TechnologyJanuary 20, 2023
2023 Special Report: Industrial Ethernet Cables & Connector Solutions

Single Pair Ethernet is leading the way by enabling new possibilities for smart factory digitalization. But industry experts point to CAT7 cable innovations, along with application-specific and hybrid solutions, as catalysts for achieving IT/OT convergence and long lasting impact on factory automation applications.
Industrial cabling and connector technology solutions have moved center stage with potential game-changers for smart factory applications.
In this special report, the Industrial Ethernet Book has reached out to industry experts to gain their insights into Single Pair Ethernet, along with innovations in cabling and connectors, that are ushering in new levels of factory and IIoT connectivity.
Potent connectivity solutions
CAT7, SPE, Application-Specific Solutions, IP67 and Hybrid Installations.
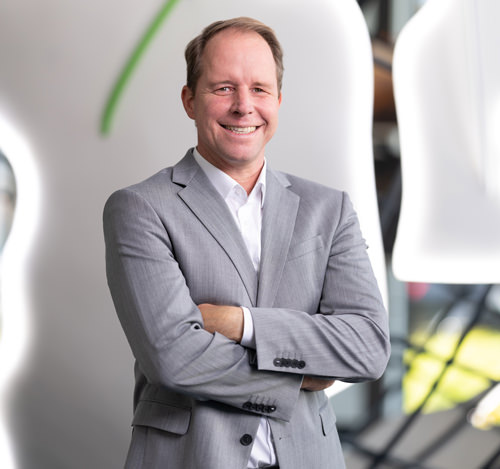
Ralf Moebus, LAPP
According to Ralf Moebus, Head of Product Management Industrial Communication at Lapp, the key technical trends influencing the development of the latest generation of Industrial Ethernet cables and connectors are found in five areas.
- Cat. 7 for 10 Gbit/s date rates: Higher data rates are becoming more and more the standard in the factory.
- SPE: Single Pair Ethernet enables Ethernet communication via one single twisted copper pair instead of 2 or 4 pairs.
- Application-specific Ethernet cabling: For use in applications such as Robotics, including the new Type R standard for PROFINET which defines application specific test for use of ETHERNET cables.
- IP67 protected Ethernet connectors: M12D and M12 X for installation of Ethernet devices in the field without cabinet.
- Hybrid Installations: with data and power in the same cable.
Key technology benefits
Moebus explained that these technology solutions offer a series of key technical benefits that are providing solutions for specific applications.
Cat.7 for industrial Ethernet cabling enables higher data rates and higher safety margin for future enhancements of the factory.
Single Pair Ethernet reduces installation effort, saves space and has cost saving potential for the components. Therefore, it makes Ethernet installations for the lowest field levels more cost effective and enables an economical integration of sensors and actuators in the network infrastructure. So it is an important technology to make data from the field accessible for the smart factory.
Application-specific Ethernet cabling makes Ethernet installations in industrial machinery more endurance since the specific application requirements like mechanical stress or special environmental conditions are considered in the design of the cables.
IP67 protected Ethernet connectors are used for the connection of IP 67 rated Ethernet devices in the field. No cabinet is needed; this reduces cost and saves precious space on the shop floor.
Hybrid installations with data and power in the same cable saves space since only one cable is needed instead of two. The connection and replacement of end devices is quicker since only one connector needs to be connected.
Targeted applications
When asked what specific application areas and networking architectures are these solutions targeting, Moebus noted the following impact on potential applications:
- Cat. 7 is mainly used for the Backbone of industrial Ethernet Networks, and is the backbone used for Machine to ERP/MES Systems, Machine to Cloud and Machine to Machine communication.
- Single Pair Ethernet addresses mainly the lowest field level of the factory network. SPE bridges the gap between the sensors and actuators and the automation network or the cloud. By direct SPE integration in these devices they can provide much more information which can be used in other systems like Edge Computers and enable new data driven use cases like predictive maintenance or detailed process surveillance.
- The new PROFINET Type R Standard is a good example of application-specific Ethernet cabling solutions. The Type R Standard was developed for use in Robotics and ensures that cables work reliably in industrial robotic applications. It describes mechanical test procedures for cables that are used for the PROFINET communication from the robot controller to the end of arm tool on the robot.
