TechnologyNovember 7, 2022
60 GHz wireless data interconnect for slip rings
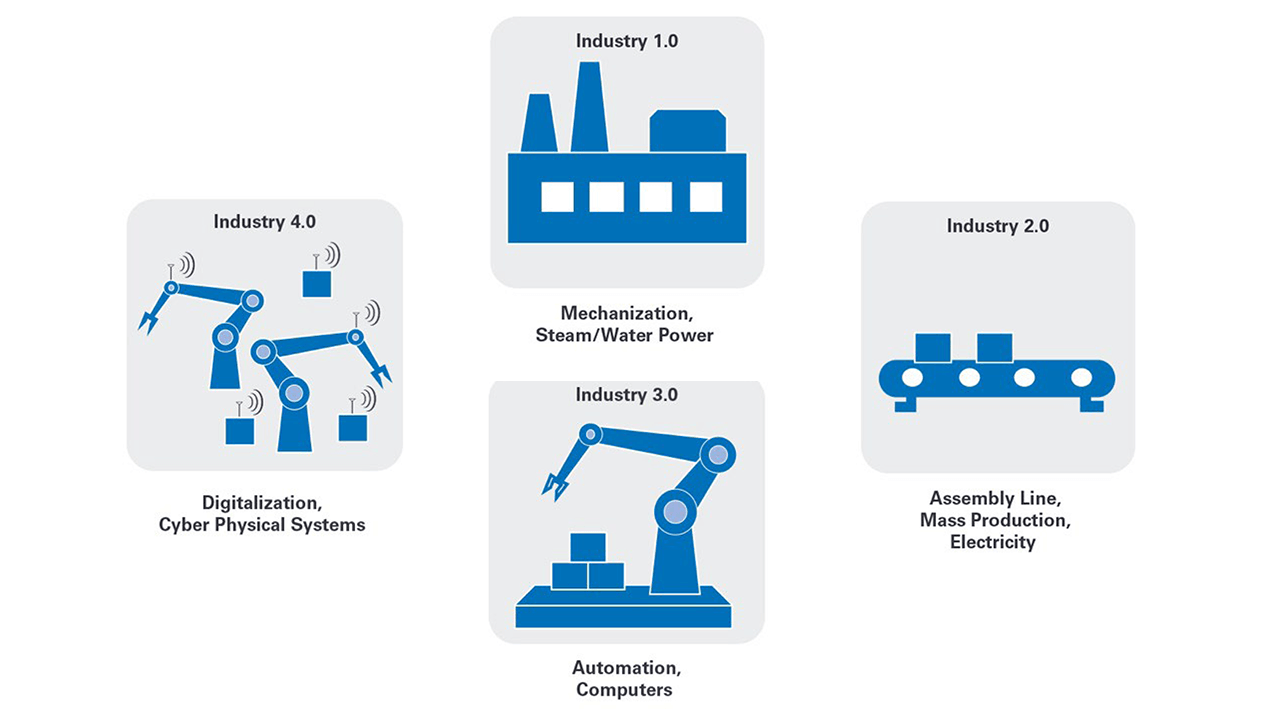
High performance integrated and discrete RF and microwave components can be implemented across the entire frequency spectrum to enable application specific designs for a contactless Gbps-level data transmission via rotary joints.
The fourth industrial revolution drives digital manufacturing forward by implementing new scenarios into the production process. These scenarios rely on fundamental design principles that include device interconnection, information transparency, technical assistance, and decentralized decisions. The realization of all these principles in modern smart factories would not be possible without advanced wireless communication technologies. They enable multifaceted applications for a broad range of areas including process automation, asset tracking, machinery control, intralogistics, and infrastructure networking.
Smart factories incorporate various cyber-physical systems that require faster and more reliable wireless solutions to handle ever increasing amounts of data in the toughest industrial settings. The main drivers facilitating new developments of these solutions to be deployed in highly demanding Industry 4.0 scenarios include the implementation of mobile SCADA, replacement of legacy systems, and realization of data transmission from moving equipment where it was not possible or was limited before. This article focuses on the wireless technologies driven by this latter aspect.
