TechnologyJuly 15, 2021
Ethernet-APL: the future of process automation connectivity
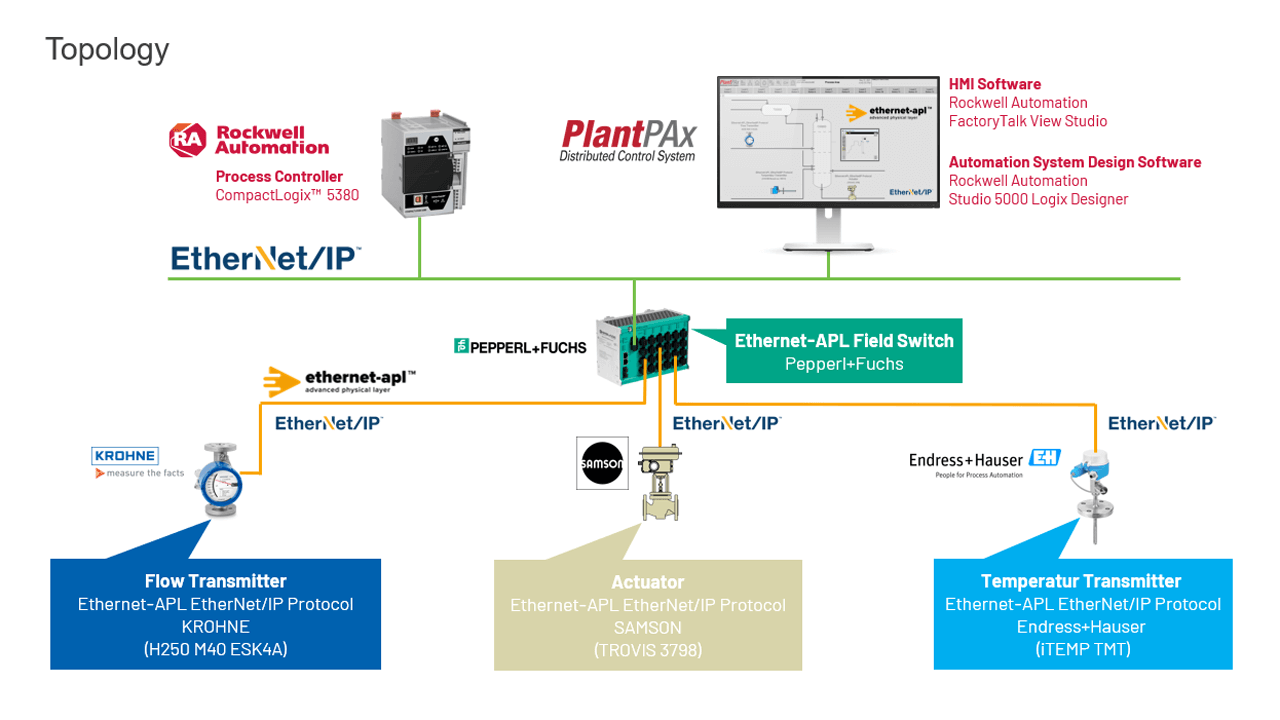
Competition and cost pressures combined with Industry 4.0 have made device health status, operations analytics and predictive maintenance via the device, edge and cloud more important than ever. The process industries are poised for a major shift, with Ethernet connecting directly to field devices via Ethernet-APL.
The reliability, security, and safety requirements of process industries that are driven by their critical infrastructure role along with high fixed plant costs have led to usage of dependable and proven control technologies such as 4-20ma for far longer than most other industrial sectors.
Some of the downsides to this approach are that field device commissioning takes minutes instead of seconds and there is a limited amount of process and diagnostic information available beyond critical process variables.
Process fieldbus solutions offered potential device status and remote commissioning possibilities, but were not adopted on a mass scale due to concerns about training, maintenance, reliability, and interoperability resulting in a very limited overall industry change and benefit to end users.
Ever-mounting competitive and cost pressures combined with technology advances via Industry 4.0 have made device health status, operations analytics and predictive maintenance via the device, edge, and cloud more important than ever. Process industries are poised for a major shift, and the time has come for Ethernet to connect directly to field devices with the launch of Ethernet-APL.
