
Variable Frequency Drives (VFDs) store a plethora of information that can be easily accessed. Regardless of the connection method, traditional fieldbus or Industrial Ethernet, the main objective can be to retrieve that production data and use it to create information that helps transform and drive business strategies.
Pick the term that suits you best for the fifth industrial revolution – Industrial Internet of Things (IIoT), Industrie 4.0, and Smart Manufacturing are just to name a few. When you dig deep into each term, they all vary slightly on what they mean and the pathway to the fifth industrial revolution. But if you take a high level view of all different terms, they all revolve around three things: (1) connectivity of industrial devices; (2) acquiring data from industrial devices, and most importantly; (3) using the data to drive your strategy.
Connectivity
When it comes to discussing connectivity, it mainly revolves around connecting a device to an Ethernet network. One of these industrial Ethernet protocols could be PROFINET, EtherNet/IP, Modbus TCP/IP, or EtherCAT to name a few. But if you take a look at the machines in your facility, you might discover that there is a lot of installed equipment that either do not support or cannot be made to support any of these protocols.
The thought of getting your plant to partake in the fifth industrial revolution has suddenly become an overwhelmingly daunting task, because of all the various devices on your machines that will need to be changed out and the capital that is required to make this all happen. However, this type of mindset is like trying to eat the whole elephant in one sitting.
In reality, you may already have things in place that can get you moving in the direction that you’re trying for, i.e. eating the elephant in small sizeable chunks over a period of time (sorry to elephant lovers that may be offended by the analogy).
One step is taking a look at the devices that are currently installed on your machine. Of primary interest would be if your machine has a variable frequency drive, or VFD, installed. A VFD is responsible for the prime mover, i.e. motor, that is used to run your machine. Its ability to vary speed of machines through electrical means has allowed machines to have fewer mechanical components, hence less wear component to worry about.
Its inherent energy saving capabilities are an added bonus. But when it comes to the fifth industrial revolution, a VFD can provide a plethora of information. It’s just a matter of accessing all the information and putting it to use. A VFD that has an embedded protocol like Modbus RTU installed can take advantage of that with no additional cost. It would just be a matter of adding a Modbus RTU master that can be used to retrieve the data from the VFD. Or perhaps your machine was already designed using an existing fieldbus protocol like PROFIBUS or DeviceNet, in which case you’re already connected to a network and the ability to gather more data is available.
Data
As mentioned previously, a VFD has a plethora of information contained. Regardless of the connection method, traditional fieldbus or Ethernet, the main objective is to be able to pull that information out of the VFD and be able to use it to your advantage. One such example is reading the VFDs output current.
When read instantaneously, the output current from the VFD could provide information on whether or not the machine is overloaded due to the process or a mechanical failure that is present. But if the output current is recorded and monitored over time, the data could be analyzed to provide deeper insight into the machine. If the operating current has steadily increased over time, this could indicate that there are mechanical components that are starting to wear and will eventually fail. With this information, you can proactively plan to change out the offending components at the next scheduled downtime, or face costly downtime if the component fails while in operation.
In addition to being able to implement preventative maintenance measures, another large advantage is being able to analyze and correlate different pieces of data to achieve different objectives. Perhaps you want to be able to maximize how efficiently your machine is producing a component (i.e. energy used per part). Recording the power output of a VFD over time and the number of parts produced, which would be a data point from a different part of the machine, you can achieve a quantitative value. This will allow you the ability to experiment and vary the throughput of the machine to find this value. Or perhaps you are trying out a new process and want to get insight on how the machine reacts to the new process. Being able to read various data points from the VFD like current, output frequency, output power, plus other values from sensors that are mounted on the machine, can give users a bigger picture look and determine if additional tweaks are needed or not.
Getting your factory to join the fifth industrial revolution shouldn’t be a daunting task. Taking a careful look at what you have available and taking on various tasks as small chunks will go far. You may be surprised to find that you already have things available to help you along the way. Perhaps it is a VFD that isn’t currently connected to a network, but can easily be put onto a network using the embedded protocol, like Modbus RTU. Or perhaps an existing fieldbus is already in use. It’s just a matter of taking advantage of this. You might be surprised by how quickly and easily it is for you to join IIoT, Industrie 4.0, Smart Manufacturing … pick a term.