TechnologyJuly 10, 2018
Networking existing or legacy machines to an IoT gateway
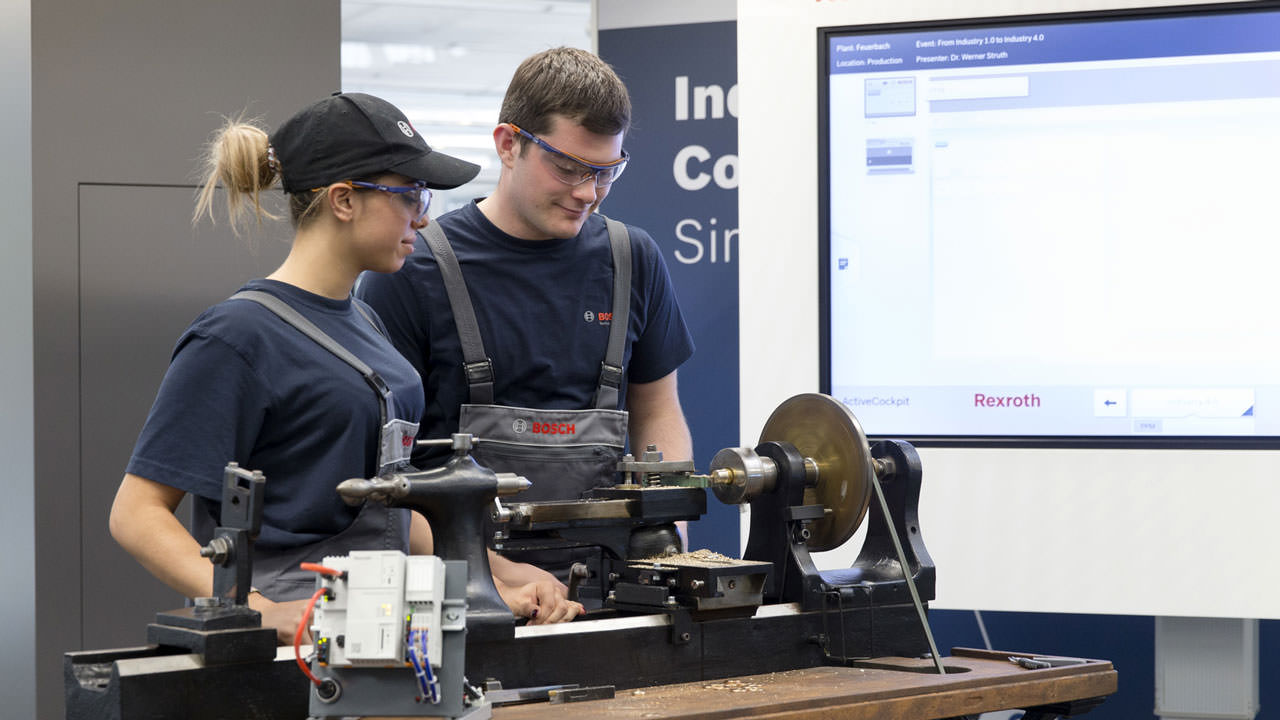
IoT gateways can tap the wealth of data constantly generated on the plant floor and the key to pulling legacy machinery into the digital, Industry 4.0 age. With planning to identify necessary and relevant data streams, it’s a tool for connecting OT equipment to IT business systems.
IN THE MANUFACTURING WORLD, data is the key to increasing efficiency and cutting expenses to create the most profitable product. Reacting quickly to machine shutdowns, supply chain issues and safety events get our plants back to what they are supposed to be doing: making our product! But getting the manufacturing floor to communicate with the business side of manufacturing has been historically difficult. Before the digital age, it was paper and people.
Computer technology started to automate some of the information exchange. The modern era of artificial intelligence (AI) and machine learning is starting to automate some of the analysis itself. But there has always been a divide between Operational Technology (OT) and Information Technology (IT).
The reason for this divide is simply that the technologies grew out of different needs. Operational technology grew from the need to monitor sensors and communicate data to and from machines. Loss of data is unacceptable for safety reasons in many cases and machine protection in others.
Communication standards were formed around reducing the need to have hardwired digital and analog signals between devices. Human interaction was limited to an HMI for machine control or a push-button station. Information Technology grew from a need to get information to and from people. Data transfer speed and reliability isn’t as important as the quality and usability of the information.
These two data streams, OT and IT, are now converging as new business models are being developed that require a tight integration between the two. On-demand ordering and batch-of-one customization are some examples.
Challenges with legacy equipment
The problem is that our manufacturing plants are full of old equipment, not designed to communicate with IT systems. The variety of these machines adds to the problem. A 40-year-old machine still has value in some manufacturing processes, but the communication technology will be obsolete or may not even exist.
