TechnologyFebruary 2, 2021
Edge computing for smart factories and smarter machines

Edge computing platforms offer new revenue and cost reduction opportunities for machine and equipment manufacturers. They also offer OEM machinery builders a technology pathway to developing new generations of smarter equipment that meet changing customer demands and the need for digital transformation.
Different types of OEM machinery builders face one challenge that is always the same; the market is highly competitive. Each generation of equipment offers price/performance improvements over previous generations.
Design, engineering and product management departments must constantly evaluate the tradeoffs between new technology improvements and associated cost increases as they bring new designs to market.
Automation has been an integral part of equipment design for many years, but new concepts such as digital transformation, Smart Manufacturing, Industry 4.0 and the Industrial Internet of Things (IIoT) are being increasingly applied in the manufacturing world to deliver competitive advantages.
This article focuses on what machine and equipment manufacturers (OEMs) can do to leverage these new concepts and how Edge Computing can meet their unique needs as well as their customers’ requirements.
The need for smart machines
In the same way that machine automation, using PLCs and PACs, revolutionized equipment design a generation ago, Smart Factories and Smart Manufacturing are evolving the industrial world again. Applying digital transformation concepts enables companies to operate at peak performance by leveraging the data collected by control systems and sensors.
This approach provides real-time analytics to operators, inputs that help improve Overall Equipment Effectiveness (OEE), and data that can be collected and analyzed locally. Data can also be sent to the Cloud for deeper analysis in a variety of applications.
Applications can include optimized maintenance, supply chain agility, and increasing yield across multiple facilities engaged in similar production.
Machines and OEM equipment are fundamental elements of production. Smart Factories and Smart Manufacturing can only be achieved by Smart Machines operating as designed by their OEM or specified by the end user. Embracing digital transformation enables machine and equipment builders to enhance design and supports the development of new services around equipment performance and maintenance.
An important question is what is the best way to develop new generations of smarter equipment, or enable existing designs and deployments to meet the requirements that customers are demanding? Edge Computing is an approach that can solve many of the key design requirements.

Edge Computing platforms offer OEMs possible, new revenue generating services and improved TCO.
What is edge computing?
Edge Computing comes in many forms and can be broadly defined as any computing that takes place outside the data center. With such a broad definition, it is not surprising that there are many confusing definitions that span both the IT industry and the automation and controls industry that we refer to as Operational Technology (OT).
Gartner, a major analyst firm, has published a simple topology that enables everyone to understand what type of Edge computing might be useful to them.
This topology image demonstrates an infrastructure technology stack that shows the types of servers, devices, or platforms that can be characterized as Edge Computing and where they reside from the physical endpoint “at the edge” of the data source.
It alludes to the types of computing power, collection, analysis, and data movement that is available outside the actual data center. Edge provides extremely important benefits for equipment manufacturers and their customers.
From this topology, it is easy to see that the Device Edge through the Compute Edge are applicable to machine and equipment builders. In practice, all machines and equipment today have aspects of the Device Edge with PLCs, and some have Gateway Edge devices.
In some respects, Industrial and panel PCs used by machines or equipment fall into this Gateway category. They may be the first “point of contact” for a device edge PLC. Yet IPCs have limited computing and analysis power or suffer from common reliability and usability issues that are similar to a typical PC or server that is not manufactured for harsh environments. So, other types of purpose-built Edge compute platforms are required to meet customer needs.
When it comes to the modernization of machine control and automation systems, it is the Compute Edge that should be the focus for equipment builders. Edge Computing delivers all the characteristics and capabilities necessary for machine and equipment manufacturers to enhance their current designs and transition to the delivery of even smarter equipment.
Edge computing technology
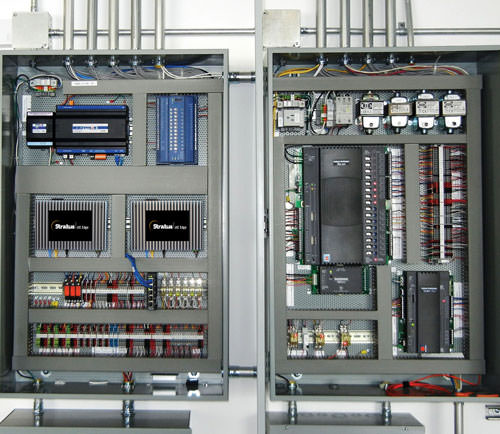
Ruggedization is important along with eliminating downtime, and offering remote monitoring.
Edge Computing is a scalable modular technology that supports the development of standardized, modular software components and applications to increase efficiency.