- With IP 67 rated Ethernet connectors, the installation of Ethernet devices in the field is possible. Especially directly in the machines, where space is limited, the reduction of boxes and cabinets creates potential to build machines more compact in size. For modern decentralized automation architectures cabinet, less installation is also very supportive.
- Hybrid Ethernet installations are bringing data communication and also power to the end devices. It is a good solution for applications that need more power than Power over Ethernet can provide. Due to the availability of different cross sections in the cables, it is a scalable solution which can be adopted to the power demand of the individual application. Therefore, hybrid installation is the ideal solution for actuators like smart servo drives.
Addressing engineering challenges
These newest solutions are designed to address a series of engineering challenges.
“If powerful factory backbones with up to 10 Gbit/s need to be build up, and the network shall be future proof, than Cat. 7 Industrial Ethernet cables are the right choice,” Moebus stated. “If Data from the sensor/actuator Level shall be made available and not very high Data rates are needed than Single Pair Ethernet is a very economical solution.”
Moebus said that the movement of robots causes a lot of torsional and bending stresses to cables. In the past the there was no standard that describes these specific mechanical requirements of Cables that are used on robots. With Ethernet cables the fulfill the Type R standard, the Engineer can trust that the PROFINET communication will work reliably.
He added that, for installation of IP67 rated Industrial Ethernet devices outside the cabinet, M12D Coded for up to 100Mbit/s connectors and M12X Coded connectors for up to 10 Gbit/s are a standardized solution. If actuators like servo drives need to be connected to Ethernet than hybrid installation can save space and installation effort.
Single Pair Ethernet
Enabling IIoT digital operational technology networks.
“Single Pair Ethernet (SPE) is a crucial enabler of adding the things in IIoT to digital Operational Technology (OT) networks,” Dr. Al Beydoun, President and Executive Director of the ODVA, told the Industrial Ethernet Book recently. “These things include contactors, push buttons and motor starters located in cabinets, along with temperature, level, and flow sensors in process plants, and even RFID sensors and gate cylinders in logistics facilities.”
“Many of these devices are currently analog with little to no diagnostic or parametrization capabilities. Some of these devices are already on digital fieldbus networks today; however their status and commissioning abilities are oftentimes underutilized leading to a substantial amount of stranded data and untapped operational improvement potential,” he said.
Enabling IT/OT Convergence
Beydoun’s basic point is that SPE will help enable IT/OT convergence by allowing OT devices to leverage the same underlying Ethernet technologies making it easier to ensure data makes it way up from the field level through gateways and onto SCADA, MES, ERP, and cloud systems.
There are many versions of SPE for different applications with multiple cable lengths and types, speeds, and other factors such as intrinsic safety. SPE encompasses 10BASE-T1L General Purpose SPE applications, 10BASE-T1S in-cabinet applications, and 10BASE-T1L Ethernet-APL applications. Furthermore, there are multiple IEEE SPE standards in addition to those mentioned here.
“The adoption of SPE by both device manufacturers and end users alike is a critical step in unlocking the full potential of IIoT to transform business through more efficient operations. Ethernet-APL is a specialized version of SPE for process automation that includes hazardous area protection, power to field instrumentation, and support for long cable runs of up to 1,000 meters,” Beydoun added.
According to ARC’s Valentijn de Leeuw, “Felix Hanisch, president of the NAMUR board, mentioned that an Ethernet-APL information highway to the OT systems is critical, and maybe the industry’s last chance to enable ‘top-to-bottom’ digital transformation.”
Technology & IIoT benefits
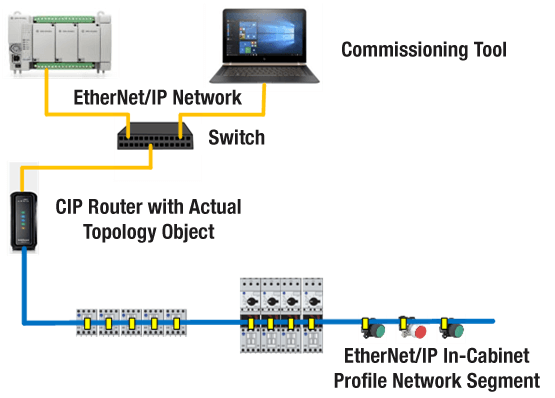
EtherNetIP In Cabinet Resource Constrained Device Topology 1
Beydoun said that one of the most clear and important benefits of SPE is the lower cost of cabling relative to standard Ethernet since only a single twisted pair is required. While this may seem small, the difference can add up quickly with factories and plants that have cable runs of hundreds of meters and thousands of communication nodes.