Ethernet-APL Overview
Ethernet-APL is a combination of Single Pair Ethernet (IEEE 802.3cg-2019, 10BASE-T1L), engineered power, Intrinsic Safety (IEC 60079, 2-WISE), and Type A fieldbus cable (IEC 61158-2, for intrinsic safety). As a result, Ethernet-APL satisfies the process industry needs for long reach cabling of up to 1,000 meters per trunk length, powered infrastructure and intrinsic safety protection for all Class 1 hazardous Zones and Divisions.
The use of 2-WISE to define intrinsic safety protection enables simple steps for verification of intrinsic safety without calculations, and 10BASE-T1L allows for dramatically increased speed at 10 Mbit/s.
As it is just a physical layer, Ethernet-APL allows end users to access standard safety and security services built on IEC 61508 and ISA/IEC 62443 from the leading industrial automation standards bodies.
Additionally, Ethernet-APL will be able to support EtherNet/IPTM, HART-IP, OPC UA, PROFINET, or any other higher-level network protocol. In summary, Ethernet-APL allows Ethernet to seamlessly extend from the field instrumentation to the plant process automation system to higher level enterprise resource planning systems and cloud environments, thereby reducing gateways.
Ethernet-APL technology launch
“The APL Project” is made up of standards development organizations FieldComm Group, ODVA, OPC Foundation, and PROFIBUS & PROFINET International (PI), and 12 major industrial project members. After three years of successful cooperation, the APL Project launched the Ethernet-APL technology at the ACHEMA Pulse digital fair on June 15th, 2021.
The technology launch included the release of specifications, engineering guidelines and conformance test plans. The launch also includes defined port profiles that create the Ethernet-APL concept for multiple power levels with and without explosion hazardous area protection and standardized product marking.
Next steps include release of field devices from companies with initial products now available from select vendors. Ethernet-APL value was demonstrated during ACHEMA via a multivendor demonstration showing participation across different product vendors and industrial protocols, highlighting the options and interoperability Ethernet-APL offers end users.
Next steps for Ethernet-APL
It’s likely that hybrid industries such as pharmaceutical or food and beverage will be early adopters of Ethernet-APL technology to take advantage of the significantly enhanced data visibility of field devices for use cases where field devices are significantly spread out requiring long cable lengths or are located in hazardous environments.
Traditional process industries will likely follow with adoption once the concept is proven via technology demonstrators, industry pilots, and internal testing. Process end users will gain the most value from adoption as the increased speed will enable advanced analytics, predictive maintenance, and enhanced operational management. The long cable length and intrinsic safety capability will make it possible for Ethernet to become the standard field device solution.
Additionally, process companies can potentially re-use existing installed Type A fieldbus cable that meets the resistance standards of 100 ohms with +/- 20 ohms tolerance for Ethernet-APL. The ability to potentially re-use Type A fieldbus cable and to have both power and communication on the same cable can allow for significant cost savings due to not having to run new cable.
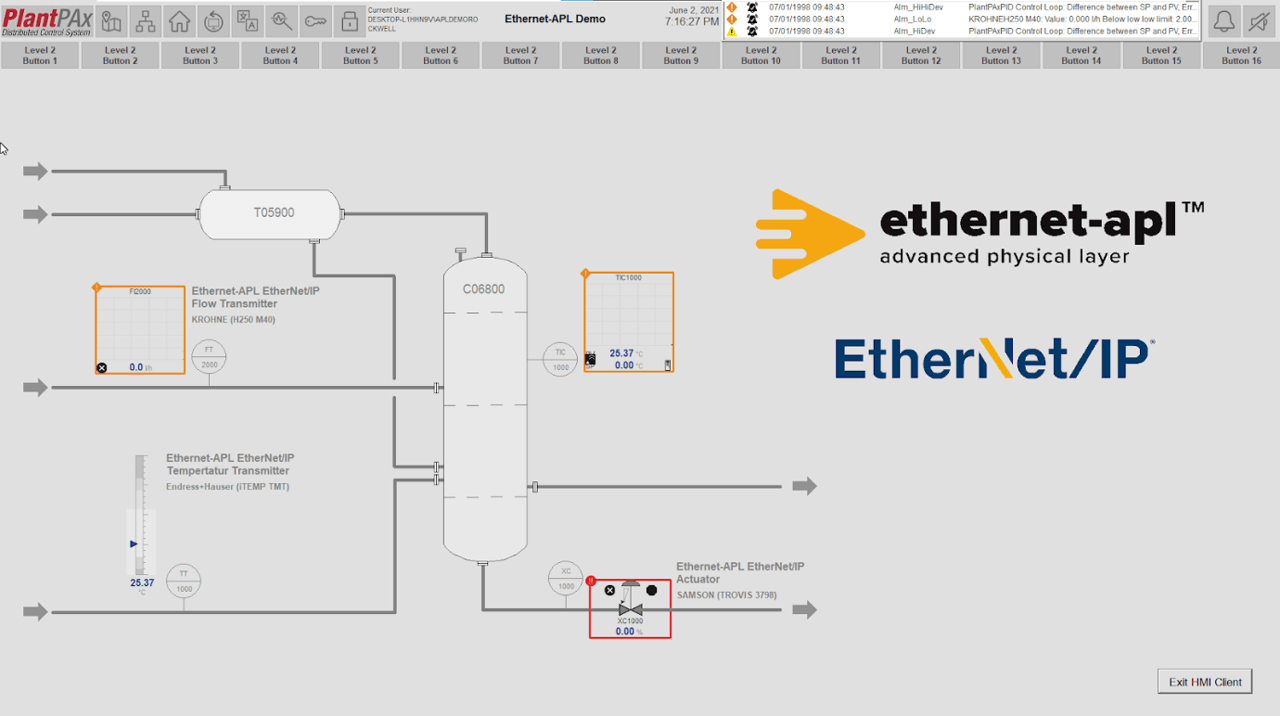
EtherNet/IP Network HMI Client – Operator Display.
