TechnologySeptember 10, 2018
Wireless technologies make manufacturing objects smart
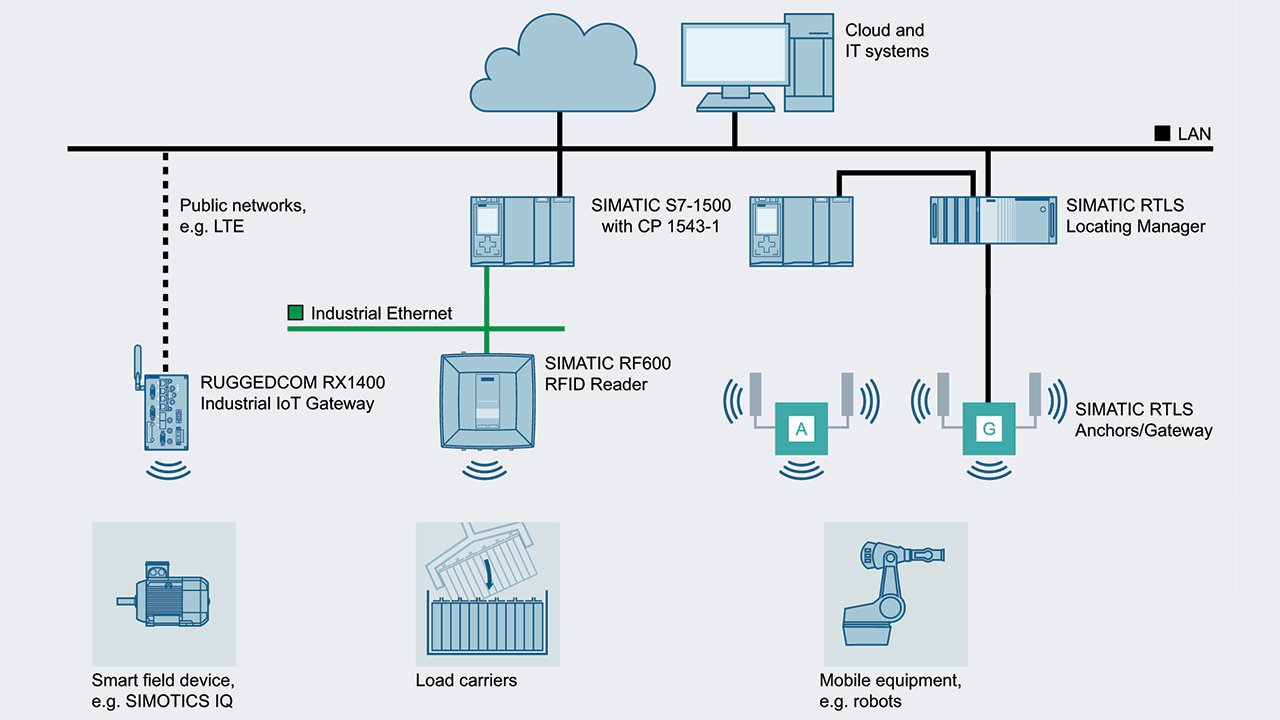
Analysis of machine utilization, highly flexible production control, and predictive maintenance are possible using smart manufacturing objects and wireless technologies. WLAN, RFID and RTLS are all highly suitable for industrial environments by combining rugged component design with reliable communication paths.
The Industrial Internet of Things (IIoT), promises to deliver significant added value through the evaluation of data from the field level in cloud systems. But what can you do if relevant manufacturing objects like containers, aggregates or products do no offer their own communication capabilities? This is where the flexibility of wireless technologies can come into play.
For machines and plants that have their own sensor technology, the IIoT connection can be realized relatively simply. There are only a few field devices that can be connected directly to the IT systems including up to the cloud. Rather, there is a wide diversity of connection methods, electrical parameters and protocols that have come up throughout the years as an optimization of the respective application from current interfaces (4 mA to 20 mA) up to complex fieldbuses such as PROFIBUS.
