TechnologyMarch 9, 2020
IIoT in automation from machines to the cloud and back
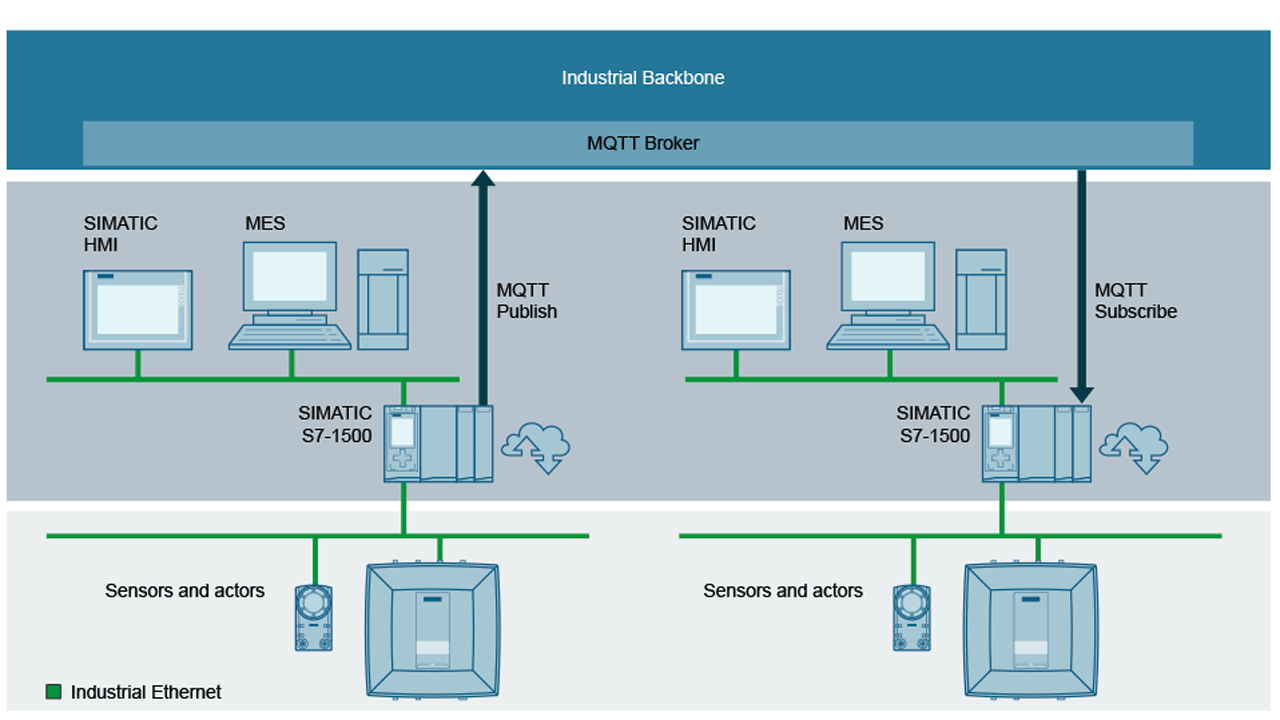
Use of digitalization offers new possibilities for optimizing manufacturing processes by leveraging data analytics through cloud-based systems. New communication methods for automation systems via standards-based open protocols such as MQTT is helping users fully integrate components regardless of manufacturer.
Advancing digitalization offers new possibilities for optimizing production processes. Use of state-of-the-art components to connect a controller to a cloud system can increase productivity and thanks to extended maintenance intervals provide for an uninterrupted production, leading to a significant competitive advantage for the enterprise.
Digitalization is changing today’s production and business processes of modern companies more and more. The increasing availability of data and advanced Industrial Internet of Things systems provide greater opportunities to optimize the production process throughout the entire chain by skillfully analyzing the data. In doing so, the maintenance intervals of the machines used can be extended and unplanned downtime be avoided.
After connecting a machine to a cloud system, for example, data on the motion sequence can be transmitted to it and comprehensively analyzed there. In case of deviations from the set point, the failure of the machine can be predicted from the absolute deviation as well as from the rate of change.
As a result, maintenance intervals based on the analysis result from the data can be planned dynamically and precisely. This approach is called predictive maintenance and represents a major use case for using cloud-based systems.
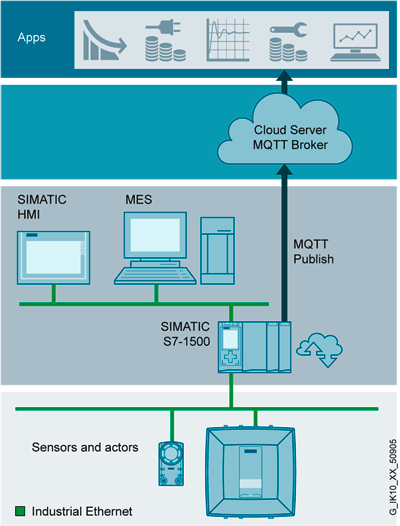
Data transmission communicates from an automation system to a cloud system for the further analysis.
