TechnologyNovember 25, 2024
Industrial wireless impact on smart manufacturing
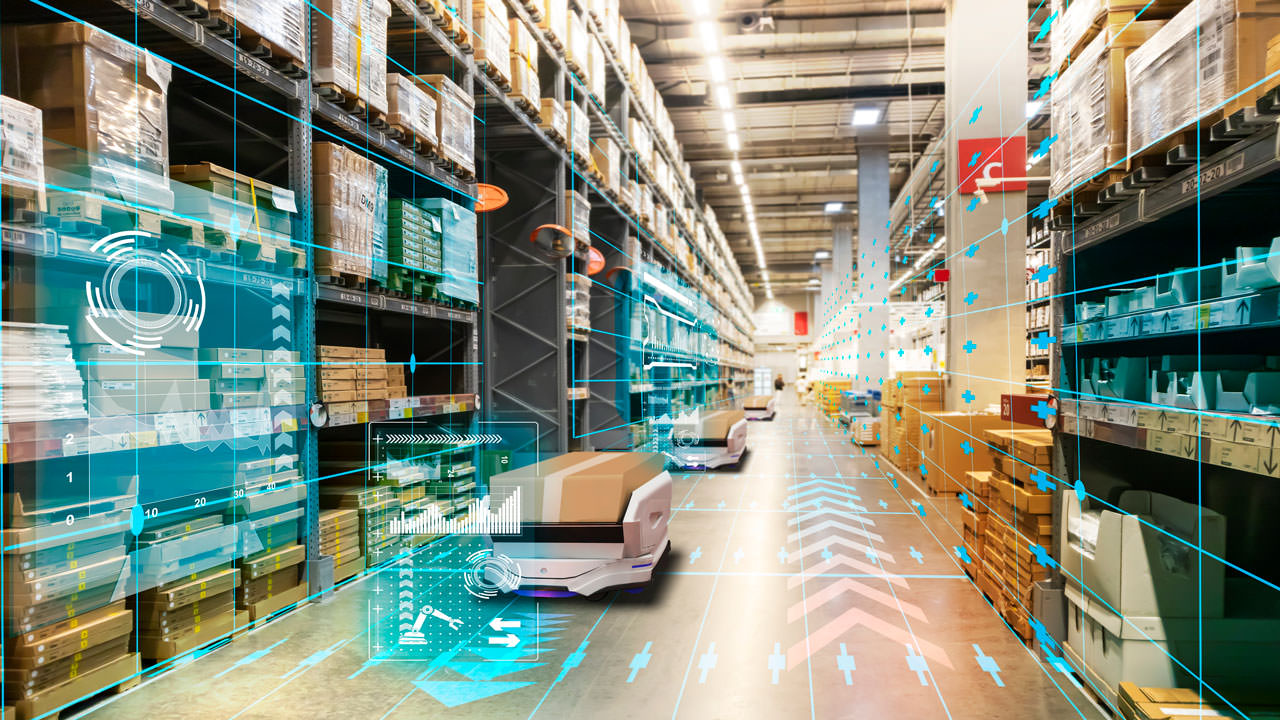
Industrial Wireless enables secure and reliable wireless connections for industrial applications. Depending on requirements, Wi-Fi 6E and Wi-Fi 7 are continuing to provide excellent solutions. Industrial 5G is also making an impact by enabling smarter, responsive, and more efficient factory operations.
INDUSTRIAL WIRELESS SOLUTIONS ARE PROVIDING TECHNOLOGY SOLUTIONS to support a growing range of Industry 4.0 applications from connected mobile objects to smart manufacturing tools. Industrial Wireless LANs based on Wi-Fi, Industrial 5G or both open up a broad spectrum of possibilities for industry but the question is what’s the right choice today and into the future.
For this special report on Industrial Wireless technology, IEB reached out to industry experts to get their perspective on the technologies that are impacting smart manufacturing operations.
Industry leaders have responded with their take on the trends for industrial wireless, and how a combination of Wi-Fi 6 and 7 along with the emergence of Industrial 5G offers effective solutions for manufacturing.
