TechnologyMay 14, 2022
Ethernet-APL: Optimizing Process Automation with Actionable Insights
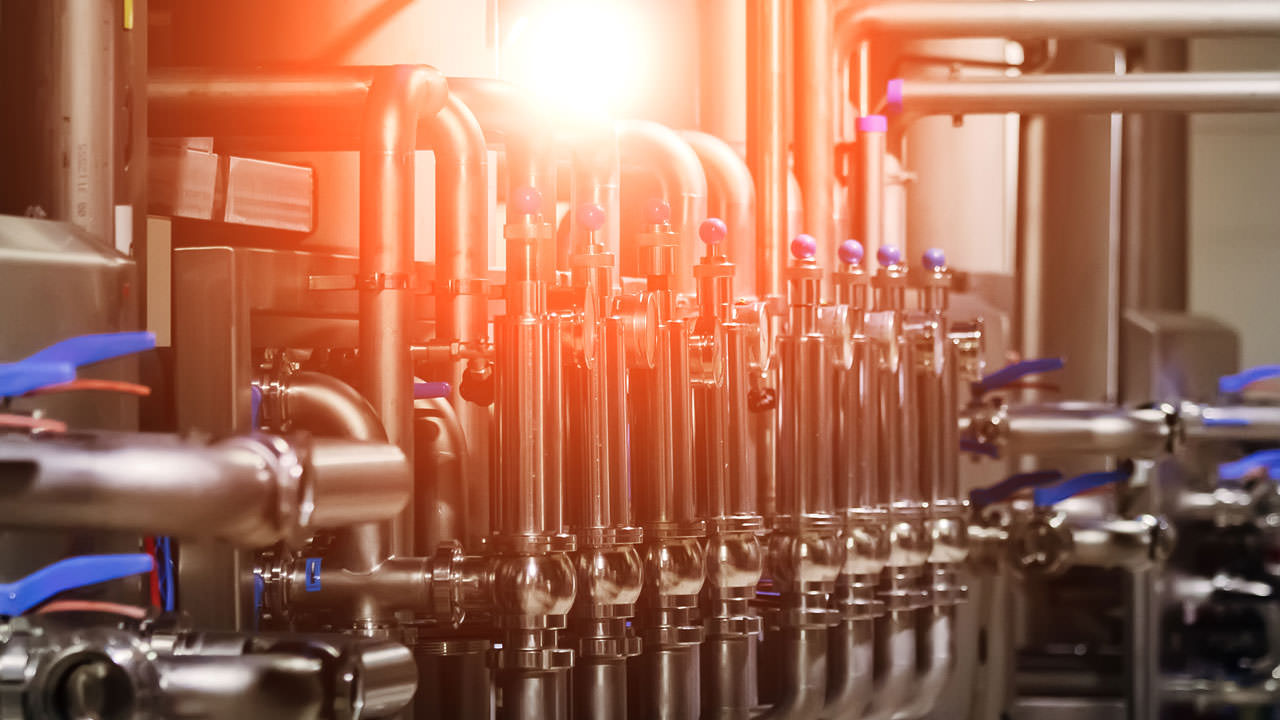
Ethernet-APL (advanced physical layer) specifies the details of the application of Ethernet communication to sensors and actuators for the process industry and will be published under the IEC. Leading companies in process automation are working together to make Ethernet-APL work across Industrial Ethernet protocols and to accelerate its deployment.
Ethernet-APL is based on the new 10BASE-T1L (IEEE802.3cg-2019) Ethernet physical layer standard, approved on November 7, 2019, and specifies the implementation and explosion protection methods for use in hazardous locations. The leading companies in process automation are working together under the umbrella of PROFIBUS and PROFINET International (PI), ODVA, Inc., and FieldComm Group to make Ethernet-APL work across Industrial Ethernet protocols and to accelerate its deployment.
Why is Ethernet-APL important?
Ethernet-APL will change the process automation world by enabling high bandwidth, seamless Ethernet connectivity to field devices. It solves the challenges that, to date, have limited the use of Ethernet to the field. These challenges include power, bandwidth, cabling, distance, and use in hazardous locations. By solving these challenges for both brownfield upgrades and new greenfield installations, Ethernet-APL will enable new insights that were previously unavailable, such as combining process variables, secondary parameters, and asset health feedback and seamlessly communicating them to the control layer. These new insights will awaken new possibilities for data analysis, operational insights, and productivity improvements through a converged Ethernet network from the field to the cloud.
