TechnologyJuly 20, 2022
Edge computing for easily implementing IoT applications
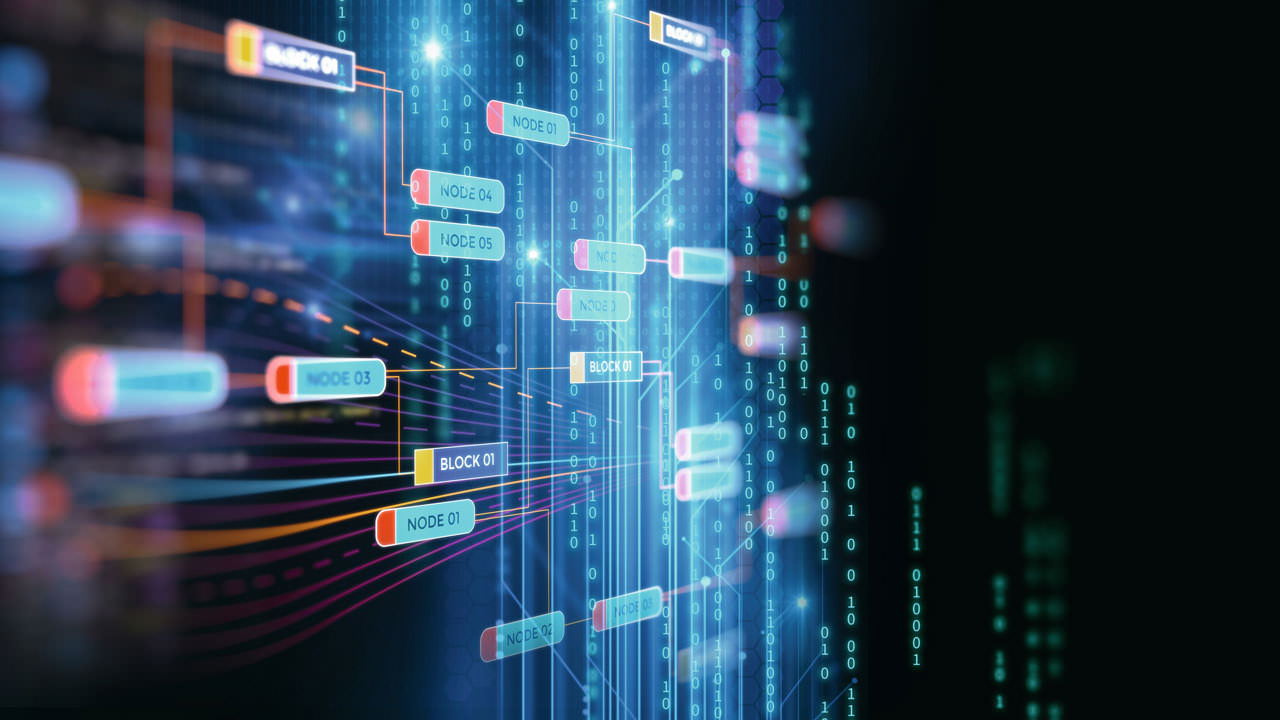
Intelligent IoT edge solutions can close the gap between the IT and OT worlds. With preinstalled software packages as well as universal graphical user interfaces and programming environments, powerful Edge PC hardware are enabling simple development and implementation of edge applications.
The advantages of edge applications are already known. However, a traditional PLC cannot locally preprocess incoming data. That’s why Phoenix Contact has developed Edge PCs with preinstalled software tools for easy implementation of IoT applications.
The discussion of whether edge computing lends itself to industrial applications comes up with increasing frequency today. The concept involves a decentralized computing infrastructure that is close to the data source. Edge computing solves the challenges of cloud computing in the production industry, as the cloud applications are pushed into the production applications. Cloud computing is already established in many office-related IT applications.