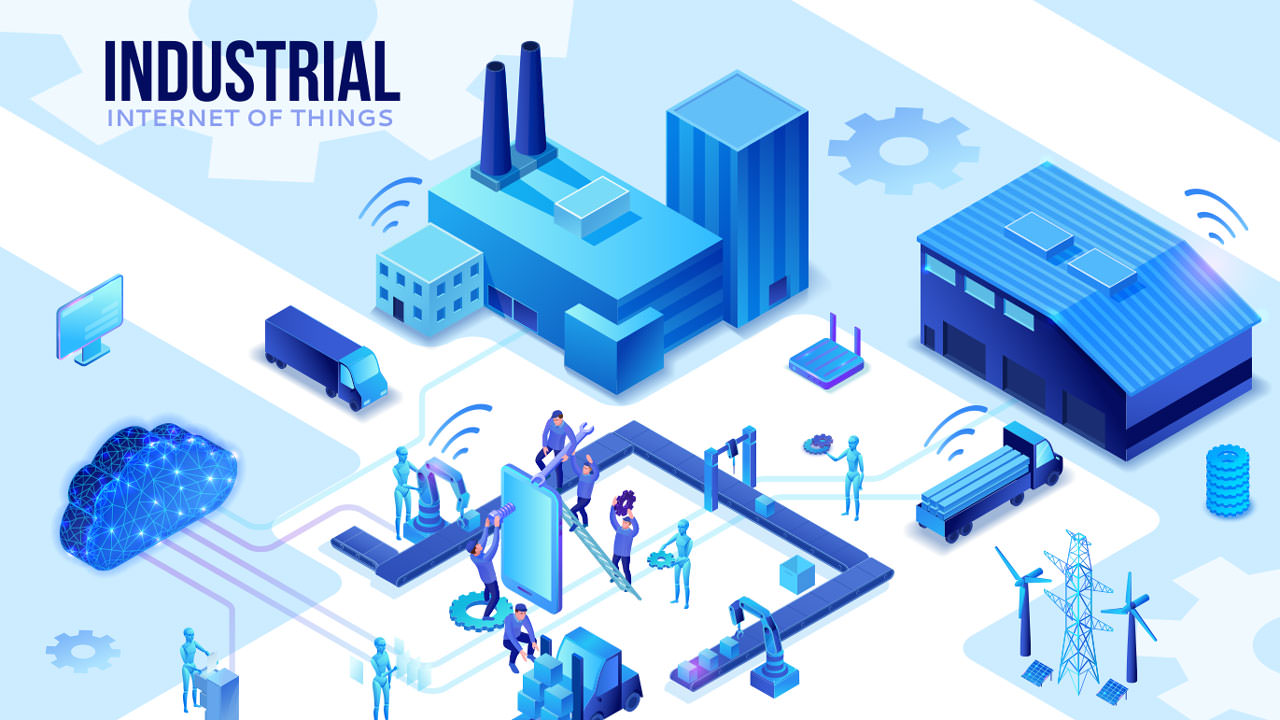
“The integration of Industrial 5G offers substantial technological advantages, enabling smarter, more responsive, and more efficient factory operations. However, it is crucial to integrate 5G into the overall network operations and controls, ensuring that these advantages do not come at the cost of siloed networking or compromised security,” — Andrea Orioli, Director Product Management, IIoT Wireless, Cisco Systems, Inc.
Industrial wireless delivers for manufacturing
Wi-Fi 6E and Wi-Fi 7 emerging. Industrial 5G enabling smarter, responsive, and more efficient factory operations.
“Wireless is fundamental to connect moving assets, and it offers greater flexibility to the environment, potentially reducing costs and installation times for connecting fixed assets,” said Andrea Orioli, Director Product Management, IIoT Wireless, Cisco Systems. “Wired connectivity is not available everywhere and can be prohibitively expensive to deploy and maintain depending on the location. “
Orioli said that, in the past years, we have seen Wi-Fi 6E and Wi-Fi 7 emerge. These Wi-Fi versions bring vast improvements in bandwidth, speed, and capacity compared to their predecessors, enabling organization to connect a wider range and higher number of devices. Wi-Fi 6E adoption continues to grow and we expect Wi-Fi 7 should follow in two to three years when a significant number of clients supports it.