The first part of the article summarizes the main requirements imposed by modern industrial applications on a communication interface between mechanically rotating subsystems. The second part attempts to classify numerous data interface technologies employed in these subsystems today according to the type of mechanisms used to transmit data between a rotor and a stator. It gives a concise overview of these technologies and discusses their main advantages and disadvantages. The third part of the article proposes a novel 60 GHz wireless solution for high speed, low latency communication that enables realization of advanced data interface architectures in slip ring assemblies to meet the demanding requirements of new industrial scenarios.
Industrial Requirements for Data Interfaces in Rotary Joints
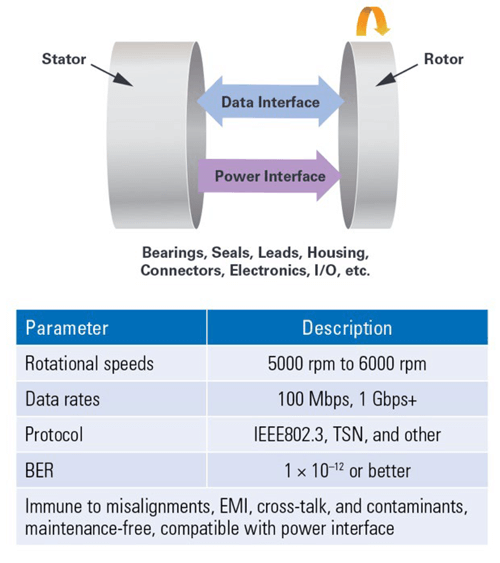
Figure 2. Rotary joint—high level block diagram and requirements.
A rotary joint, also often interchanged with the term slip ring, is an assembly for transmitting data and power across a rotating connection (see Figure 2). The growing need for faster and more reliable data transmission between rotating components in modern industrial scenarios imposes strict requirements on bandwidth, crosstalk, and EMI performance of the data interfaces used in rotary joints. Meeting these requirements is essential to guarantee real-time operation, continuous uptime, and maximum efficiency of the corresponding industrial equipment.
Industrial rotary data interface assemblies must ensure constant transmission quality at very fast rotational speeds of 5000 rpm to 6000 rpm at rates of typically 100 Mbps. In most cases these data rates are sufficient, but some specialized applications require faster transmission at 1 Gbps and higher, which is becoming a fairly standard benchmark nowadays. Industrial applications also call for support of IEEE802.3-based (Ethernet) and other industrial bus protocols, as well as deterministic real-time communication, to permit time sensitive applications and IIoT functionality. Data interface solutions designed for these applications must be immune to physical misalignments, electromagnetic interferences, and crosstalk to enable error-free data transmission with bit error rates (BER) of 1 × 10−12 or better. Contaminants present in the industrial environment should not affect the operation of a rotary joint that ideally must be maintenance-free and not suffer from wear. Finally, the data interface technology must be compatible with power transmission subsystem of a rotary joint assembly to meet all functional requirements of a target application.
Data Interface Technologies
There are different types of rotary joints that vary in terms of their functional features, form factor, rotational speeds (rpm), maximum data rate, power ranges, type of supported interfaces, channel count, and many other design aspects shaped by application requirements. Among these design considerations, the data interface has some of the most critical requirements and it is therefore crucial to make the right choice of technology for its implementation in a slip ring assembly. Data communication technologies used to realize this function can generally be classified into contacting and contactless. They abound with many variations depending on the type of coupling they utilize in order to realize a communication channel for data transmission.
Contact-Type Interfaces
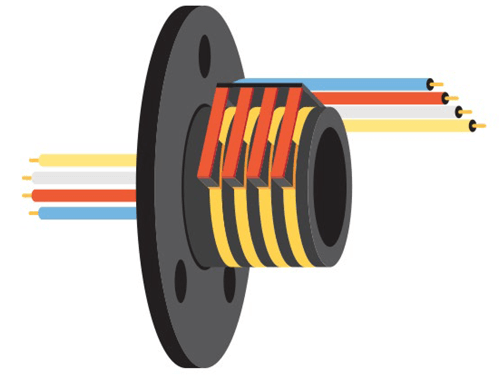
Figure 3. Contact-type slip ring. Courtesy: Servotectica/CC BY-SA 4.0.
