TechnologyMarch 22, 2024
Digital transformation: make your digital factory a reality
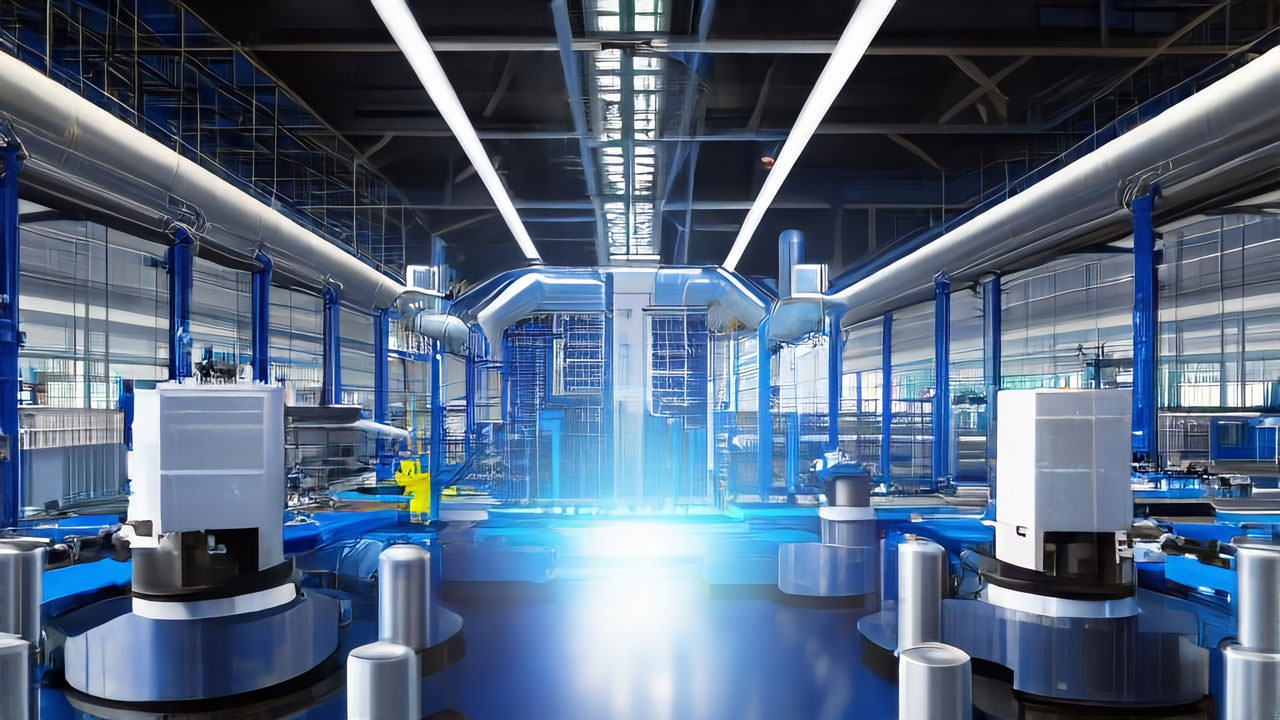
As digital transformation accelerates, factories face both opportunities and challenges. New technologies are key to increased efficiency, but implementing these technologies can be complex and requires thoughtful execution. Explore how digital factory implementations can help realize manufacturing plant efficiencies.
Are you interested in how a digital factory works and operates? This article parallels the operation of the digital factory to the workings of the human body, outlining the importance of data as the lifeblood of the digital factory. Explore how digital factory implementations can help realize manufacturing plant operational efficiencies through Intelligent Edge insights.
The digital factory, whose operations are built on data, represents a system of component elements working in harmony to optimize operational efficiency across the factory floor. In some ways, it could be likened to the human body. The sensors act as the eyes and ears that allow a central controller—or brain—to be aware of its surroundings. The actuators act as the muscle to make adjustments as required. The factory connectivity network can be equated to the nervous system deployed throughout the body, while the skin is representative of the cybersecurity technology crucial to protecting the data.
Benefits of the digital factory
Before exploring the components of the digital factory, let’s first outline the benefits. The benefits of the digital factory are centered on enabling greater productivity, which is transforming the manufacturing landscape. New insights from the digital factory ecosystem help to inform real-time decision-making. This results in improved product quality and increased overall operational efficiency, culminating in more sustainable production processes. Given that the industrial sector consumes approximately 50% of the world’s total energy, for manufacturers with a net zero goal, the digital connected factory is at the heart of this transformation.