It can help enable equipment manufacturers’ existing applications—such as monitoring and control software—to be consolidated onto a single platform while enabling other critical applications to run on the same platform. This makes it easier to develop smart, Industrial Internet of Things (IIoT)-enabled machines and equipment, and to easily add future applications that support customers’ evolving Industry 4.0 and Smart Manufacturing demands.
When implemented, Edge Computing can facilitate a smooth evolution from the equipment of today to digitalized machines that are integrated into a customer’s operations. This includes multiple capabilities such as on-prem or Cloud connectivity to fully-integrated Smart Machines that embrace Digital Transformation without the need for complex retrofitting and redesign.
Edge computing for OEMs
While the Compute Edge category is quite broad, there are a number of key characteristics that narrow the types of functions that apply specifically to a machine or equipment manufacturer.
Edge Computing platforms must be capable of running existing control and automation applications in a modular way, without the need for significant re-architecting. Virtualization is a key technology. Essentially, each existing IPC can run as a “virtual IPC” or virtual machine on the Edge Computing platform.
This enables consolidation of all existing IPCs onto a single platform. None of these virtual machines are aware of the other virtual machines so all applications continue to run independently.
Modifying existing controls
With a virtualized Edge Computing platform, it is now possible to add much bigger degrees of flexibility to machine and equipment operation and monitoring. For example, with the traditional IPC/HMI approach, each station on a machine or piece of equipment is limited to what that IPC/HMI can display so only a single operator can monitor complex equipment from a single location.
This is not an ideal model. Using virtualization, equipment manufacturers can achieve increased flexibility for their customers by having multiple people remotely access data and applications at different stations. This autonomous model is preferred and provides customers more options.
Addition of new analytics
With virtualization it can potentially be easier to add new applications simply by creating a new virtual machine on your Edge Computing platform.
This paves the way to for companies to add new applications without impact to existing applications. This can include localized data collection, real-time analytics and data filtering before transport to external locations, such as a customer’s data center, or to the Cloud, perhaps your own. This can also depend on such things as data privacy laws and, of course, assumes you have a scalable Edge Computing platform as needs expand.
Support for OT/IT convergence
This is perhaps a topic not often considered by machine and equipment builders, but it is increasingly important in Digital Transformation initiatives.
The control and automation applications that operate the machine are well understood by your design engineers and your customers who operate the machines. They are focused on the Operational Technology (OT).
The expertise to develop sophisticated analytic capabilities, perhaps involving machine learning (ML) and artificial intelligence (AI), plus the capability to securely transfer appropriate data to a data center or to the Cloud is often the domain of Information Technology (IT) experts.
Edge Computing platforms can support both OT and IT requirements. It is important to ensure that a platform that supports multiple types of operations applications is simple to deploy and maintain, and easy to manage by both OT and IT professionals.
New revenue opportunities
Many of the capabilities and new applications that Edge Computing platforms support create the possibility of new revenue generating services, or the optimization of existing service and support capabilities. For example, a trend that is beginning to emerge is the concept of the “machine as a service” or “equipment as a service”, whereby the end customer pays based on time or usage instead of a traditional capital purchase. To successfully implement and maintain such a model, the machine or equipment manufacturer must understand the performance and maintenance profile of equipment, and have the ability to accurately collect and analyze the appropriate data.
Ruggedization
For a machine and equipment manufacturer, this is perhaps obvious, but Edge Computing platforms are supplied by a variety of vendors – not all of which are aware of the equipment’s final operating environment. It is not just about ruggedization, but also about eliminating downtime, making maintenance and support as simple as possible, and offering remote monitoring.
Similarly, Edge Computing platforms in the OT world must be prepared to operate autonomously for long periods of time as often there may be no connectivity to the outside world.
Cost reductions
Ultimately, adopting Edge Computing only becomes viable if it meets the stringent cost constraints of the highly competitive markets in which equipment builders play. When evaluating Edge Computing platforms, it is important to consider capital costs as well as development and ongoing costs. In addition to the savings from things like virtualization, cost is a function of value.
More expensive platforms provide a much higher set of value and benefits than simple devices or gateways with lower computing power. This approach will reduce other costs such as manual monitoring, downtime, staff resources, and application efficiency.
Some of these costs can be less tangible, but as industries move to automation, Digital Transformation and related initiatives, such as Industry 4.0, Smart Manufacturing and IIoT, equipment manufacturers must consider future applications and changes in the customers’ environment.
Summary
The machine and equipment manufacturer market is entering an evolutionary period that will bring as much change as the introduction of the PLC a generation ago. Edge Computing is a critical technology that will enable and ease this transition. Edge Computing platforms will play in integral role in expanding the traditional control and automation capabilities of equipment.
They will also provide the bridge for equipment manufacturers to embrace digital transformation initiatives for themselves and to integrate with initiatives of their customers.