TechnologySeptember 1, 2020
Ethernet trends in the Industrial IoT environment
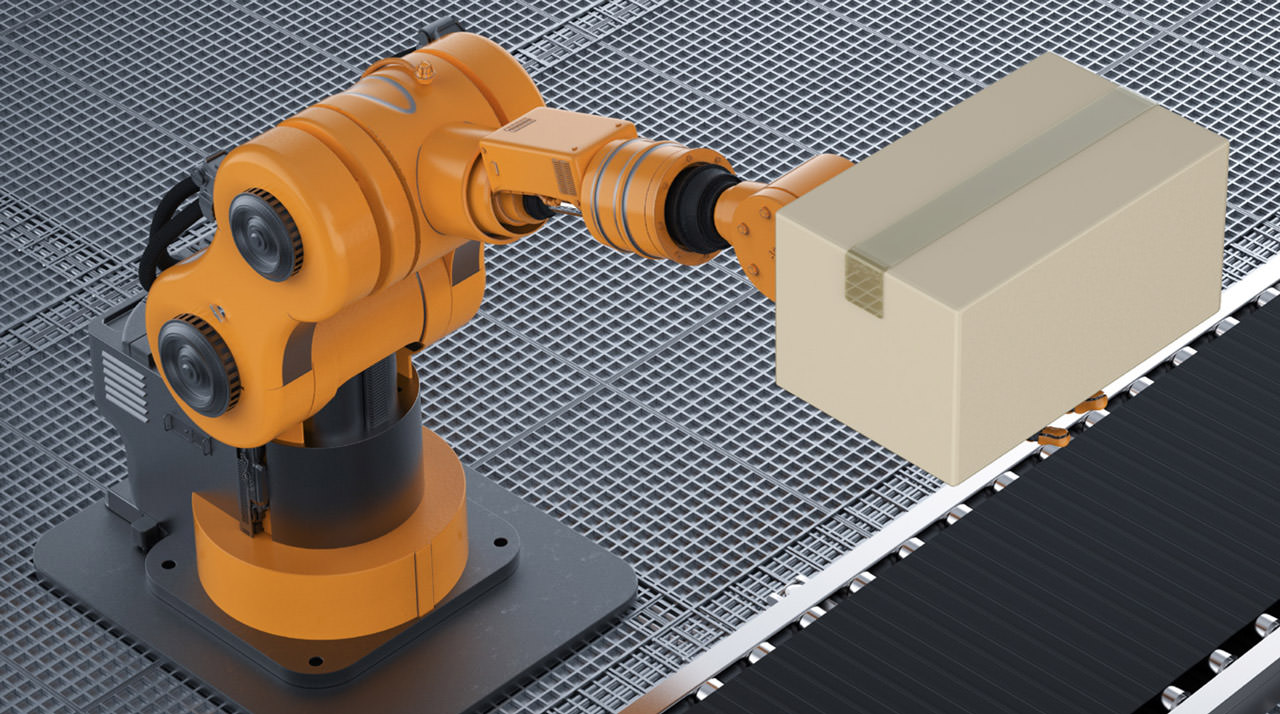
Learn how machine builders and machine users are improving productivity and more. The emergence and continually increasing utility of Ethernet connectivity is opening up new opportunities for creating more productive and more reliable workflows in industrial environments of all kinds.
Slowly but surely, Ethernet has become the communications protocol of choice for machine, robot and other factory automation applications in the industrial/ operational technology (OT) environment. Use of Ethernet is escalating as users identify and implement new ways to capitalize upon the protocol’s advantages over traditional fieldbuses.
This article will discuss several ways in which industrial operators of all kinds are making use of Ethernet technology to increase productivity, improve process reliability and secure other valuable gains on the plant floor. It will also consider these trends from the perspective of the robot and machine builders. OEMs benefit directly from some of these trends as industrial manufacturers themselves.
In addition, they also have the opportunity to differentiate their products and services and gain competitive edge by being well-versed on these trends from their customers’ perspectives, and by working to ensure that their offerings help customers most readily capitalize on them.
