TechnologyJuly 16, 2024
5G at the Intelligent Edge Creates Access to Data
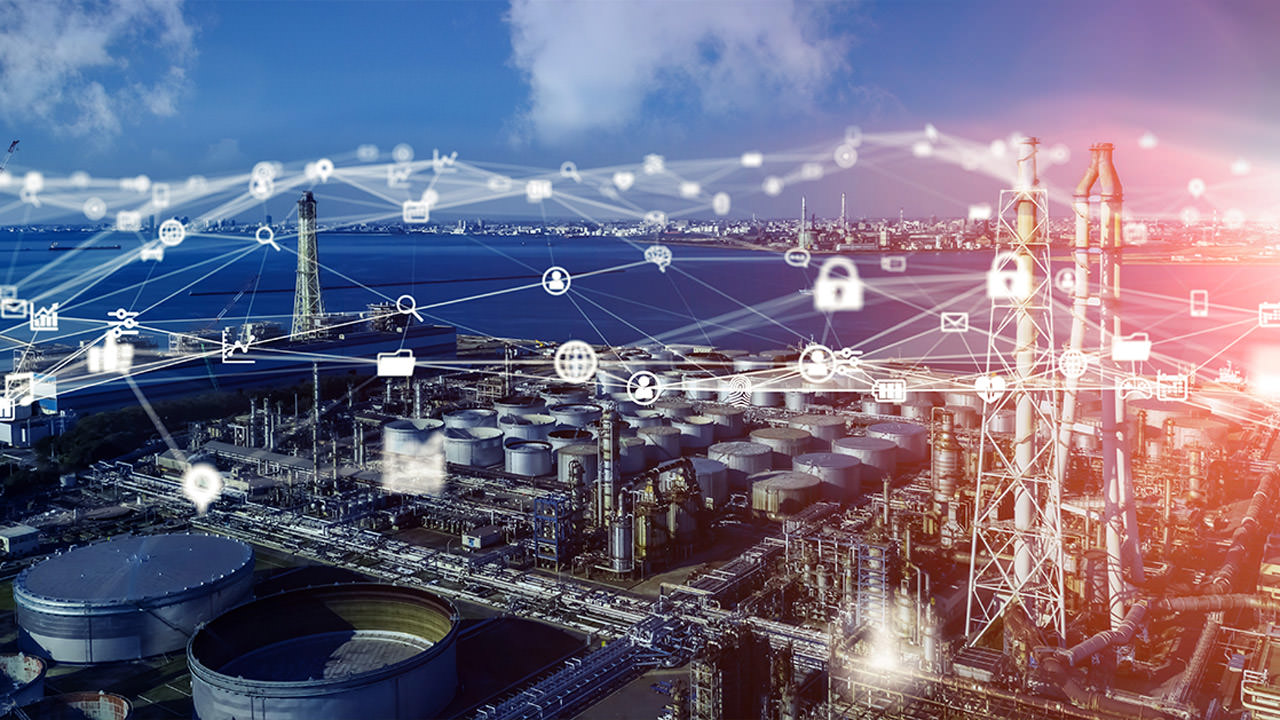
The merits of 5G wireless communications on the factory floor are obvious, but as with any networking technology that promises to disrupt the status quo, it will take time, resources, and a concerted effort to ensure all factories can benefit from the investment.
Today, the most precious resource in the manufacturing industry isn’t steel, coal or electricity – it’s data.
With more than half of the world’s energy being consumed by the industrial sector, there is an urgent need to double the efficiency of factories around the globe. To do this, we need real-time access to data, so that we can communicate faster, more reliably, and more securely on the factory floor.
With reliable and real-time data and easily reconfigurable systems, manufacturers can make decisions quickly such as scheduling maintenance, adjust a machine setting, or pivot from making shirts to face masks, as an example.
5G, with its high capacity and low latency, is making this possible – whilst also enabling manufacturers to add cutting-edge technologies, such as automated robots and IoT devices, into their operations.
But for these machines to work safely and securely, they need to be able to securely sense, measure, and interpret the real world. This requires converting analog data, including pressure measurements or vibrations, to digital data, to allow for more signal processing.
