TechnologyMay 10, 2018
Deploying operational data to an OT/IT cloud
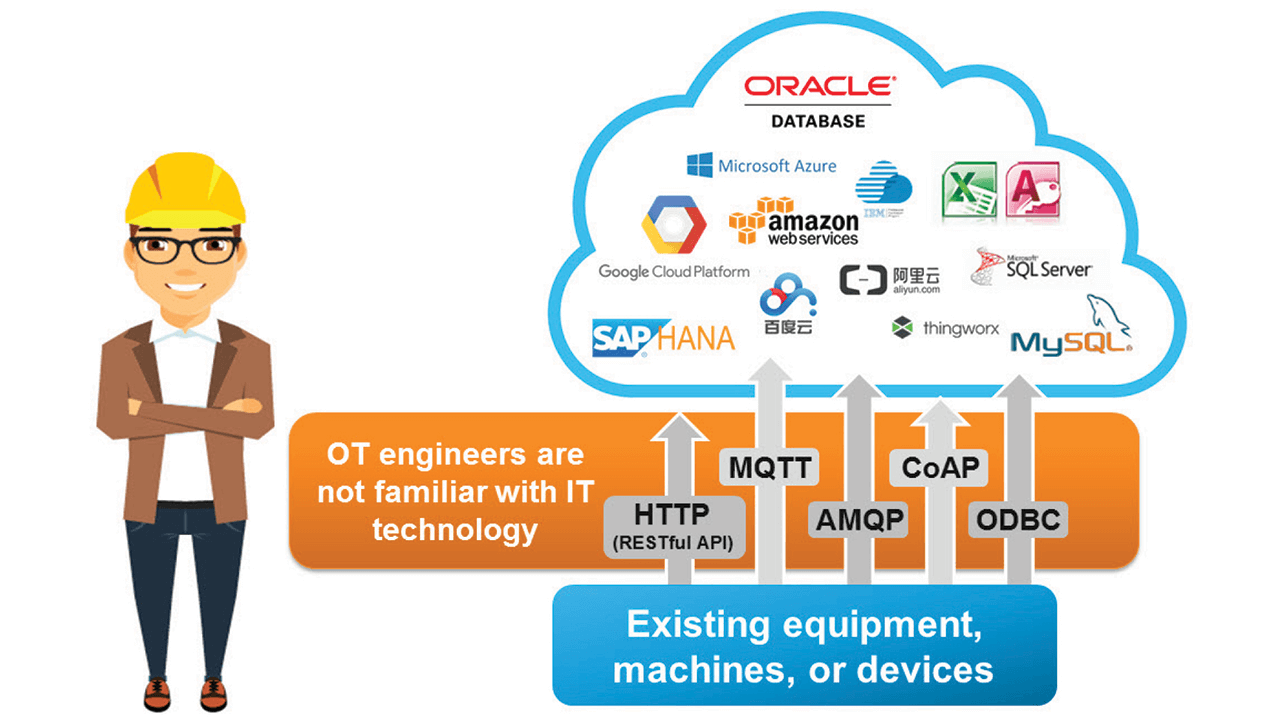
With IIoT applications collecting and processing vast amounts of data, deploying processed data to the cloud securely and efficiently is a key aspect of system performance. But fortunately, new software tools are providing seamless, cost-effective ways to store operational data using an OT, IT, or hybrid cloud.
IIoT SOLUTIONS ARE GOING MAINSTREAM for corporations looking for benefits such as production quality, cost reduction, legacy asset optimization, and even new business model opportunities. In this article, we discuss the importance of deploying OT data to an OT/IT cloud, and highlight how to help OT engineers complete such a daunting task.
Deploying OT data to OT/IT cloud
Over the past few years, the Industrial IoT (IIoT) has been transformed from a concept to real solutions that focus on business-to-business, device-to-device, and people-to-device connectivity across industrial networks.
The first step to realizing an IIoT application is data collection, and an ever-increasing number of IIoT technologies are now available to collect large amounts of data from monitored OT systems. Prime examples of such technologies are cloud services and pub/sub protocols. Because of the continual diversification of IIoT applications, the amount of data that needs to be collected and processed is increasing faster than ever.