Shifting from serial technology
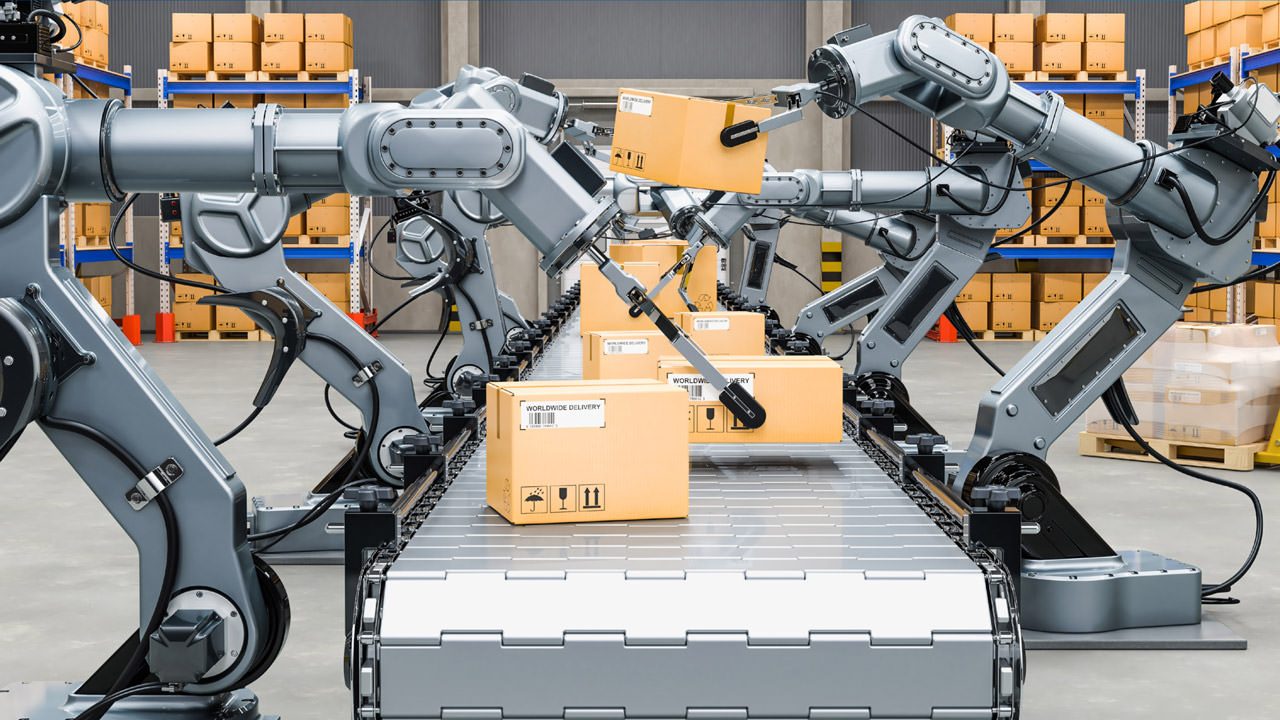
Use of Ethernet technology continues to change how machine builders and machine users gather data.
Industrial Ethernet has been in effective use in plant environments for more than two decades—in fact, Belden introduced its first industrial Ethernet switch in the mid 1990’s. Over much of that time, traditional fieldbuses such as DeviceNet, PROFIBUS and Modbus were the more commonly used protocols in industrial/operational technology (OT) environments, providing reliable and secure service for most users.
Capitalizing on Ethernet-enabled capabilities and more, OT environments of all kinds are integrating machines, robots and other key pieces of automation equipment in new ways, identifying and benefiting from new processes that can lead to even greater productivity and yields, more reliable uptime performance, higher product quality and greater overall profitability.
A specific subset of OT operators, the OEMs who manufacture the original machines and robots, might additionally benefit from some of these insights. Many whether they manufacture several small presses a day on an assembly line or require months to construct a single highly sophisticated machine on a dedicated build floor can benefit from these trends in their own OT environment; they can also benefit from understanding how they might impact the needs of their customers.
When applied properly, Ethernet ports, sensors, devices and other supporting components can help OEMs satisfy identified end-user goals and differentiate themselves in the marketplace.
