TechnologyJuly 18, 2025
Machine monitoring with edge devices
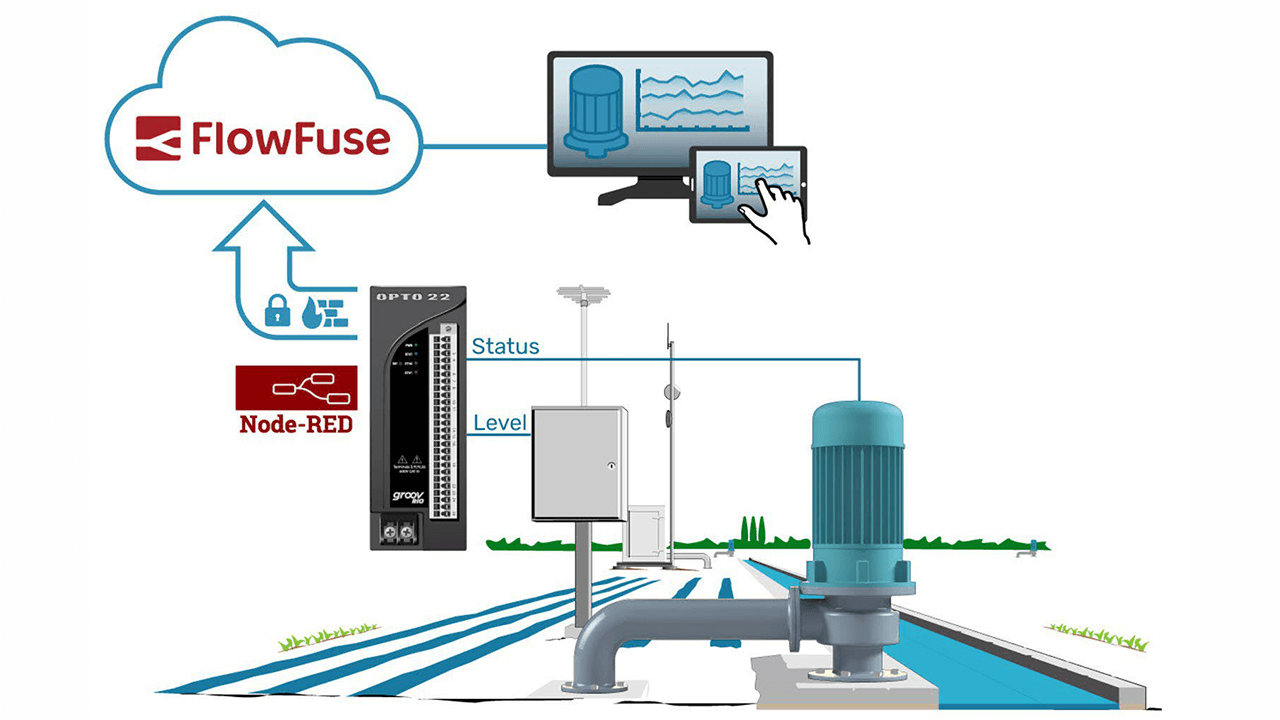
Gaining real-time insights into use of edge devices can help avoid downtime, reduce costs and optimize industrial performance. With today’s flexible edge devices, users can create tailored machine monitoring solutions that fit a wide variety of specific business needs.
A critical manufacturing conveyor belt at a plant suddenly stops during peak production hours. The entire assembly line grinds to a halt, operators scramble to diagnose the issue, and the company racks up thousands of dollars in lost productivity every hour it’s down.
Eventually, a technician discovers the problem: an overheated motor bearing that could have been detected days earlier with proper monitoring.
Keeping machines running smoothly is at the heart of every industrial operation. Machine monitoring helps avoid these downtime scenarios by providing the real-time insights needed to catch problems early and keep equipment working.