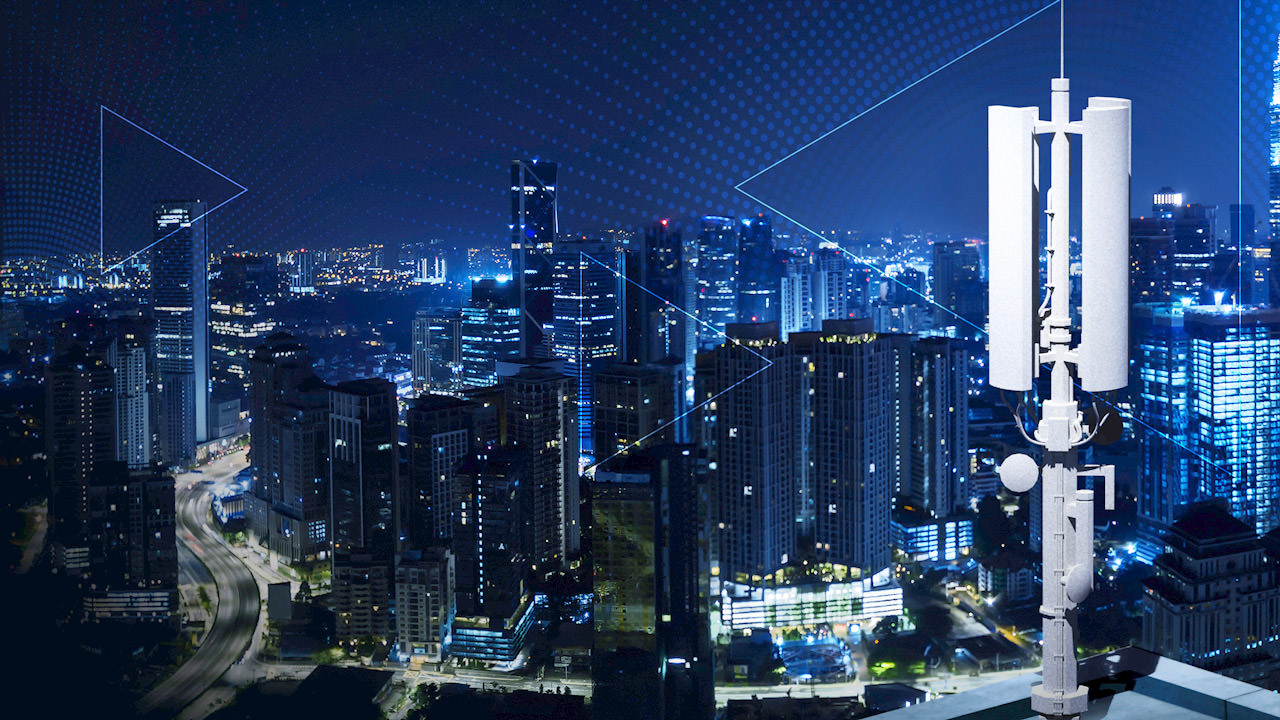
Eliminating wired connectivity by using 5G provides the manufacturing environment with more flexibility.
Intelligent edge
The highest quality data can be found at what we call the Intelligent Edge. Take a gigafactory, for example. When it comes to battery manufacturing a robot must apply uniform coating requiring a high degree of precision. This precision can be ensured through data from the Intelligent Edge. 5G gives us the ability to harness these insights at the Edge and make better decisions, thereby enhancing efficiencies overall.
5G is also accelerating efficiencies simply by making it safer for humans and machines to work together. Manufacturing processes are faster, more efficient, and more cost-effective when humans and robots operate in tandem.
With increased automation and robots taking on repetitive, dangerous work, manufacturers can augment human labor and ensure continuity of production. 5G’s reliability and speed mean machine-to-machine communication and, increasingly, human-to-machine interaction is vastly improved, reducing the risk of accidents.
Eliminating the need for wired connectivity through 5G also provides the manufacturing environment with a lot more flexibility, in turn, augmenting process automation, remote monitoring, and maintenance and device life cycle management.