M2M communication
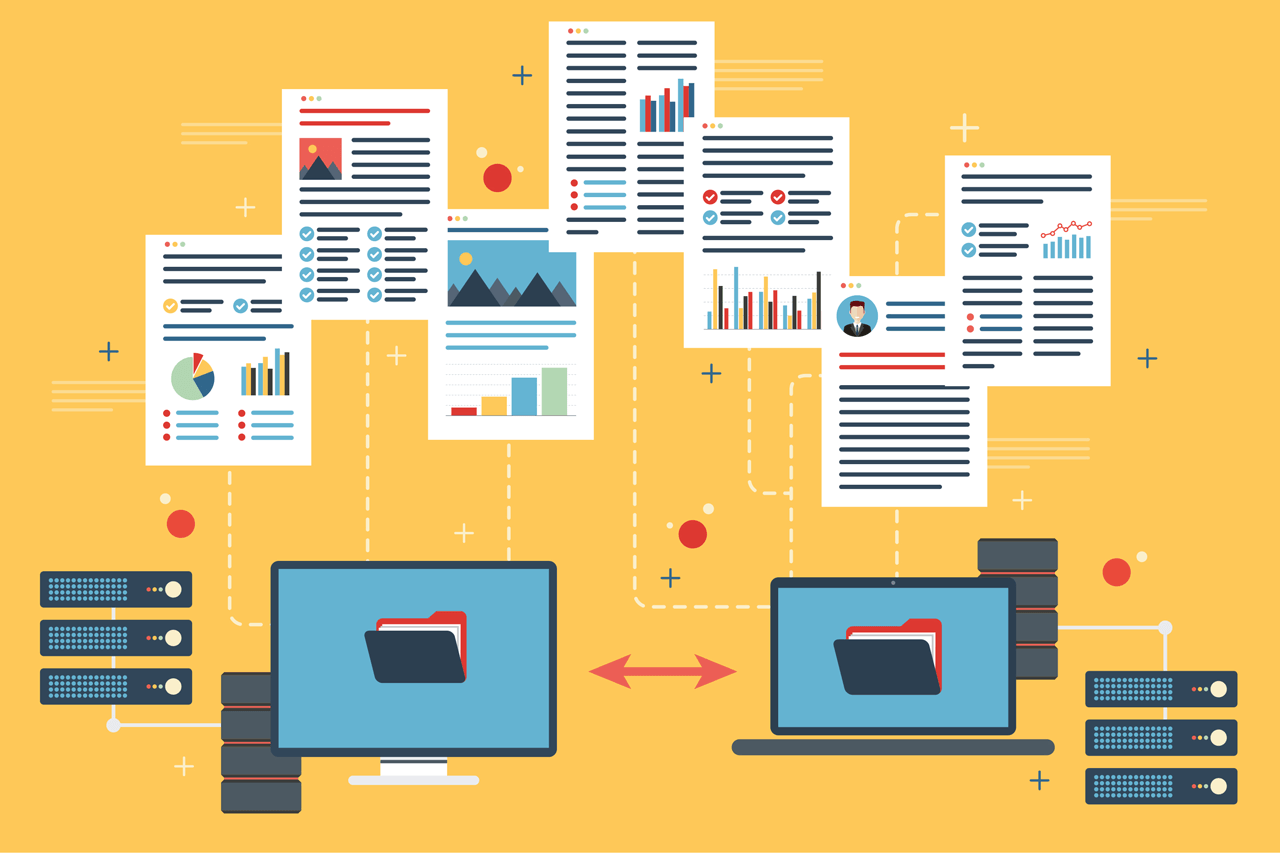
The key to a successful Ethernet installation is building in redundancy that seamlessly shifts transmissions to keep operations running safely.
Ethernet’s ability to communicate instructions at high speeds, accurately to within milliseconds, repeatedly and consistently, opens the door to taking significant human intervention out of the manufacturing equation. It decreases the need for central control as well. Indeed, more and more devices are being developed that control their own logic and behavior and pass instructions directly to the next machine in the line.
For example, an uplink might be created between a robot that precisely places and holds a connector and its partner machine that inserts that connector into a panel. Similar, direct connections can be established between a machine that places an object and the picker that will move it to the next step in the process. Or, a vision system with integrated circuitry and Ethernet ports that performs its own QA can be used to allow passed items to proceed quickly and decisively down the line.
This distributed remote operation can add speed and certainty to the process as well as maintain uptime in aspects of the operation in the event of a central controller issue. Self-contained, stand-alone manufacturing “sub processes” can be strategically developed.
