TechnologyJanuary 10, 2023
Role of IIoT sensors and cloud in data-driven maintenance
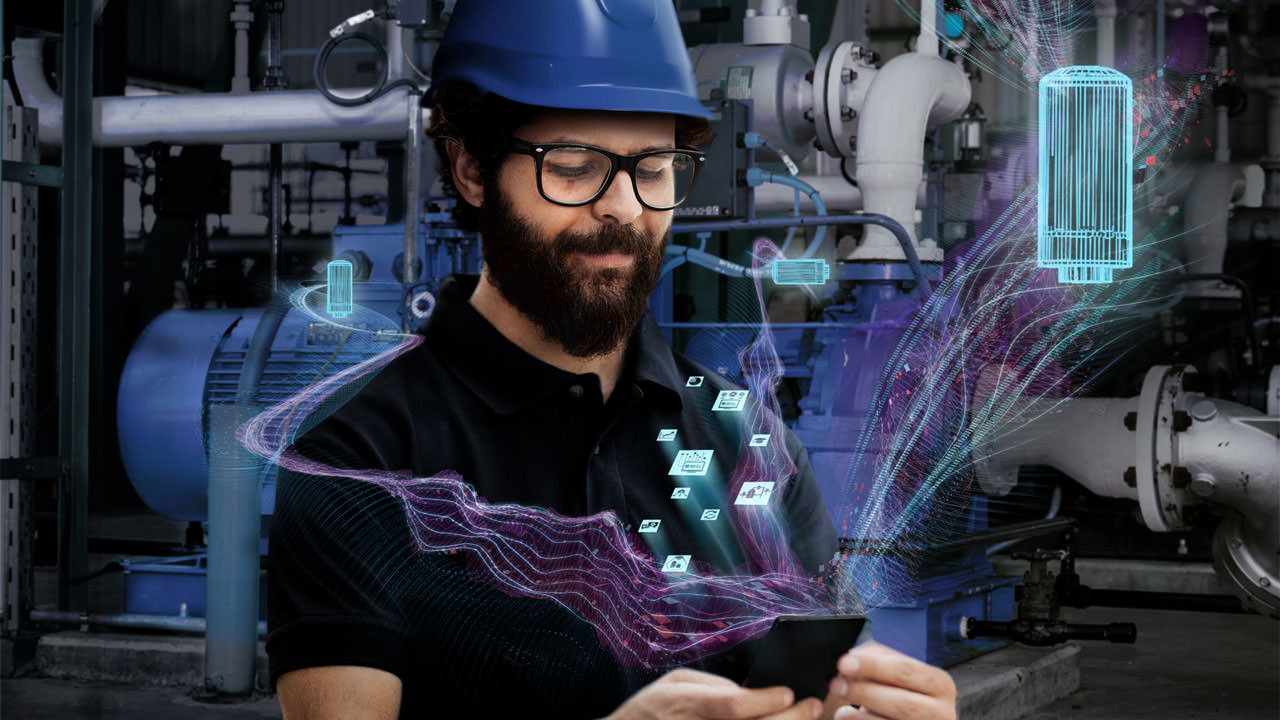
Smart condition monitoring uses artificial intelligence to make mechanical plant components fit into data-driven maintenance models. In these systems, IIoT sensors monitor and gather vibration and temperature data which is sent via Bluetooth to gateways, and from there to a cloud application for analysis.
In terms of IIoT, Smart Factory or digitalization in general, the lack of actual implementation is often due to many unresolved questions: Where to start? With the supply chain? In production? Or with distribution? What is the resource commitment required for this? And what is the goal to be achieved? Discover an application yielding quick results.
Just as other process industries, production facilities in the food industry have matured and heterogeneous infrastructures. Ultra-modern and networked plant components stand alongside closed production units that have been operating reliably for many years. The degree of automation of individual lines differs, etc. All in all, the lines are integrated into systems ensuring stable production performance and high product quality.
In any case, this includes maintenance and repair management. However, traditional maintenance models based on experience, legal requirements and fixed maintenance intervals quickly become cost-intensive for extensively automated lines with many integrated units and are outdated today. Modern plant components monitor their health status independently and provide the basis for so-called condition-based maintenance. In this monitoring maintenance, measures are taken based on the current state of wear and not according to fixed schedules.