Contact-type solutions typically rely on composite, monofilament, or polyfilament brushes on a stator that slide against conducting rings on a rotor, thereby creating an uninterrupted passage of electrical signals between moving and stationary components (see Figure 3). The selection of brush type with regard to data communication depends on the signal bandwidth, data transfer rate, required transmission quality, operational currents, and rpm. Although this is a well-established technology that has been employed in slip rings since their invention, it has certain limitations. Reliability of contact-type slip rings suffers in harsh operating environments due to the presence of mechanical contacts requiring regular maintenance. Electromechanical rotary joints are also prone to electromagnetic interference. In addition to that, the characteristics of the physical media used to establish the contact interface, as well as various mismatch effects, have a strong impact on the channel bandwidth. Moreover, sliding contacts generate electrical resistance variation that degrades the transmission quality, which can be especially critical in high data rate real-time applications.
Contactless Interfaces
Contactless rotary joints overcome those limitations by using radiating or non-radiating electromagnetic fields to transfer the data across rotating parts. This technology offers several performance advantages over electrical signal transmission. The lack of mechanical contacts avoids contact wear requiring less maintenance and does not suffer from data loss arising from resistance at high rotational speeds.
Fiber Optic Rotary Joints
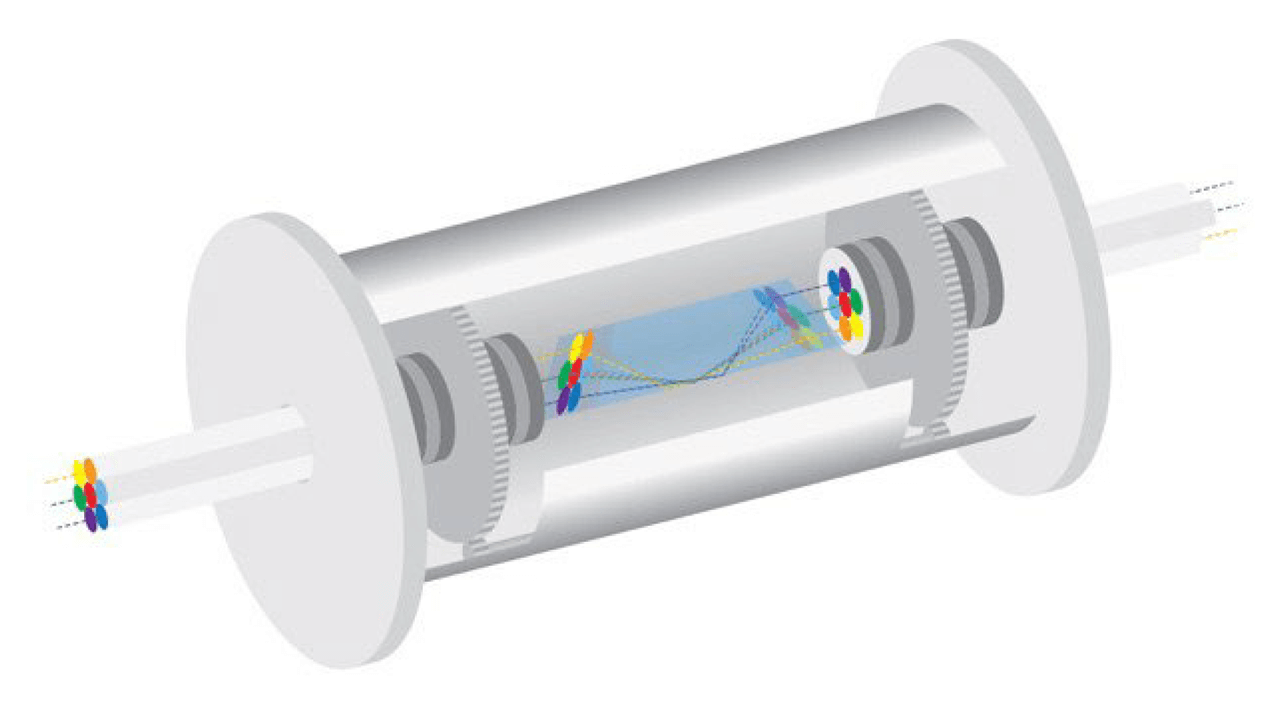
Figure 4. Fiber optic rotary joint. Courtesy: Servotectica/CC BY-SA 4.0.