Operators in manufacturing environments in the process of planning a new workflow should consider investigating which small machines might currently be available with onboard controllers installed— there may likely be new products on the market since their last purchase.
And they should discuss the possibilities with their OEMs to see if/how such devices can be incorporated in a line using the appropriate switches and Ethernet infrastructure. OEMs can also consider the reduction in complexity in PLCs and other devices that can be driven by significant distributed control, and the impact that it can have on machine design simplification and cost.
Increasing data capture
The speed and bandwidth of Ethernet is enabling the collection of large volumes of real-time data in ways never before possible. The myriad benefits that this information can enable are still being identified. For example, organizations are using real-time data to perform predictive maintenance by placing a sensor near a wear item and trending changes in temperature or velocity to get the maximum amount of useful life out of a component.
Some are collecting reams of production data secured from smart devices and feeding it through sophisticated analytics packages, allowing them to identify tweaks to a recipe that can optimize yields or lower operating costs substantially in the aggregate. Others are collecting and archiving quality data that can assist with regulatory compliance or liability protection efforts.
Some organizations are well along the way in capturing these benefits; others have barely scratched the surface. Many organizations have likely not gone nearly as far as they can in utilizing the data that lies unrecovered and unexamined in their processes, and there are likely many opportunities for operations of all kinds to reduce their downtime and optimize their productivity by strategically capturing operating data.
End users should analyze their workflow for opportunities as new techniques, software packages and other tools are made available. In addition, they should include machine and robot builders in the discussion about planned communication infrastructure, sensors and other components in their equipment that can help enable valuable new data capture processes. OEMs should be ready to participate in and lead such discussions for optimum win-win partnerships.
OEM-End user partnerships
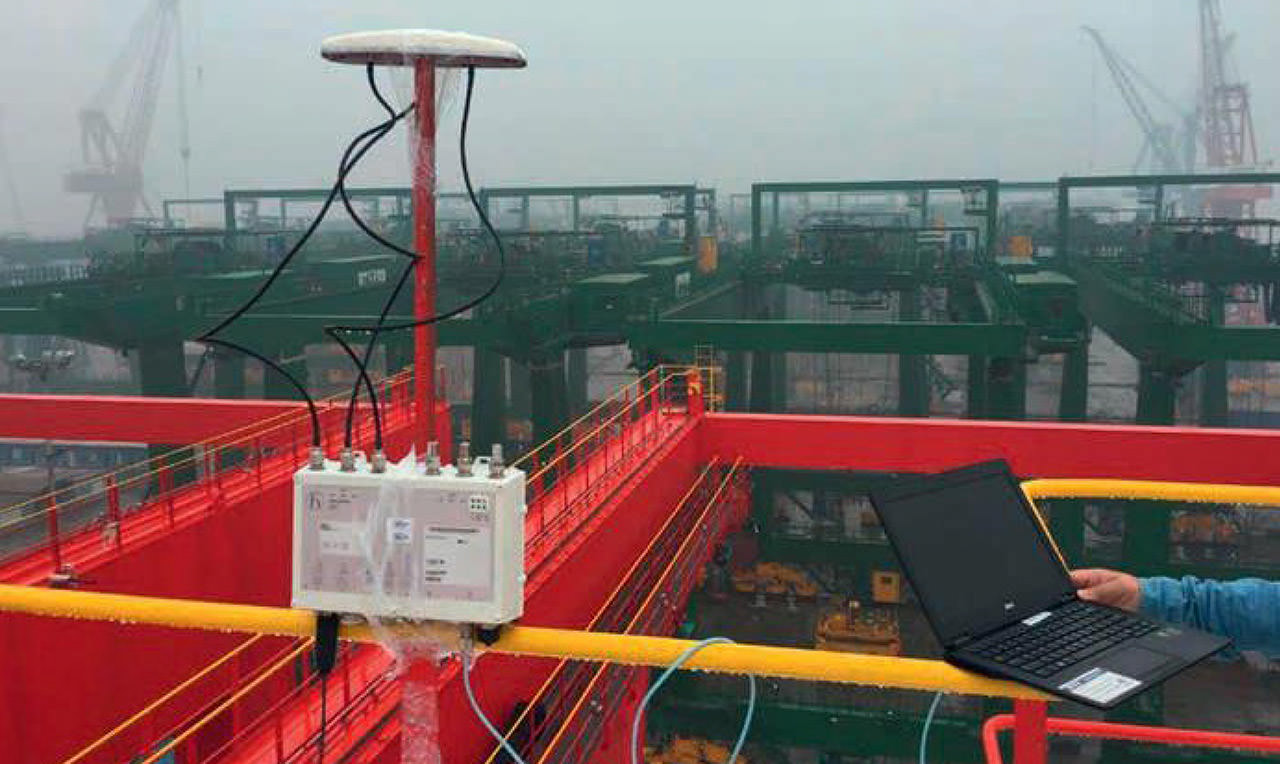
In industrial environments, Ethernet components must be built to withstand harsh operating conditions.