IIoT solutions are becoming mainstream for corporations looking for benefits such as production quality, cost reduction, legacy asset optimization, and even new business model opportunities. In this article, we discuss the importance of deploying OT data to an OT/IT cloud, and highlight how Moxa can help OT engineers complete such a daunting task.
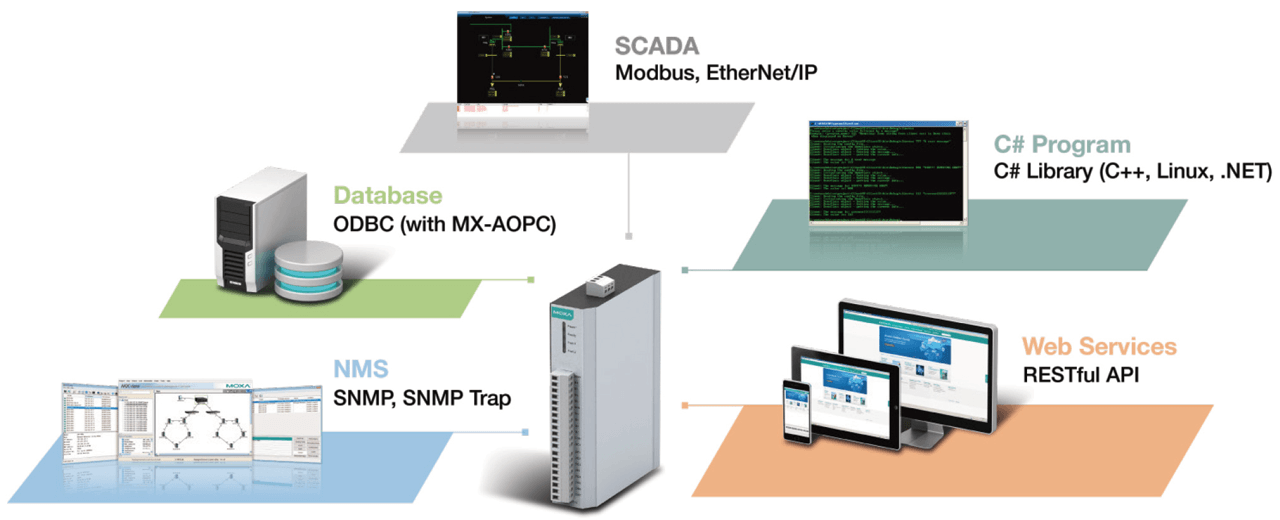
Multiprotocol smart I/O supports variety of protocols for both OT and IT engineers.
Value chain integration
Historically, operational technology (OT) departments have been responsible for keeping their plants running smoothly. The typical scenario has been to monitor the status of and data produced by manufacturing processes performed by shop floor machines. For some advanced corporations, process data was uploaded to SCADA systems as part of an effort to migrate from passively monitoring equipment status to proactively improving Overall Equipment Effectiveness (OEE) and control.
Information technology (IT) departments, on the other hand, were responsible for managing business applications related to finance, the supply chain, and product orders. In addition, they endeavored to improve the supply chain by enhancing the connectivity between enterprise resource planning (ERP), manufacturing execution systems (MES), and the factory’s OT system.
Generally speaking, both IT and OT departments work to ensure that data is meaningful and accessible for use across the corporate value chain by making the data available to the ERP and MES systems, and consequently, these IT and OT engineers need to coordinate their efforts.
Predictive maintenance/availability
A leading use of the IIoT is the implementation of predictive maintenance for critical, expensive assets, with the ultimate goal of increasing the availability of these assets. By implementing a predictive maintenance strategy that includes monitoring historical patterns of a machine’s vibration, current, and other data, corporations can schedule required maintenance on a regular basis, instead of shutting down the entire operation when unexpected failures occur.
Predictive maintenance is attracting attention due to its impact on a corporation’s output and revenue. An intelligently implemented predictive maintenance strategy provides clear financial benefits, whereas the ROI of run-of-the-mill IIoT applications are relatively hard to evaluate.