Machine monitoring: not just for new machines
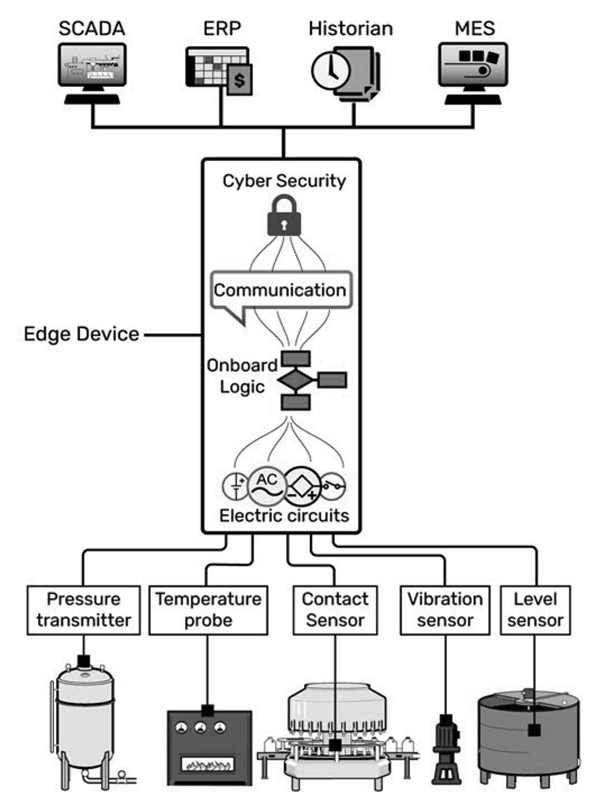
Here is how an edge device can easily integrate with non-networked machines.
Perhaps you’ve been tasked with an IIoT (industrial internet of things) or digital transformation initiative. The boss wants live production data from existing equipment to improve production visibility, help predict maintenance issues, and keep production operating smoothly.
You might think machine monitoring is only practical or cost-effective for new, high-tech equipment. After all, Industry 4.0 and IIoT platforms are often marketed as solutions for greenfield systems.
But the truth is, the greatest value of machine monitoring lies in improving the equipment you already own—capturing real-time data to optimize performance and prevent unplanned downtime.
Introducing edge devices
But how can you monitor legacy machines? One solution manufacturers are turning to is edge devices, small-footprint computing devices you can install next to a machine at the edge of your network. Edge devices bridge the gap between your older, non-networked machines and newer smart systems. They collect, process, and transmit data efficiently regardless of the machine’s capabilities and without disturbing existing machines or processes.
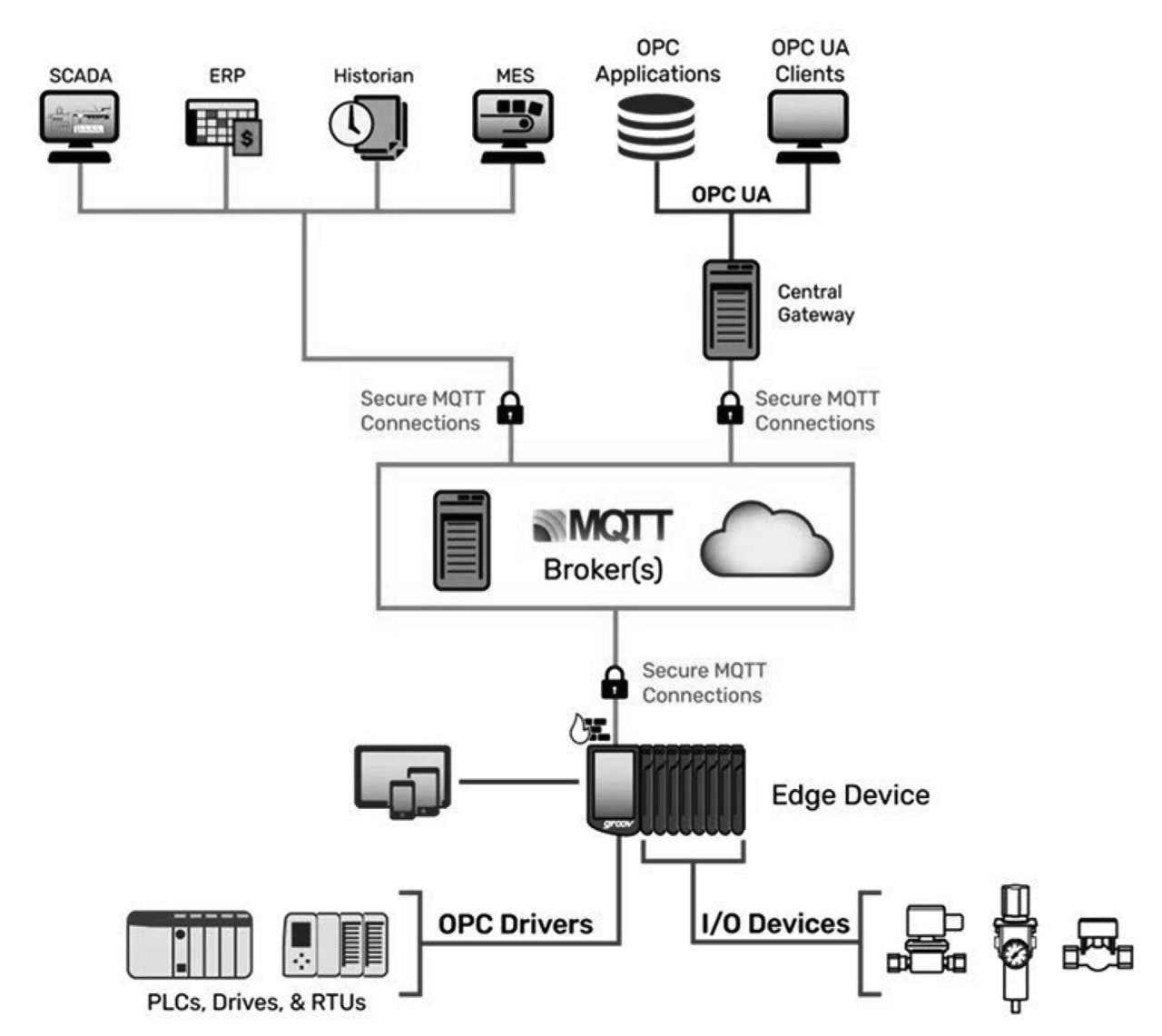
Leverage OPC drivers on legacy hardware to communicate with MQTT brokers and securely send data to OPC UA clients using edge devices.
How do they work?
Edge devices offer a number of unique features and benefits:
Multi-signal support: Modern edge devices connect to common industrial signals from digital and analog inputs, supporting standards such as 0–10 VDC, 4–20 mA, thermocouples, thermistors, and digital pulses for counting applications. You can monitor a wide range of parameters, from temperature and pressure to machine cycles, ensuring compatibility with diverse equipment.
Protocol bridging: Edge devices translate proprietary and legacy protocols into IIoT-ready formats like MQTT Sparkplug® B or OPC UA®. Whether legacy systems are on Ethernet or serial, edge devices have tools to connect them to modern IT infrastructure.
Local data processing and modeling: Edge devices pre-process data locally, converting raw signals into context-rich formats like user-defined data types (UDTs). Pre-processing reduces the amount of data that is sent and simplifies trend analysis and performance monitoring when the data arrives at its destination.