Use of MQTT
For the integration into modern cloud-based systems, the open standard protocol MQTT (Message Queuing Telemetry Transport) is often used. It is a simple protocol based on the client/server principle, where the participants (clients) communicate as MQTT Publisher or MQTT Subscriber via an MQTT Broker (server). Devices only wanting to send data to a cloud system use the MQTT Publish function.
In the context of digitalization in the company, the opportunity presents itself to employ a system such as MindSphere, the cloud-based, open IoT operating system from Siemens, which makes it possible to analyze data from a machine by means of special apps in order to determine the optimal maintenance time for the machine.
However, it is very important for the user to identify in advance the data to be transmitted to the cloud system. It is advisable to proceed frugally here, since an optimal data selection not only leads to better clarity in the cloud system, but also optimizes the data load in the network. In addition, the data volume in the cloud system is reduced (saving money).
The heart of a machine from which data is to be transmitted to a cloud system frequently consists of an automation system of the type SIMATIC S7-1500, which ensures the proper process sequence within the machine. By using appropriate sensors to record, e.g., temperature, vibration, or rotational speed of axles and motors, deviations can be determined over a longer period and downtime be planned much more precisely, or unplanned downtime be detected earlier.
Communication processors
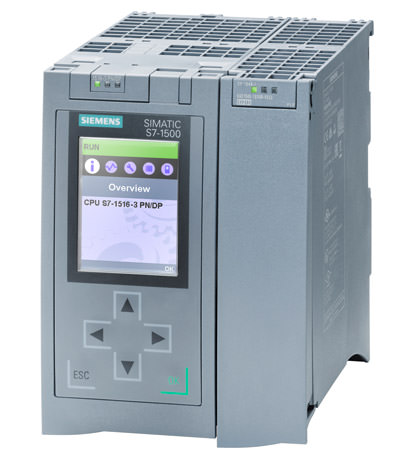
SIMATIC communications processor and controller.
A new communications processor CP 1545-1 is available for integration into the modular automation system SIMATIC S7-1500. Via the MQTT protocol, the MQTT Publish function can be used to transmit selected data from the automation system to the cloud system.
After entering the access details for the cloud system in the configuration software TIA Portal, the data to be transmitted is also selected there using data points. Besides the name of the selected data point, other attributes are defined, such as timestamp, data type, status, or limits.
The transmission of data via MQTT additionally requires the entry of a name for a topic to which the data points are assigned. By means of topics in the MQTT protocol, the user structures the data to be transmitted according to the desired topic.
When using multiple topics, it is therefore possible to assign the data to be transmitted according to the different function of the data points. An example would be machine1/TemperatureSensor2. Of course, this structure must also be mapped in the cloud system for the data to be processed correctly.
For the transmission of the data to the cloud system, the user also defines corresponding trigger conditions. Thus, data can be transmitted either via a time trigger (e.g., once a day or cyclically) or according to a threshold trigger (e.g., value lies outside a defined range).
It is of course also important for the operation of this solution that user already thinks in advance about the necessary security. This also depends on the cloud platform used and on the locally installed (on-premise) or Internet-based solutions.
Since MQTT can be encrypted using Transport Layer Security (TLS), the CP 1545-1 already provides the first component for comprehensive security, which can be easily activated for the module in the configuration software TIA Portal.
To protect the cell, the integrated firewall of the CP 1545-1 can be used in addition. Since the user is responsible for the security of the installed solution, it is generally recommended that a holistic security concept be implemented in which the functions mentioned are only one component.
If the user is now able to send data to a cloud system and analyze it there with the help of apps, the idea of wanting to use the analysis result to send data to the machine according to the instructions of the user inevitably comes up. This can, if it is determined in the context of predictive maintenance that increased wear has occurred, serve to put the machine, for example, in an emergency state to protect the components.
If a cloud system is able to send data to a machine, the CP 1545-1 in the SIMATIC S7-1500 automation system is already prepared for this. For instance, it can already send data via MQTT Publish to an MQTT Broker installed in the Industrial Backbone or receive data from an MQTT Broker it via MQTT Subscribe.
Conclusion
Advancing digitalization offers new possibilities for optimizing production processes by skillfully leveraging data analytics through cloud-based systems, creating a competitive advantage for the enterprise. New ways of communication for automation systems via standards-based open protocols such as MQTT help users to fully integrate components regardless of manufacturer.
In the future, the possibilities of receiving data in the systems could further simplify the processes. The technical requirements are already provided by some products today, such as the SIMATIC CP 1545-1 communications processor.