But what about machines that don’t have built-in self-diagnostics? For such mechanical components still largely lacking automation and communication capabilities, Siemens has developed a system that propels these plant elements into the league of IIoT devices in just a few steps.
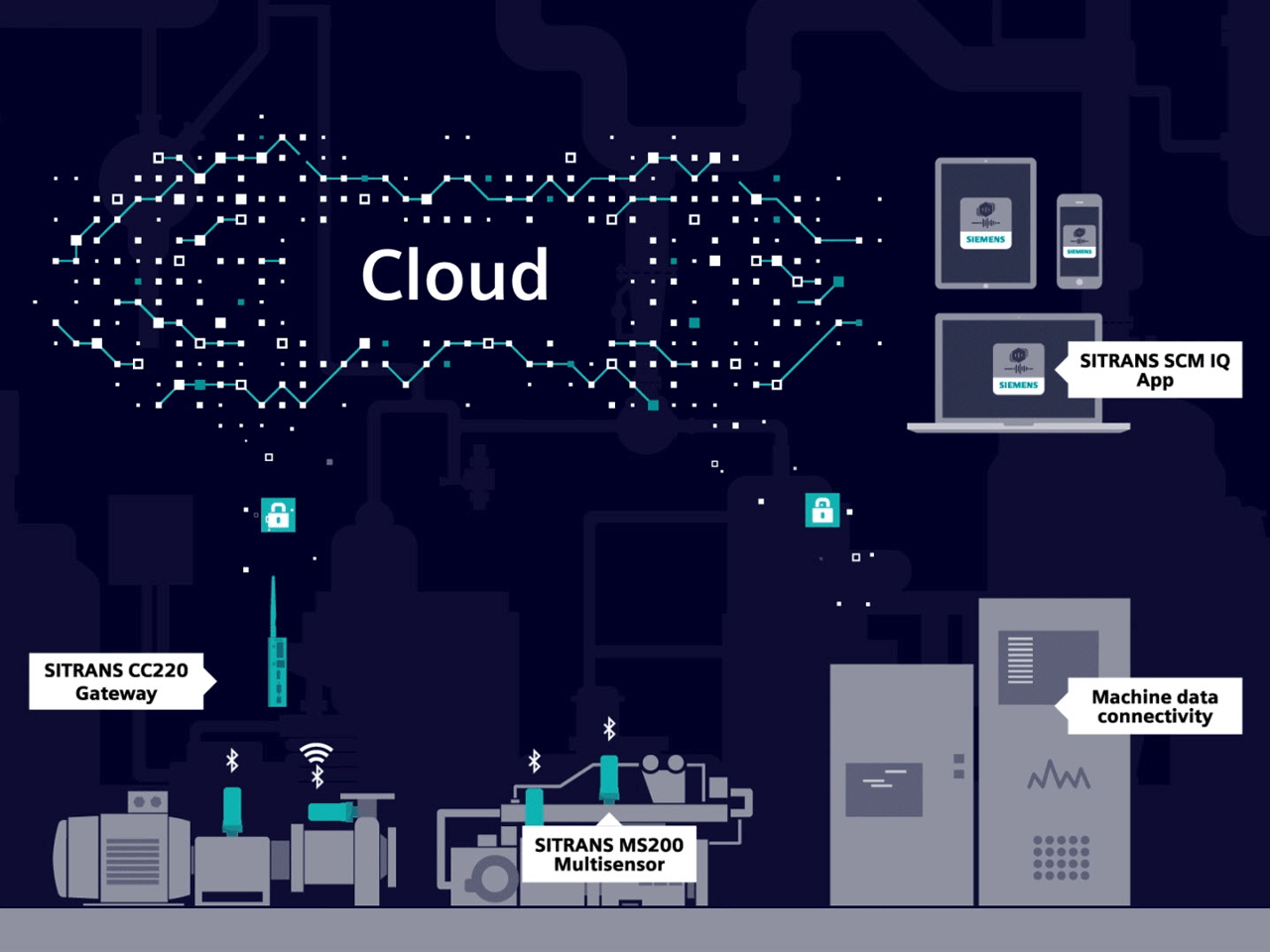
Making mechanical plant components fit for the future: Enabled by an intelligent combination of IIoT sensors, gateways and cloud services – easily retrofittable.