Cisco Ultra-Reliable Wireless Backhaul (URWB) is an extension of Wi-Fi that was created to support applications that cannot withstand any loss of communication and need seamless handoffs. It has been successfully adopted to support AGVs in manufacturing, teleremote applications in ports and communications-based train control in rail.
“Private 5G adoption has been growing, but it is still considered complex and expensive to maintain. Additionally, regulations and spectrum availability vary depending on geographic locations,” Orioli added.
Industrial 5G
Orioli said that Industry 4.0 and the digitalization of the factory floor are increasing the demand for robust network capabilities. 5G is a powerful technology with a proven track record in our day-to-day lives. Its inherent capacity (speed), broad coverage, and fast handover capabilities are making a profound impact on smart factories, offering several technological advantages over traditional networks.
“The integration of Industrial 5G offers substantial technological advantages, enabling smarter, more responsive, and more efficient factory operations,” Orioli said. “However, it is crucial to integrate 5G into the overall network operations and controls, ensuring that these advantages do not come at the cost of siloed networking or compromised security.”
Together with Wi-Fi and URWB, Industrial 5G offers a robust solution for smart factory operations by accelerating digitalization, delivering production flexibility, and supporting robotics, autonomous, and automated vehicles like AGVs. We will see more and more factories deploying a combination of these technologies based on specific needs and use cases.
New industrial wireless solutions
Orioli said that as automation grows in different industries new mobile and automated or autonomous assets are being deployed. Many of these assets are very sensitive to latency and packet loss, any loss of communication can cause productivity losses and accidents. URWB is an extension of Wi-Fi, that enhances reliability beyond what is possible with Wi-Fi to address this need and is ideal to support highly critical applications.
URWB’s Multipath Operations (MPO) technology can deliver uninterrupted connectivity to fast-moving devices by sending high-priority packets via redundant paths on uncorrelated frequencies at the same time to multiple access points. It can duplicate protected traffic up to eight times and avoid common paths. This functionality, combined with cutting edge hardware capability, can further reduce latency and improve reliability, addressing both interference and hardware failures. MPO is an application layer protocol that is portable across Wi-Fi protocols and versions.
“In the recent years, we completely refreshed our industrial wireless hardware portfolio, which is fully based on Wi-Fi 6E,” Orioli said. “In our experience, organizations need different wireless technologies to support different applications. With that in mind, our access points can also run both in Wi-Fi 6E or URWB mode. The operational mode can be swapped in the field, facilitating the transition between the two technologies and optimizing the investment.”
Orioli stated that Cisco has also innovated on the form factors to support different deployment scenarios. For example, the Catalyst IW9165E comes in a compact DIN rail form factor. It was purpose-built for easy attachment to moving vehicles and small spaces. Its DIN rail mount position is flexible to simplify deployment in whichever position industries need.
Applications focus
“Wireless technology is a critical driver for enabling industrial automation. With higher reliability and speeds, wireless connectivity creates more possibilities to connect and automate various applications,” Orioli said. “One of the areas where we have seen enormous growth lately is the use of new automated and autonomous moving assets. These assets are becoming increasingly sophisticated, enabling greater process efficiency.”
The use of wireless for industrial control continues to grow. Analytics from data collected from sensors can be used to predict maintenance, and issues can be addressed earlier to avoid downtime in production lines. Real-time monitoring and control facilitate the automation of control systems, allowing for adjustments to be made quickly and efficiently. AGVs are used to transport heavy and bulky items and increase productivity delivering what is needed to each worker or location.
