TechnologyMay 18, 2023
Digital data chain saves time and costs
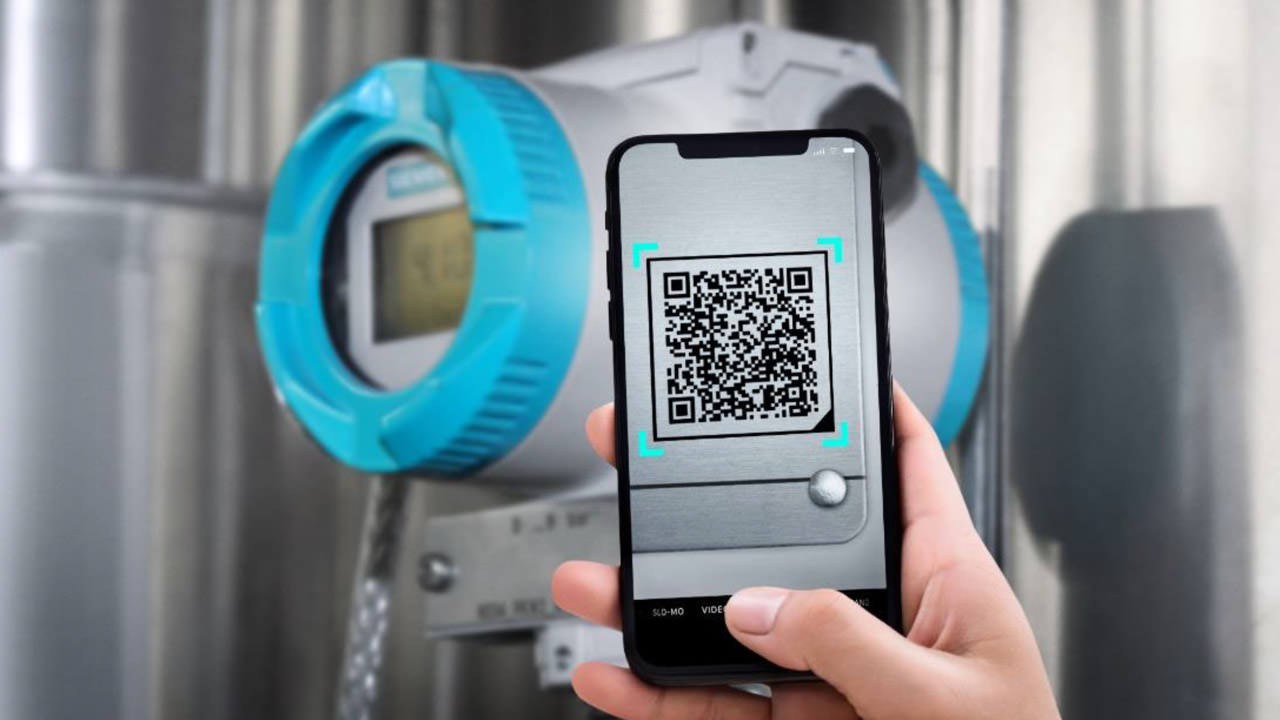
The Digital Data Chain combines future-driven technologies offering an efficient exchange of data and information based on a uniform standard, on all levels, and with international validity. In the future, all of a plant’s components will be quickly identifiable via an ID Link using standard mobile devices.
Making product data for plant components available digitally and at all times – that is the basic idea of the so-called Digital Data Chain (DDC).
Digital data chain
Siemens is a pioneer in mapping the entire digital data chain as the company has now supplied Bayer’s Crop Science Division with several SITRANS P320 pressure transmitters with standardized ID links for unique object identification. In this way, the associated instance-specific, digital documentation according to VDI standard 2770 could be transferred directly to the ERP system used by Bayer.
“With the digital data chain, plant operators save a lot of time and money,” said Axel Lorenz, CEO Process Automation at Siemens. “Currently, plant maintenance personnel spend most of their working time searching for relevant information.”
“In the future, components at the field level can be identified quickly and reliably via mobile devices. At the same time, all information about the component is immediately available digitally – for example for operation or maintenance,” he added
Manufacturer information on plant components crucial for operation
Various technical goods, plant components and equipment are used in process plants. For their correct planning, installation, commissioning, operation, cleaning, maintenance and servicing over the entire life cycle of the equipment, technical information is required that is contained in the original manufacturer’s specifications.
This information can now be read out in the cloud in a standardized manner via a digital data chain and made available regardless of location. Behind the Digital Data Chain is the Digital Data Chain Consortium (DDCC), a cross-industry association of more than 50 companies in the process industry founded in 2021.
The aim is to create standards and platforms for the exchange of information among each other. In the future, all physical plant objects will be identifiable as an instance via a digital nameplate – for a lifetime and across all stages of the product life cycle.
Transfer all information to the ERP system via scan
Three technologies underlie the data consistency of the digital data chain: the automatic identification of plant components (according to IEC 61406-1), digital manufacturer information (according to VDI guideline 2770) for standardized data provision and a cloud-based information platform (IEP – Information Exchange Platform).
The minimum requirements for a globally unique identification of physical objects are specified in the international standard IEC 61406-1. Based on this standard, Siemens is delivering more and more devices with such an ID link, which enables access to a cloud-based backend via which the product information is provided.
“The digital data chain makes it possible for manufacturer specifications of components to be transferred directly to the recipient’s ERP during the scan in goods receipt,” Lorenz said.
In addition to the SITRANS P320 pressure transmitter, Siemens has made further products DDC-compliant, such as the DQ 16 digital output module of the SIMATIC S7-1500 controller.