SPE can also reduce the labor and time needed for panel installations with easier to use connectors and fewer wires required. ODVA’s in-cabinet resource-constrained device solution is an example as it enables contactors and push buttons to be connected to EtherNet/IP via a SPE multidrop flat cable.
The long cables lengths of up to 1,000 meters, potential reuse of type A fieldbus cable (IEC 61158-2), and up to 10 Mbit/s communication speeds of Ethernet-APL can enable the benefits of Ethernet to be realized at the field level in process plants. One of these advantages is that process instrumentation can easily communicate multiple variables such as temperature, level, and flow from one instrument via the increased bandwidth of Ethernet-APL.

EtherNet/IP In Cabinet Resource Constrained Device Topology 2
An additional benefit is that SPE minimizes hardware requirements by allowing for usage of smaller physical interfaces, which makes it cost effective to connect to simple devices.
Additional device connectivity opens up possibilities for diagnostics along with development of prognostics. Incentives to utilizing SPE to add devices to Ethernet networks include remote commissioning, digital troubleshooting, and failure prediction via edge and/or cloud enabled analytics.
The cost savings from being able to quickly and easily add a new device to the network and to identify a malfunctioning device without having to physically test for failures adds up quickly between labor savings and downtime reduction. Industrial Ethernet networks, such as EtherNet/IP over SPE can help unlock previously untapped data into insights that can transform operations to increase OEE/production output, flexibility and quality while also driving down cost.
Impact on Smart Manufacturing
Given that the IIoT is already more than ten years in the making, Beydoun’s assessment of the progress and overall impact of the IIoT on industrial automation and smart manufacturing is slow but steady.
“IIoT development progress has been taking place at a steady, yet measured pace over the past decade. The initial steps were organizations working to create a common internal understanding of what IIoT and Industry 4.0 meant and what type of impact they could have on industry,” he said. “This was followed by low cost and simple test projects to see what kind of data could be extracted from existing applications and what benefits could be derived from this information by highly trained data scientists.
Further progress was made with IIoT gateways that can consolidate existing operational technology data from the factory floor and then send it to the edge or cloud for analytics and insight development such as operational improvement recommendations.”
He said that recent and newer gateway software solutions have been introduced that allow for easier scaling of IIoT gateways across entire facilities. Additionally, easy to use data science software is being made available by companies such as Microsoft to alleviate both the shortage and high cost of data scientists.
The recent trend toward developing solutions that can scale at a reasonable cost is a very encouraging trend that will hopefully transform IIoT from being limited to testing among only a portion of an organization to a critical strategic focus that everyone will play a role in.
Key next steps
“Executives at device manufacturers and end users alike have an opportunity to accelerate the development of IIoT applications by making digital transformation a core part of their operational business strategy.” Beydoun said.
“Significant focus, funding, training, and cultural adjustments are necessary to overcome the challenges of developing and adopting new technologies that many current workers aren’t familiar with. This approach needs to be undertaken with an understanding that this change will be a long-term shift that will have immense challenges early on and increasing benefits over time.”
He concluded that short term results may be limited by the time it will take for full ecosystems to develop, to overcome the learning curve presented by new technology, and to work though the training and inherent cultural resistance to change. Ultimately, a level of risk that organizations don’t normally take on will need to be taken on to move from limited IIoT pilot projects to full scale implementations.
“However, the alternative of inaction is to become at a significant disadvantage relative to competitors who do invest in enabling diagnostics, prognostics, and data insights across the entire business, which can help to make business decisions that increase quality, output, and margins over the long run,” he said.
Ethernet Key to Digitalization
Connector and cabling technology will play a major role in digitalization.
