ApplicationsDecember 7, 2020
Process device diagnostics leverages NAMUR NE 107
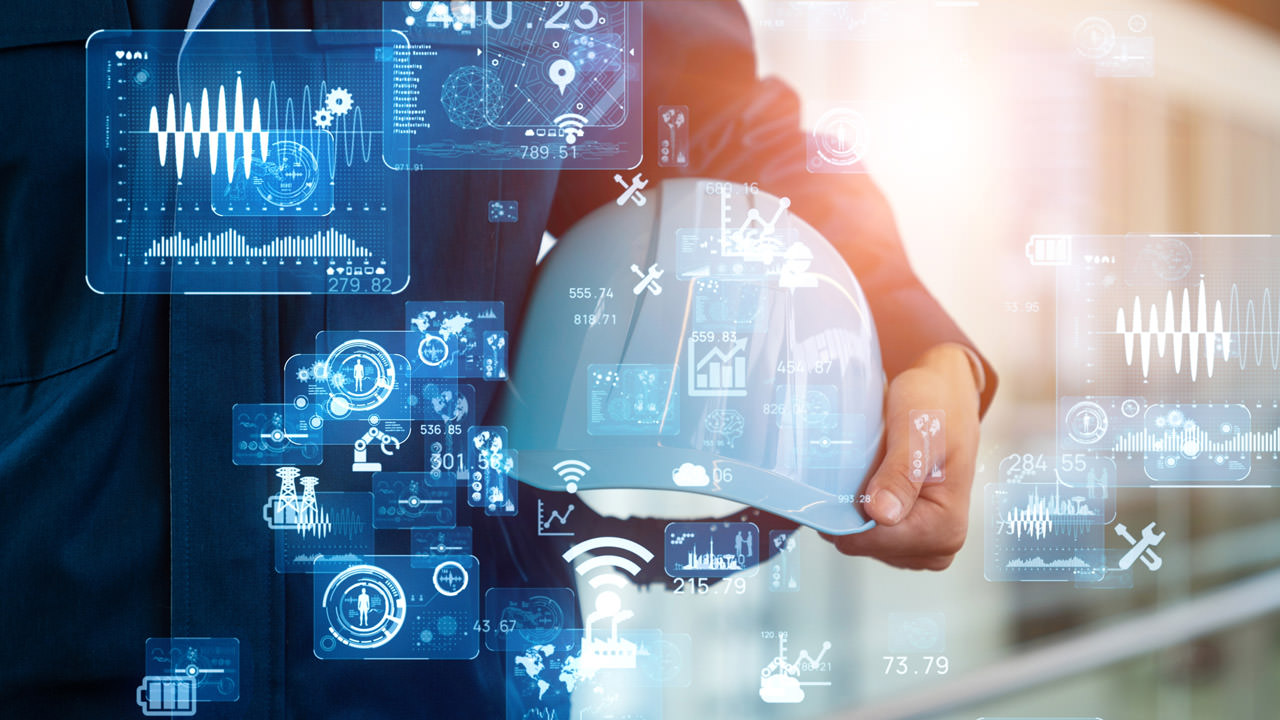
The goal of NAMUR NE 107 diagnostics is to limit downtime and increase plant performance. An effective Process Device Diagnostics Object implementation can help improve process plant maintenance, and provide an expanded set of tools for service technicians, operators and application programmers.
Industrial Ethernet protocols in the present technological marketplace have become more significant with the application of IIoT concepts for the improvement of process responsiveness and efficiency.
EtherNet/IP based on the Common Industrial Protocol can contribute to the application of IIoT by improving connectivity, efficiency, scalability, time and cost savings for process industrial organizations.
The Process Industries SIG (Special Interest Group) added in 2019 the Process Device Diagnostics Object to ODVA’s Common Industrial Protocol. Based on the device’s current diagnostics and the NE 107 status (NAMUR), the Process Device Diagnostics Object through the asset controlling and monitoring will bring simplicity, precision and rapidity of execution to the different stakeholders including application programmers, operators and field technicians.