Nevertheless, their evaluation is possible with data analytics by, for example, “tapping into” the next higher aggregation level, usually a programmable logic controller (PLC). Modern systems such as Simatic S7-1500 offer the required Ethernet connection for further processing on the controller (CPU) itself, or they can be supplemented by a corresponding communication module, which provides advantages from a security point of view. The CP1543-1, for example, not only expands S7-1500 systems with another interface but also with a firewall.
The sensor and field data are required to generate a digital image of production, and create an ability to analyze and then effectively operate downstream processes. For example, relevant information can be provided automatically for maintenance planning through operating hours counters, temperature sensors or measuring equipment for the current consumption. The wide range of data also allows for Big Data analyses. These are algorithms that search through large amounts of data for new patterns, and consequently uncover new causal relations.
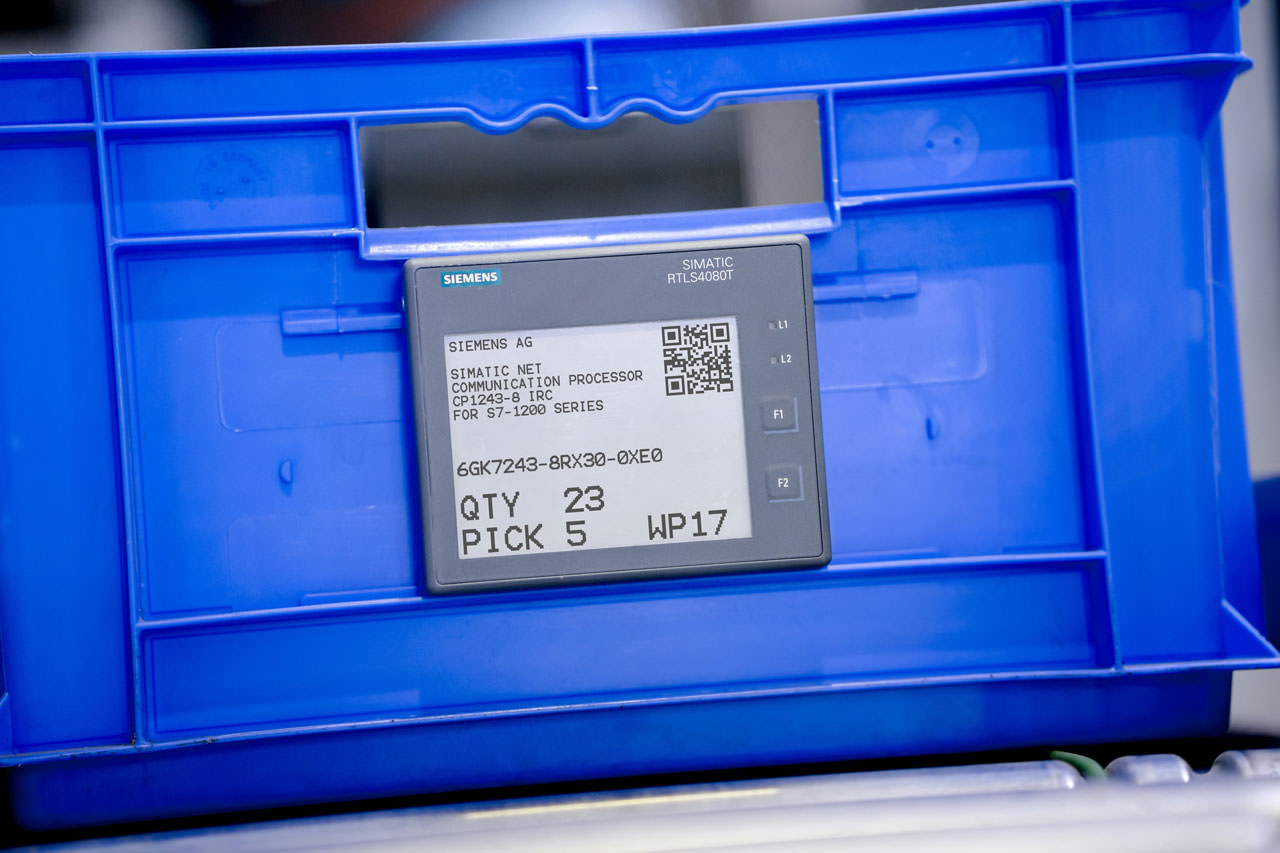
Using RTLS data, it is possible to display information derived from the actual position and status.