The most common example of a contactless solution is a fiber optic slip ring known as a fiber optic rotary joint (FORJ), which is schematically shown in Figure 4. FORJs rely on optical radiation to transfer data and operate typically at infrared wavelengths between 850 nm and 1550 nm allowing EMI-free transmission of every kind of analog or digital optical signal at very high data rates of several dozens of Gbps.
However, fiber optic solutions are not without challenges. They experience strong extrinsic losses that result in signal attenuation caused by angular and axial misalignments. These misalignments are also the main contributor to rotational signal fluctuations that can be critical in some applications. Moreover, fiber optic rotary joints usually require high levels of protection in harsh industrial environments.
Inductive and Capacitive Interfaces
Another type of contactless technology is based on near-field coupling mechanisms realized through electric and magnetic fields generated by primarily non-radiating inductive and capacitive circuit elements in lower frequency bands of the electromagnetic spectrum.
Inductive method applies the principle of electromagnetic induction to interface moving parts of an assembly. Slip rings using this type of coupling, which is schematically depicted in Figure 5, are useful for industrial applications with high rotational speeds but they are more suitable for transmission of power rather than for transmission of high speed data. They are widely used in wind turbine applications to provide electrical signals and power for blade pitch control systems, and in packaging applications where moving parts run at high rpm.

Figure 5. Inductive coupling.
In contrast to inductive slip rings relying on a magnetic field, the slip rings based on capacitive technology use electric fields to transfer data between a rotor and a stator. The capacitive coupling method shown in Figure 6 offers the realization of a relatively low cost and light weight solution with negligible eddy current losses and excellent misalignment performance. This technology enables reliable data transmission at high speeds of several Gbps in harsh operational environments and independent of rotational speeds. Capacitive slip rings are often designed for a combination with Ethernet field buses and they are broadly used in time sensitive industrial applications.
Other Types of Interfaces
Apart from contactless slip ring technologies utilizing primarily inductive or capacitive coupling mechanisms, solutions relying on a combination of both types of mechanisms can be realized by using proper coupling structures such as waveguides or transmission line elements. There are also special types of slip rings: for instance, those relying on mercury as a conduction media. However, mercury-wetted slip rings have strict demands for operational environment settings and cannot be used at high temperatures, which makes them not suitable for industrial use cases.