IIoT for retrofitting
The system is autonomous and does not influence the process operation to any extent. This circumstance, coupled with very simple installation, makes Sitrans SCM IQ a partner for the move into digitalization and thus opens up ways to significantly more efficient maintenance strategies and higher plant availability.
Sitrans SCM IQ from Siemens AG is a smart condition monitoring system using artificial intelligence to make mechanical plant components fit for data-driven maintenance models. For this purpose, IIoT sensors are screwed onto the machines to be monitored and gather vibration and temperature data which is sent via Bluetooth to gateways, and from there to a cloud application for analysis. Artificial neural networks constantly monitor vibration characteristics, and event-based warnings are issued in case of deviations that indicate an impending asset failure.
Example: Pumps in the cloud
Food production involves a lot of movement. This process requires, for example, pumps that are subjected to high loads. Normally, these aggregates are embedded in a rigid maintenance plan and are additionally serviced on the basis of experience and trained observation.
The lack of data, communication options, computing capacity and visualization options prevents the integration into a monitoring or even predictive maintenance system.
It is precisely along this signal chain that Siemens has bundled products and services in Sitrans SCM IQ. To start with, the pump is equipped with one or several Sitrans MS 200 multisensors, depending on the scope of the monitoring. The IIoT sensors are housed in a robust industrial enclosure with IP 68 protection, which is screwed directly onto the plant component using a stud bolt or grub screw. In principle, the multisensors work with all assets that vibrate or rotate and that are within the range of the sensor’s specification.
The battery-powered sensors do not need to be wired. The vibration and temperature data are sent via Bluetooth Low Energy (BLE) to the next link in the chain, the decentralized data processing in cloud gateways. A Sitrans CC220 gateway can receive the transmitted information from several multisensors and transfer it from there to the cloud – the industrial IoT-as-a-service solution MindSphere.
All paths are fully encrypted from the sensor, to the gateway and from there to the cloud and the apps. In the cloud application, the delivered data is analyzed and monitored for anomalies. Finally, the last link in the chain is visualization. Via the Sitrans SCM IQ app, the user is always informed about the status of his monitored plant components.
Turning data into added value
Once the battery is installed, the sensor initializes and is reported to the corresponding Sitrans CC220. After configuring the gateways, everything is ready on the machine side. As soon as the connection with the cloud application is established, vibration and temperature data are transferred to it and the learning phase begins:
Over a period of approximately two weeks, the system learns about different operating states of an asset.
Using statistic methods and explorative data analysis, the application detects patterns in the data streams and selectively assigns them to the good state. During this time, the user does not have to document the operating states or explicitly report them to the system.
Obviously, the system will likewise recognize a condition not yet learned as an anomaly at first, for example a load condition or CIP operation that has not occurred before. The good state can be conveniently extended by re-learning the corresponding time periods. The application does not only allow to evaluate the vibration and temperature data of the multisensors.
In fact, the methods can also be applied to other machine data available in the cloud, such as speed or counter values. Thus, already built-in aggregates can be very easily and conveniently integrated into a condition-based predictive maintenance strategy.
Once the training phase is over, Sitrans SCM IQ reliably detects deviations: If an anomaly occurs due to increased vibration, the system reports that a machine part is on its way to bad condition. The maintenance specialists are informed by SMS or e-mail.
After checking the corresponding machine part and determining the cause, the app feeds back the results to the system, e.g. signs of incipient bearing or seal damage, an imbalance, etc. In addition, the maintenance steps performed on the machine can also be documented. If the same characteristic deviation occurs at any time, Sitrans SCM IQ reports that it is very likely the same incipient fault and how it can be resolved.
