TechnologyNovember 8, 2022
Ethernet-APL for end users and device manufacturers
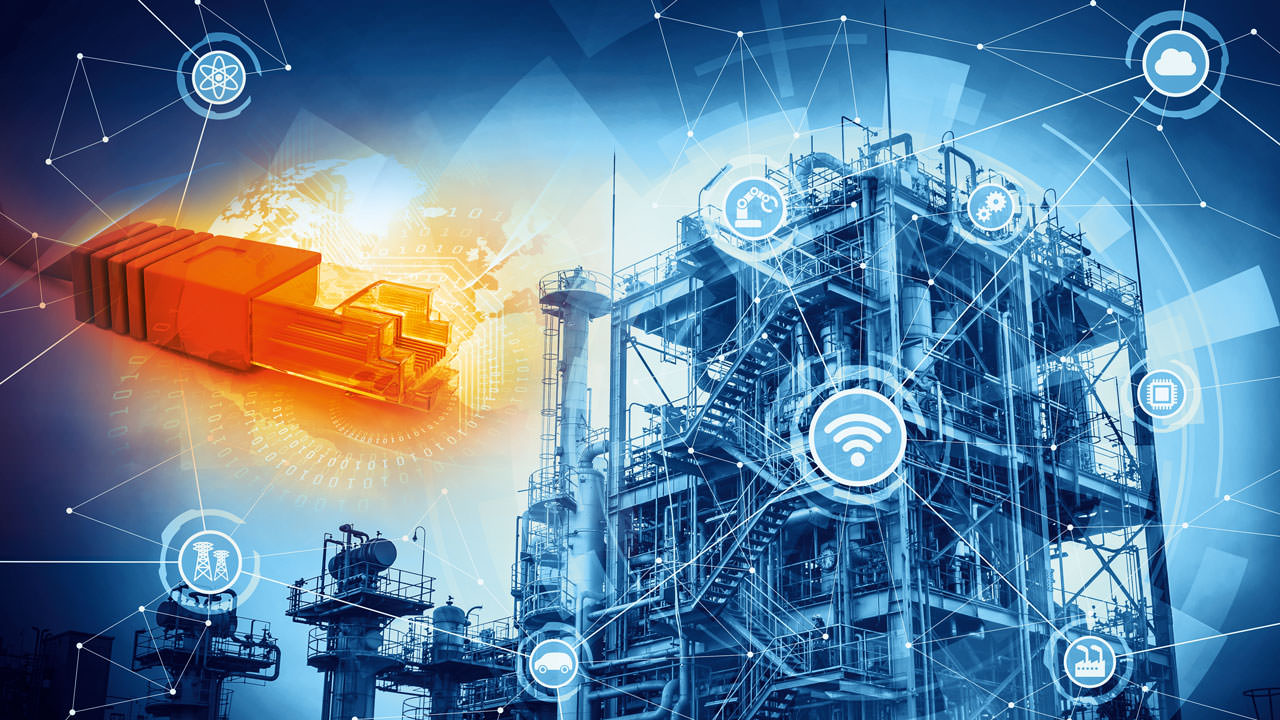
Ethernet-APL (Advanced Physical Layer) offers considerable benefits for end users in the process industry by facilitating seamless connectivity between field devices using the Ethernet protocol and greatly simplifying the creation of high-performance automation networks.
From simple sensors to complex, analytical instruments, we find millions of installed devices in process manufacturing – with millions more being added every year. Even today, most devices still use 4–20 mA technology, maybe supplemented by digital point-to-point communication over the HART protocol.
This is true even though, roughly three decades ago, digital field buses like PROFIBUS PA and FOUNDATION Fieldbus H1 were introduced, which use a centralized communications network to supply control systems with other measurement data in addition to simple process values, plus many parameters and field device states. Apparently, the deployment of these field buses is restricted to comparatively few – often highly specialized – applications, due to their complexity and performance data.
Considerable expertise is required, and specialized gateway components are also needed to integrate them into upstream Internet infrastructure. Alongside triggering additional hardware costs, configuring these network gateways also requires quite a bit of configuration effort.