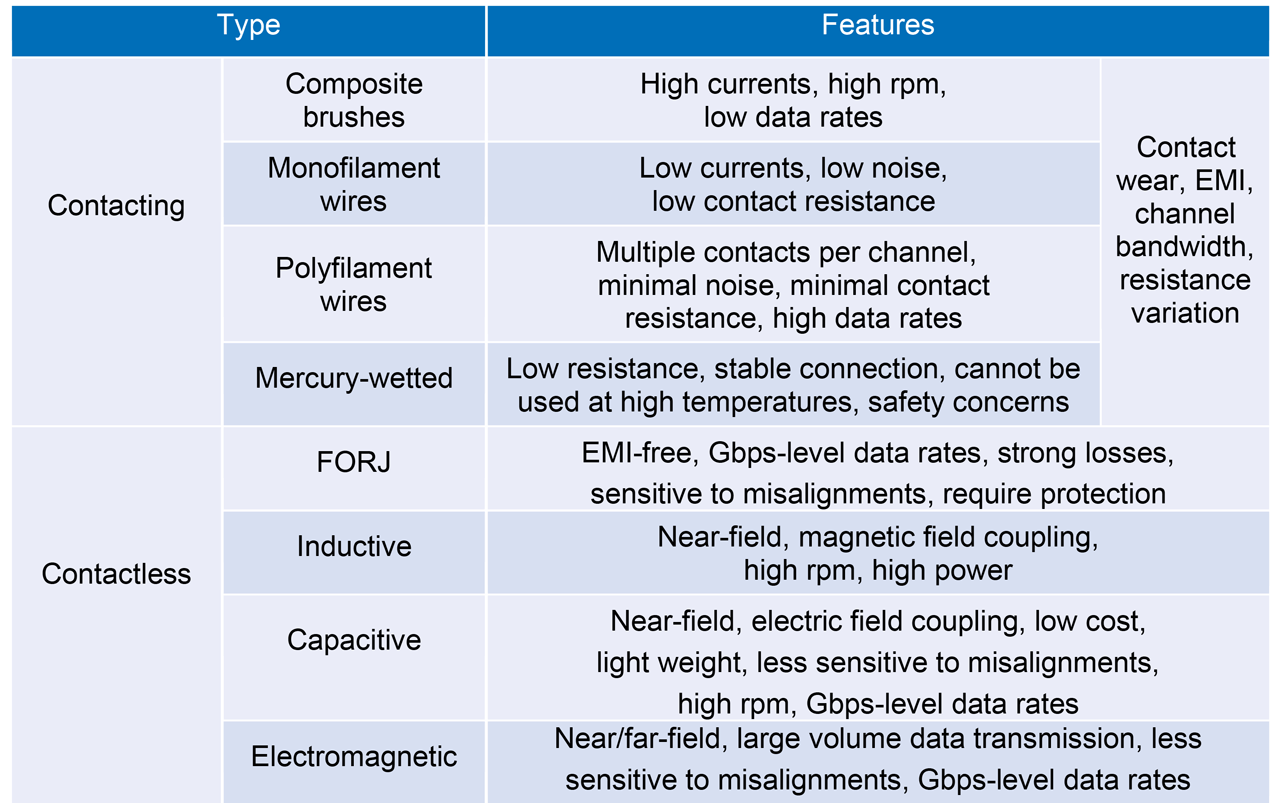
Table 1. Classification of Rotary Joints Based on Data Interface Coupling Technologies.
The broad spectrum of all discussed data interface technologies summarized in Table 1 offers numerous sets of features and capabilities that can meet typical requirements of industrial slip ring applications. However most of these conventional technologies are effective for data transmission only over short distances, which requires transceiver elements on a rotor and a stator to be in very close proximity to each other. Moreover, the fourth industrial revolution imposes strict requirements on configurability, reliability, and speed rates of data interfaces for slip ring applications that cannot always be met by conventional technologies existing today.
This article presents a novel solution based on a contactless technology that overcomes some critical limitations of other methods by relying on electromagnetic millimeter waves for transmission of data over longer distances in radiative near-field (Fresnel) and far-field regions. The proposed solution enables not only a compact and a cost-effective realization of an advanced microwave data interface for slip ring applications, but it can also be combined with conventional coupling elements of non-radiating rotary joints to achieve better performance at lower cost.
Millimeter Wave Data Interface Solution
60 GHz Frequency Band: The emergence of low cost microwave component fabrication technologies has recently made them a commercial reality for broad market applications beyond the military space. In particular, millimeter wave 60 GHz technologies are receiving increased attention from today’s broad market due to the unique advantages of this frequency band located in the upper region of the microwave spectrum. This global license-free and largely uncongested band offers a wide bandwidth of up to 9 GHz, which permits high data rates, provides short wavelengths that allow for a compact system design, and that has a high ratio of attenuation, which results in a low interference level. These benefits made 60 GHz technologies attractive for such applications as multigigabit WiGig networks (IEEE 802.11ad and the next-generation IEEE 802.11ay standards), wireless backhaul connectivity, and wireless transmission of high definition video (a proprietary WirelessHD/UltraGig standard).
In the industrial area, 60 GHz technologies are mostly used for millimeter wave radar sensors and lower data-rate telemetry links. However, rapid advancements in this domain make 60 GHz technologies very promising for the realization of high speed, ultralow latency data transmission in industrial subsystems.