In addition to sustainability benefits, digital factories provide the flexibility and real-time configurability to rapidly respond to evolving changes in consumer demand. For example, in the healthcare sector, there is an increasing demand for personalized medical devices such as 3D-printed joint implants tailored to an individual patient’s anatomy. As factory designs become more modular and production cells become smaller and more adaptable, workflows can be scheduled and changed in real time, boosting manufacturing speed and supporting the viability of cost-competitive on-shoring efforts across Europe and North America.
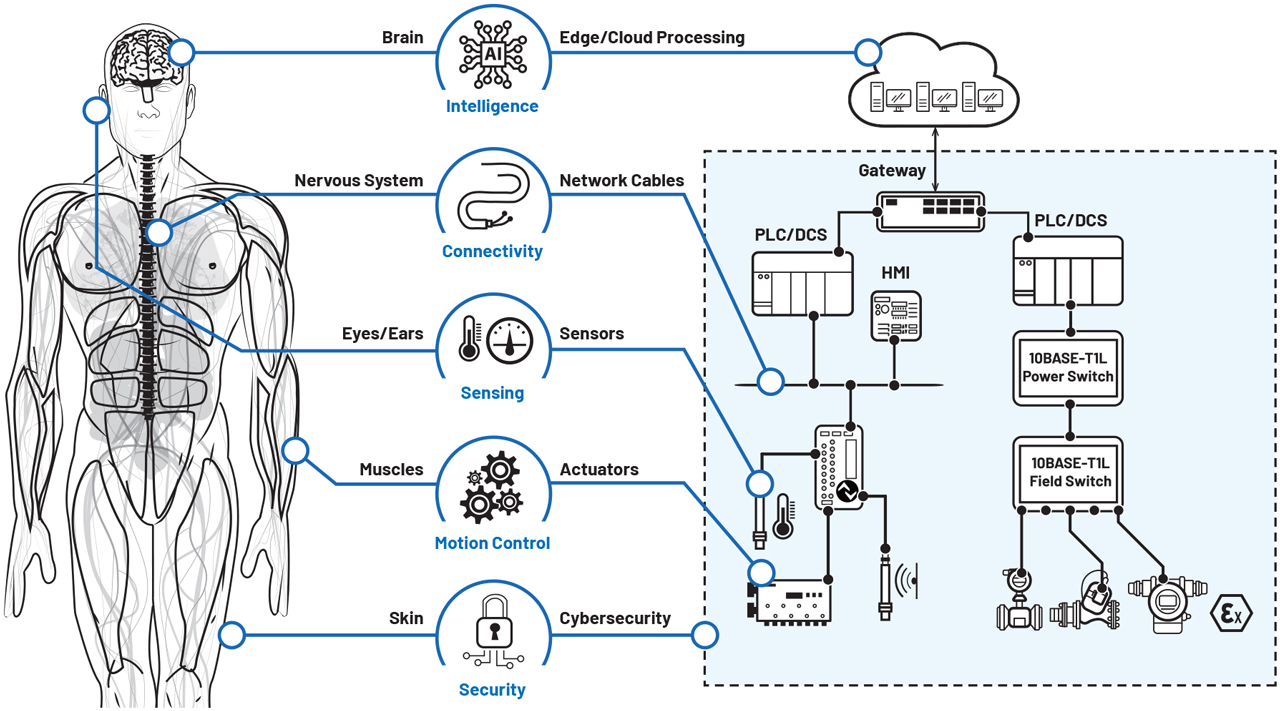
Figure 1. The anatomy of the digital factory.
Data: lifeblood of the digital factory
Both real-time and nonreal-time data, derived from multiple sources across the factory, must be analyzed quickly and reliably, at the Intelligent Edge—where the data is born—and aggregated at a central level to reveal a holistic picture of the complete factory operation. Operational insights derived from this data are integral to realizing the full operational efficiency potential of the factory.
Sensors: eyes and ears of the digital factory
More sensors and varieties of sensing modalities such as temperature, pressure, flow rate, proximity, and vibration need to be deployed to acquire the necessary data. Precision measurement and sensing technology is required to continuously sense, measure, and interpret factory assets. IO-Link® technology enables sensors to become intelligent. A pressure sensor locally decides if the pressure exceeds the required threshold and thus only needs to provide the controller with a single Boolean bit variable (yes or no), representing one bit of data instead of a full digital value representing the actual pressure measurement. Localized decision-making saves communication and processing time, making for efficient distributed control.