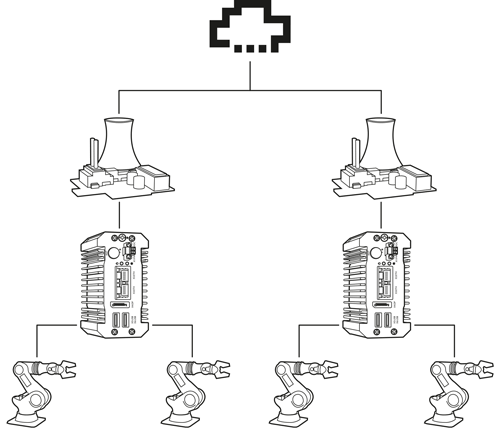
By definition, edge devices are installed at the edges of the network.
Many of these application areas, such data analysis and storage, are also relevant to the manufacturing industry – that is, operational technology (OT). There are some challenges in this environment, however, in terms of data protection and data security, lag time in information processing, data transfer rates, and computing power and storage space costs. Edge computing brings data processing closer to the machine and thus closer to the data source. Relocating the cloud application to the edge (that is, the edge of the network) allows such problems to be overcome.
It is important to realize, however, that there isn’t just the one edge. Rather, there is potential along a spectrum from the machine edge to server-based solutions for entire production sites. And the actual functionality of the edge solution differs from application to application. Cited as typical edge applications are data collection and compression, data (pre)processing and analysis, the use of artificial intelligence, and cloud connection.
Edge computing does not replace cloud computing, though. Instead, it complements it. The edge and the cloud thus have a partnership in which the distribution of tasks between the two solutions can differ according to application.
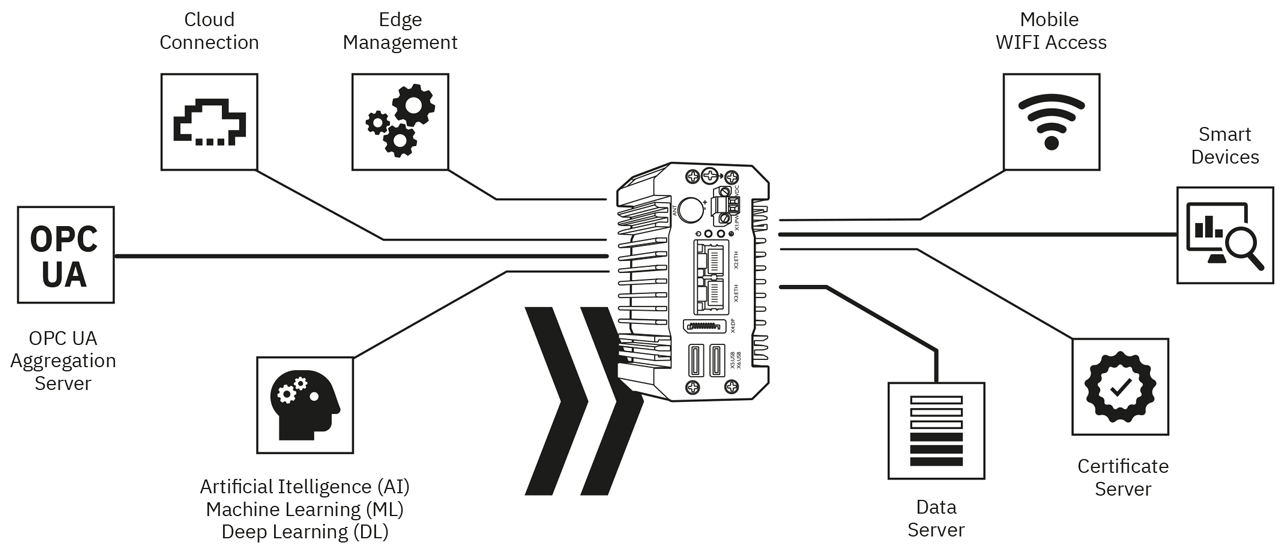
The Edge PC serves as the ideal device for edge applications within PLCnext Technology.