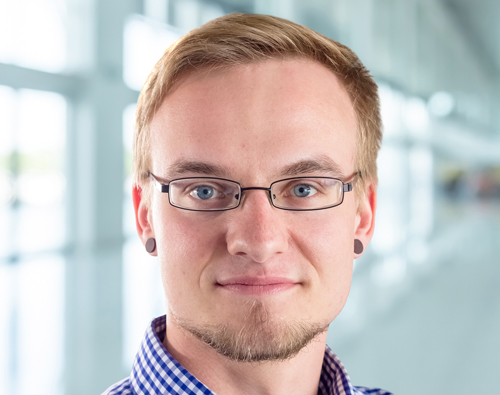
Jonas Diekmann, HARTING
“Ethernet is conquering more and more shares of all industrially used communication nodes every year. At the same time, the multitude of different bus protocols is on the retreat.” Jonas Diekmann of HARTING told IEB. “All in all, the growing demand for bandwidth down to the lowest field applications can be clearly seen. Connectors and cables play a major role in the development of digitalization. They are the road for all data packets. Without a suitable road, no data traffic.”
Diekmann added that, at the same time, the trend of miniaturization can be seen. Devices are shrinking, the infrastructure must also offer smaller solutions than before.
“The last point that must not be ignored, especially in industrial applications: reliability. Interfaces must simply work. This is taken for granted, but unfortunately it is not always the case. And troubleshooting takes a long time and costs money. Transmission rate – miniaturization – reliability: key factors for an IoT-suitable infrastructure,” he added.
Industrial RJ45
The well-known RJ45 is the most widely used data connector worldwide both in office applications and in industrial markets. However, the original version of the connection is based on a telecommunications connector that was not very well suited for harsh environments. With its RJ Industrial MultiFeature, HARTING has created a robust and industrially suitable version of the RJ45, which is not only robust and optimally shielded, but can also be easily assembled in the field without special tools.
“User-friendliness is the top priority for the HARTING RJ45, as it is for the preLink cabling system. This separates the formerly fixed connection of cable and connector into a universal, multiple reconnectable connection of cable and connector. A termination block is contacted on the cable, which can then be inserted into all preLink connectors. Whether RJ45 plug, RJ45 socket, M12 plug, soldered PCB socket or coupler,” Diekmann stated.
HARTING offers the globally compatible interface in an absolutely reliable version that can transmit high data rates of up to 10Gbit/s, is easy to use and creates absolutely reliable connections.
For smaller applications, the company offers its ix Industrial connector standardized according to IEC 61076-3-124. Diekmann said that it is up to 70% smaller in the device than RJ45 sockets and contributes significantly to the successful miniaturization of devices. It also transmits up to 10Gbit/s with the best possible protection and establishes a secure connection in a space-saving manner.
“In the future, Single Pair Ethernet will fill the last white spots on the Ethernet map. Ethernet via only one pair of copper wires with up to 10Gbit/s transmission speed and with a range of up to 1000 meters. This makes continuous Ethernet communication from the cloud to every sensor a reality,” he added.
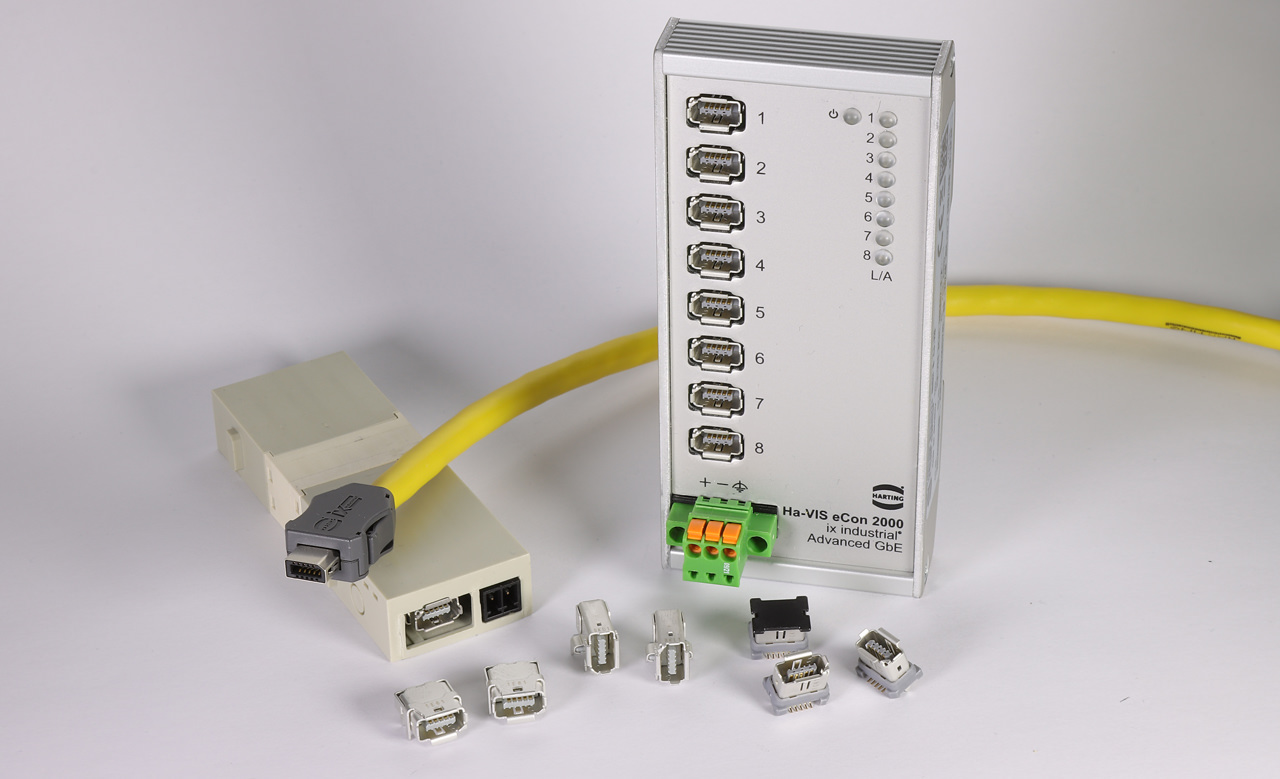
Industrial Ethernet switches and connectors
Focus on applications