EtherNet/IP and Ethernet-APL
EtherNet/IP communication networks will be able to utilize the Ethernet-APL physical layer in process plants, which will unlock the advantages of commercially based industrial control hardware, an object-oriented foundation, and standard internet protocol compatibility including TCP/IP, HTTP, FTP, SNMP, and DHCP.
The first Ethernet-APL infrastructure and field devices that support EtherNet/IP are expected to be available in 2021. Continuous enhancements to EtherNet/IP are both planned and underway to meet future industrial communication and control needs across discrete, hybrid and process applications. Recent EtherNet/IP process enhancements include the addition of NE 107 diagnostics, HART integration, IO-Link integration, and device description enhancements.
With EtherNet/IP, NAMUR NE 107 diagnostic information can be easily transported to a DCS for an operator’s review or to an edge device mapping for predictive maintenance. Seamless information sharing with broad usage of EtherNet/IP in process automation, even better than what is now possible between HART and EtherNet/IP and between IO-Link and EtherNet/IP devices, will enable a more efficient and interconnected infrastructure. ODVA is continuing to expand the EtherNet/IP ecosystem with the next generation of digitized device description files, including FDT, FDI, and xDS, to simplify integration into process asset management tools. The end goals of the device description efforts are to provide a standard, robust and detailed description of device information, implement secure device description artifacts, and prepare for a future driven by Industry 4.0 and the industrial IoT.
IEEE Ethernet standard compliance provides users with a choice of network interface speeds — e.g., 10, 100 Mbit/s, 1 Gbit/s and beyond, installation options including copper, fiber, fiber ring and wireless, and topologies including star, linear and ring. EtherNet/IP provides support for functional safety with CIP Safety™, device defense with CIP Security™, with parallel redundancy protocol (PRP) and Device Level Ring (DLR) for fault tolerant redundancy. ODVA is committed to ensuring that EtherNet/IP meets all requirements of Industry 4.0 and IIoT.
EtherNet/IP is a proven industrial automation network that is multivendor interoperable, and highly standardized. Ethernet-APL along with process specific enhancements will open the door to the advantages of EtherNet/IP within process automation for network and device health monitoring, built in security and safety, and remote device configuration.
Ethernet-APL value for end users
Ethernet-APL will open the door to widespread use of industrial Ethernet in process automation. Process end users can now leverage Ethernet-APL as a single Ethernet physical layer for long distance field devices, intrinsic safety, and application-layer industrial protocol support to optimize production while maintaining the safety, security, and ease of use from prior solutions.
Additionally, usage of gateways will be significantly reduced. Conformance tested products will be released soon to enable the start of the Ethernet to the field revolution in process plants. Ethernet-APL offers new possibilities including enhanced remote commissioning, asset management, control, analytics, and diagnostics/prognostics, which will help drive adoption of this new technology. It’s not hyperbole to say that Ethernet-APL is the future of process automation given that it meets the requirements of the process industry, including enabling the NAMUR Open Architecture (NOA) second channel.