Actuators: muscle of the digital factory
Actuators, often the unsung heroes of the digital factory, act as the muscle—critical to getting the job done. These actuators are used to control valves, pistons, and other mechanical devices. This allows the flow of fluids to be controlled precisely, ensuring that the correct amount of material is delivered to each part of the process.
Both sensors and actuators need to be tolerant of conditions found in their application space. Harsh factory environments include high temperature and electromagnetic compatibility (EMC) emission exposure, as well as supply voltage transient spikes and mechanical vibration. For these edge sensing and actuating systems, power delivery is another key consideration.
Power delivery performance requirements increase as sensors and actuators become smaller, with the accuracy and quality of the signal acquisition increasing at the same time. This demands highly efficient, low noise power management solutions with reduced footprint, critical in what can often be space constrained designs. Without the necessary power technology suitable for specific sensing requirements, the real-time configurability benefits of the digital factory cannot be realized.
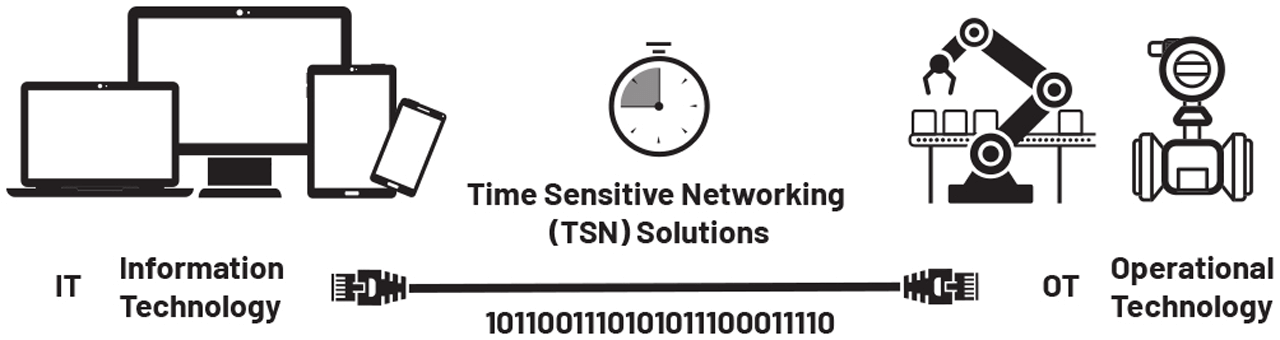
Figure 2. Benefits of the digital factory.
Edge and central intelligence: brain of the digital factory
Given that the digital factory requires devices at the edge to have increased levels of functionality and intelligence, more computations and analytics must occur within the device itself to enable localized decision-making. To enable such edge autonomy, local artificial intelligence (AI)/machine learning (ML) engines, low power accelerators, increased memory, and processing power are required.
Sensor fusion is another type of edge intelligence where data from multiple different types of sensors can be simultaneously combined to reveal a more accurate measurement—one that would be impossible using sensors singularly.
With new high precision and high bandwidth ADCs, a single sensor front end can be used to monitor multiple sensor elements, saving space and power. AI microcontroller technology enables neural networks to execute at ultra low power, while low power transmitters enable enhanced diagnostic capabilities even in remote process plants, often an extension of the smart factory.
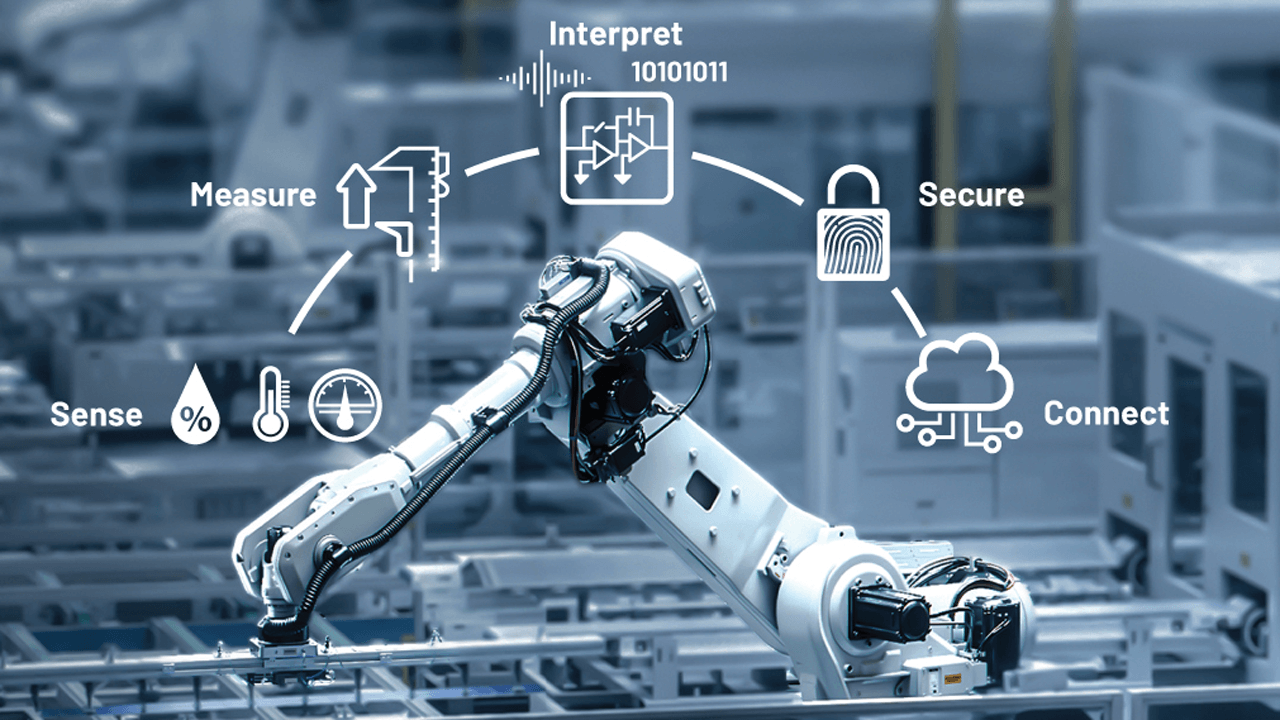
Figure 3. Building blocks of the modern digital factory.
Connectivity: nervous system of the digital factory
Despite this edge device autonomy, for manufacturers to extract valuable and productivity-improving insights from the abundance of available data, the ability to transport, analyze, and merge this data with existing information streams within the factory is paramount. This requires low latency, time-bound, low power, robust, industrial connectivity technology. 10BASE-T1L is an Ethernet physical layer standard (IEEE 802.3cg-2019) set to dramatically change the process automation industry by significantly improving plant operational efficiency through seamless Ethernet connectivity to field-level devices (sensors and actuators).
