TechnologyDecember 4, 2020
No edge computing without an appropriate network
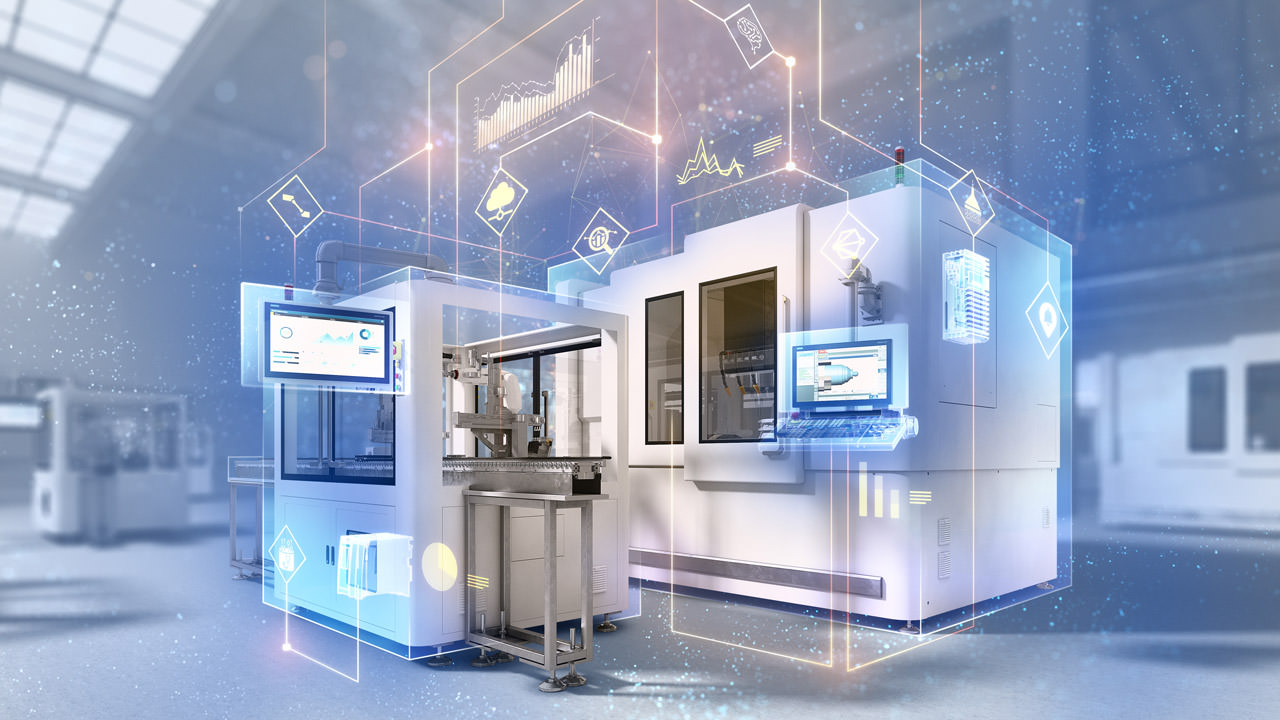
With the continuing emergence of the Industrial Edge, the industrial network will play an even more central and vital role, particularly in highly connected manufacturing operations. But also the advantages of end-to-end Ethernet networking can only be fully utilized, if the network is equipped with necessary resources.
Edge computing in its various forms is considered one of the next big steps not only in automation engineering. What can be easily overlooked is that the communication infrastructure, the network, is becoming more and more important.
Much has happened since Ethernet-based protocols for industrial communication such as EtherNet/IP and PROFINET were introduced in the early 2000s. It is now clear that Ethernet is the key foundation for industrial networking and will probably remain so for some time. This is supported by further developments such as TSN that rely on wide acceptance from automotive applications to system networking, as well as the strong growth rate of Ethernet-based protocols such as PROFINET.
The triumph of Ethernet technology
The big advantage has been flexibility. By utilizing a common technological basis, interoperability and the parallel use of different technologies has become easier.
In terms of communication, this means that it is no problem, for example, to carry out the process communication in an automation cell via PROFINET, while OPC UA is used in parallel to read data from individual devices or to send data directly via an Industrial IoT gateway such as the SIMATIC CC716. Both communication paths can serve completely different applications.
A co-existence is possible. For this to run smoothly, it is important that the industrial network meets the requirements of the applications. Another big trend with a very similar core competence is edge computing.