Consider a factory, for example, where the physical connectors have disappeared and command instructions are sent wirelessly between robot subsystems, increasing production speed while reducing costs. All of this is possible through a 5G wireless network because it maximizes communication, reduces the margin for error (or accidents), and importantly, keeps the technology secure from hackers or malicious entities.
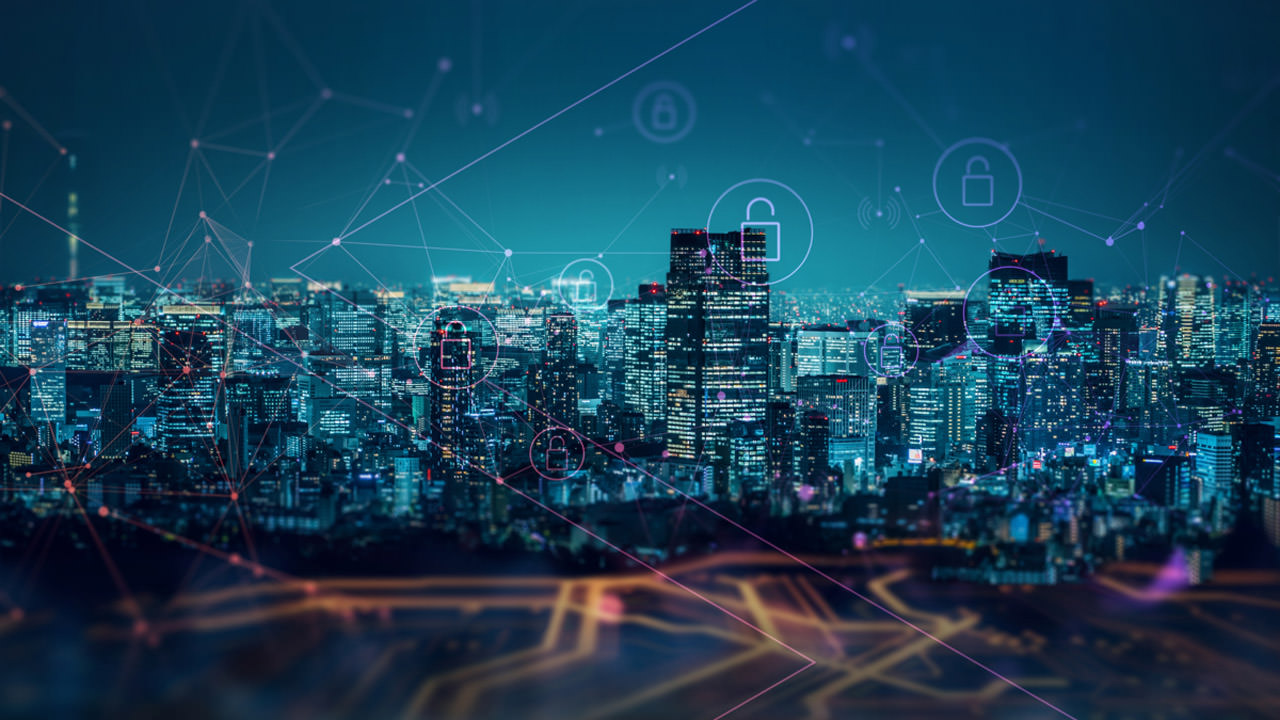
5G harnesses insights at the Edge to make better decisions, enhancing efficiencies overall.
Benefits of 5G on factory floor
The merits of 5G on the factory floor are obvious, but as with any technology that promises to disrupt the status quo, it will take time, resources, and a concerted effort to ensure all factories can benefit.
The transition from wired to wireless networking is a complex upgrade. Each industrial customer has a unique set of circumstances, from cultural dynamics to financial position to appetite for innovation that sways the organization’s ability to make the significant upgrade to wireless.
That said, the number of digital factories will increase rapidly over the next few years as traditional manufacturing facilities come to the end of their life cycles. The COVID-19 pandemic taught many difficult lessons to firms about the risks of too much offshoring. As a result, many are now looking to bring their facilities closer to the customer.
This is opening the door to newer, more powerful facilities, underpinned by 5G technology. Once 5G is fully realized, we will be living in a world that holds the potential to dramatically improve life for all.