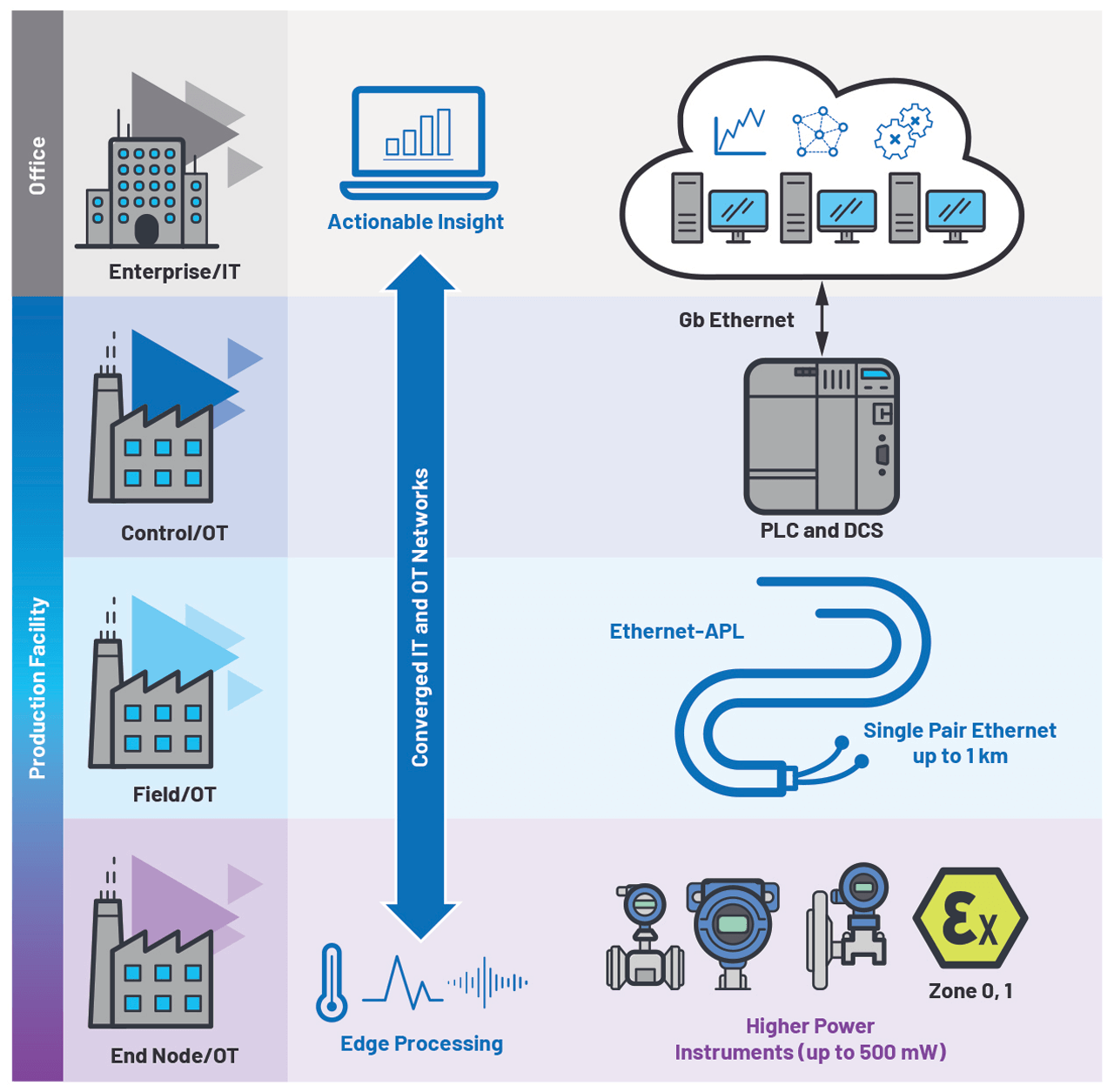
Seamless Ethernet connectivity with Ethernet-APL in process automation.
