ApplicationsJuly 10, 2018
Connections add value onboard and trackside
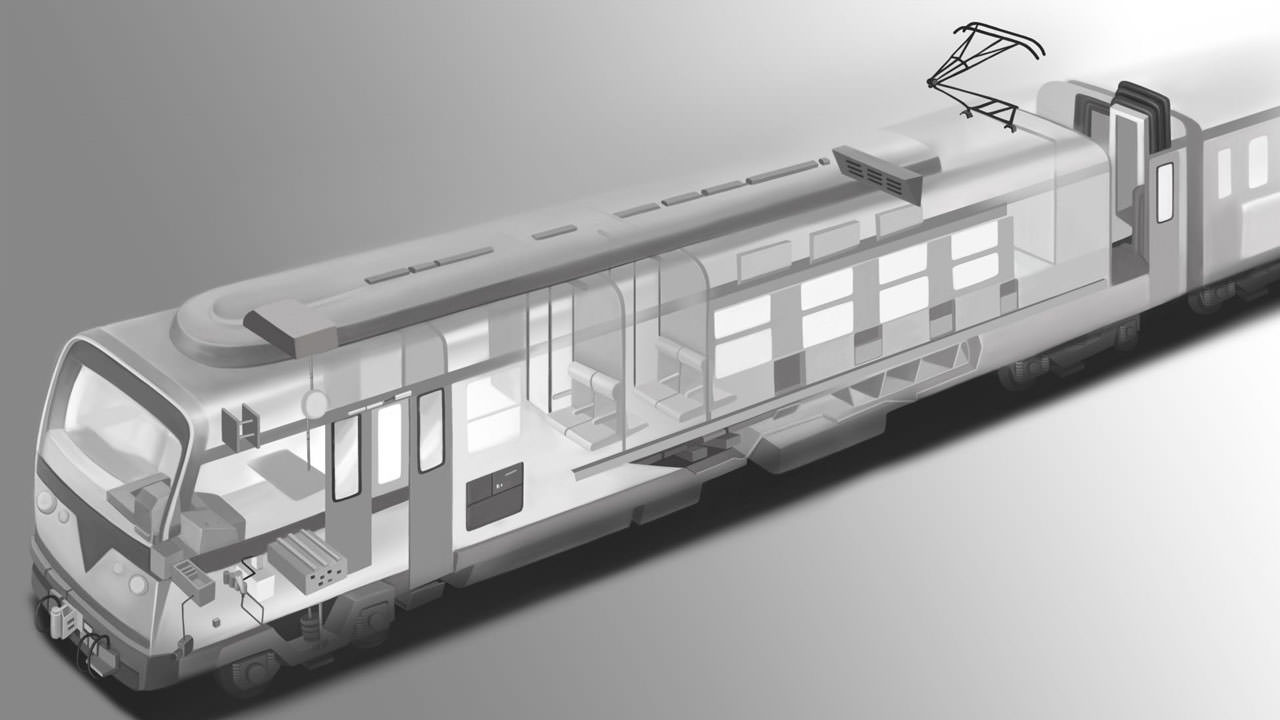
Train manufacturers have made huge strides in recent years to reduce the weight of rolling stock. One area with potential for saving weight is adopting cables with high performance thin-walled insulation. Thin wall cable is 50-100% smaller in diameter, 30-50% lighter and can offer significant weight savings.
EXPECTATIONS HAVE NEVER BEEN HIGHER for railways. Passengers and governments rely on rail transport to be fast, efficient and highly reliable. There is also a growing focus on reducing energy consumption to save costs and combat climate change.
At the same time, more sophisticated infotainment systems and web-connected condition monitoring systems are increasing reliance on data and power connections.
The next step in saving weight
As a result, railway infrastructure firms and rolling stock OEMs (original equipment manufacturers) want to do more with less. For example, train manufacturers have made huge strides in recent years to reduce the weight of rolling stock.
The reason is that up to 80 percent of a commuter train’s energy consumption arises from the regular and repeated accelerations as it pulls away from stations. Saving weight means less energy consumption for acceleration, traction and braking, as well as less load on components such as motors, brakes and tracks – reducing maintenance.
Recognising this, train operators often purchase rolling stock based on its Total Cost of Ownership (TCO) rather than its initial purchase price. TCO includes the cost of buying, operating and maintaining rolling stock – including its energy consumption.
As a result, many OEMs have already found ways to save weight and reduce energy consumption. Adopting lightweight and high value materials has saved weight, whereas regenerative braking systems and high-efficiency motors have cut energy losses.