Challenges
“One of the challenges that automation engineers face, which wireless technology is helping to address, is the use of automation to replace labor in locations and situations that can be dangerous,” Orioli said. “For example, autonomous and automatic robots can lift heavy parts and equipment or transport them in areas prone to accidents, thereby increasing personnel safety.
Another challenge is improving operational uptime. Automation streamlines processes, and reliable wireless connectivity ensures that assets remain connected, preventing operational stoppages.”
She added that cybersecurity is another challenge that continues to grow. The latest wireless technologies have enhanced security features and capabilities to make connectivity more secure. An additional challenge is the need for flexibility and scalability.
“Market demands shift quickly, and wireless solutions give automation engineers the flexibility to reconfigure product lines or adapt their processes to new demand or requirements easier and faster than with wired connectivity,” Orioli said. “Wireless networks also offer easier scalability, allowing new devices to be added seamlessly without extensive infrastructure changes. In terms of outlook, we expect adoption of wireless technologies to increase as more organizations recognize the benefits of flexibility, scalability, and cost savings. Advances in wireless technologies supporting higher throughput and reliability enable the use of more sophisticated applications such as AI-driven predictive analytics and autonomous robotics.”
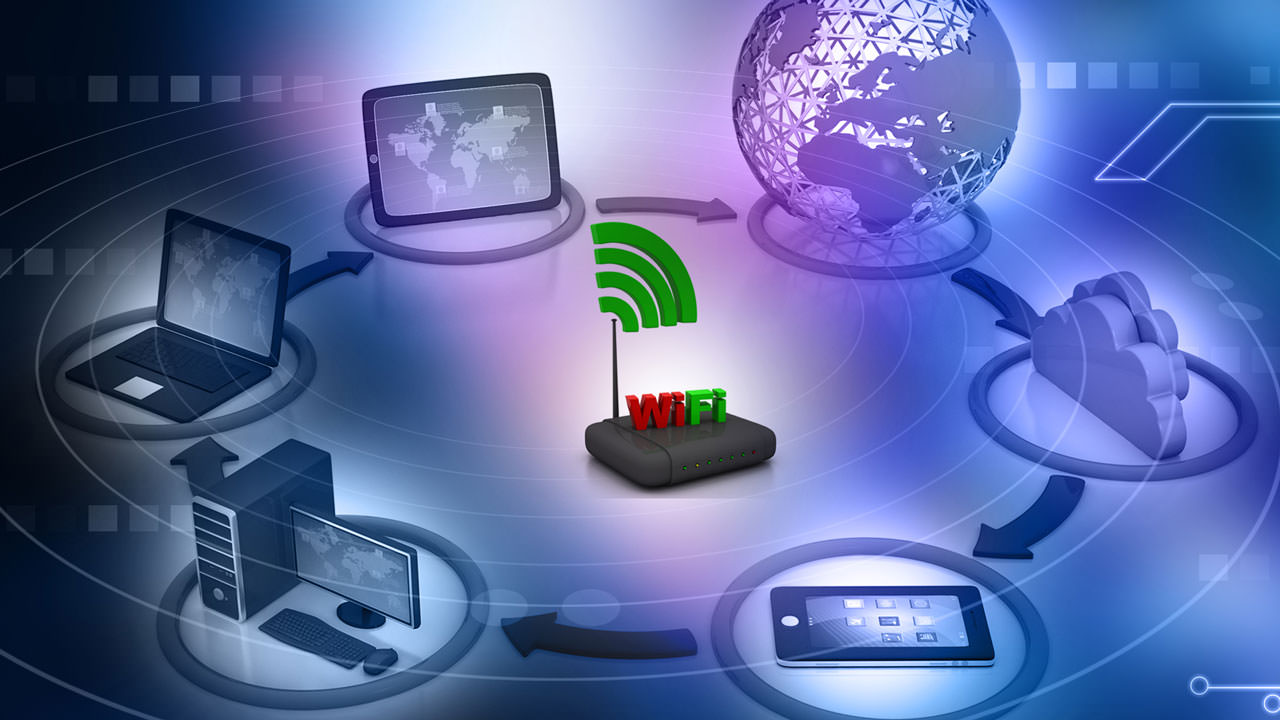
“Wi-Fi continues to improve performance and provide better options to users and developers. LPWAN solutions like LoRaWAN are good solutions where low data rates can be used and Wi-Fi or 5G cellular use too much power. 5G cellular adds several features related to increased number of devices, density, data bandwidth, lower latency, and improved security over existing cellular and Wi-Fi.” Matt Hoover, Global Product Manager, Wireless & IIoT Products at Rockwell Automation.