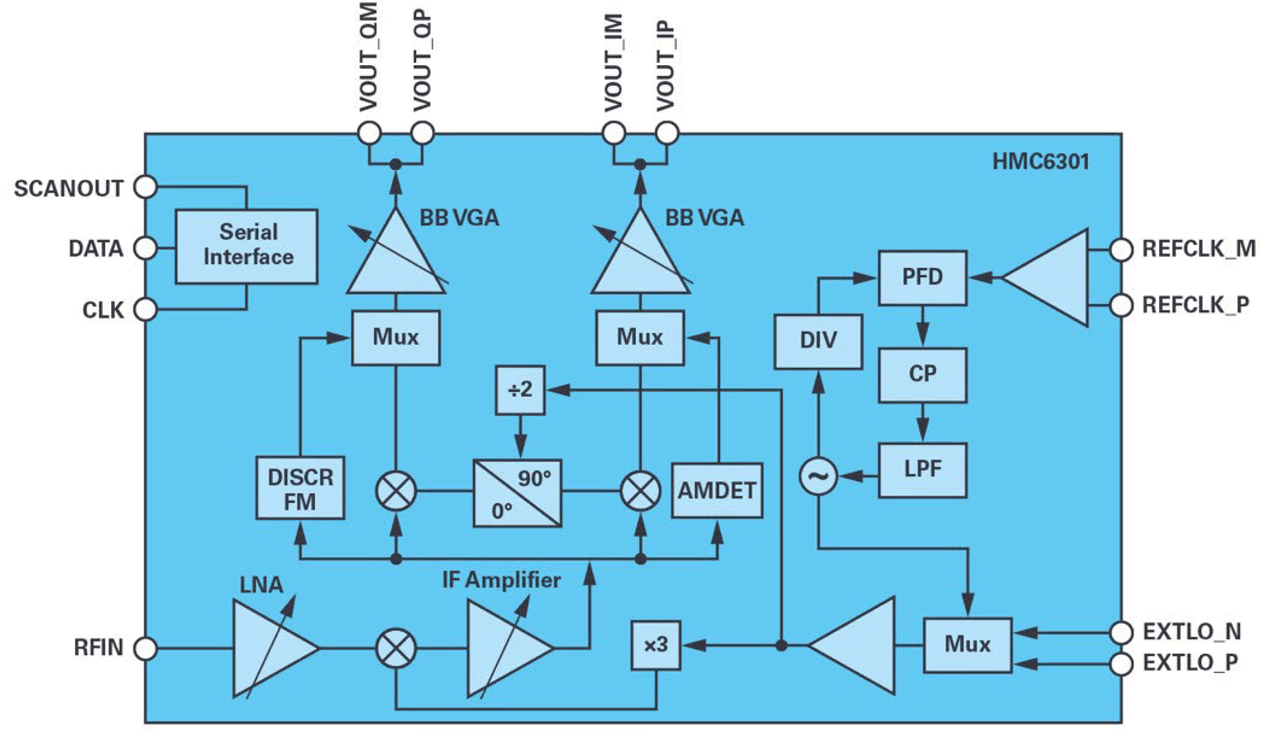
Figure 8. Functional block diagram of the receiver HMC6301.
Integrated Data Interface Architecture: This article proposes a novel millimeter wave data interface solution utilizing 60 GHz frequency band for industrial slip ring applications. The key functional element of this solution is the Analog Devices 60 GHz integrated chipset comprised of the HMC6300 transmitter the HMC6301 receiver, which are schematically depicted in Figure 7 and Figure 8, respectively. This complete silicon-germanium (SiGe) transceiver solution was originally optimized for the small cell backhaul market and it perfectly meets the data communication requirements of industrial slip ring applications. The chipset operates in the frequency range of 57 GHz to 64 GHz, and it can be tuned using either an integrated synthesizer in discrete frequency steps of 250 MHz, 500 MHz, or 540 MHz, or with an external LO signal to meet the specific modulation, coherency, and phase noise requirements of the target application.
The transceiver chipset supports a wide variety of modulation formats including on-off keying (OOK), FSK, MSK, and QAM with the maximum modulation bandwidth of 1.8 GHz. It offers a maximum output power of 15 dBm that can be monitored using an integrated detector. The chipset features flexible digital or analog IF/RF gain control, a low noise figure, and adjustable low-pass and high-pass baseband filters. One of the unique features making this solution ideal for ultralow latency industrial slip ring applications is an integrated AM detector in the receiver signal chain that can be utilized for demodulation of amplitude modulations such as OOK.
OOK is a very popular modulation method for control applications because it does not require the use of expensive and power-hungry high-speed data converters, thus enabling implementation of simple and low-cost communication solutions. Moreover, since OOK system architecture does not include complex modulation and demodulation stages, it offers low latency performance which is important for industrial real-time applications.
