TechnologySeptember 30, 2024
Challenges of a High-Density and Non-Concentrated Temperature Monitoring System
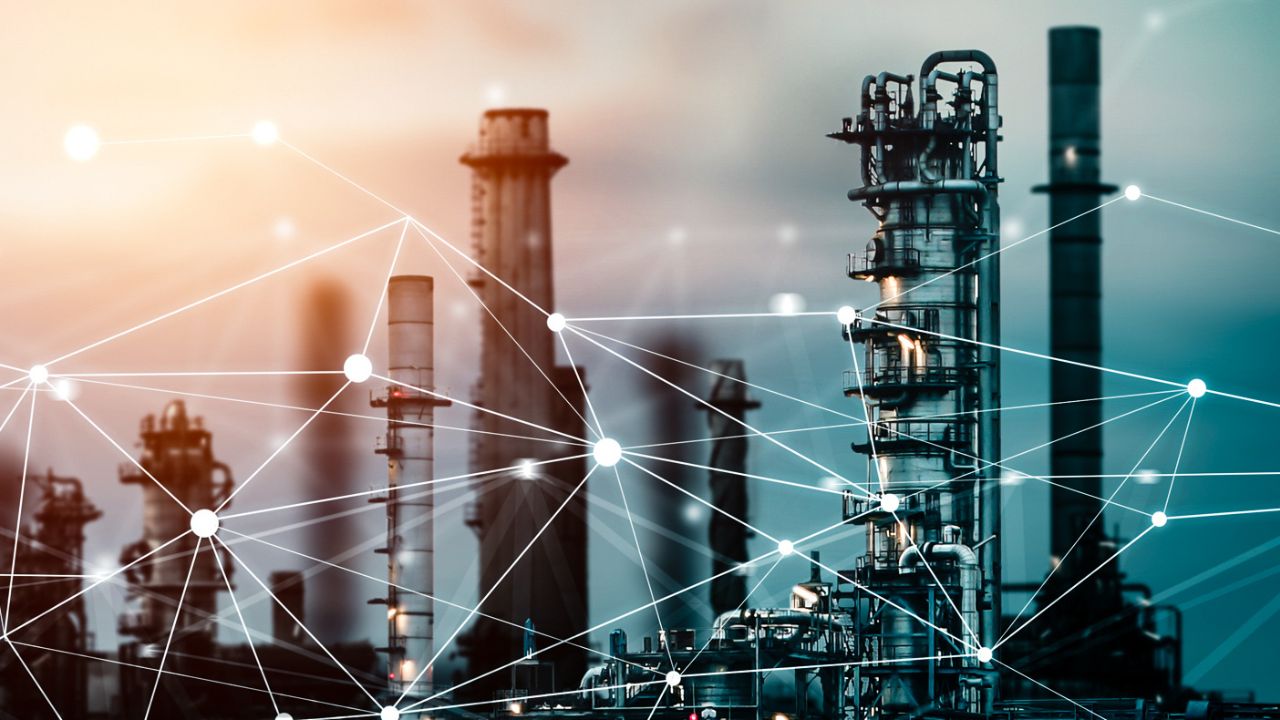
The traditional approach to temperature monitoring in process control applications involves challenges that can increase initial setup and ongoing maintenance costs, while also complicating monitoring system management and reducing operational efficiency.
Within the process control industry, precise temperature monitoring is crucial not only for ensuring product quality but also for safety reasons as well. Temperature may need to be monitored at different ranges within several different parts of a facility, requiring the need for many different types of thermocouples and RTDs connected to dedicated temperature transmitters for each zone or point that needs to be monitored. This brings several challenges including complex wiring and installation, costly and long lead wire extension cables, high cost of dedicated transmitters per point, and often space limitations for temperature transmitter installations.
One of the biggest aforementioned challenges of a temperature monitoring system that doesn’t utilize a high-density concentrated monitoring solution is the complex and costly wiring and installation of the overall system. A traditional non-high-density monitoring system would require an extensive wiring infrastructure, with each temperature sensor connected to a dedicated temperature transmitter via individual wires for each pairing. This can result in a maze of cables that need to be carefully managed and installed. The complexity only increases with each sensor type and transmitter within the monitoring system, leading to time-consuming installations, more potential for errors, and maintenance challenges as the equipment and extension wire age. Incorrect wiring within the system can lead to faulty temperature readings and sometimes even damage the monitoring equipment. When an issue arises within a large temperature monitoring system with extensive wiring, locating the exact source of the problem can be challenging which can lead to longer repair times and thus increased downtime.
The cost implications within a traditional temperature monitoring system that involves temperature transmitters can also be significant. The need for multiple temperature sensors, transmitters, and extensive wiring translates to high initial setup costs. Each temperature transmitter not only adds to the overall cost of equipment but also requires additional power and space. Ongoing maintenance cost is another concern as routine maintenance of equipment is necessary to ensure accurate readings and operation. Some examples of maintenance of the sensors and transmitters can be calibration of transmitters, replacement of faulty sensors or transmitters, and inspection of the complex wiring, which all incur costs. Additionally, the power consumption of several transmitters adds to the overall operational expenses, either through multiple regulated bulk power supplies and marshaling cabinets or higher-end control system cards that provide loop power to the transmitters, all of which directly increase the overall cost of the system.
Managing data from numerous temperature transmitters in a traditional temperature monitoring system also has its cost and configuration challenges. Each sensor-transmitter pair must be wired back to a centralized control system such as a BCPS (Basic Process Control System) or PLC (Programmable Logic Controller), creating high costs including analog input cards and lots of copper twisted pair. Once wired, all control system inputs need to be configured and ranged, tagged, and assigned to an input register.
Consider a chemical plant that needs to monitor 100 temperature points within its processing facility. In a traditional temperature transmitter-based monitoring system, each of the 100 temperature sensors would need to be individually wired to a temperature transmitter, potentially involving hundreds of meters of cable and wiring through the plant. This requires significant labor and time. With each transmitter costing multiple hundreds or even thousands of dollars, the initial setup of just the transmitters alone could easily exceed costs in the tens of thousands of dollars. Once set up, each temperature transmitter requires detailed configuration and documentation within the control or monitoring system. If the temperature transmitters have to be installed in hazardous areas, expensive explosion-proof housings or a complex intrinsically-safe network of barriers and marshaling cabinets must be designed and procured, further leading to higher ongoing maintenance overhead and costs.
The traditional approach to temperature monitoring in the process control industry involves several challenges that not only drive up the initial setup and ongoing maintenance costs but may also complicate the monitoring system’s management while reducing operational efficiency. Addressing these issues can be accomplished with a more efficient and cost-effective temperature concentrator or remote I/O system such as the TCS Temperature Concentrator System.
Learn About Overcoming These Challenges With Ethernet