The Dark Ages
The control of fire by early humans was a turning point in the cultural aspect of human evolution. Fire provided a source of warmth, improvement on hunting, cooking food, protection and security. Before this discovery, as soon as the sun set, humans had security issues.
Nowadays, after thousands of years of fire control and technological development, humans are still unsafe in a dark environment. This unsafe state can be viewed in different environments. Being unsafe takes from man the precious thing he has, his freedom. The industrial environment is full of dark spaces, mysterious, and dangerous places. Human eyes are not able to see inside a pipe or to know the status of an electronic card.
The industrial environment plunged humans back into the dark ages. The name black box was not chosen by accident; it is a system which can be viewed in terms of its input and output yet still remains mystical to the majority of people. Some industrial installations are seen as a black box. Many cables, sometimes without denominations, and electrical plans updated without documentation, can really cause confusion. For a field technician, the service continuity has the highest level of priority and, as a result, any incertitude must be minimized.
John is our field technician; he is our eyes on the field side and will inject a little humanity into this article. John is in charge of keeping the plant in a safe state, far removed from the possibility of any downtime. Having downtime in a plant is the worst situation John must face and we are doing our utmost to help him to avoid this occurrence.
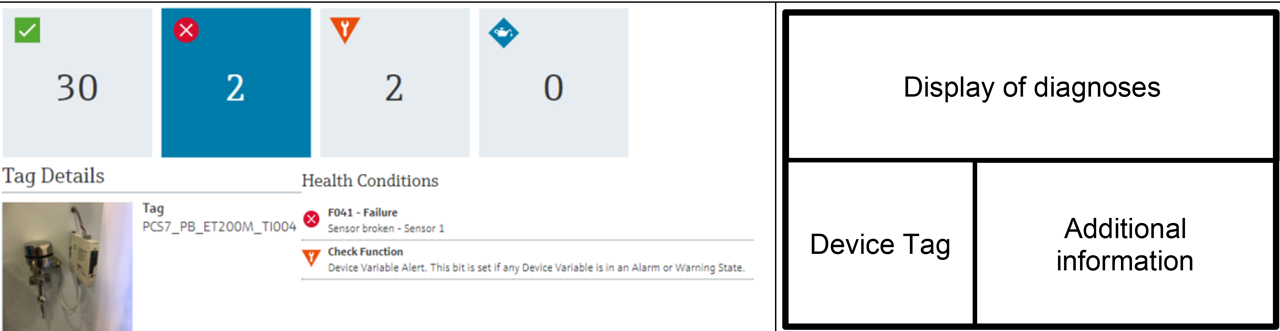
Simple and straightforward NE 107 application in a well appreciated monitoring system.
Problems in the field
The wide range of activities John has includes, an automation project, installation, commissioning, troubleshooting, calibration, and servicing, which is one of the most time and energy demanding. Field technicians like John in the current process industries have a wide repertoire and are required to do many different tasks with regards to automation. One of the main problems a field technician has to deal with is the diversity of activities.
There are always fewer technicians in the field, less specialized, and the fact that they need to deal with most of the portfolio and multiple vendors means that more training effort is required.
The main goal a field technician has is to maintain the functional state of the installation, which means keeping the process running and avoid downtimes. In order to avoid downtimes maintenance technicians stick to effective maintenance principles like:
- keeping equipment in good condition;
- developing programs to carry out its services;
- perform quality work;
- anticipate and prepare for future work;
- achieve continued improvement
In addition, these responsibilities include preventive maintenance, predictive maintenance and many more principles.
Preventive maintenance
Preventive maintenance may include service contracts, inspections, cleaning activities, testing, lubrification efforts, and scheduled shutdown service. Inspection is the most significant activity a service technician has, and it should lead to early detection.
John: “inspection looks like a waste of time, it brings us back to the beginning of the previous century.” John is, unfortunately not a good candidate for this inspection. Most of us agree with him, our eyes don’t have the ability to see inside the process, inside the field devices.”