As assets are added over the years, different technologies make their way to the plant floor, such that there isn’t a unified architecture.
OEM machine vendors use different suppliers for their automation, which, in years past, means that there are proprietary communication protocols and proprietary hardware as well. Different machine functions mean that even modern data streams are in different formats as well.
Machine Tools might use MT Connect. Packaging machines might use PackML. So even if a industrial machine is only a few years old, there are still difficulties in pulling data from such a variety of machines without a tool to help.
Also, IT systems do not always have the capability to speak machine languages or keep up with the data streams that are generated on the plant floor. Furthermore, some machinery and operations around a manufacturing process are too simple to warrant a processor capable of communicating at all.
As technology progresses, new machines replace old ones and the price of processing comes down, OT and IT systems will continue to grow closer in their data exchange. But in the meantime, a translator is needed to join the two and this is where an IoT Gateway comes in.
Human-powered lathe example
One extreme example that Bosch uses to illustrate the problem includes/features a human-powered lathe from 1887. The lathe was original to one of Robert Bosch’s manufacturing plants. It is powered by a foot treadle and adjusted with hand cranks. It is arguably a pre-Industry 1.0 machine as it wasn’t even powered by an external source such as steam or electricity. But there is data that we could collect from this machine. If we knew the speed differential between the main drive wheel and the spindle, we could detect the belt was slipping and needed attention.
If we monitor the cutting speed versus the position of the cutting head, we might be able to see when an operator was tiring and needs a break before quality starts to drop off. By implementing sensors and an IoT Gateway, we can pull this machine up into the digital Industry 4.0 age and increase its usefulness and value to our manufacturing process. The IoT Gateway allows value to be extracted from the process without replacing or redesigning the machine, both costly options.
In real-world applications, IoT Gateways are the connection to all types of operational data. While machine data and sensors are obvious data streams, there are others that can be collected to paint a more accurate picture of the entire manufacturing process. Ambient environmental data such as temperature, humidity, lighting levels and noise volume can be collected alongside machine data to correlate the effects on process performance.
Vibration sensors can detect changes in mechanics long before the ill effects of load imbalances or lubrication needs demand attention. Operator biometrics and performance can be tracked to optimize the safety of the operator and provide a work environment tailored for that operator’s needs. Creating individual data streams to a central data system is expensive and time consuming. An IoT Gateway can act as an edge device, collecting data, buffering it and even grooming it before transport to the upper-level analytics software.
It is in these upper-level IT systems that true value can be mined. As we described before, it is here where the people-to-people and people-to-data tools can be deployed to maximize communication of relevant data to the right people in a form that is informative and efficient. And it’s the IoT Gateway that lifts the data from the plant floor into these systems that begin to process large quantities of data to predict machine wear, maintenance needs and environmental effects on production. Once the IoT Gateway has made this data “air-borne”, it can be used by multiple visualization and analytic products to provide value.
IoT gateway solutions
So what should we look for in an IoT gateway? There are different features and qualities that will help with a successful IoT deployment. The IoT Gateway needs to speak many languages, both on the OT and IT sides. Collecting data will require speaking the language of different PLCs, not only from different vendors but from different eras.
Some PLCs and sensors use standard protocols like OPC, TCP/IP, Modbus, CAN or others, so supporting those is important too. On the IT side, there are popular systems like Microsoft Azure, Amazon Web Services and Oracle IoT Suite. Additionally, there are streaming protocols such as OPC, MQTT, REST and more. Network security features are important to protect machines from unauthorized access. Encryption, user management and authentication methods are needed for these. Another useful quality is openness. It may be difficult for any single product to meet all the needs of one application, so the ability to be configured and extended to meet specific needs is important.
An open SDK for the gateway and use of open standards can help in this regard. Lastly, but just as important, is user-friendliness. The measure of whether or not an IoT project makes it off the drawing board is the return on investment. If the engineering costs to stand up an IoT solution are too high, then the value of that project cannot be realized. The lower the engineering cost, the more projects come into the range of possibility. It is hard to find someone who is an expert on every data stream that needs to be connected. An IoT Gateway that is configured, rather than programmed is important. Many cheaper IoT Gateways have the hardware to connect to different streams, but no software to go with it.
Conclusion
An IoT Gateway can help tap the wealth of data that is constantly generated on he plant floor. They are the link to pulling old-Industry machinery into the digital, Industry 4.0 age.
With planning and upfront effort in identifying the necessary and relevant data streams, an IoT Gateway can be a valuable tool to quickly and efficiently connecting your OT equipment to your IT business systems, creating new business models and value streams.