Last year, with the aim of removing these obstacles, a new standard, Ethernet-APL, was adopted for continuous Ethernet communication down to field devices. The standard accounts for the specific requirements of the process industry, like the bridging of large distances with a simple, two-wire conductor that not only handles data communications but also supplies power to the connected field device. At 10 Mbps, transmission rates are far higher than with HART and field buses. Corresponding performance definitions also allow the implementation of intrinsically safe devices. Since Ethernet-APL limits itself to defining a new data exchange standard for Ethernet at the lowest layer, it retains compatibility with arbitrary Ethernet-based protocols at higher layers. For the first time, this enables transparent communications between production and even corporate networks right down to the field device, without the need for gateways. It also allows a free choice of automation protocol and other conveniences like web servers, OPC UA, and cloud/edge connectivity.
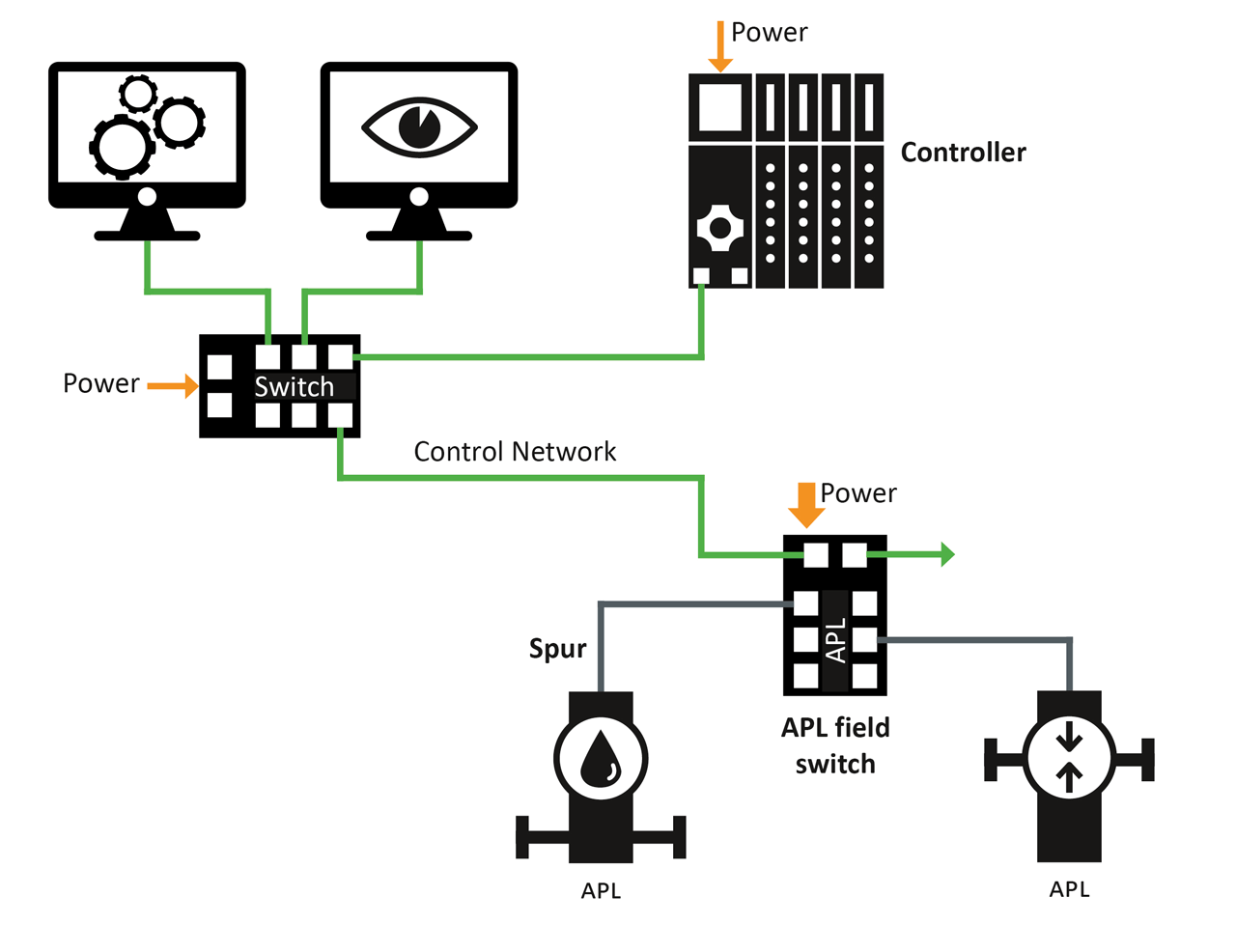
Standard Ethernet topology.