Manufacturing objects
Big Data can also help with manufacturing objects such as transport containers, tools or the products in process optimization. However, these objects lack an essential property for IIoT. They do not have a communication interface, which is essential for automatic data acquisition and evaluation. However, various wireless technologies that close the gap between Ethernet communication networks and these production objects offer a solution. And there is also a need to differentiate between Wireless LAN (WLAN), Radio-Frequency Identification (RFID) and Real-Time Locating Systems (RTLS).
WLAN networks are already widespread and are suitable for numerous tasks that, depending on the requirements placed on the bandwidth, can be implemented simultaneously in the same network. Sensors with WLAN capability are required as counterparts for the wireless networks. Depending on the plant situation, different advantages can be exploited.
ensors with WLAN capability eliminate cabling costs, which can be substantial, especially if no communication infrastructure exists at specific points in the plants (such as outdoors) yet. A second advantage is the data transfer from mobile objects to the cloud for which cabling cannot actually be realized.
An example of how WLAN can be used for “the last meters” in the IIoT is Simotics IQ for the corresponding drives from Siemens. Simotics IQ is an easy-to-handle sensor box that collects various parameters of a drive without interfering with it and then transmits these data to the cloud over WLAN. A Ruggedcom RX1400 can be used as an access point, for example. It can also transfer the collected records to MindSphere over wireless networks. This even makes opening of the existing company network superfluous. RFID should certainly be listed as a second technology essential for the IIoT. RFID systems have already been used in production control and logistics applications for many years.
In these systems the manufactured objects are equipped with small data carriers (transponders) that the RFID reader can read and write to wirelessly. RFID transponders have become so inexpensive that not only circulating containers are equipped with them. Depending on the process, small radio chips are also being introduced directly into the actual product today, like an electronic rating plate, and can be used by several participants in the industrial supply chain for automatic identification. This makes RFID systems particularly suitable for the acquisition of data across departments and even between companies for cloud-based evaluation.
Real-Time Locating Systems
Finally, Real-Time Locating Systems (RTLS) have also started conquering production halls. In this case all relevant objects are also equipped with a transponder, but it has to be equipped with an energy source – unlike with RFID. Through a network of so-called anchors (comparable to the access points in WLAN) transponders can be located three-dimensionally, even at one-second intervals, if necessary.
This allows for automation of a wide variety of processes that require the current location of an object. Manual search processes or manual scanning of logistics and production orders at the respective transfer points become superfluous. But the possibilities offered by IIoT go even further.
By comparing the position data with the digital image of the products, for example, the machining steps can be documented and controlled by tools. The resolution in the centimeter range makes it possible to adjust the torque of power screwdrivers automatically, for example, without the need for manual, and thus potentially faulty, operating steps.
Commercial analyses are also feasible: If the frequency and duration of usage for transport containers is acquired automatically, for example, the inventory can be reduced to optimum levels without compromising practical processes.
A third field of application results from the data channel is being offered, for example, by Simatic RTLS from Siemens. In this case, location-specific information, combined with data from systems such as enterprise resource planning or production planning, can be sent back to the transponder. A paper-ink display using particularly low power consumption provides employees with information that is available directly on the “smart transport container”.
All of these technologies – WLAN, RFID and RTLS – are highly suitable for industrial environments. This is accomplished by the rugged design of the components, and the reliability of the communication paths. Specific supplements to the standards ensure that the special demands arising from the industrial applications are covered. For example, the iPRP function (Industrial Parallel Redundancy Protocol) of the Scalance W family ensures interruption-free redundancy in communication.
RFID transponders are also available in heat-resistant versions which means they can stay on the product in painting lines. And RTLS transponders can also collect additional sensor data so that digital systems are supplied with more than just location data.
Wireless systems therefore supplement wired communication systems seamlessly and ensure an integrated Internet of Things, even at the end of the (Ethernet) line.