All of these robust data interfaces can be used in different market areas. Automation, machinery, transportation, everywhere a strong, reliable und fast connection is demanded.
“The different solutions out of RJ Industrial, ix Industrial and Single Pair Ethernet are working together like a cascade,” Diekmann said. “RJ45 is typically used in enterprise and IT level, cabinets and standard applications. ix Industrial is the perfect solution for smaller cabinets, space reduced devices and every application, which needs to be small but connected to standard Industrial or Gigabit Ethernet.”
He added that Single Pair Ethernet (SPE) reaches the “last mile”. Without a protocol and system break, without gateways ethernet can communicate straight to the edge, if necessary, in real-time. All together, they enable building the infrastructure for IIoT communication.
Engineering challenges
Diekmann said that the I/O interface of a device is often the biggest part of its PCB. If there would be a smaller, but equally powerful and trusty connectivity solution, engineers can reduce the size of housings more effectively.
Many parts of an automation concept are using RJ45 interfaces, but in the past, cheap infrastructure caused a lot of interruptions and network issues. One solution is to level up and use a product such as the HARTING RJ Industrial MultiFeature solution.
“You want to upgrade an old machine concept with vision systems, but a bus System does not support necessary data rate? Use SPE and our internationally standardized (IEC 63171-6) interface T1 Industrial. It’s compatible with all vendors, using the IEC standard, much smaller stand 4 or 8 wire solutions. Perfect for the field,” Diekmann said.
Learn More: Industrial Ethernet Week 2
If you want to learn more about future industrial communication innovations, sign up for Industrial Ethernet Week 2, held from the 21st to the 23rd of February 2023. Interesting guests and HARTING experts will discuss all of the challenges and opportunities with Industry 4.0.
Cat7 – The cabling solution for industrial requirements
Cabling technology with a high data rate and a sturdy connection
Future-proof networks are especially required in industrial installations. An important part of this is the use of the correct cabling solution. Industrial cables need to support the high demands of an industrial setting, whether it is a high data rate or a sturdy connection. This is where the new IE FastConnect Cat7 cable from Siemens comes into play.
The new Cat7 cable has been developed for the use in industrial areas. Cat7 performs according to the IEC61156 specifications, ensuring a data rate high enough for industrial purposes (up to 10G Ethernet). Thanks to being designed without an internal cross divider, stripping the cable can be done in a single step with the help of the FastConnect stripping tool. The Cat7 cable also easily connects to the IE FC RJ45 Plug 4×2 and the IE FC M12Plug PRO 4×2. This ensures that all expectations of future-oriented and industrial-grade installation components are met.