Built-in cybersecurity: Today’s edge devices are designed with robust security features, including firewalls, SSL/TLS encryption, certificate-based authentication, and zero-trust architecture. They support user authentication with LDAP (Lightweight Directory Access Protocol), VPN tools for secure remote access, and publish/subscribe communication models that prevent inbound port access, reducing vulnerabilities to cyberattacks.
How can you put an edge device to work in your operation? The approach depends on the hardware you’re working with.
Different approaches
When considering how you can incorporate edge devices, the approach differs between legacy brownfield equipment (non-networked machines) and newer machines with smart controls (networked machines). Let’s explore why.
Non-networked machines
If you’re working with older, non-networked machines that don’t have built-in connectivity, adding sensors and connecting them to edge devices is a clear-cut and low-cost way to start collecting real-time data.
This straightforward approach unlocks valuable data from even the oldest equipment, without requiring costly upgrades or modifications.
To get started:
Identify critical data points: Determine the key performance indicators (KPIs) that matter most, such as temperature, vibration, cycle counts, or energy usage. Focus on the metrics that directly impact machine performance, maintenance, and your overall operational goals.
Add sensors: Choose sensors suited to your data points. For example:
- Vibration sensors detect imbalances or wear in rotating machinery.
- Temperature probes monitor heat levels in motors or bearings.
- Flow sensors track the movement of lirrent transformers (CTs) measure energy consumption and detect faults.
- Proximity sensors detect the presence, position, or movement of objects, making them ideal for counting parts and monitoring conveyor systems.
Connect sensors to an edge device: Use an edge device with built-in I/O points to read and process sensor data. Then, democratize your data (make it widely available) to your digital infrastructure (SCADA, QMS, OEE, MES, ERP, etc.) via open-standard, IIoT-friendly protocols like MQTT Sparkplug B or OPC UA.
Networked Machines
If your machines have built-in communication capabilities, existing control systems like PLCs or fieldbuses can provide direct access to data by allowing you to leverage your equipment’s built-in communication infrastructure to collect the data that you need.
But if your machines use locked PLC programs or proprietary protocols, edge devices can bridge the gap between closed legacy equipment and modern IT infrastructure, ensuring seamless data access.