The emergence of Industrial Ethernet opens opportunities for machine builders and machine users to work more closely in the design and planning stages of an industrial network. Thus, this technology enables a win-win environment for long-term partnership and success. That is, opportunities are emerging that keep them profitably connected and in daily communication even years or decades after the initial sale—quite a different scenario than the way the relationship might have been structured in the past.
Ethernet makes this possible by enabling fast access to detailed real- time status and diagnostic information remotely from anywhere in the world. Theoretically, end users can get instant access to the best machine diagnosticians on the planet—the team that actually built the machine— without the downtime and expense of waiting for an emergency in-person call.
Redundancy mechanisms
In the early days of Ethernet OT networks, redundancy technologies fast enough to ensure that data would not be lost in the case of a connectivity failure in the factory were hard to come by.
Many OT environments went without this vital protection completely or installed what was readily available. One such example was spanning tree, a network protocol developed for and successful in the significantly less demanding office IT environment but not fully effective in meeting the needs of the factory environment. Over the years, faster versions based on the spanning tree framework, including rapid spanning tree, were developed and standardized, but still often left users with lost data in the event of failure.
Meanwhile, however, several more robust and sophisticated redundancy technologies—offering recovery in intervals of 10 milliseconds or less and adequate even for mission-critical applications— have been developed. Some are even standards-based.
However, based on our experience in thousands of industrial environments, many operations that could benefit from these faster mechanisms have not as yet adopted them, risking the ability for full recovery in the event of a failure. Those operations that have not recently analyzed their needs in terms of the marketplace should consider investigating protocols such as Device Level Ring (DLR), Media Redundant Protocol (MRP), Parallel Redundancy Protocol (PRP) and High-availability Seamless Redundancy (HSR). The latter two promise zero packet loss redundancy, wherein no data can be lost because packets are actually duplicated as back up.
A key to adapting these types of protocols is the use of managed switches as opposed to traditional unmanaged switches. End users should inquire in the interview planning process as to the machine builder’s capabilities around installing managed switches and other hardware that can provide “built-in” robust redundancy.
Savvy machine builders will proactively ask the redundancy question, offering their expertise and explaining the possibilities to less sophisticated end users—helping deliver maximum uptime for a truly value-added partnership.
Time-Sensitive Networking (TSN)
One of the key benefits of Ethernet over serial networks is the protocol’s ability to control high speed manufacturing processes, such as the desired hand-off actions between machines in an assembly line, down to milliseconds, on a constant and repeatable basis.
Currently, an “upgrade” to Ethernet, called Time-Sensitive Networking, is emerging that promises to allow manufacturers to control processes significantly more accurately still—down to the microsecond and possibly even into nanoseconds.
As this technology continues to emerge, manufacturers of all kinds will have the opportunity to re-imagine their workflow and consider where opportunities for more precise and more controllable processes might be advantageous, perhaps allowing fine-tuning that boosts productivity and yields and improves safety even further in their facilities. And, ultimately, many savvy machine builders will offer “TSN-ready” capabilities built into their equipment as an option to end users looking to gain a competitive edge.
Cyber security, staffing and more
Unfortunately, these beneficial Ethernet trends can also bring with them a number of vexing challenges for end users and machine builders.
First and most serious among them relates to the fact that the same increased connectivity that drives many of Ethernet’s productivity and reliability benefits also opens the OT network up to outside influences, and therefore viruses, worms, ransomware, malicious targeted hacks and other dangers that can bring the line to a screeching and costly halt.