To replace 4 mA to 20 mA or fieldbus communications (Foundation Fieldbus or PROFIBUS PA) with Ethernet-APL in process automation applications, both power and data need to be provided to the sensors and actuators. The distance between field-level devices and control systems in process automation applications has been a significant challenge to existing Industrial Ethernet physical layer technologies being limited to 100 m. With distances of up to 1 km required in process automation applications, combined with the need for very low power and robust field devices suitable for use in Zone 0 (intrinsically safe) applications, a new approach to realize Ethernet physical layer technology for process automation was required. Ethernet-APL is this new approach.
Ethernet-APL is based on 10BASE-T1L physical layer capability of a full-duplex, dc-balanced, point-to-point communication scheme with PAM 3 modulation at a 7.5 MBd symbol rate, 4B3T coding. It supports two amplitude modes; 2.4 V peak up to 1000 m cable and 1.0 V peak at a reduced distance. The 1.0 V peak amplitude mode means that this new physical layer technology can also be used in the environment of explosion-proof systems (Ex) and meet the strict maximum energy restrictions. 10BASE-T1L enables long distance transmission on two-wire technology of both power and data over a shielded, single twisted pair cable.
When it comes to power delivery to field devices, Ethernet-APL can deliver up to 500 mW in Zone 0 applications, compared to that of approximately 36 mW delivered by 4 mA to 20 mA systems today. In nonintrinsically safe applications, up to 60 W of power is possible depending on the cable used. With significantly more power available at the edge of the network, new field devices with enhanced features and functions can be enabled because the power limitations of 4 mA to 20 mA and fieldbus no longer apply. For example, higher performance measurement and enhanced edge processing of data is now possible with this additional power. This will unlock valuable insights about process variables that will now be made accessible via a web server running on the field-level devices (field assets), and which will ultimately drive improvements and optimizations in process flows and asset management.
To exploit the rich dataset containing these valuable new insights, a higher bandwidth communications link is required to deliver the datasets from these new field devices across the process installation to plant-level infrastructure or up to the cloud for processing. Ethernet-APL removes the need for complex, power hungry gateways and enables a converged Ethernet network across the information technology (IT) and operating technology (OT) domains. This converged network delivers a simplified installation, easy device replacement, and faster network commissioning and configuration. This results in faster software updates with simplified root cause analysis and maintenance of field-level devices.
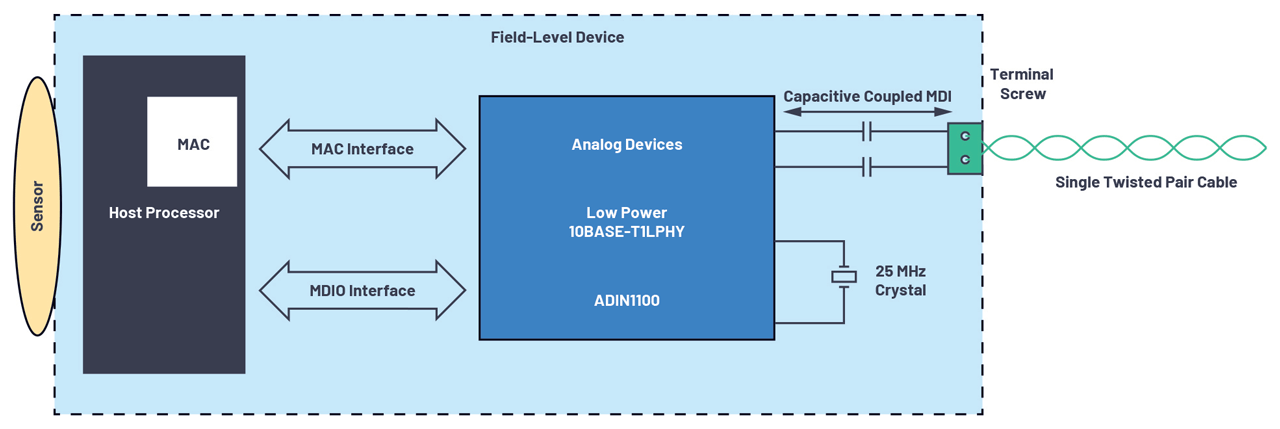
Ethernet-APL field-level device data connectivity with a 10BASE-T1L PHY.
