TechnologyMay 20, 2024
Ethernet-APL: Single Pair Ethernet in hazardous environments
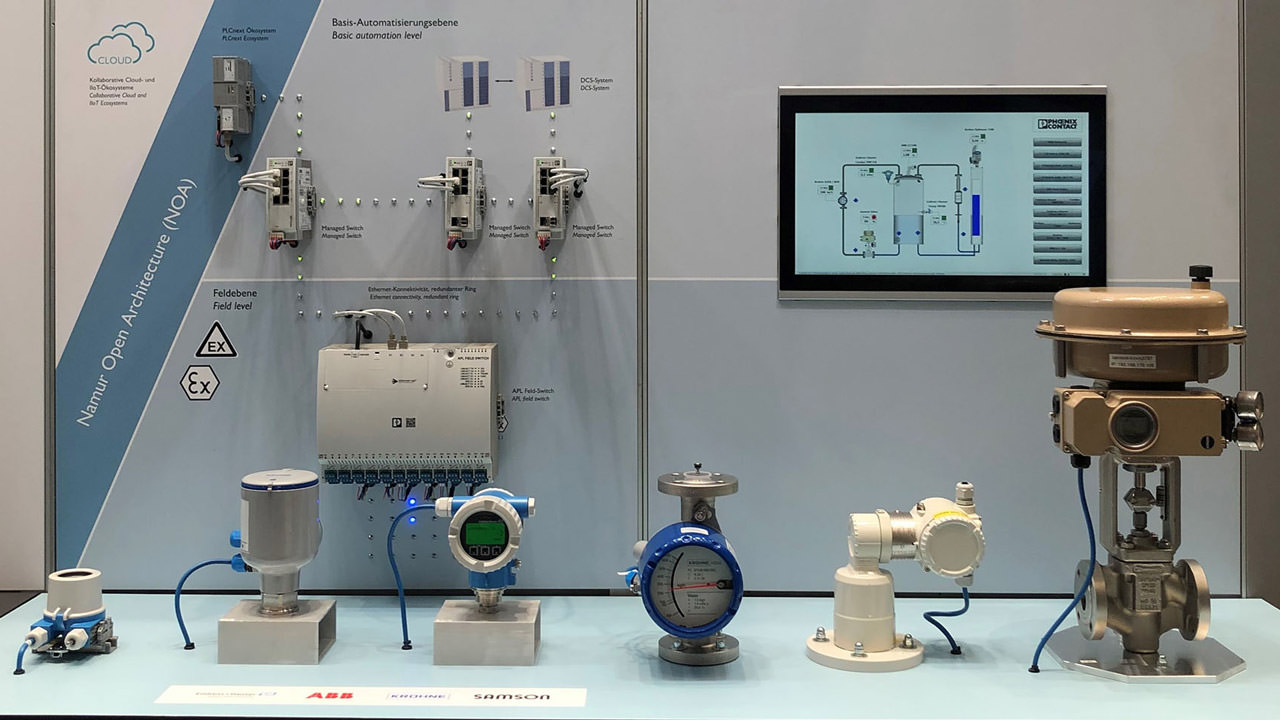
Ethernet-APL is based on IEEE 802.3cg and allows field devices to perform critical process automation tasks in severe Zone 1 locations. The technology will form the basis of future digitalization efforts and applications globally offering a speed of 10 Mbits per second, a reach of 1,000 meters and intrinsically safe protection.
Field devices in process automation applications must coordinate process values (flow, pressure, level, temperature, and process analytics) with intelligent control valves in the most dangerous and severe environments, known globally as hazardous locations. Users of the technology work in areas defined areas as Zones or Divisions, depending on their location in the world.
Ethernet-Advanced Physical Layer (APL for short), based on IEEE 802.3cg, allows the latest generation of field devices to perform these critical process automation tasks, even in the most severe locations, such as Zone 1.
As Ethernet-APL is implemented in process field devices, it will form the basis of future digitalization efforts globally. With a speed of 10 Mbits per second, a reach of 1,000 meters (3,280 feet), and intrinsically safe protection, Ethernet-APL promises a host of new possibilities for existing and future applications.
Introduction
Ever since electronics replaced pneumatics for most process industry applications, the de facto industry standard has become 4-20 mA signals over a twisted shield pair of wires powered with 24 V DC.
The 16-mA difference in the signal allows for a single process variable value to be sent or received over long distances. The 24 V DC-powered loop with a floating zero-point can detect a wire break in the signal loop when less than 4 mA is present.
The signal loop distance of up to 1,000 meters can easily exceed the 100-meter limitations of regular office Ethernet and is connected at the end opposite the process field device to a controller or remote I/O station.
Many process field devices can access additional device information via the HART communication protocol. This data can be sent and received without compromising the important primary variable (PV) device signal. The signal is sent at 1,200 bits per second using the Bell 202 standard.
Ethernet, with its classic 10/100 data-rate capability, offers significant speed advantages. And the 10 Mbits per second speed is a giant leap for the market.