Benefit from openness of ecosystem
Behind PLCnext Technology is an open control platform for industrial automation technology that is part of a complete ecosystem. The ecosystem consists of the following components:
- PLCnext Control as a robust piece of hardware in the form of a PLC or industrial PC to which an I/O system can be connected
- The engineering and configuration software PLCnext Engineer, which supports IEC 61131-3
- The PLCnext Store as a digital marketplace where software related to PLCnext Technology can be downloaded
- The PLCnext Community, which serves as an information source and is there for exchanging knowledge about the ecosystem
Because of the openness of PLCnext Technology, any customer application can be integrated into the complete project, regardless of programming language. The openness and completeness of the ecosystem thus creates the ideal foundation for edge computing in the manufacturing environment. PLCnext Technology already offers numerous advantages here:
- The inclusion of various programming languages reduces development time
- The OT communication protocols most widely used in the production environment, such as OPC UA, PROFINET, or Modbus/TCP, are already supported by the hardware
- PROFICLOUD or multi-cloud connection is possible with a Cloud Coupler
- The components are based on a security-by-design development in accordance with IEC 62443
- Customer-specific and open-source software can easily be integrated into the overall application
- New apps can be reloaded to the controller easily through the PLCnext Store
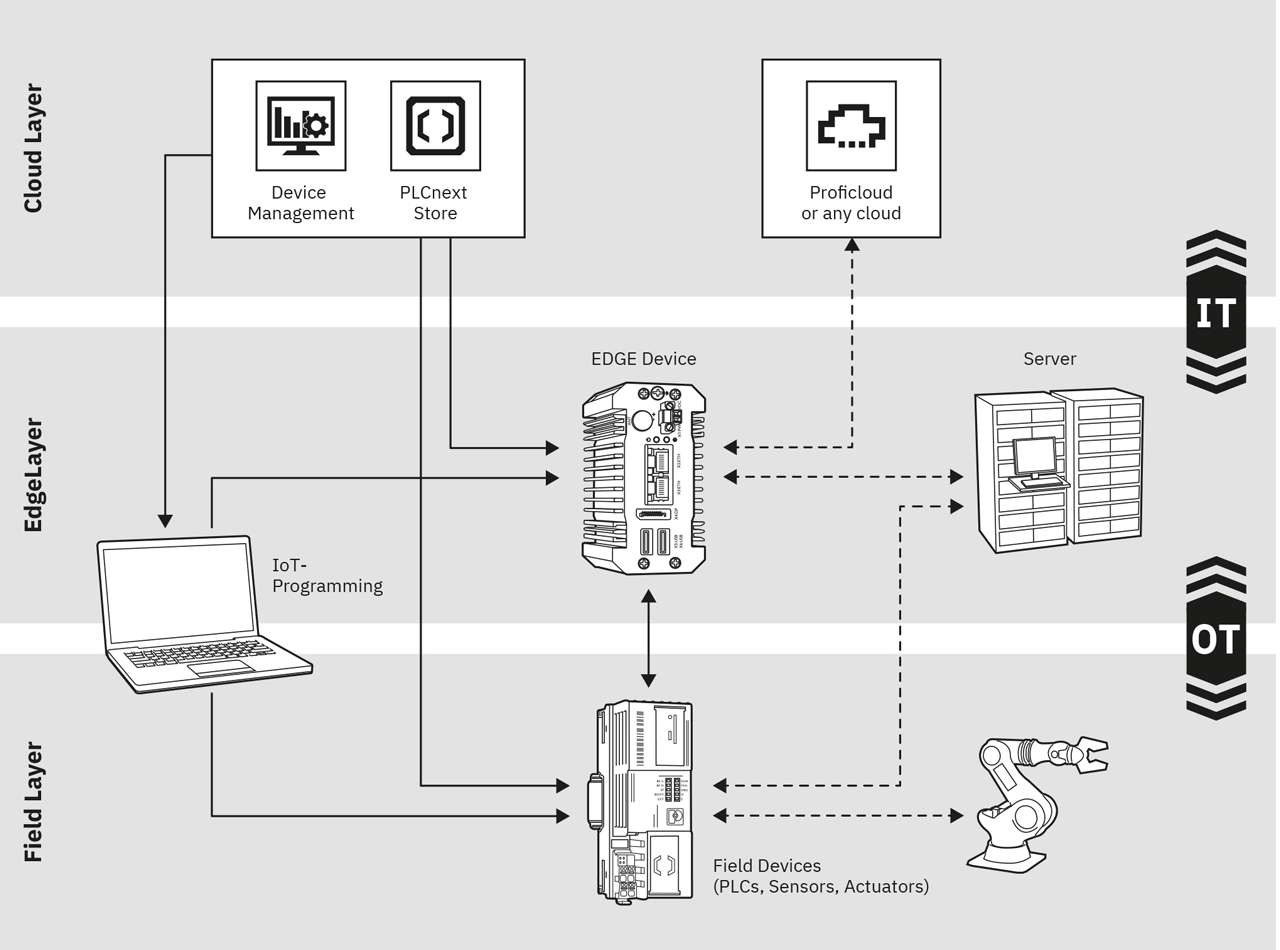
Functionalities of the Edge PC.