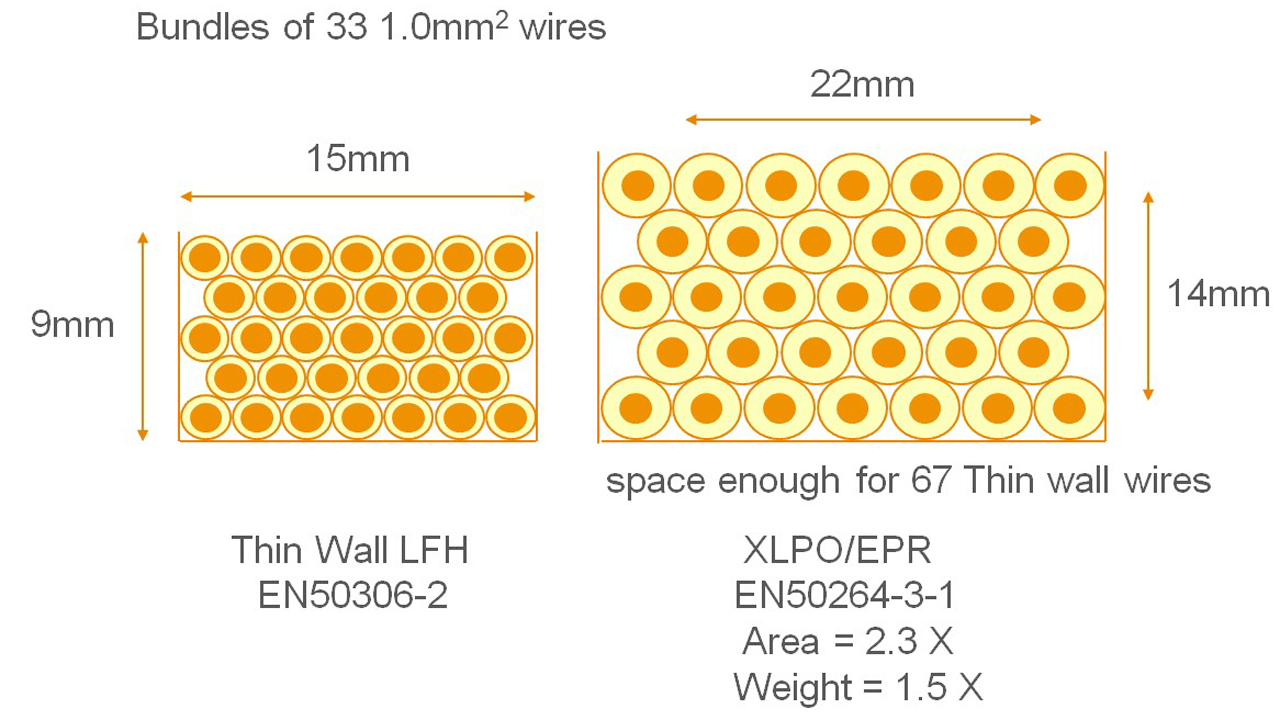
Thin wall cable is easier to handle and install. This is partly due to its being lighter and smaller, but also because the insulation material has a low surface friction that allows cables to slide past each other easily.
Rail connection solutions
One area with additional potential for saving weight is by adopting cables with high performance thin-walled insulation. Two types of rail wire and cable are available on the market. They are defined by the thickness of their protective insulation and covered by different technical standards. Thick wall cable is based on low-cost polyethylene resins mixed with additives that lend Low Fire Hazard (LFH) properties under the EN45545 or DIN 5510 standards for the railway industry.
In comparison, thin wall cable is insulated using advanced polymers. These give the same LFH properties but have fewer chemical additives. The result is a wire or cable insulation material that gives the same high performance from a thinner coating. This leads to a comparatively small cross section that meets the EN50306 standard for thin wall rail cable as well as the same standards as thick wall cable.
Thin wall cable is 50-100% smaller in diameter and 30-50% lighter and therefore it can offer significant weight savings.
An average eight-car commuter train can carry 30 km of cable, weighing 500 kg or more. Switching to thin walled cable could save half of that weight. Every 100 kg less weight saves around 36 MWh and 5 tons of CO2 over a 30-year operating life. Assuming energy costs of 10 cents per kWh, the financial saving to the train operating company would be in the region of $60k.
However, there are additional benefits to thin wall cable. Importantly, it allows smaller cable bundles. This could either create more space for passengers or allow an OEM to pack more services into an existing cable duct. This could be used to house wiring to supply power sockets at every seat for passengers to charge their devices.
In addition, thin wall cable is also easier to handle and install. This is partly due to being lighter and smaller, but also because the insulation material has a low surface friction that allows cables to slide past each other easily.
This is a significant advantage in the assembly shop, when handling of thin wall cable can be faster and safer than the thick wall alternative, especially when bending bundles to thread them into ducts.