Wi-Fi leader in wireless applications
5G adoption continues to be slow due to complexity, initial and ongoing costs, and lack of devices with integrated 5G connectivity.
Matt Hoover, Global Product Manager, Wireless & IIoT Products at Rockwell Automation said that improvements in technology like Wi-Fi (6 / 6E and 7), Low Power Wireless (LPWAN) and cellular 5G are examples of how technology trends are enabling new industrial wireless solutions.
“Wi-Fi continues to improve performance and provide better options to users and developers. LPWAN solutions like LoRaWAN are good solutions where low data rates can be used and Wi-Fi or 5G cellular use too much power,” Hoover said. “5G cellular adds several features related to increased number of devices, density, data bandwidth, lower latency, and improved security over existing cellular and Wi-Fi.”
Adoption and acceptance rate
Hoover said that Wi-Fi continues to be the leader in wireless applications. Ease of use, cost, availability of devices and understanding the network contribute to ongoing success. This will continue with Wi-Fi 6/6E and 7. Customers will typically not remove their Wi-Fi networks to install a Private 5G network, they will run both. LWPAN solutions continue to grow in specific use cases where low power and low data rates are acceptable.
“5G adoption continues to be slow due to complexity, initial and ongoing costs, and lack of devices with integrated 5G connectivity. These challenges will be addressed over time and customers will add Private 5G to their network infrastructures when it makes sense,” Hoover said
Smart factory synergies
Hoover said that customers are considering Industrial 5G, but cost, complexity and lack of devices are keeping the adoption low. Customers continue to work on justifying the additional cost and complexity of 5G related to improved business outcomes. One of the key areas for 5G is data analytics. If the data can be analyzed appropriately the customer can see improvements in quality and production rates. If customers have the need to move equipment and they would typically run new cable in each case, Industrial 5G can be used to reduce wired cabling.
“Industrial 5G allows a customer to use a wireless connection where they typically would only consider wired in the past. 5G provides better handover, low latency, better device destiny, larger device count and better coverage. All these items allow plant personnel to be more creative with design and how they implement the concept of a smart factory,” Hoover said.
He added that, in addition to innovative design for manufacturing, personnel can also improve efficiency, quality and productivity. The internal system must be updated, and data must be used to realize these benefits, but 5G does enable the opportunity.
New industrial wireless offerings
Hoover said that Wi-Fi is not new, but customers continue to push the limit for what can be done with Wi-Fi. As Wi-Fi improves with 6 / 6E, and 7 customers will continue to use Wi-Fi in new applications. Module vendors continue to integrate processing and RF into modules and add certifications to different form factors. This allows developers to add application processing to the RF module and reduce the complexity of the end device.
Device and gateway vendors continue to create different form factor devices to make it easier to add Industrial Wireless to a variety of products. This allows a customer to use the same gateway product and add different wireless technologies based on the application.
Device manufacturers continue to enhance their software offerings with complete cloud management solutions as well as APIs to integrate their products into a customer’s management solution. All these capabilities continue the trend of making it easier for end customers to add industrial wireless to their plants.
Industrial wireless solutions
“The newest solutions are high speed edge-to-cloud connectivity for real-time data transmission, and reliable coverage for cloud-hosted artificial intelligence and machine learning solutions,” Hoover said. “Getting data from the plant floor to IT to improve business continues to be a good use case for industrial wireless.”
He added that connected workers using industrial wireless (5G-compatible) handsets and tablets can access mobile applications. Example applications include analytics, digital twins, machine repair and mobile asset applications (MES).