In today’s factories, an information technology (IT) network is deployed at an office/enterprise level. The IT network is traditionally concerned with things like data storage, data analytics, and business applications. While these are important, they are not typically as time critical as data exchange on the factory floor. The network running the production lines on the factory floor is referred to as the operational technology (OT) control network. Within that control network, there can be multiple different production cells or machines that often have limited ability to communicate with each other. The concept of the converged IT/OT network within the digital factory changes all of this. It offers one unified factory network, where all devices, machines, and robots are connected and interconnected, and speak the same language.
Each IP-addressable device can be communicated with in real time or near real time and be configured independently of other devices on the network. Key enabling technologies for such a converged digital factory network are Industrial Ethernet, time sensitive networking (TSN), Ethernet-APL (advanced physical layer), and IO-Link. With all devices speaking the same Layer 2 language, it is now possible to control both the IT and the OT portions of the network with the same control and network management system, while the time sensitive traffic of the operational network is respected.
The sheer volume of both time-critical and nontime-critical traffic demands network upgrades for increased bandwidth to ensure the latency-free delivery of data, which is critical to the high product quality and operational efficiency of the manufacturing plant. The convergence of OT and IT makes scalability opportunities virtually limitless.
Cybersecurity: layer of skin protecting trusted digital factory data
With increased interconnectivity comes the need for heightened data security, as smart factory environments expose people, technology, processes, and intellectual property to cyber threats. This is driving the need for features like secure boot, secure software update, secure transmission authentication, and hardware root of trust.
A fundamental aspect of securing a network is the authentication of each new device attempting to connect to the network. It consists of checking that the device is genuine before authorizing any network transaction with it. Like device authentication, secure boot is a must have, ensuring field equipment executes only software coming from a trusted source with public key cryptography employed to verify the digital signature of the firmware.
What technology solutions are available today?
Analog Devices has always been valued for innovative precision technology used to sense, measure, and accurately control devices throughout the factory. Combining this with an expansive industrial connectivity and power portfolio, and additional digital capabilities, including AI expertise, ADI has the technology and domain expertise to make advanced digital factory capabilities become a reality.