Advantages of an Ethernet-APL Solution
By converging on Ethernet-APL, the need for expensive, complex, and power-hungry gateways has been removed. This also enables a transition from the hugely fragmented fieldbus infrastructure that has created data islands where access to the data within field-level devices is limited. By removing these gateways, the cost and complexity of these legacy installations is significantly reduced and the data islands they created are removed.
Process automation applications to date have used the legacy communications standards, as shown in Table 1, which have several limitations that the new 10BASE-T1L Ethernet standard overcomes. 10BASE-T1L provides the potential to reuse some of the existing installed cables, creating significant opportunities for brownfield upgrades of process automation installations with Ethernet-APL based on the 10BASE-T1L physical layer.
Table 1. 4 mA to 20 mA with HART® vs. Fieldbus vs. 10BASE-T1L Communications
Comparison | 4 mA to 20 mA with HART | Fieldbus | 10BASE-T1L |
Data Bandwidth | 1.2 kbps | 31.25 kbps | 10 Mbps |
Higher Level Ethernet Connectivity | Complex gateways | Complex gateways | No gateways seamless connectivity |
Power to Instrument | <40 mW | Limited power | IS: 500 mW non-IS up to 60 W (cable dependent) |
Knowledge/Expertise | Shrinking knowledge/ expertise | Shrinking knowledge/ expertise | Ethernet technology is very familiar to all college graduates |
To communicate with an Ethernet-APL enabled device, a host processor with an integrated medium access control (MAC) or an Ethernet switch with 10BASE-T1L ports is required.
Ethernet-APL Cabling and Network Topology
The 10BASE-T1L standard does not define a specific transmission medium (cable), instead it defines a channel model (return loss and insertion loss requirements). The channel model fits well with the fieldbus type A cables already used for PROFIBUS PA and Foundation Fieldbus today; therefore, some installed 4 mA to 20 mA cables can potentially be reused with Ethernet-APL. Single twisted pair cabling has the advantages of being lower cost, smaller size, and easier to install when compared to more complex cabling.
With the proposed network topology for Ethernet-APL, referred to as a trunk and spur network topology, the trunk cables can be up to 1 km in length with a PHY amplitude of 2.4 V peak and reside in Zone 1, Division 2. The spur cables can be up to 200 m in length with a PHY amplitude of 1.0 V peak and reside in Zone 0, Division 1. A power switch resides at the control level, providing Ethernet switch functionality and supplies the power to the cable (over the data lines). Field switches reside at the field level in the hazardous area and are powered from the cable. The field switches provide the Ethernet switch functionality connecting the field-level devices on the spurs to connect to the trunk and pass the power to the field-level devices.
Multiple field switches are connected on a trunk cable to provide for the high numbers of field-level devices to be connected to the network.
New Ethernet-APL Devices to Create New Opportunities
Ethernet-APL will enable the transition to seamless field-to-cloud connected process automation installations, including hazardous locations for food and beverage, pharmaceutical, and oil and gas installations. With significantly more power available, new Ethernet-APL-enabled field devices with enhanced features and functions can be supported. These new devices will unlock rich datasets for cloud computing with powerful data analytics, driving process optimization with actionable insights. New business models for the process industry will now be possible, to deliver more complex process manufacturing flows and to create value from the new insights that are now available.