Take stock and decide what to do
First, identify critical data points: Tracking your machine’s operating state—idle or in use—helps with utilization and maintenance planning. Monitoring specific alarms and signals, like temperature or vibration, can reveal anomalies indicating potential failures before they occur.
Next, evaluate communication capabilities: Start by identifying the communication protocols your machines support, such as EtherNet/IP, Modbus®/TCP, PROFINET, EtherCAT®, or even older serial networking like RS-232, RS-422, or RS-485. While you can often directly integrate Ethernet-based protocols into modern systems, serial networks may require additional tools, like serial-to-USB or serial-to-Ethernet converters, to make the data usable.
Try to overcome common challenges: Even with Ethernet-based communications, networked machines often have challenges like locked PLC programs or proprietary protocols. In many cases, you can add third-party software, like an OPC UA server, to help bridge these gaps and translate proprietary protocols into modern IIoT protocols without disrupting operations.
Consider using an edge device to bridge the gap: With common challenges like these, you may find it easier to use an edge device—similar to the approach with non-networked machines. An edge device can tap into existing signals, add new sensors, or leverage onboard OPC UA servers with custom drivers to gather data from proprietary protocols.
And what if your legacy machines are on a serial network? Even older serial protocols can be integrated into modern edge devices using simple and inexpensive serial-to-USB converters. The edge device then converts legacy protocols into cybersecure IIoT standards like MQTT Sparkplug B or OPC UA.
Turning data into action
Whether you’re integrating legacy systems or enhancing smart machines, edge devices provide the bridge between your equipment and your Industry 4.0 or IIoT initiatives. Now you can turn your existing equipment into a valuable source of real-time data—without costly overhauls or operational disruptions.