Mobile asset applications—particularly automated guided vehicles (AGVs) and autonomous mobile robots (AMRs) require both mobility and fast, reliable handover. Industrial wireless allows AMRs and AGVs to better coordinate and map the plant floor.
Untethering stationery, low latency industry assets increases operational agility and reduces time needed for retooling on the shop floor.
As far as the status of the use of wireless for industrial control, Hoover said that it generally depends on the control application. Some AMR and AGV applications use Wi-Fi while others use Private 5G. Most control applications are still wired. Rockwell Automation is currently testing Industrial 5G applications to characterize control applications.
Outlook for industrial wireless
Industrial wireless helps engineers solve the following:
- Quick change over and flexibility in equipment location related to production requirements
- Reduce the cost of cable and cost to install and run backhaul cable connections when equipment needs to move
- How to better manage AMRs and AGVs
- How to quickly connect new equipment from connected worker to mobile assets
- How to provide machine and production data to IT for applications like AI and data analytics
Hoover concluded that the outlook is very good, but adoption will take time, and device manufacturers need lower cost solutions. Rockwell Automation continues to test and characterize Private 5G in our Connected Enterprise Lab.
“We work with customers to help them understand how they can leverage wireless technologies, especially Private 5G. We are testing Edge to Cloud, Connected Worker, Mobile Asset and Untethered Stationary Asset. We are working on validating latency and jitter for industrial control applications,” Hoover said.
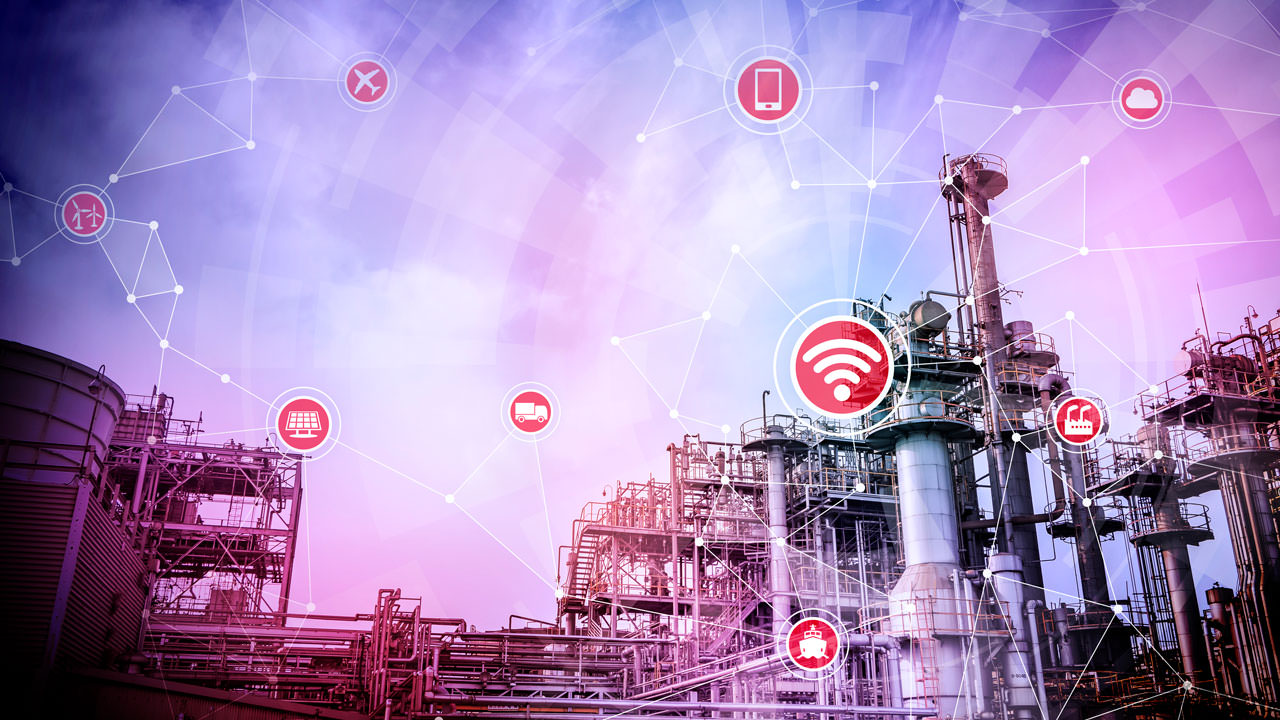
“There is a growing acceptance and adoption of these wireless solutions across various industries, enabling more efficient and flexible operations. With growth of an ecosystem of end devices supporting these new technologies the adoption will be accelerated,” Daniel Mai, Director Industrial Wireless Connectivity at Siemens AG.