Industrial edge computing
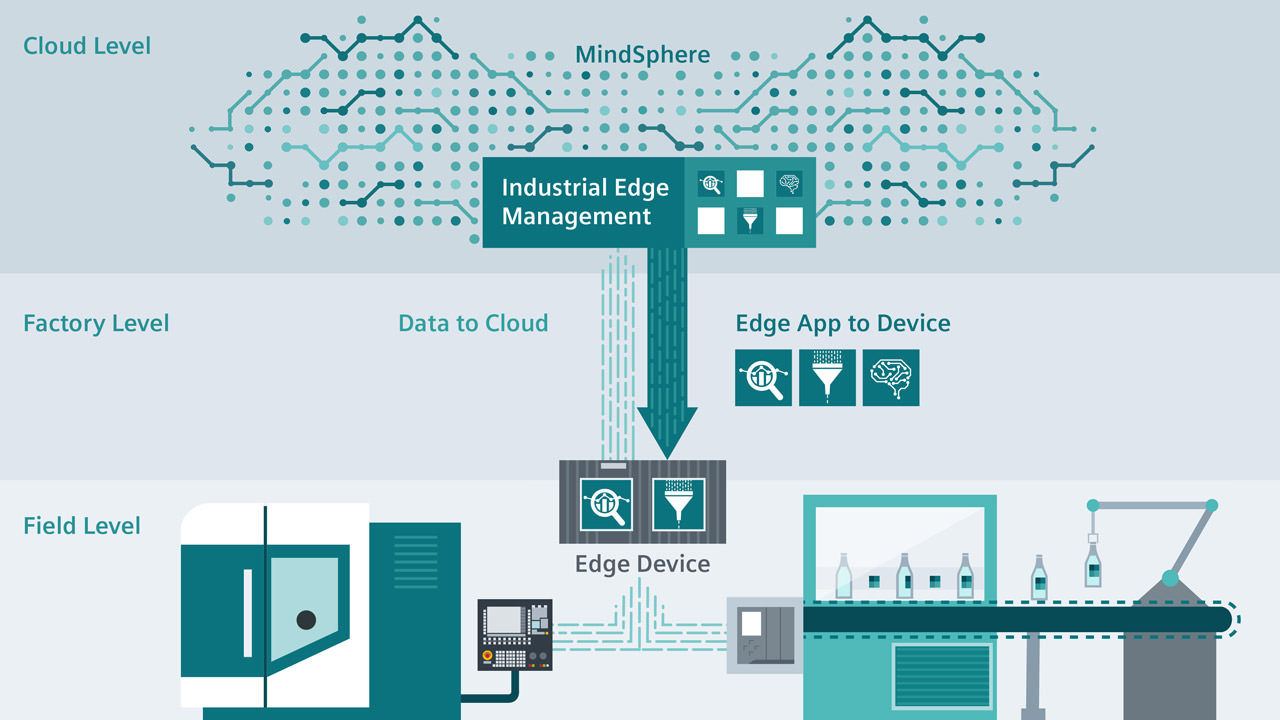
Industrial edge enables flexible management of software and industrial edge devices.
The basic idea behind edge computing is quite simple; it is the logical development of the “cloud concept.” That is the abstraction of hardware in order to be able to handle software functionality more flexibly and with more focus on the solution.
The term “edge” already indicates the crucial difference. In the context of edge computing, the execution layer shifts closer to the actual process again. Economic considerations also play a role here. Data that is processed directly on site does not need to be transferred to higher-level systems, or maybe only in compressed form, which saves bandwidth and consequently money. It gets a bit fuzzy when it comes to determining where the “edge” actually lies. Since the terms allow a lot of leeway, here is a concrete example: Siemens Industrial Edge.