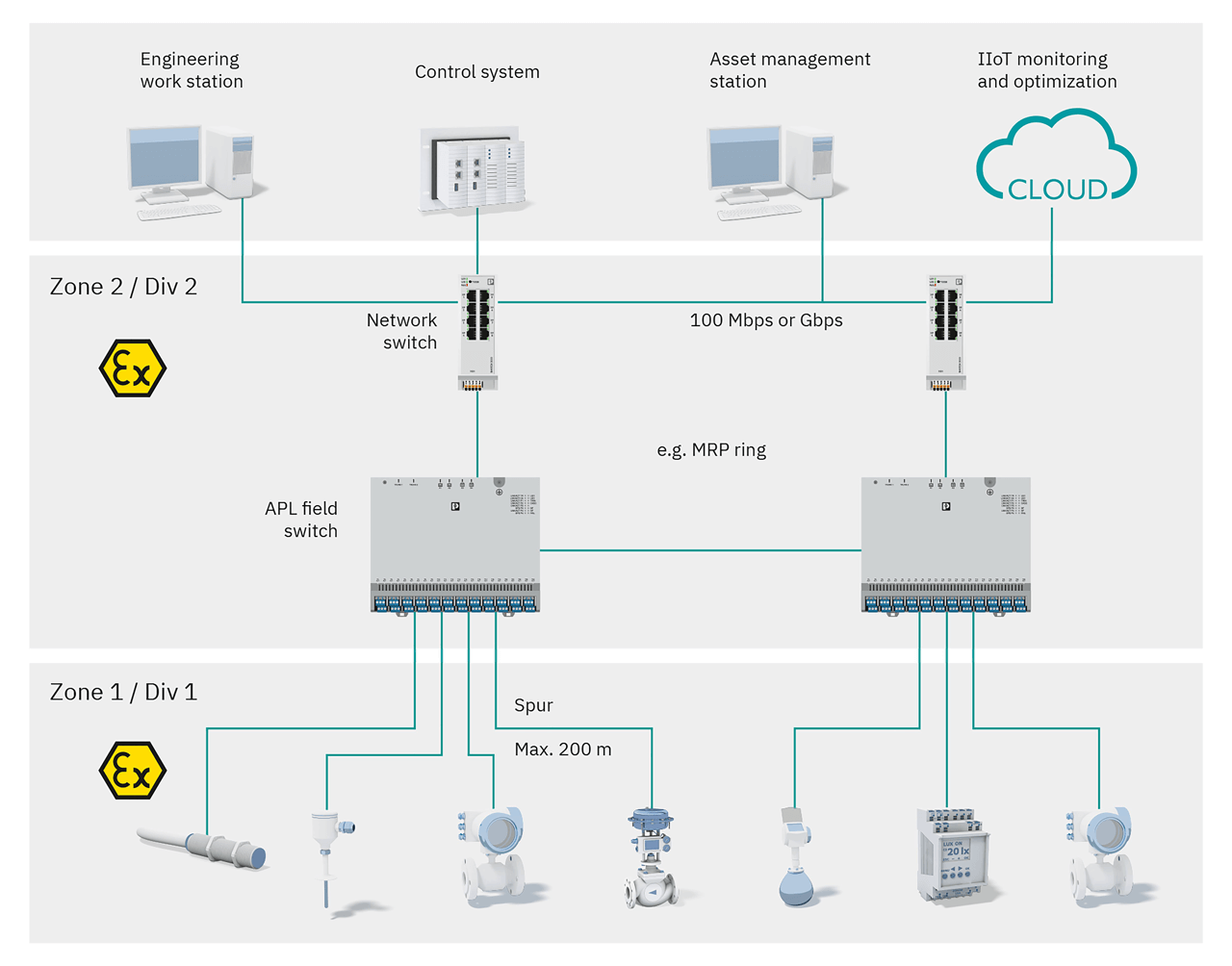
Figure 3: The Ethernet-APL topology offers redundancy, and Phoenix Contact offers managed switches, which share their heritage and functionality with the new 24-port APL field switch.
Where Ethernet-APL comes from
In June 2021, 12 well-known manufacturers in the process automation industry presented the first Ethernet-APL prototypes as part of the virtual ACHEMA Pulse event. This represented an exciting upgrade to the existing commercially available technology. Previously, the more complex process field devices required close to 10 minutes for device download, update, or programming scans when using HART. Similar Ethernet-APL field devices, however, could execute the same steps in mere seconds.
The transition of field devices running with serial communication to fully bidirectional digital solutions based on two-wire Ethernet was immediately evident. The market fully appreciates what this disruptive innovation can offer: improved access, accelerated efficiency, and optimized process plant capability.
However, more can be understood about the development of this unique technology. The “APL Project” team consists of the four influential standards development organizations (SDOs) involved in process automation: PI International (PROFINET), ODVA (EtherNet/IP), FieldComm Group (HART-IP), and OPC Foundation (OPC-UA). In addition, it also includes 12 leading manufacturers, who represent the combination of advanced process controllers, infrastructure switches, and best-in-class field devices required to build a working system.
The APL Project involves the collaboration of customer input, industry knowledge, and process safety site standards, coupled with global standards, laboratory testing, and third-party certification. In addition, the special PHY chips needed to develop the APL technology are now available from companies like Analog Devices and Texas Instruments.