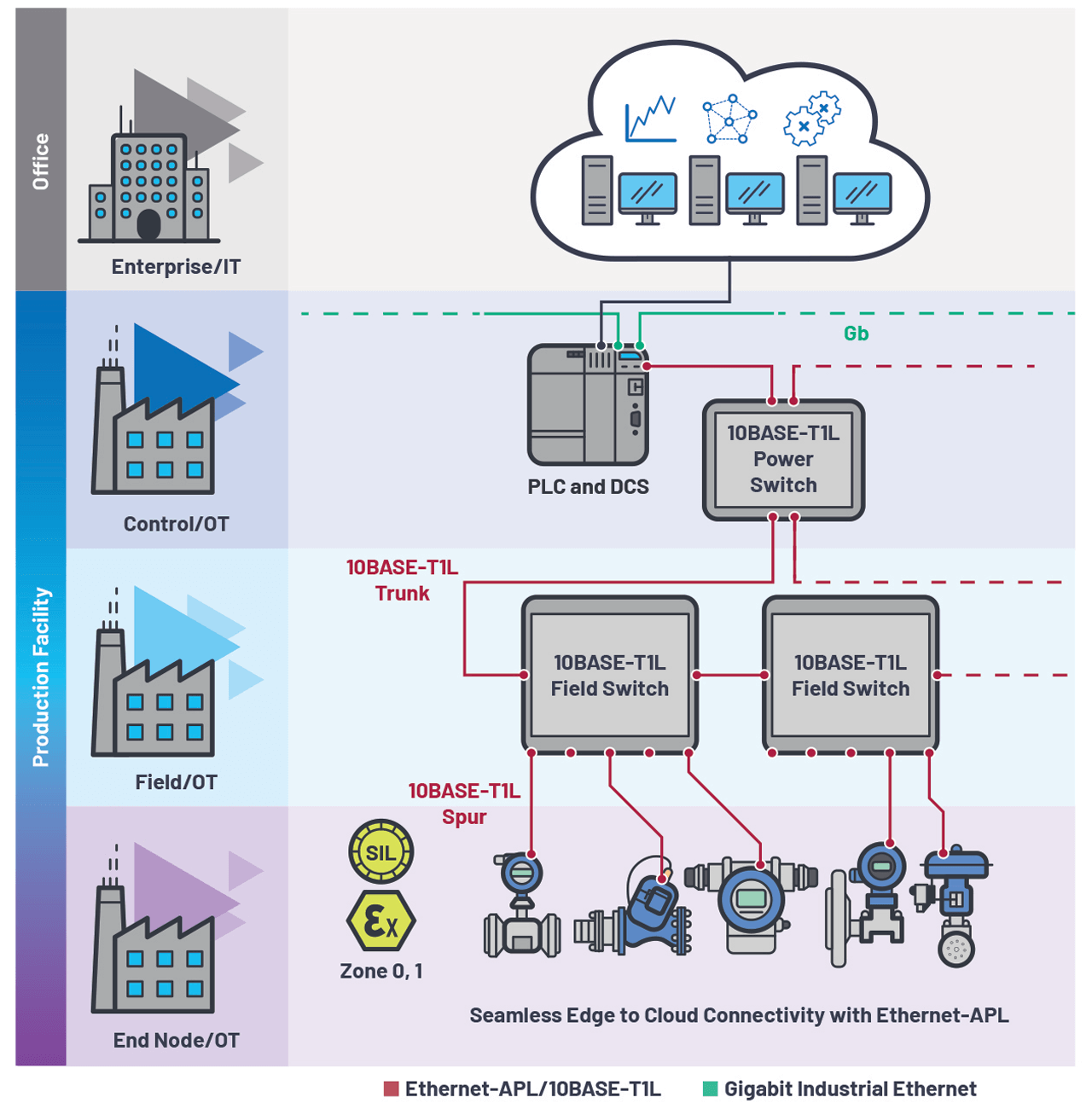
Future, seamless edge-to-cloud connectivity with Ethernet-APL and 10BASE-T1L.
What Solutions Are Available Today
ADI has extended its ADI Chronous™ portfolio with new offerings that bring long-reach, robust, 10BASE-T1L Ethernet connectivity to process automation in support of Ethernet-APL. The new Industrial Ethernet solutions are offered in two flexible options, MAC PHY (ADIN1110) and PHY (ADIN1100). The ADIN1110 enables the industry’s lowest power system design, which simplifies retrofitting for Ethernet in field instruments, sensors, or actuators, and preserves existing investment in software and processor technology. ADI’s unique MAC-PHY technology provides an SPI interface to ultra low power processors without integrated MAC, to enable lower overall system power consumption.
The ADIN1100 provides standard Ethernet interfaces and supports use in more complex designs such as field switch developments. ADI’s ADIN1100 and ADIN1110 10BASE-T1L solutions can transfer data over 1.7 km of single twisted pair cables and consume only 39 mW and 43 mW of power respectively. Single-pair Power over Ethernet (SPoE) or engineered power solutions combined with a 10BASE-T1L PHY or MAC-PHY provide both power and data over a single twisted pair cable.