John: “the visual inspection is quite limited because of the miniaturization and the increase of hidden elements”.
Predictive maintenance
Predictive maintenance may include vibration analysis, shock pulse methods, ultrasonic, thermographic analysis and much more to monitor and detect changes in condition to allow more precise intervention. John: “I would like to be able to anticipate earlier when the measurement devices might require servicing.”
The number of sensors, actuators constituting an installation is always higher and always more digital and seem like a Blackbox. The more visibility the technician has, the more freedom and time he will have to develop and improve the performance of the installation.
Downtime
John: “When you think that everything is under control then it suddenly happens”.
Downtime is, by definition, very short stoppage in production but in fact, extremely time-, cost-, and energy- demanding. The sources of downtime are many and result from a series of small, undesirable events.
Downtime and chain reaction
A chain reaction that happens, for example, in chemical process, is when elements have an impact on another element and so on. It is exactly what happens under control in an atom reactor and in an uncontrolled way with a nuclear weapon. An industry has a lot of systems, sensors, and actuators that influence each other and exchange information.
A sequence of undesirable reaction can also happen in this context. When a sensor or an actuator goes in default mode and delivers wrong information, the system can absorb it and continue the production process. However, the field technician must be informed, otherwise this could slowly damage the installation. In addition, if one more sensor or actuator goes to default, the system has good chance to generate a chain reaction and the issue will be the downtime of the installation.
The main point is the financial cost a downtime generates:
- Cost of time
- Cost of repair or replacement of a faulty piece of equipment
- Cost to clean
- Cost of any injury to workers as a result of equipment failure and during the troubleshooting resolution.
It is vital to a plant’s survival to minimize the possibility of downtime. A second aspect is more psychological. Downtime is considered as failure for the team, and is the result of the incapacity to structure and to maintain the production process in a safe state.
No diagnostics, no visibility
Visibility and diagnostics are linked and are going to help the field technician to keep his main goal: “keeping the installation in a state in which the production operator can achieve the production output goals”.
In the past, visibility in a plant was purely visual, nowadays with the IIOT development, visibility is linked with the ability of a field sensor to deliver the right information at the right moment.
Everyone knows what diagnostic means and the best example is the medical diagnostic. The medical diagnostic is the process of determining which disease or condition explains a person’s symptoms and signs. If translated into industrial jargon, it is the ability of a device to generate the performance and health status of all its components e.g. sensor elements, senor electronic, process connection.
John: “Nice 4…20mA analogic output also give the status, means the device is working, or the device needs to be replaced.” Analog transmitter output goes to a defined level above 20mA or below 4mA and that the system triggers alarms. When the alarm triggers, it is already too late. More detailed information could help us to avoid this critical situation.
The 4…20mA diagnostic happens during the downtime of the system and need a production stop to bring the process back into a working state.
Modern medicine is the best solution when a healthy person becomes a patient. Digital solutions are going to keep a field sensor healthy and are not science fiction. It is what happens in a plant with intelligent devices.
However, with 4…20mA, the rudimentary diagnostic solution had two main advantages: first it was standardized and second the action after the alarm signal was quite simple, it didn’t need interpretation.
Well-engineered systems are keeping the advantage of the previous technologies and are improving it. 350 is the number of pieces of status information an intelligent device can generate. Quantity versus quality is the first idea that crosses the mind of each developer when he sees this amount of information. The volume of information needs to be managed and standardized to get the benefits. In addition, an intelligent device can fail or degrade in many ways, resulting in hundreds or thousands of different diagnostic error codes.
Steven is a charge of the production performance, he’s transforming input-based product to output commercial goods in a defined time base.
Steven:” My monitoring screen always has more information. I need a simple message. I do not need details”. The operator needs to know if the measurement of the field device is valid or not.
Operators and field technicians don’t have the same requirements. A field technician needs more details than the process operator. Both need standardized and mapped feedback from the field device.