Designed for industry, not the office
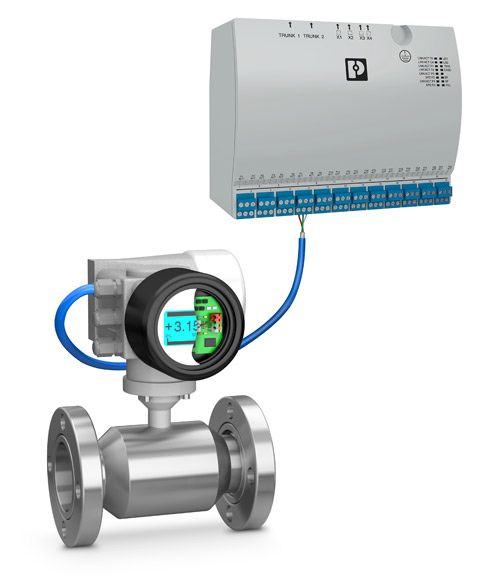
Figure 2: An example of an APL field switch from Phoenix Contact offers 200 meters of spur lines per APL field device and is particularly suitable for skid and modular system designs.
The enhancements and modifications to the original IEEE 802.3cg standard were application- and safety-related. The ubiquitous RJ45 works well in the office environment. However, a more rugged connector – like the one used for many decades in 4-20mA, HART, and Fieldbus installations – was chosen and is used on the port connections of both the APL switch and the field devices.
The voltage levels in the IEEE 802.3cg specification require more precise control of voltage, current, and total power in the loop. Even the capacitive, inductance, and resistive values must be defined and synchronized to ensure that no spark is ever present in a process automation application.
The energy limitations were already incorporated into prior Fieldbus standards and require a state-of-the-art protection method known as Intrinsic Safety. The result was the new IEC TS 60097-47 Technical Specification, with the working name of 2-Wire Intrinsically Safe Ethernet or 2-WISE.
Ethernet-APL promises to replace 4-20 mA technology in process automation in the coming years with its typical Industry 4.0 and Ethernet capabilities. A task force of manufacturers and end-users has already defined a dozen new projects that will use APL.
While the 4-20 mA signal only allows a single measurement value, the APL field device will provide multiple data sources for plant operators, increasing the efficiency and capabilities of projects and processes. In addition to maintenance personnel, process personnel will have equal access to the field devices to monitor the process with near real-time data.
As field devices become increasingly intelligent and powerful, there has been no sensible and practical way to quickly access the amount of information now possible. Industry insiders know that protocols such as HART, PROFIBUS PA, and FOUNDATION Fieldbus have promised “digital” capabilities but only at limited speeds.
Ethernet switches in the field
In the distribution cabinet, port connections on the switch are connected to spurs on the APL devices. So, as PROFIBUS PA devices are replaced with newer APL devices, the APL field switch offers a migration path from PROFIBUS PA to PROFINET APL devices. Here, the APL connection of 10 Mbits per second provides ten times faster access to internal data and process values of a comparable PROFIBUS PA device. There are field switches for use in modular units, such as skids and production lines in the pharmaceutical and food and beverage industries.
So, using fiber optics, a field switch can also be installed in processes where there is a significant distance between the controller and field devices. The 200-meter spur length per connection allows a lot of flexibility on the field device side.
Phoenix Contact is developing infrastructure components required for an APL network, such as the APL field switch. The first device to be launched is a 24-port APL field switch for Zone 2 installation. This first APL field switch therefore comes with four uplink ports – two copper, and two SFP fiber. Each of the 24 ports is an Ex ia (the most stringent) APL port with 200-meter (656-foot) length capability and the Power Class A of 540 mW, with a little more power available if needed.
With an integrated web-based manager, the switch’s 24 ports can support both APL and PROFIBUS PA field devices, and initial customer response has been extremely positive.
Since many of the APL device types are not yet available, initial projects will be based on a mix of APL and PROFIBUS PA devices. The PROFIBUS PA connection is only possible with a PROFINET controller on the uplink side.
Phoenix Contact launched its first managed switch product line almost two decades ago, and the latest generation – the FL 2000 managed switch – was introduced in 2018. This experience led to the development of the first Ethernet-APL switch, which shares this heritage and joins an extensive range of products.
The managed switch portfolio also includes an SPE switch as the entrée into both IEEE 802.3cg versions.
What’s next for Ethernet-APL?
ACHEMA, the world’s largest process automation show, will showcase many certified Ethernet-APL products in June 2024. The number of manufacturers now developing APL products has also expanded beyond the original 12. Users of the new technology should expect a portfolio of field devices (measurement and control), controllers, and infrastructure components such as power and field switches.
In addition, Ethernet-based process safety and cybersecurity will also be a part of the Ethernet-APL breadth of technologies moving forward.
For more information on the APL Project, a white paper is available at www.ethernet-apl.org.
For more information on the technology of Ethernet APL at Phoenix Contact, visit phoe.co/Ethernet-APL.
Arnold Offner, Strategic Marketing Manager – Automation Infrastructure, Phoenix Contact Development and Manufacturing, Inc.