Ethernet-APL is easily mature enough to permit the deployment of corresponding devices in production environments. Both end users and device manufacturers face challenges when getting started with this technology, however: the ideal scenario is for the pool of deployed components to be as broad-based as possible. With suitable infrastructure components and communications modules for field devices, this “waiting game” can be minimized – as is explained in the following.
The different network topologies for Ethernet-APL
The Ethernet-APL Engineering Guideline describes three separate network topologies for Ethernet-APL networks. The situation for the Ethernet-APL spurs is the same for all three topologies. Ethernet-APL devices can be connected to a switch by a Category IV cable no more than 200 m in length and can communicate at a transmission rate of 10 Mbps. In the first topology scenario discussed, an APL field switch is connected directly to a standard Industrial Ethernet network.
Whether the field switch is installed in an electrical enclosure or in the field will depend on the circumstances on-site. The control network in this scenario can be implemented using normal Ethernet copper cables or optical fiber. The typical transmission rate in this section of the network will be 100 Mbps.
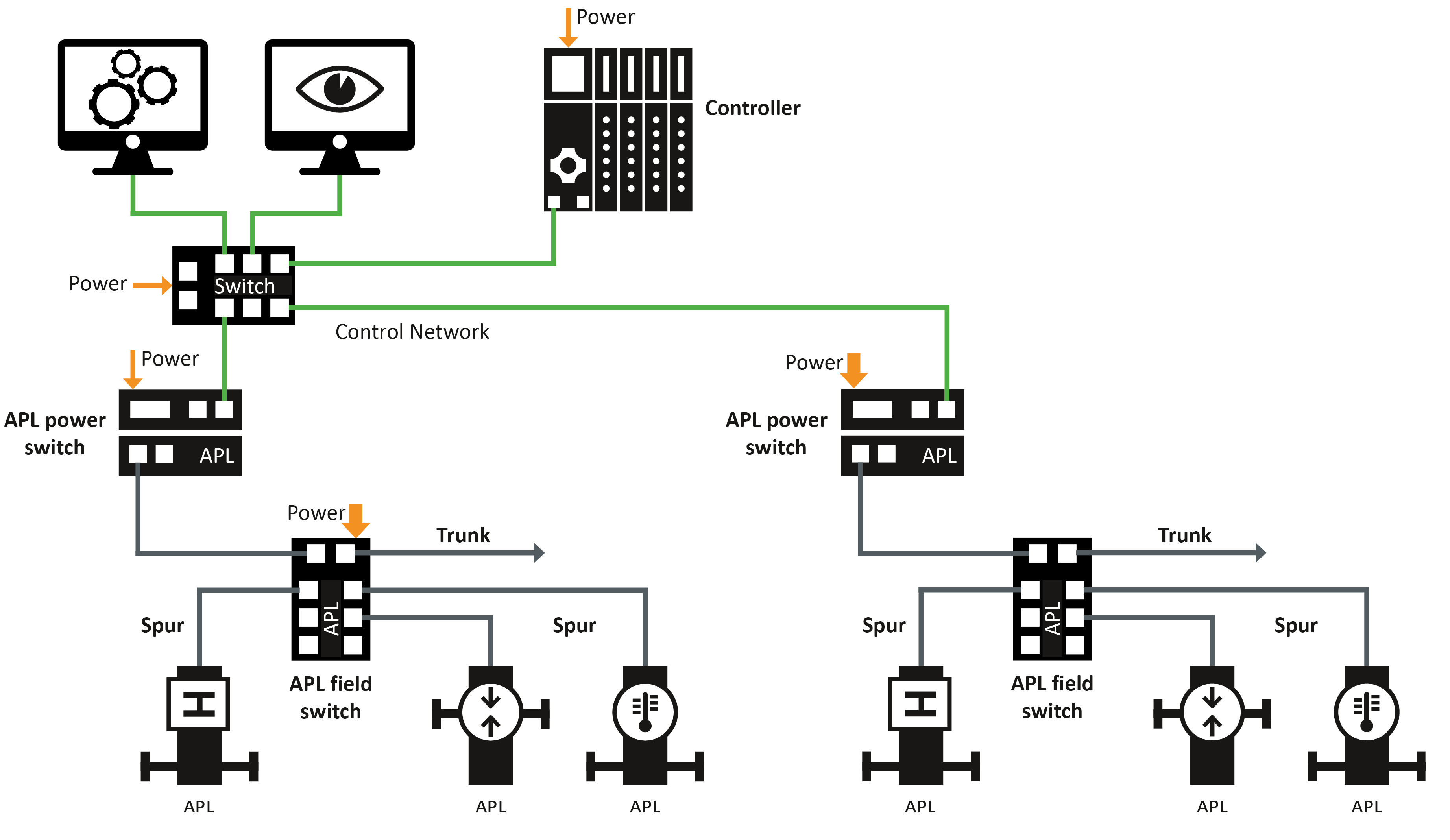
Trunk-and-spur topology.