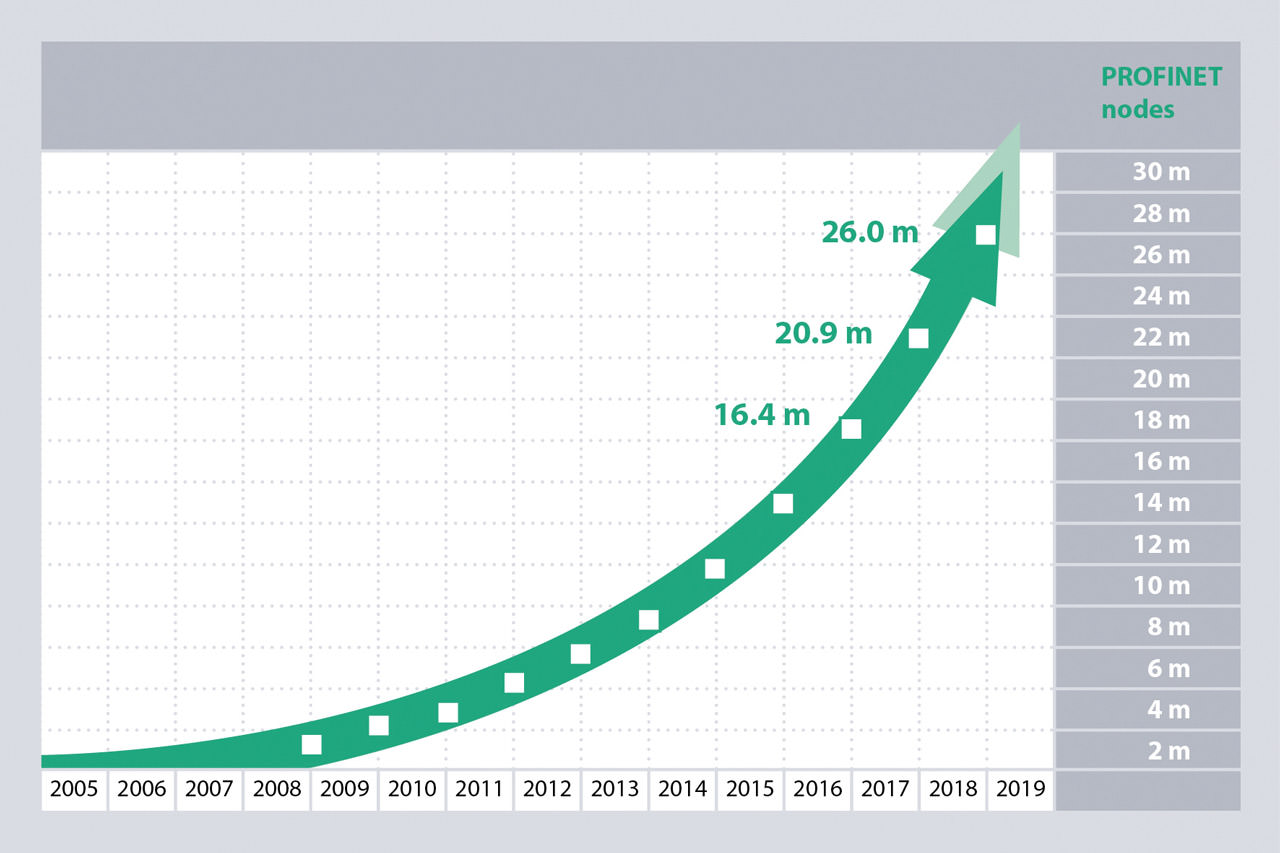
Ethernet-based protocols, including the arc of PROFINET shown here, are growing rapidly.
The system consists of multiple elements. For one thing, the “edge devices”, devices on which a runtime environment provides services for hosting “industrial edge apps.” These “industrial edge apps” are software functions based on container technology such as Docker. Devices and applications are orchestrated by a central “industrial edge management system”, either on premise in the factory or in the cloud depending on customer requirements.
The real highlight is that, in addition to the transparency pertaining to which applications run where with which version and how the devices are doing, the software becomes first and foremost more independent of the underlying hardware. For instance, hardware can be selected to match the framework conditions: Do I need a certain form factor, a certain temperature range, a certain performance class, or do I want integration into certain components – such as the PLC of my automation cell?
But one thing must not be forgotten in edge computing. Behind the logical links shown in many depictions, e.g., “App is loaded from management onto the edge device,” there is a real network that enables this functionality in the first place.
Industrial network as key element
The industrial network plays a central role, particularly in highly connected manufacturing, which, for example, makes sense when using Siemens Industrial Edge. But also the advantages of end-to-end Ethernet networking mentioned at the beginning can only be fully utilized, if the network is equipped with the necessary resources.
For one, the bandwidth requirement plays a central role. Specific bandwidth requirements for the automation cell can be calculated based on the configuration. The complexity increases for hierarchically higher networks. It is thus all the more important to be already aware during planning or expansion of a network infrastructure, where known data streams run and what bandwidths are required. Tools or services offered by various suppliers can provide support here. In the operation of the network, network management tools such as SINEC NMS help with the configuration, monitoring and, tracing of errors. Switch and router series such as SCALANCE XC and XR deliver the right performance.