Namur NE 107 Diagnostics
The operator needs to inform the field technician in a short time when something goes wrong in the plant. To achieve this important transfer of information, a standardized way is required. In addition, from the field technician perspective, status information with probable causes and recommended actions could be appreciated.
NE 107 illuminates the plant and keep operators and field technicians out of the dark.
NAMUR NE 107 harmonizes status signals across all kinds of devices. NAMUR NE 107 is the ideal choice to satisfy requirements from the operator and the field technician`s perspective. NE 107 includes continuous monitoring of the internal variables to communicate alarms when internal self-diagnostics detect problems. Early warning results of degradation detection provides precious information to the field technician and helps him to plan daily maintenance and turnarounds.
NE 107 is the perfect bridge between operators and field technicians. Diagnosis through the NE 107 structure is going to avoid downtime and increase plant performance.
The four-status signal proposed by NE 107, in addition to the fast communication of EtherNet/IP, is an obvious benefit for each stakeholder, operator, field technician and much more. In one overview, all status information is available.
Displaying the NE 107 information is one part of the information. Additionally, correct descriptions, data mappings and remedies are functions a field technician and an operator would like to have. Mapping is the action to link the field sensor information with the NE 107 status signal.
In fact, field technicians always spend less time in the plant, self-control is more than needed especially when it is time to resolve an issue. Although the remedy instruction will never replace having a colleague, it is an important support for the field technician.
This NE 107 helps the operator run and supervise the process continuously. NE 107 also helps the maintenance technician keep the plant running (e.g. field devices) by performing reactive, scheduled, condition-based maintenance activities and fixing the issues. However, the brain of the process and the stakeholder in charge of the implementation is the application programmer.
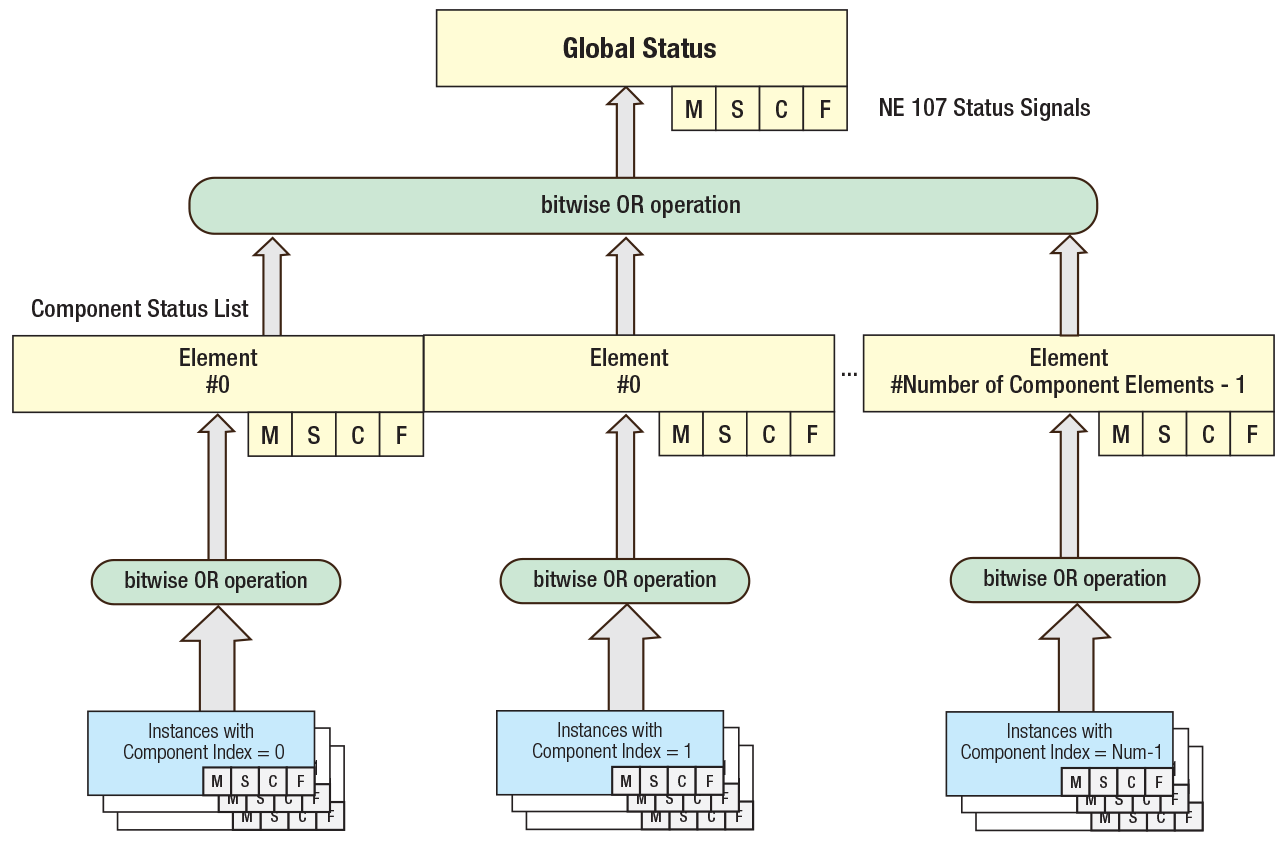
From the instances to the Global Status of the device.
How to implement
The better the communication between the operator, the field technician and the application programmer, the better the performance of the plant will be. The operator’s needs are different from those of the technician. Stanley our application programmer should have that in mind, as it is the key to customer satisfaction.
The diagnostic implementation has a lower priority than the process implementation. For Stanley: “In my implementation work plan, the diagnostic implementation has the last priority. It needs to be fast, out-of-the-box”. To help Stanley, the NE 107 implementation should be sure, easy and standardized.