Optimizing operations
One of the main reasons for deploying OT data to an OT/IT cloud is to provide machine and process data that can be analyzed for industry-specific asset optimization and business intelligence (BI).
Optimizing operations is one of the driving factors for connecting an OT system to an IT cloud to provide the information needed to coordinate resources and information to improve asset performance management.
New business models
In the past, it wasn’t possible for Original Equipment Manufacturers (OEMs) to predict when a machine they had already shipped was going to experience problems. Instead, they had no choice but to wait until customers notified them that a machine had failed. Now, by using cloud resources to remotely monitor their machines, OEM vendors can provide proactive aftersales maintenance using machine data from the OT systems used in a variety of operating environments. Machine owners benefit since their machines will be maintained, repaired, or replaced before they experience excessive downtime from unexpected machine failures.
For this reason, OEMs are adopting business models that include selling predictive maintenance subscriptions and technical support, thereby achieving near-zero unplanned downtime for equipment installed in their customers’ plants.
Interoperability between OT/IT
A fair assessment of current trends is that transmitting OT data to an IT cloud marks the start of the next chapter in industrial networks, and consequently, system integrators are striving to find the best way to build a bridge between OT and IT systems.
OT and IT departments who are usually unfamiliar with the protocols used in each other’s domains is a critical, but not impassable roadblock to cross-platform integration. OT engineers find this task to be extremely challenging, particularly since they are not familiar with the process of collecting data via IT protocols. Last but not least, how to adapt existing systems without replacing every device in a plant is also a key consideration where interoperability is concerned.
Network and data security
As more and more OT systems are being connected to IT networks, understanding how to handle network and data security is of prime importance. In the past, less emphasis was placed on network security since OT data was transmitted via legacy fieldbus or even proprietary systems that were not connected directly to the Internet. However, once it is decided to leverage the convenience of cloud storage and cloud computing applications, it is extremely important that engineers are educated on how to use the most advanced data and network security practices.
Overseeing the security of heterogeneous networks requires both OT and IT know-how to ensure success. Whereas IT engineers are well-versed in security protocols and security policies, OT engineers provide expertise in production processes and machine deployment to ensure that their production systems operate at peak performance. To lower costs, it is important to implement such systems without making huge changes to existing network environments and legacy equipment.
OT data on an OT/IT cloud
The MX-AOPC UA Suite is an example of a way to create a secure and efficient data connection between OT and IT systems. With IIoT applications collecting and processing vast amounts of data, and with the amount of data being processed expanding at an ever-increasing rate, how to deploy the data to a cloud securely and efficiently is a key aspect of system performance. The suite provides a seamless, efficient, and cost-effective way to deploy OT data to an OT, IT, or hybrid cloud.
Traditionally, it has been difficult for OT and IT engineers to write agent programs to poll the thousands of registers used for shop floor data. The difficulty stems from the fact that shop floor data is handled using fieldbus protocols, but the data needs to be written to an IT database. The difficulties are compounded considerably when it comes time to scale up a facility, particularly since the additional load created can put a tremendous strain on systems that rely on legacy data acquisition methods.
The MX-AOPC UA suite can be used to collect data from shop floor registers via a Modbus protocol. The data can then be provided to an OPC UA client such as a SCADA system, or MX-AOPC UA Logger can be used to write the data to an IT database, all without the need for additional programming effort. As an added benefit, MX- AOPC UA Suite provides security policy options for encryption and certificate exchange to ensure the security of data connections and transmissions.
Multiprotocol smart I/O
A multiprotocol smart I/O that supports various protocols, such as Modbus/TCP and EtherNet/IP for OT engineers, and SNMP and RESTful API for IT engineers, enables communication between different interfaces.
This is certainly a step in the right direction to bridging the gap between OT and IT engineers, and it does not entail changing the entire OT topology. Moreover, the multiprotocol I/O feature supports MXIO Library, which gives IT engineers an easy way to integrate the smart I/O operation with their own programs, making it possible for both OT and IT engineers to conveniently retrieve data from the same I/O device.