Software tools already integrated into the devices
The market for edge-programmable devices is currently evolving. While most providers offer edge-ready hardware, they lack the integrated software tools needed for a ready-to-use programmable edge device. That’s why Phoenix Contact Edge PCs are equipped with preinstalled software tools and were developed such that a wide range of IoT applications could easily be implemented.
With preinstalled software tools such as Node-RED, a local time series database, and a simplistic cloud connection to many cloud systems (e.g., PROFICLOUD by Phoenix Contact, Amazon Web Services, Microsoft Azure, or Google Coral), special nodes make the realization of IoT applications easier.
The Edge PC connects the IT and OT layers. Data processing happens at the edge of the network, as opposed to today’s usual process in which large volumes of data are sent to a cloud where they must then be processed and evaluated. The objective of processing data locally and upstream of the Edge PC reduces the bandwidth load on the network while simultaneously ensuring faster execution. Delay times are thus reduced. With a traditional PLC, though, data cannot be preprocessed. That’s why Phoenix Contact is currently developing Edge PCs that sort and preprocess a large portion of their sensor data at the point of origin.
Applications with high computing power and storage requirements
The company’s new Edge PCs combine the robustness of a proven industrial PC with the openness of PLCnext Technology. The devices, which are equipped with an Intel Celeron N3350 dual-core processor, offer up numerous interfaces. These include two Ethernet ports, two USB ports, one display port, and two serial RS232/RS485 interfaces. With 2 GB RAM (upgradeable to 4 GB) and 32 GB flash storage with an optional 128 GB M.2 SSD, even applications with high computing power and storage space requirements can be developed.
A user interface that can be called up via web server or locally via the display port allows access to the many functions of the Edge PC. The integrated TPM chip (Trusted Platform Module) ensures the integrity and security of the communication. The user can easily incorporate customer-specific applications and third-party applications into the solution via the PLCnext Store digital marketplace. In addition, support from Docker or Portainer enables intuitive implementation and management of containers and volumes. Consistent application of user interfaces and graphical programming environments means that users can easily develop and deploy their own edge application.
Connect hardware to common cloud platforms
Among other things, an edge application aims to reduce the bandwidth of the network through local (pre)processing of the incoming data while also ensuring faster execution and thus shorter delay time. Such an application cannot be implemented with a conventional PLC. Conversely, the user first sets up the Edge PC in the familiar PLCnext Engineer engineering environment. Data can be collected by all common communication protocols (e.g., OPC UA, Modbus TCP/RTU, or PROFINET) and can easily be stored in Node-RED with the existing nodes in the InfluxDB database.
The data can then be visualized and managed in the Chronograf user interface. Data can be compressed here, and rules can be established and alarms initiated. The opportunities appear to be endless and conform to the user’s needs in an optimal way. With nodes and the use of MQTT, connection of the Edge PC to the Phoenix Contact cloud as well as other cloud platforms can be pulled off without a problem.