The Process Device Diagnostics Object developed by The Process Industries SIG will provide the expected standardized structure that Stanley needs. Attributes and methods standardize the way to implement NE 107 and allow more time for kernel functions. Stanley’s kernel function is to adapt the diagnostic display to the customer specification. It could be more operator oriented with, for example, the Failure status or/and more field technicians, in addition to the Maintenance Required status.
Stanley: “The structured and easy to use Process Device Diagnostics Object should definitively accelerate my implementation. I could be more focused on the way to display the diagnostic. In the past, I spent 80% of my time on the diagnostic identification and 20% on the display of diagnoses, nowadays with the Process Device Diagnostics Object, it is quite the opposite.”
The problem of collecting the diagnostic data is solved with the Process Device Diagnostics Object which enables access to the current diagnostics information of a field device of any vendor.
Let’s help Stanley understand how to perform his control system with the Process Device Diagnostics object. The Process Device Diagnostics Object, like each CIP object, has a class code, in this case 0x108, class attributes, instance attributes, common services and specific services.
For Stanley, the first goal is to get Global Status for his field device. The Global Status is a logical combination of all generated diagnostics. The possibility to get the status of selected elements for a selected channel for a field device is also provided by the Device Diagnostics Object. Diagnostics are not hidden or unreachable data; Stanley also has the possibility to read this information with the Device Diagnostics Object.
Stanley understands that Elements for field devices are channels. Channels like a temperature channel for a Temperature sensor. Stanley would like to know what is behind the concept of instance.
The EDS File from a Flow sensor can have up to 300 diagnostic events. Stanley used to take these diagnostic events and map them. This diagnostic mapping means linking the diagnostic event from the EDS file and converting it in NE 107 diagnostic which took a lot of time to develop. With the Diagnostic Object these diagnostic events are represented and structured in instances.
Two types of instances are defined in the Diagnostic Object:
- Profile Diagnostics Instances, which are specified in the Device Profile Object. The Profile Diagnostics Instances guarantees Stanley that all vendors are going to follow the same data structure.
- Vendor Diagnostics Instances, which are specified by vendors. Vendors with more specific diagnostic events have the freedom to add them into the vendor diagnostic instance.