Start small. Add an edge device to a single machine or process, capture critical data, and integrate it into your digital infrastructure. From there, scale as needed, connecting more systems and expanding your monitoring capabilities at your own pace.
Your machines are already working hard—make them work smarter.
Real-world applications
With today’s flexible edge devices, you can create tailored machine monitoring solutions that fit your specific business needs. Here’s how businesses like yours are leveraging edge devices.
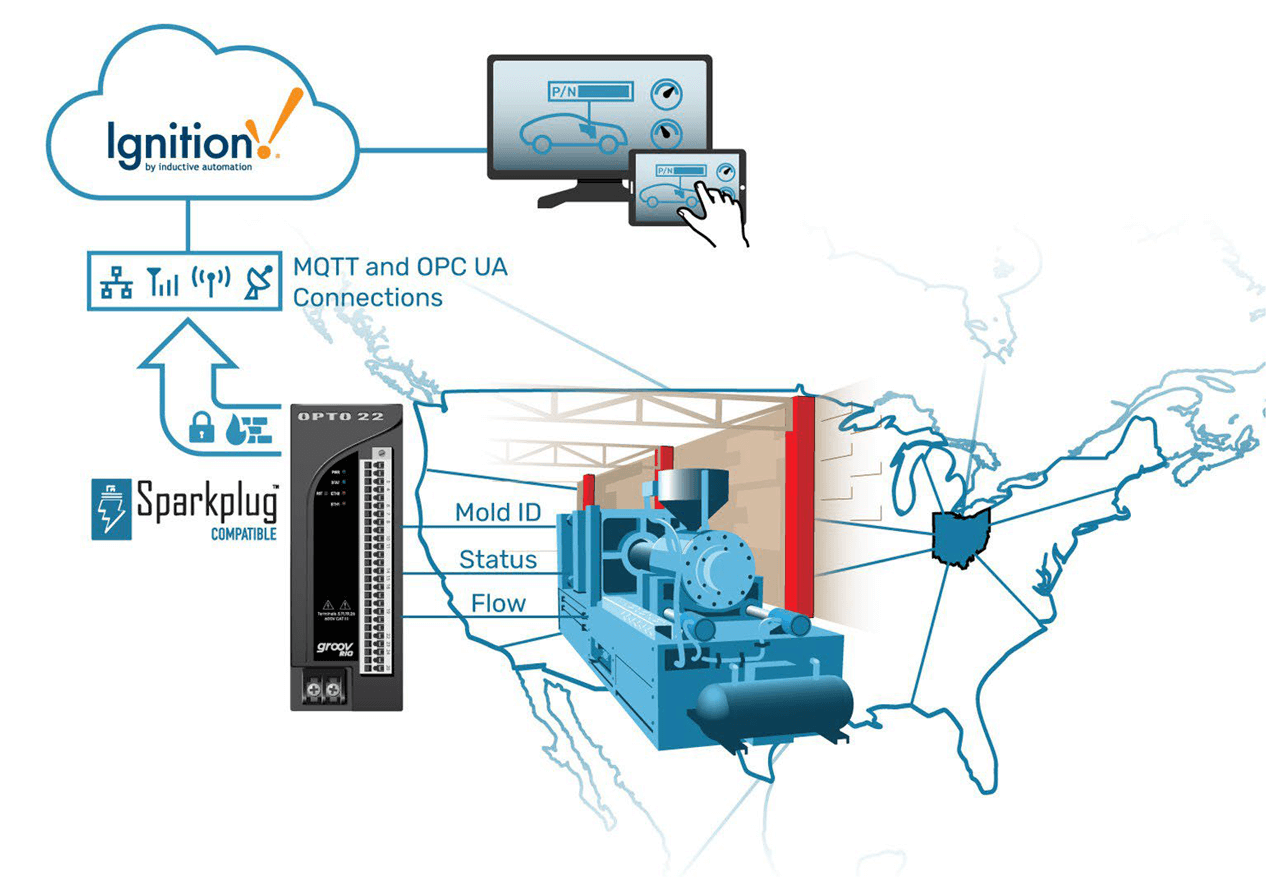
How a Tier 1 automotive supplier integrated the Opto 22 groov RIO edge device
Tier 1 Automotive Supplier
A Tier 1 automotive supplier headquartered in Marysville, Ohio, with six facilities across North America, specializes in plastic injection molding. They faced significant challenges integrating
real-time data from their diverse array of machinery. Outdated systems relied on 15-minute manual operator updates, leading to delayed insights, errors, and limited visibility into production performance.
As part of their Vision 2030 digital transformation initiative, they sought a scalable, cost-effective solution to unify their machines, regardless of age or manufacturer. By integrating a compact edge device—Opto 22’s groov RIO—they captured critical signals like full-auto status, mold changes, and water flow directly from their injection molding machines.
“groov RIO is simple. You have I/O, plug it in, connect an analog or digital signal, perform some simple configuration, and you are off to the races,” their IT specialist explains. Using groov RIO’s built-in MQTT Sparkplug B client, they now publish live data into their Unified Namespace (UNS), which runs on Inductive Automation’s Ignition SCADA hosted in the cloud.