The other two topology scenarios utilize an “APL trunk”. This involves using an Ethernet-APL trunk to connect the APL field switch to the control network. The two alternatives differ in terms of the power supply via the APL trunk.
Softing assumes that many installations will pick the first topology scenario, with direct integration of the APL field switch into the control network. For this purpose, the new aplSwitch product line from Softing provides a field switch, which can be connected to the control network either with copper or optical fiber. Optimized variants will be provided for installation directly in the field and the control cabinet. The first Ethernet-APL field switch, available as a prototype, is a variant for direct installation in the field and allows the connection of Ethernet-APL field devices in Ex Zone 1 and 0.
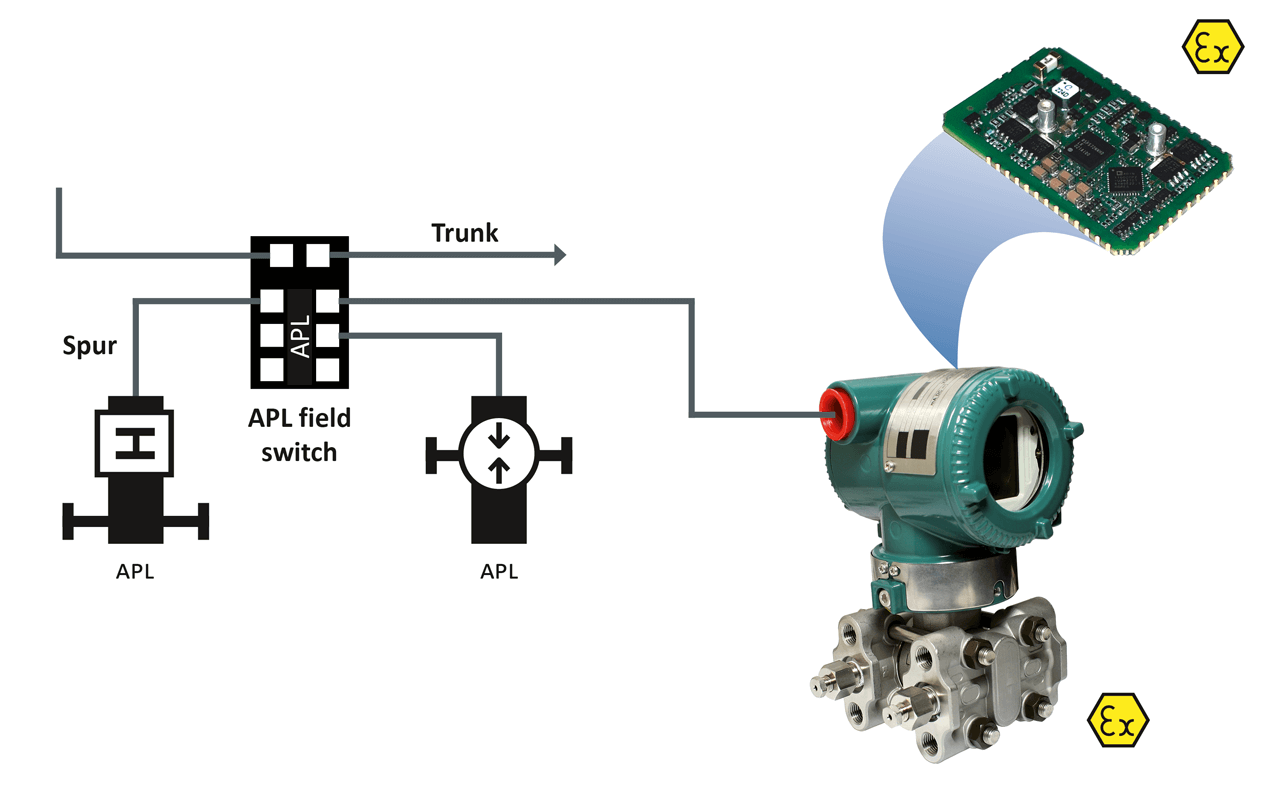
commModule APL
Network stability
Monitoring the load that Ethernet-APL devices are exposed to is essential to ensure the stable operation of PROFINET networks. Otherwise, there is the risk of load peaks causing the sporadic failure of individual devices.