Some operators think of cyber incidents as an issue only impacting IT networks archiving credit cards or other readily “monetized” data. However, in the OT world, intellectual property can be misappropriated, production can be sabotaged, safety can be compromised and more, both for gain and for sheer maliciousness, as many organizations have discovered the hard way. In addition, even accidental cyber events, inadvertently put in motion by a careless colleague, are taking their toll on operations of all kinds.
No matter how they are initiated, even a single event can cause significant negative impact on productivity, schedules, reputation, quality and more—often to the tunes of millions of dollars per incident. Of special note, while cyber attacks often originate through unprotected networks, OEMs and their customers should be aware that sometimes, networkable devices such as PLCs, HMIs, drives and I/O blocks can become “pre-loaded” with malware or spyware by hackers before they even reach the build floor, much less the end user location.
OT network professionals should be aware of the increasing threats, and be sure to work to build up their cyber security posture in lock step with building their connectivity and reaping the productivity and reliability benefits thereof.
Machine builders and end users can work together to make equipment as “cyber security ready” as possible, with the appropriate firewalls, switches or even more sophisticated devices pre-installed, as opportunities and machine purpose dictate. Care should also be taken to ensure that all devices installed contain the latest, fully patched versions of all software and firmware.
If the expertise to coordinate these processes is not available in house, the increasing demand for cyber security guidance is ensuring a healthy availability in the marketplace, with Belden subsidiary Tripwire perhaps among the most proven and experienced. Such experts can often help with optimal machine design as well as optimum network design. Fortunately, maintaining high levels of cyber security is not insurmountable— the expertise and technology is readily available. Often it is more lack of awareness, lack of action and lack of allocated resources that open organizations up to cyber security issues.
The increasing need for personnel well versed in both Ethernet networking and OT automation is leading to the creation of a new breed of professionals. While earlier on, many Control Engineers “borrowed” networking expertise on an ad hoc basis from their IT colleagues, the need to learn automation in depth often necessitates a desire for more permanent assistance. While that does mean greater head counts, perhaps, the benefits of in-house expertise in this fast-moving environment, with the stakes so high and the opportunities so vast ensures that most find it well worth the addition of key individuals or even departments.
Professionals for hire adept in both sides of the house, while still rare, are becoming less so as demand increases. What is emerging is an Automation and Data Exchange Engineer, or ADX Engineer, who understands the needs of both IT and OT. This new position facilitates and manages the requirements of IT and OT so that both of their needs are met.
Also extremely helpful is the emergence of value-adding partners such as network equipment suppliers who are offering automation engineers free or low cost vendor-agnostic training in networking topics with a focus on the unique characteristics and requirements of industrial networks, using familiar OT examples, as opposed to traditional IT examples. Much has been said about the differing mindsets of IT-trained and OT-trained professionals and how they each lack understanding of the other. However, in reality, our experience shows that a truly skilled person entering a new department will learn the needs of the new environment and adapt their skills accordingly.
Finally, industrial professionals should understand that, when specifying Ethernet equipment, whether for their own networks or to be incorporated into a larger machine, IT Ethernet equipment and OT Ethernet equipment are not always interchangeable if one wants to achieve optimum performance. That is, although they operate similarly in purpose, the environments in which they will be placed can differ substantially and such exposures should be taken into account.
In many cases, electronic devices and cables were designed years ago and their housings were made to be used in a fairly climate-controlled office-type environment, with little thought to the factory environments that may have growing need for them. For example, devices and cabling in an OT environment may be exposed to extremes of heat or cold, excessive vibration, dirt and dust, cutting and crushing, continuous motion, moisture or signal-degrading industrial noise— any of which can cause an interruption to network operation and unplanned downtime.
Fortunately, this type of equipment and cabling are readily available in more robust “industrial strength” versions, so be sure to seek these out—or offer to incorporate them into a larger machine—if the end user environment could benefit from more durable and resilient options.
Conclusion
The emergence and continually increasing utility of Ethernet connectivity is opening up new opportunities for creating more productive and more reliable workflows in industrial environments of all kinds. Knowledge of emerging and continuing trends can give savvy operators the opportunity to grab competitive advantage by developing creative ways to incorporate new technologies into work processes, increasing yields and reducing downtime.
Machine builders can not only take advantage of these trends for their own operations, but they can also use their knowledge of trends to more effectively interact with end user customers, develop even more useful products, and create even stronger long-term, mutually beneficial ongoing partnerships.