Manufacturing impact from 5G, TSN and WiFi solutions
Technologies offer higher data rates, lower latency, and improved reliability which are essential for modern industrial applications.
According to Daniel Mai, Director Industrial Wireless Connectivity at Siemens AG, new technology is driving the adoption and acceptance of new wireless solutions.
“Key technological trends driving new industrial wireless solutions include the introduction of Industrial 5G, advancements in Time-Sensitive Networking (TSN) over wireless media, and the adoption of Wi-Fi 6 and Wi-Fi 6E,” Mai told the Industrial Ethernet Book recently. “These technologies offer higher data rates, lower latency, and improved reliability, which are essential for modern industrial applications that need more and more connectivity. As a result, there is a growing acceptance and adoption of these wireless solutions across various industries, enabling more efficient and flexible operations. With growth of an ecosystem of end devices supporting these new technologies the adoption will be accelerated.”
Impact of Industrial 5G
Mai said that industrial 5G is significantly impacting smart factory operations by providing ultra-low latency and high reliability in wireless communications. This enables reliable real-time control of machines and processes, which was sometimes challenging with other wireless technologies.
“The enhanced connectivity supports the deployment of autonomous vehicles and collaborative robots, improving the flexibility and efficiency of production lines. Industrial 5G also facilitates seamless communication between a vast number of devices, contributing to more integrated and intelligent manufacturing environments. Additionally, the possibility to set up tailored private 5G networks utilizing private spectrum will enable secure and interference-free wireless connectivity on industrial campuses,” Mai said.
Unique technology solutions
Mai added that new products offer improved performance, higher data throughput, and support for deterministic wireless communication, enabling the wireless control of mission-critical applications. They meet the need for increasing connectivity and and higher data traffic in smart factories to collect and transfer data and thus enable data driven decisions and e.g. AI applications. Compared to previous solutions, they provide advanced cybersecurity measures and seamless integration with existing industrial protocols, enhancing both security and ease of deployment and creating a reliable OT-backbone.
“The latest industrial wireless solutions are targeting applications that require high bandwidth, low latency, and reliable connectivity. This includes mobile robotics, remote monitoring and maintenance, augmented reality for training and complex assembly tasks, and process automation,” Mai said. He added that the use of wireless for industrial control is becoming more prevalent, as modern wireless technologies have addressed many of the reliability and latency concerns that previously hindered their adoption. Industries are increasingly confident in deploying wireless solutions for a broader range of control applications.
“A big game changer will be the introduction of AI to the industrial space,” Mai said. “AI applications need data. Implementing a reliable wireless communication infrastructure will facilitate the easy deployment of additional sensors and edge devices in existing factories to feed AI and enable data driven decision making.”
Facing challenges
Mai said that automation engineers often face challenges such as the inflexibility of wired networks and high installation costs. Advances in industrial wireless technology are helping to overcome these issues by providing increased mobility, flexibility, and real-time communication capabilities.
This allows for easier reconfiguration of production layouts and more scalable operations. Looking to the future, the outlook for industrial wireless is promising, with expected continued innovations in areas like Industrial 5G, Wi-Fi technologies, and edge computing. These advancements are likely to lead to fully connected and highly adaptable industrial environments, driving efficiency and productivity to new levels.