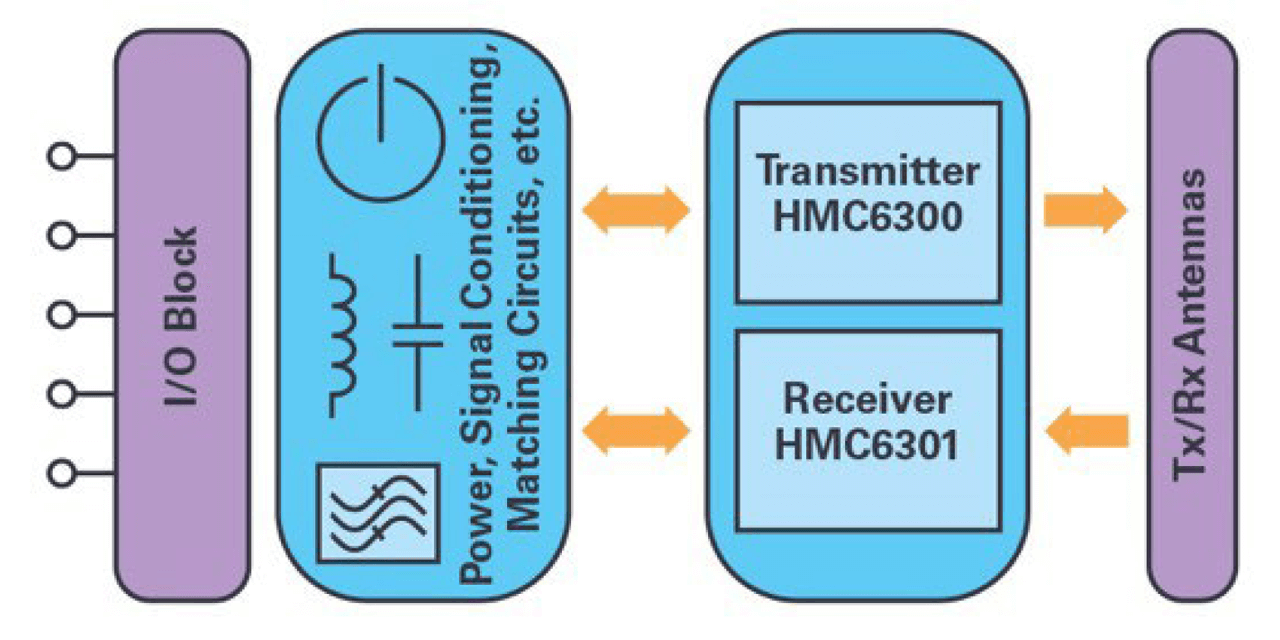
Figure 9. Block diagram of a 60 GHz full-duplex data interface.
The Analog Devices’ transmitter HMC6300 and receiver HMC6301 integrated solutions both come in a small 4 mm × 6 mm BGA type package and offer an exclusive combination of features and performance capabilities to meet the most demanding requirements of modern high speed slip ring applications. In addition to the core transceiver elements, the complete concept of the full-duplex slip ring data interface includes an antenna, power management, I/O blocks, and auxiliary signal conditioning components that can be chosen according to the requirements of a target use case.
A high level block diagram of the complete 60 GHz full-duplex data interface solution concept is shown in Figure 9. This solution enables high speed, ultralow latency data transmission at speeds above 1 Gbps with a negligibly small bit error rate. Using a proper antenna design and gain settings, one can achieve reliable communication over distances of several tens of centimeters, which opens up a wide range of slip ring solutions for specific industrial scenarios.