The initial proof of concept quickly scaled to over 100 machines across multiple facilities, enabling them to track performance and availability in real time. “Now we can develop systems that plug into our UNS and make real-time decisions based on live data down to the second,” adds the IT specialist.
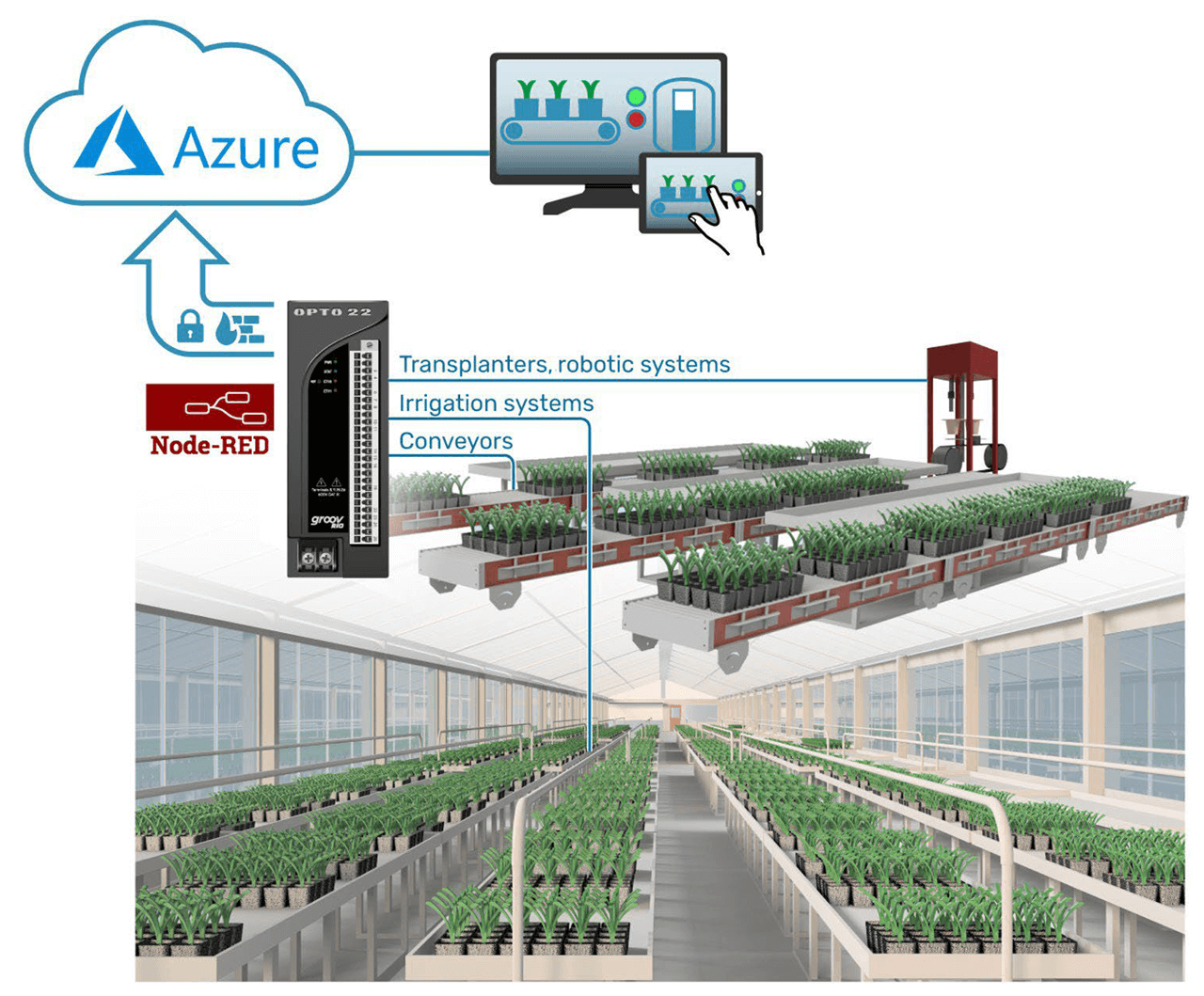
How an ornamental plant grower integrated the Opto 22 groov RIO edge device
Ornamental Plant Grower
One of the world’s largest ornamental plant growers, headquartered in Miami, Florida, faced challenges collecting real-time data from diverse equipment like transplanters, robotic systems, conveyors, and irrigation systems.
Traditional PLCs required costly software licenses and specialized expertise, making data access difficult. Recognizing that the lack of live data hindered their ability to optimize operations, their automation manager sought a solution that was simple, scalable, and cost-effective.
By integrating a compact edge device—Opto 22’s groov RIO—into their existing control systems, they collected data across their machinery, used Node-RED dashboards for real-time visualization, and used SQL nodes to store data in a cloud database on Microsoft® Azure®—leveraging tools like Power BI® for advanced analysis and insights to optimize operations.
“We realized that without accurate, real-time data, we couldn’t manage or optimize operations effectively,” the automation manager says. “For under $1,000, copying and pasting code that I already wrote, we can get a new groov RIO deployed in just a few minutes.”
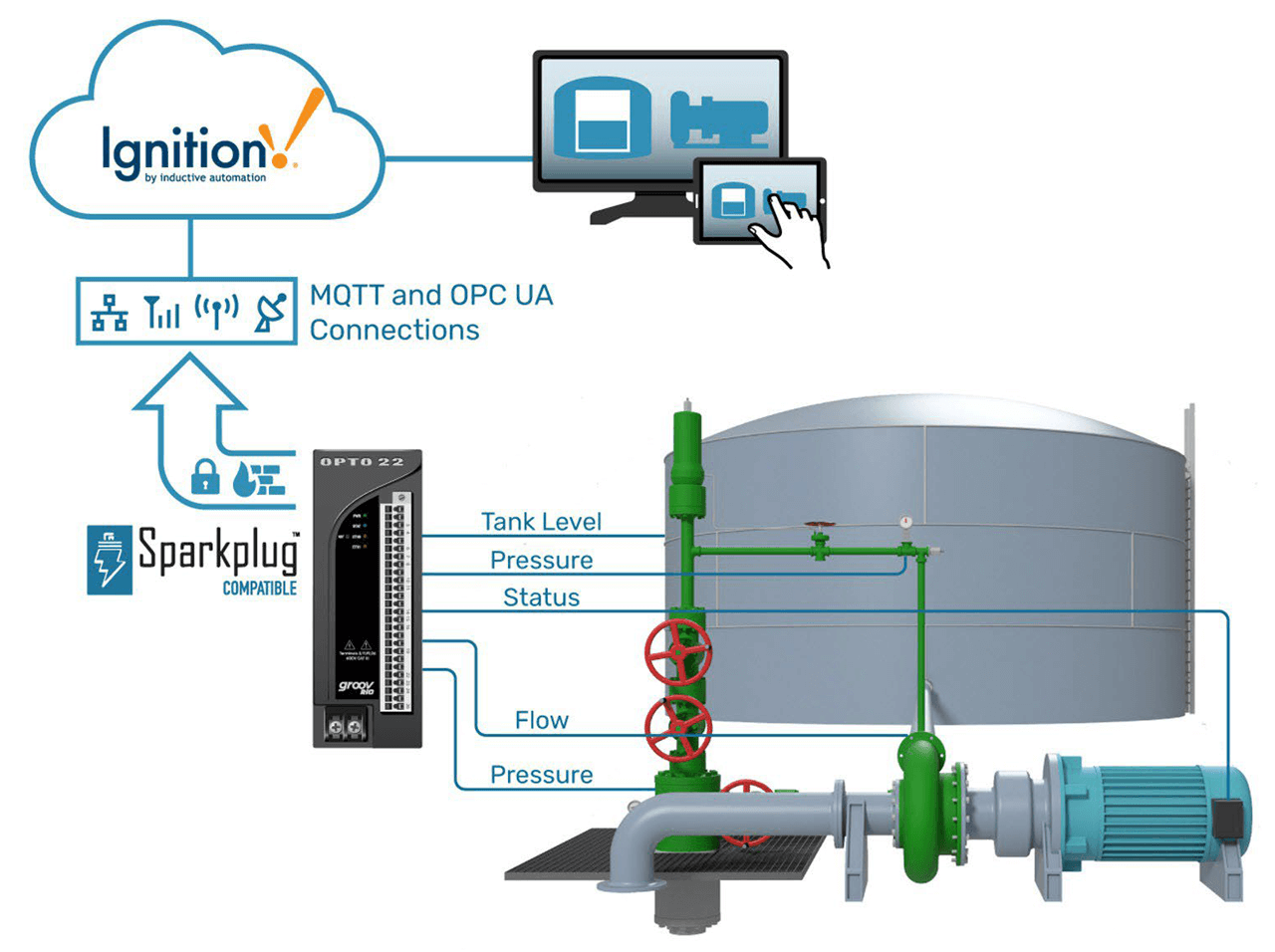
How an oil and gas company integrated the Opto 22 groov RIO edge device.
Oil and Gas Company
A Texas-based oil and gas company headquartered in Fort Worth faced challenges with outdated manual systems at their saltwater disposal sites, leading to inaccurate measurements and costly overflows—at $200,000 apiece.
Their automation engineer integrated Opto 22’s groov RIO edge devices, using both the RIO’s physical I/O connected to level sensors and its built-in Modbus/TCP communication to intelligent pressure sensors.