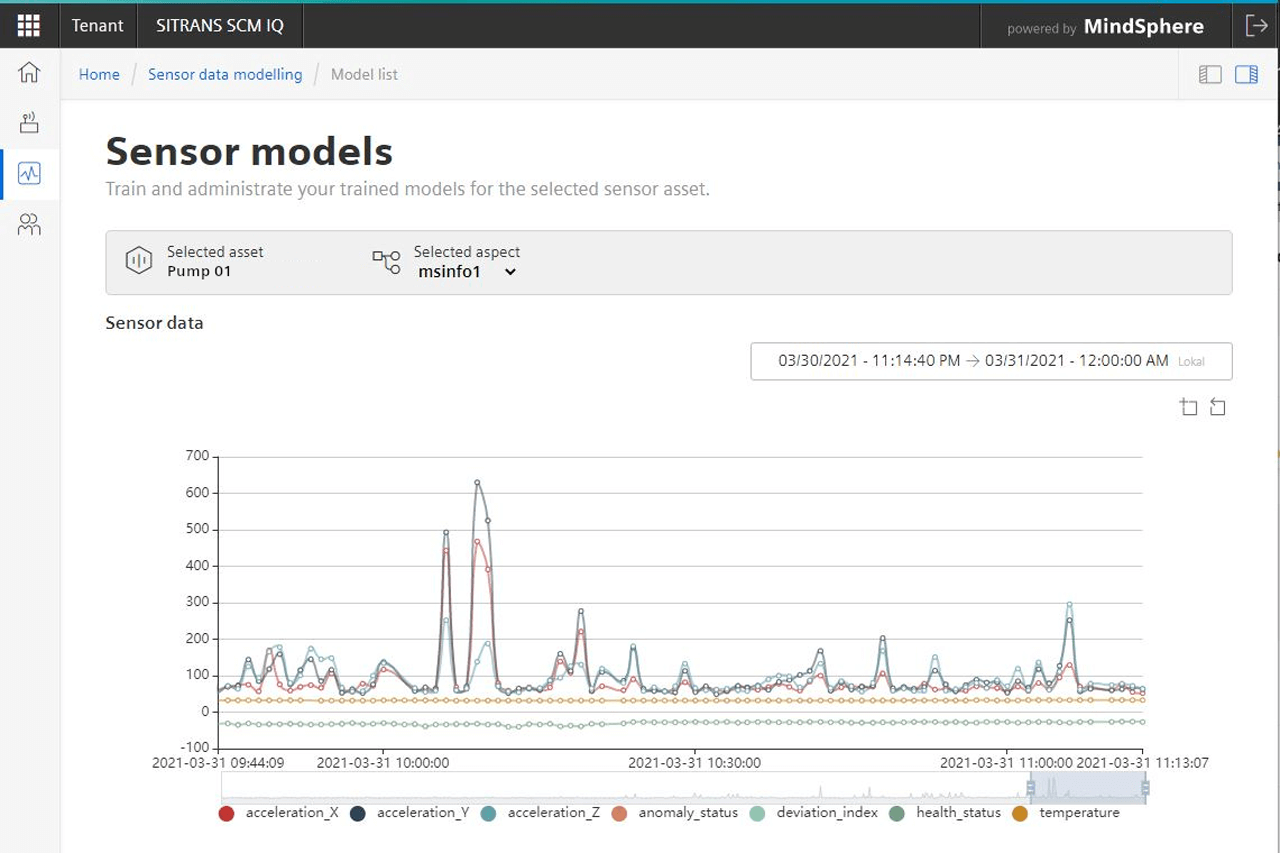
Is everything running smoothly? Vibration and other data from machines such as pumps or fans are clearly visualized in dashboards. Automatic notification is sent in the event of anomalies.
Quick wins and long-term successes
On this basis, condition-based predictive maintenance is possible, resulting in far greater plant performance than corrective and preventive approaches.
Sitrans SCM IQ allows users to retrofit individual aggregates or entire machine parks with a condition monitoring system in a very cost-effective way and with little installation effort.
To get started, a clear use case is recommended, such as a pump used in a problematic process step. Valuable insights can be expected here within a short time due to the retrofitted condition monitoring. The system can then be easily extended to other assets or entire lines or plant sections by installing additional sensors and gateways. Sitrans SCM IQ was partly developed as a co-creation project between Siemens and Coca-Cola Hellenic Bottling (Coca-Cola HBC) Company’s plant in Edelstal, Austria. The customer’s feedback was directly used to improve the products.
Within six months after the system was installed, managers at Coca-Cola HBC saw a demonstrable reduction in downtime. Four unplanned line shutdowns were averted during this period thanks to timely maintenance measures. At the same time, plant performance improved because maintenance measures could be planned and combined over the long term.