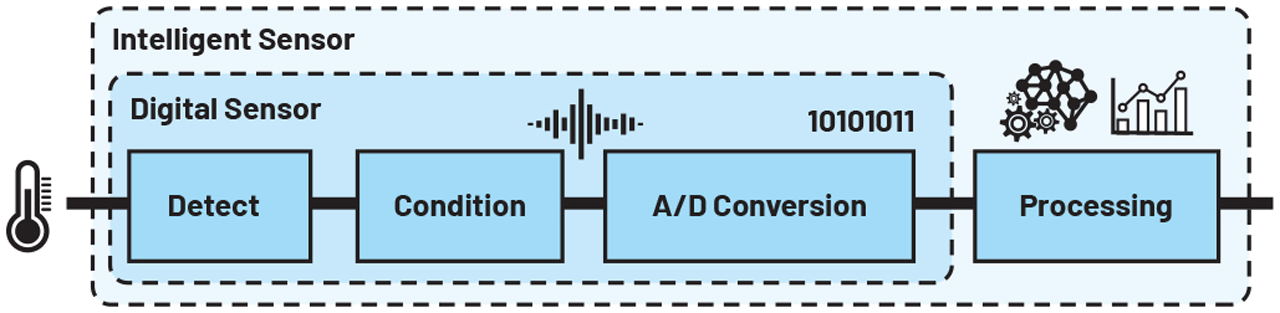
Figure 4. Enabling edge autonomy with intelligent sensors.
Low bandwidth, multichannel sigma-delta ADCs such as the AD4130 family integrate the full analog front-end circuitry for effortless interfacing to multiple sensor types. This enables sensor fusion with advanced diagnostics to support localized fault detection and fast decision-making.
The industry’s lowest power 10BASE-T1L ADIN1110 MAC-PHY and accompanying ADIN1100 PHY enable the transition to seamlessly connected field devices, bringing Ethernet-APL all the way to the process edge, over 1.7 km of single-pair Ethernet cables.
For cybersecurity, turnkey, hardware-based solutions allow customers to easily integrate data security into their products. The DS28S60 and MAXQ1065 are ultra low power secure integrated circuits (ICs) that enable public key cryptography even in the most power and computational-resource constrained designs.
The MAX78000 AI microcontroller enables neural networks to execute at ultra low power, providing actionable insights from AI at the edge.
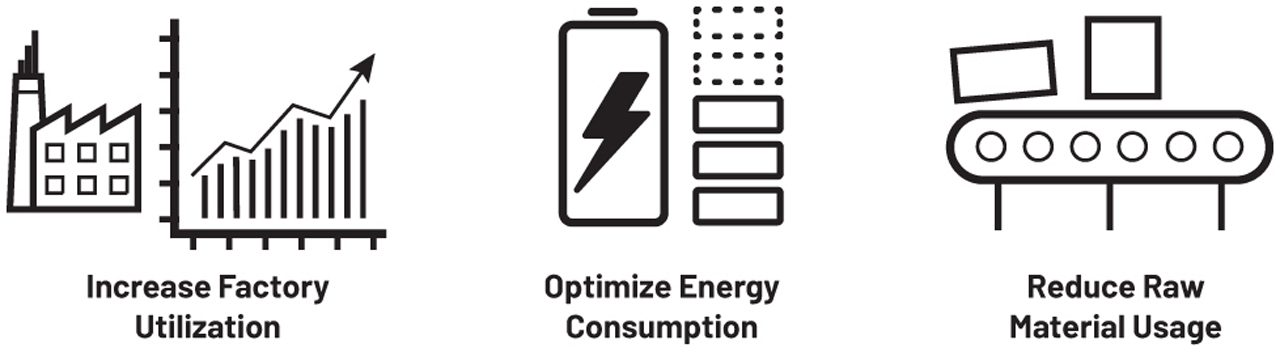
Figure 5. IT/OT convergence within the digital factory.
Path to the pervasive deployment of the digital factory
Industry surveys suggest that 85% of companies have accelerated digital transformation within their manufacturing plants in the past 2 to 3 years. However, full digital factory implementations are not the norm yet.
The World Economic Forum’s global lighthouse network of leading manufacturers is demonstrating how digitalization strategies and digitally infused operations bring benefits beyond productivity gains to create a base for sustainable, profitable growth. These manufacturers are capitalizing on productivity improvements by unlocking capacity through the deployment of innovative technologies. These technologies accelerate efficiencies and, in turn, yield environmentally favorable outcomes. This is resulting in a dual benefit of increased productivity with increased sustainability—effectively eco-efficiency.
Conclusion: make your digital factory a reality
Leveraging partners with deep domain expertise is paramount to enhancing operations and unlocking efficiencies. This collaboration lies at the heart of the most robust and adaptable digital factories of tomorrow.