Describing the edge device as the “Goldilocks solution”—not an expensive panel with unnecessary extras nor a basic PLC lacking the necessary I/O and modern communications—the engineer highlighted its suitability for their IIoT architecture.
Now monitoring tank levels, flow rates, and pump statuses, the groov RIO publishes MQTT Sparkplug B data to their Ignition SCADA system, improving visibility, reducing environmental risks, and saving hundreds of thousands annually.
Water District
An irrigation and drainage district serving over 30,000 acres of farmland in Gila Bend, Arizona, struggled with costly downtime and pump failures, with annual repair costs reaching up to $400,000. Limited monitoring capabilities forced technicians to rely on frequent site visits, hindering efficiency and timely responses.
To modernize their operations, the district implemented Opto 22’s groov RIO edge devices. Using Node-RED dashboards for real-time visualization and leveraging their FlowFuse™ infrastructure for secure remote management, they automated the collection of data and critical metrics like pump statuses and water levels to improve monitoring.
“This is easily going to pay for itself,” says the district manager, noting reduced pump failures and an estimated $300,000 in annual savings.

How a water district integrated the Opto 22 groov RIO edge device.
OEM Heat Treatment
An OEM manufacturer of heat treatment systems headquartered in Terre Haute, Indiana, faced challenges in monitoring energy consumption for their high-power furnaces, some of which consume up to 350 kVA per hour. Precise energy tracking was essential to calculate and understand the operational costs of their systems.
To track energy use, the manufacturer integrated Opto 22’s groov RIO EMU, an IIoT-ready edge device for power and energy monitoring, into their latest furnace designs. The EMU provided real-time energy consumption data, allowing them to calculate the exact energy cost per part produced.