Where networks transition from 100 Mbps to 10 Mbps, a higher network load in the 100 Mbps control network is especially critical for the Ethernet-APL devices on the 10 Mbps spurs, as their data throughput is just 10% of the control network.
In this case, the IEEE (Institute of Electrical and Electronics Engineers) envisages limiting ingress and egress data traffic at switch ports. Softing’s Ethernet-APL switches support these net-load rate limits, therefore making a key contribution to keeping networks stable.
PROFIBUS PA devices
As organizations start rolling out Ethernet-APL, they will encounter the problem of not having enough of the devices in their plant available as Ethernet-APL models. In the specific case of PROFINET Ethernet-APL networks, this problem can be mitigated by substituting existing PROFIBUS PA devices for these non-existent PROFINET Ethernet-APL devices.
To date, integrating PROFIBUS PA devices into a PROFINET network has meant using PROFINET-PROFIBUS PA proxy gateways like Softing’s pnGate PA. But to avoid users having to install additional gateways during the transition period, it makes sense to integrate the PROFINET-PROFIBUS PA proxy into the Ethernet-APL field switch. This allows PROFIBUS PA devices to be connected directly to the switch.
Models with an integrated PROFINET-PROFIBUS PA proxy are available for all Softing Ethernet-APL field switches. In technical terms, the switch creates an extra PROFIBUS PA network segment, to which the PROFIBUS PA devices then connect. Modules that are shown in the switch’s PROFINET device can then be used in the PROFINET controller to access the data from the PROFIBUS PA devices.
Ethernet-APL PROFINET devices and PROFIBUS PA devices both implement the PNO PA profile, so the data that is provided is similar in each case and can be converted easily when switching from PROFIBUS PA to PROFINET.
Field devices
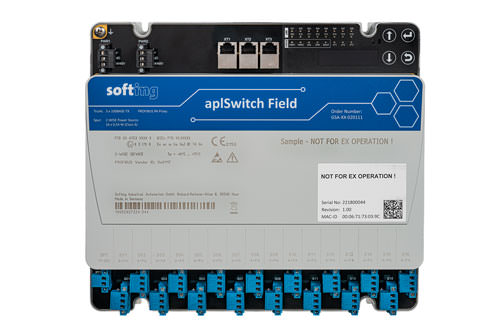
aplSwitch prototype
To make process equipment that was previously operated using HART available for Ethernet-APL as quickly as possible, device manufacturers can avoid having to start development from scratch by opting for a redesign that utilizes an electronics module providing all of the hardware and software components needed for communications.
A conventional hardware development project would require companies to implement and validate all of the Ethernet-APL interface aspects (physical connection, power supply and monitoring,…) themselves. Effort would also be needed to port a protocol stack, and implement device properties (profile) as well as the actual device application with its dynamic behavior.
Once complete, this device would then need to pass various kinds of conformity tests and certifications. Alongside EMC and environmental testing, this would also include APL Physical Layer Conformity, plus Ex certifications and conformity testing from the various Fieldbus organizations, as required. Past experience shows that this involves major effort and development times lasting up to several years. But by using a compact, pre-certified, and configurable electronics module like Softing’s commModule APL, however, many of the tasks mentioned above can be skipped or considerably shortened.
As a low-cost SMD hardware module, commModule APL not only handles the required Ethernet-APL connectivity but also offers application software that can be easily configured to implement the required behavior from the respective field device. Existing HART and Modbus devices can be migrated to Ethernet-APL without a single line of code having to be written. To achieve this, their previous hardware communications port is now provided fully digitally by the module’s UART pins.
A configuration tool is then used to define all of the necessary assignments to the device application’s existing HART or Modbus commands and load these permanently onto the module. The module software handles the mapping to the automation protocol autonomously on the basis of this configuration. The module also supplies power to the application electronics, sourcing both this energy and the power it needs itself directly from the Ethernet-APL connection.
This considerably simplifies a hardware redesign for a field device. Perhaps the biggest benefit to device manufacturers is that the module has already passed a wide range of reference certification and conformity testing. This reduces development risk while providing reference data for the relevant certification needed by the overall field device.
Another key advantage offered by a module solution is that it is a standard product in the portfolio of its manufacturer, who in maintaining this product can independently accommodate further developments in the relevant protocol profile specifications, as well as supply chain issues, and so relieve the field device manufacturer of these burdens.