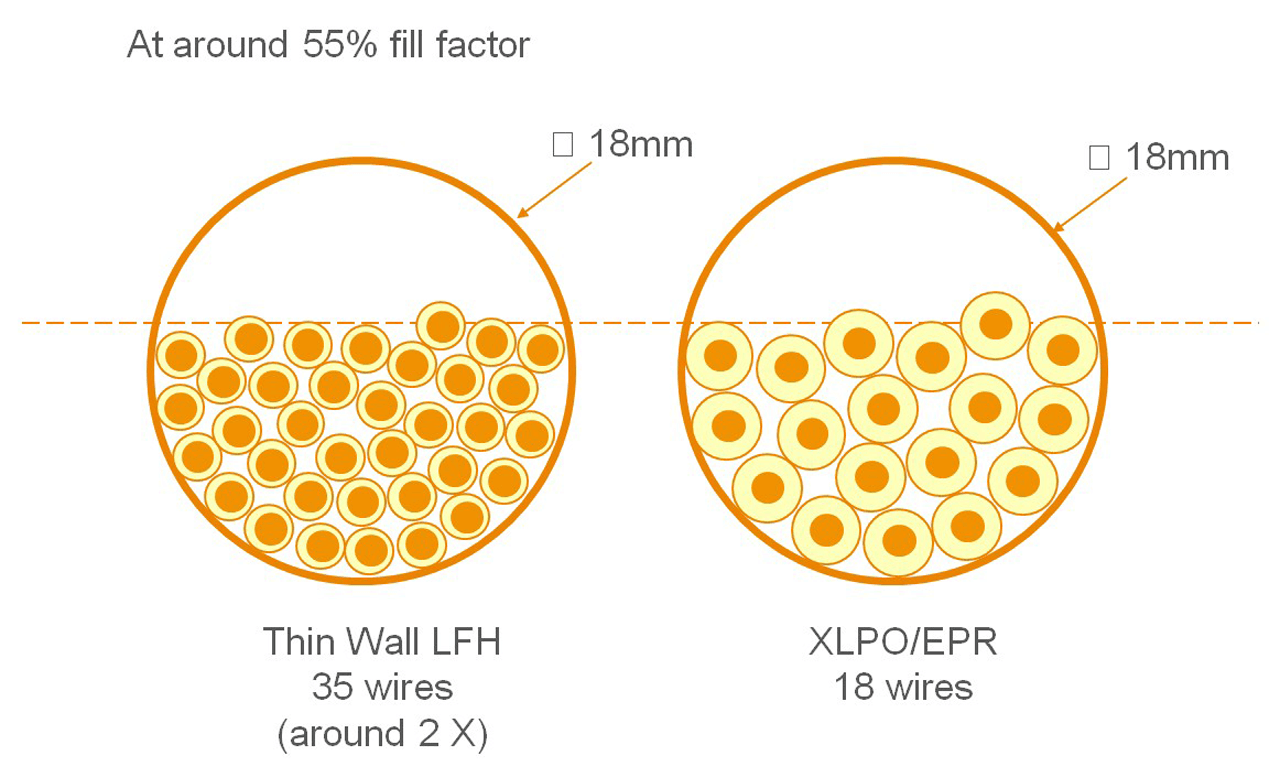
Thin wall cable creates smaller cable bundles and a much higher fill factor than alternative products.
Fast-track substation connectors
Versatile and reliable connections are also important for high-voltage trackside infrastructure. When deploying technology, TE’s engineers must often adapt their standard designs to suit on-site conditions at short notice.
One example was on France’s new LGV Sud Europe Atlantique (LGV SEA) line. The line opened in 2017 as the first high-speed rail connection on the 302 km route between Paris and Bordeaux.
As a well-established supplier of high-voltage clamps and connectors, TE had supplied its products for the project. TE’s original design complies fully with French utility specifications for a conventional outdoor substation.
However, after beginning its work on-site the installation team found that it needed non-standard products at one particular substation, which was designed in a compact format. At this site, the busbars are mounted in a horizontal position on insulator posts and this meant that the conventional contactors were not suitable. Therefore, the contractor asked TE to adapt its connectors on a fast-track basis.
With the civil engineering work already being complete the installer was keen to complete the work in time for the scheduled start of high-speed services in summer 2017.
TE worked closely with the installer to find an alternative design based on its recently-introduced SIMABUS connector. This is an innovative type of connector that was designed as a universal product to replace multiple different types of high-voltage busbar connector. Following detailed analysis, TE’s engineers designed a modular version of the connector that could be installed either vertically or horizontally without the need to adapt the supporting structure.
As the design featured standard components, TE was able to meet the customer’s requirement for fast-track delivery. Whereas the lead time for a bespoke design can be 12 weeks, the modular and standardized approach used in the SIMABUS connectors means that they can be delivered to site within weeks.
This allowed the customer to install the new connectors only three weeks after approving the proposed design. Crucially, the rapid delivery of the highly-engineered connectors avoided a delay to commissioning and financial penalties that would have resulted.
As a result, the LGV SEA line began service on 2nd July 2017, cutting the journey time between Paris and Bordeaux by more than an hour to just over two hours.
One significant benefit of opening the line on schedule is that it has freed up capacity on the French railway network for freight. As a more sustainable alternative to road and air travel, this demonstrates the role of technology in saving energy and limiting environmental impact.