Stanley needs to re-map diagnostic codes, a special attribute named User Diagnostic Groups, which are available in the Diagnostic Object for that use case. For example, Stanley could map an over-range and an under-range condition to the same “out-of-range” bit.
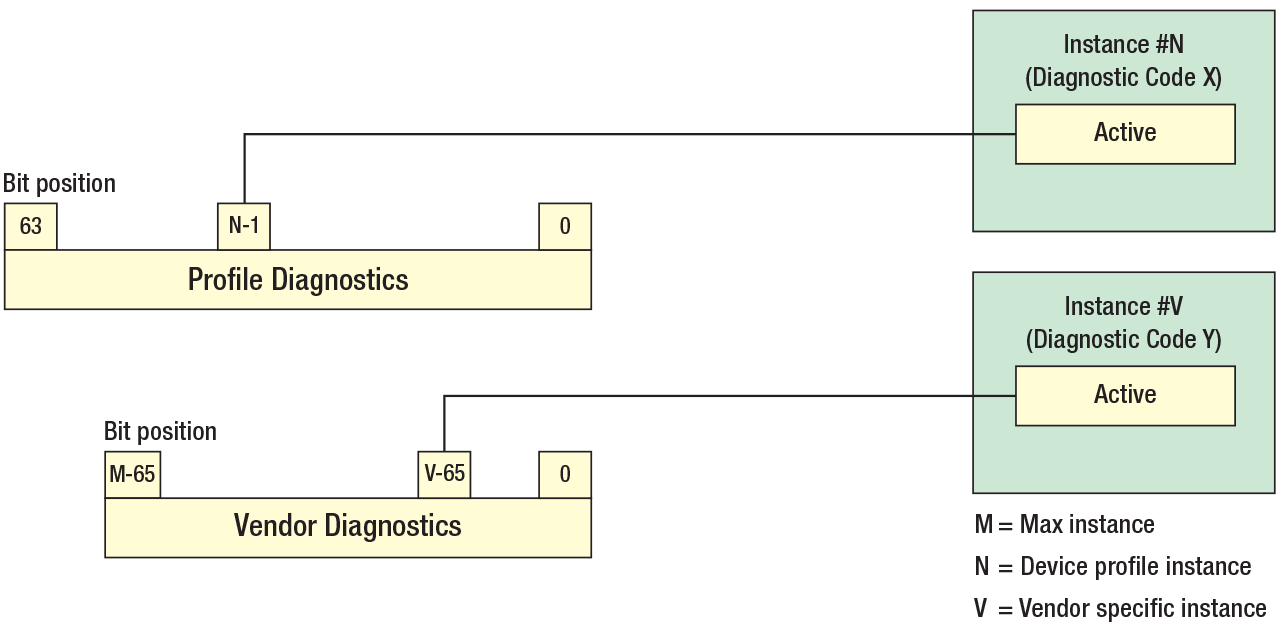
Two types of Diagnostics are available: Profile and Vendor specific.
The class attribute gives global information, the first piece of information that appears to Stanley is the Global Status. Instance Attributes are the structure that specifies diagnostic events. The diagnostic event F022 will have a Diagnostic Code: 022 and a Status Signal: F (Failure regarding NE 107 standard). Stanley also has the possibility to activate or deactivate instances, or in a common field technician language to activate or deactivate diagnostics. Stanley can read the diagnostic timestamp information and additional diagnostic messages like “Temperature sensor defective” to provide more clarity and flexibility to Steven the operator.
Stanley has the possibility to scan all instances (all diagnostic events). If Stanley’s purpose is to read Vendor Diagnostics, the first step will be to define the right buffer size with Size of Vendor Diagnostics. Then with the Get_Attributes_All service to get a specific Vendor Diagnostic.The diagnostic implementation is no longer a question. The application programmer with the Process Device Diagnostics Object based on NE 107 and Device integration tools are able to answer any diagnostic display requirements the customer has in a suitable and efficient time frame.