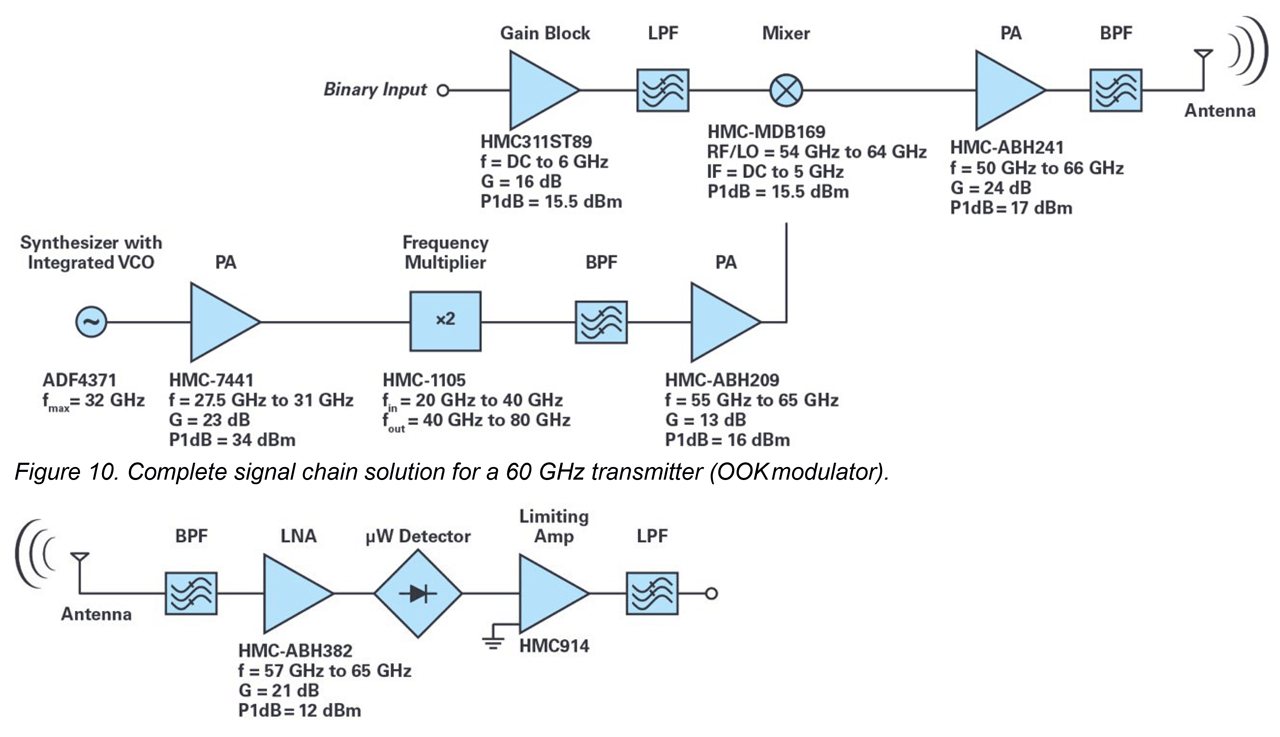
Figure 10. Complete signal chain solution for a 60 GHz transmitter (OOK modulator).
Discrete Data Interface Architecture
Performance capabilities of the proposed integrated solution are sufficient for most industrial slip ring applications, but the general trend toward customization of industrial components may require an implementation of even faster data interfaces supporting multigigabit speeds. In this case, it is possible to configure a customized solution to meet specific requirements using discrete components.
Figure 10 and Figure 11 show an example of a complete signal chain solution for a 60 GHz data interface supporting data rates above 5 Gbps. This OOK solution is realized with Analog Devices’ standard RF components and basic custom blocks represented by passives, matching circuits, stub filters, bias tee, attenuators, and others (not all of them are shown in the figures).

Figure 11. Complete signal chain solution for a 60 GHz receiver (OOK demodulator).
This discrete proposal is based on a single detection system architecture. However, depending on the performance requirements can also help realize a superheterodyne architecture by downconverting the RF signal before the video detection stage.
Conclusion
Industry 4.0 is driving change in many technologies and one such change is industrial communication. New application scenarios shaped by the fourth industrial revolution demand faster, more reliable, and more accurate ultralow latency data transmission between rotating parts of automation equipment operating in real time.
Analog Devices offers a broad range of high performance integrated and discrete RF and microwave components across the entire frequency spectrum that enable application specific designs for a contactless Gbps-level data transmission via rotary joints. This article proposed an integrated and a discrete data interface solution utilizing millimeter wave electromagnetic waves to transfer data between a rotor and a stator. The proposed solution offers not only high speed data transmission, ultralow latency, negligible bit error rate, strong interference attenuation, and maintenance free operation but it can also withstand higher misalignments and permits transmission over larger distances to enable a wide range of slip ring assemblies to meet the ever increasing needs of modern industrial applications.
Analog Devices offers Industry 4.0 partners deep industrial domain expertise and delivers next generation capabilities to develop faster and more cost-effectively advanced solutions for today’s factory infrastructure, with a future-ready pathway to what comes next.