“With energy monitoring, we can calculate in real time how much it costs to heat treat parts, and we can now accurately assign the cost of energy to the production of a particular component,” explains their controls engineer.
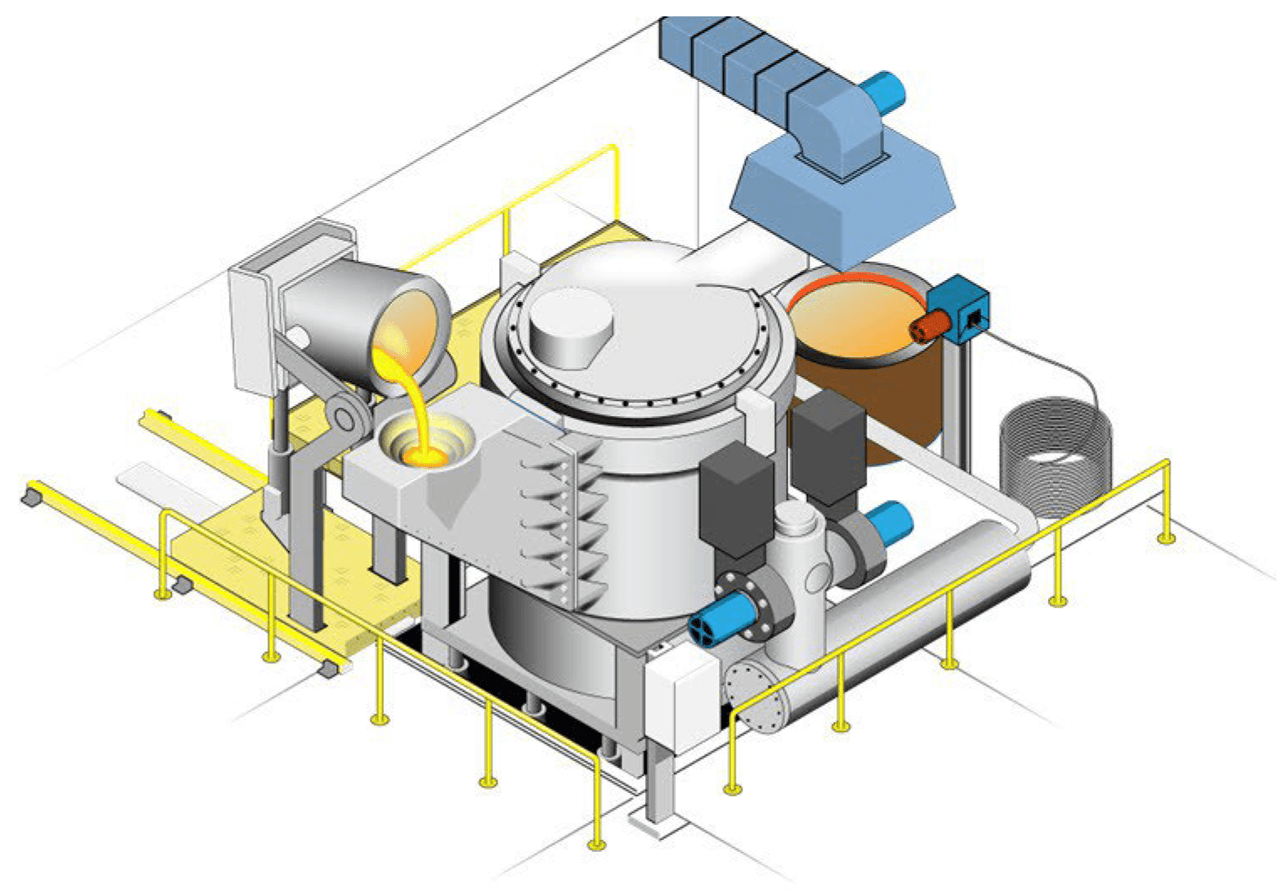
Furnaces and other high temperature equipment are often the largest energy consumers in a facility.
This insight enables them to precisely allocate energy costs to specific jobs, refine their pricing models, and identify opportunities to improve furnace efficiency—directly impacting their bottom line.
Conclusion
These companies followed the exact steps outlined in this article: they identified the data they needed, monitored existing signals, added new sensors where necessary, and leveraged existing protocols to collect critical operational data.
Each solution addressed their unique challenges and delivered real results. So what about you? What data will you capture, and how will you use it to take your operations to the next level? The tools are there—now it’s your move.