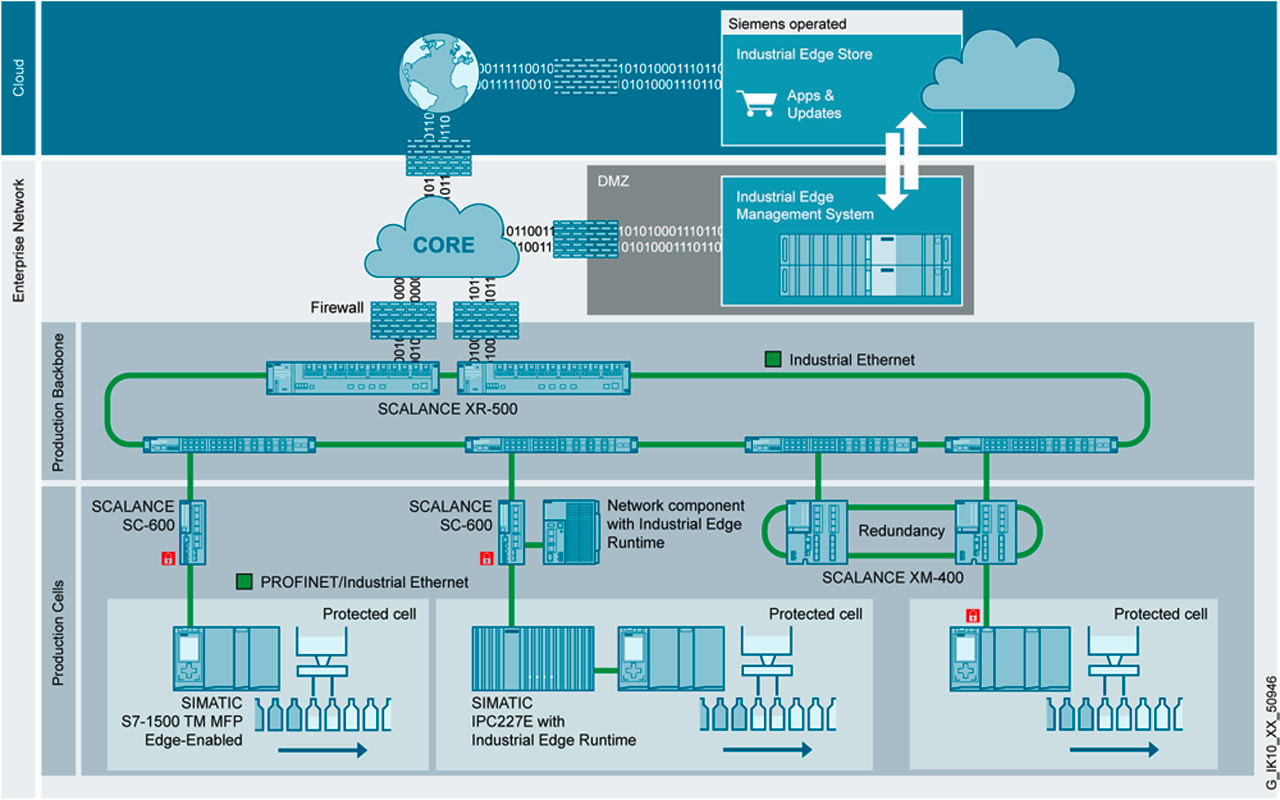
A carefully planned industrial network creates the foundation for a successful digitalization strategy
Furthermore, the targeted availability must be taken into account. Are short-term outages of the network tolerable because the individual components are able to continue to work self-sufficiently for a certain time? With a view to the ever-increasing linkage, the highest possible availability is becoming more important. Redundancy mechanisms, at least in the backbone networks, are the means of choice in addition to components intended and suitable for industrial use.
Last but not least, security must always play a central role. A security concept adapted to the character of the network or the production can provide strong protection against unauthorized intrusion by means of access restrictions, network segmentations, etc. Here, too, Siemens and external suppliers assist with the design and building of competence in your house – for example, on the basis of the “defense in depth” concept from Siemens. At the cell level, the requirements are implemented technically with, e.g., SCALANCE S Industrial Security Appliances.
How it works out
Due to the implicit demands on the infrastructure from edge computing, the industrial network is becoming more important than ever.
Hence it pays to earmark time and resources to equip it to meet your own requirements because it not only provides a robust communication infrastructure for today’s requirements, but also a sustainable basis for the digitalization of tomorrow. Partners like Siemens can support you with the right products and services for planning and implementing your network infrastructure.
Frederik Nitsche, Product Management of SIMATIC Communication Products, Siemens.