TechnologyJanuary 23, 2022
Flexible, productive, sustainable smart manufacturing
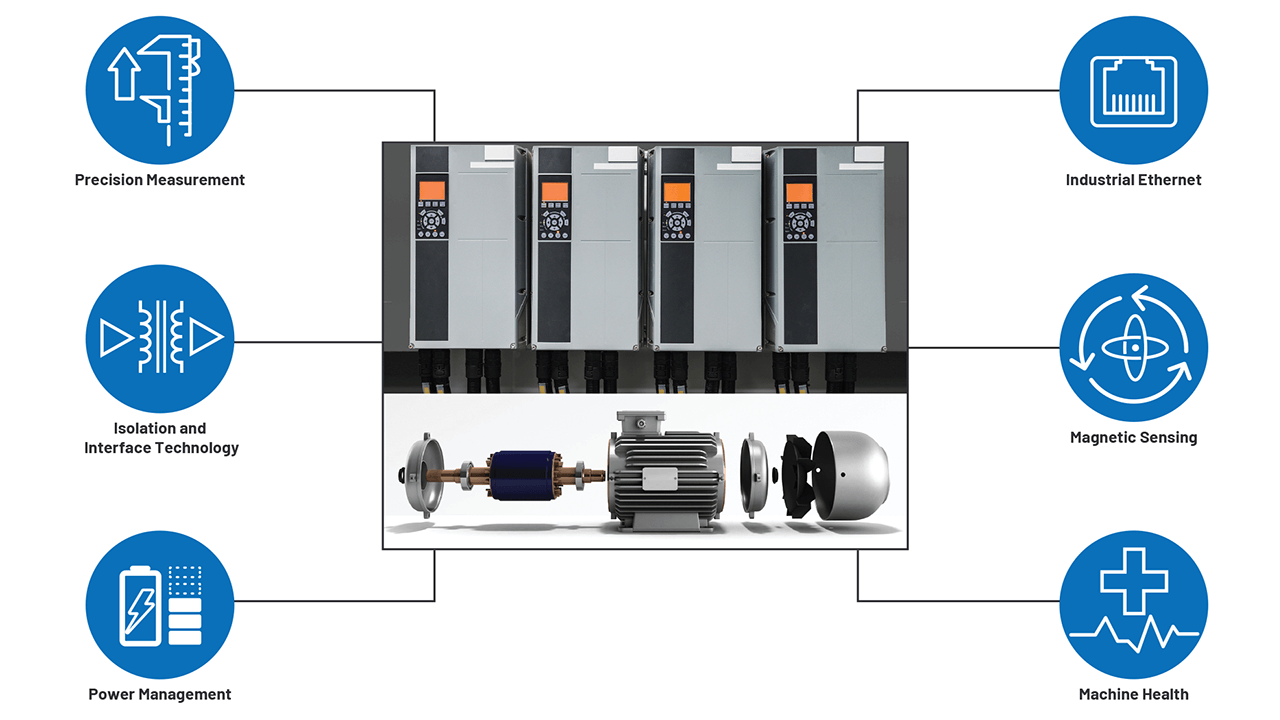
Smart manufacturing using intelligent motion control supports more agile and scalable manufacturing, including batch size 1 production. By optimizing the manufacturing flow for higher throughput, less energy is consumed resulting in more sustainable smart manufacturing.
Intelligent motion control is the core building block of smart manufacturing, enabling highly flexible and efficient manufacturing. Intelligent motion control combines precision feedback, advanced sensing, high performance control, and seamless connectivity to deliver deterministic motion solutions.
Seamless connectivity of motion insights to PLCs and manufacturing execution systems (MES) allows advanced analytics to optimize manufacturing flows and identify potential issues before production stops.
Smart manufacturing using intelligent motion control can be reconfigured quickly to support more agile and scalable manufacturing, including batch size 1 production. By reducing the time to complete a manufacturing step and optimizing the manufacturing flow for higher throughput, less energy is consumed resulting in more sustainable smart manufacturing. Intelligent motion applications include: pumps, fans, hoists, VAC, conveyors, winding, printing, extrusion, machining, robotics, pick and place, handling, and many others.
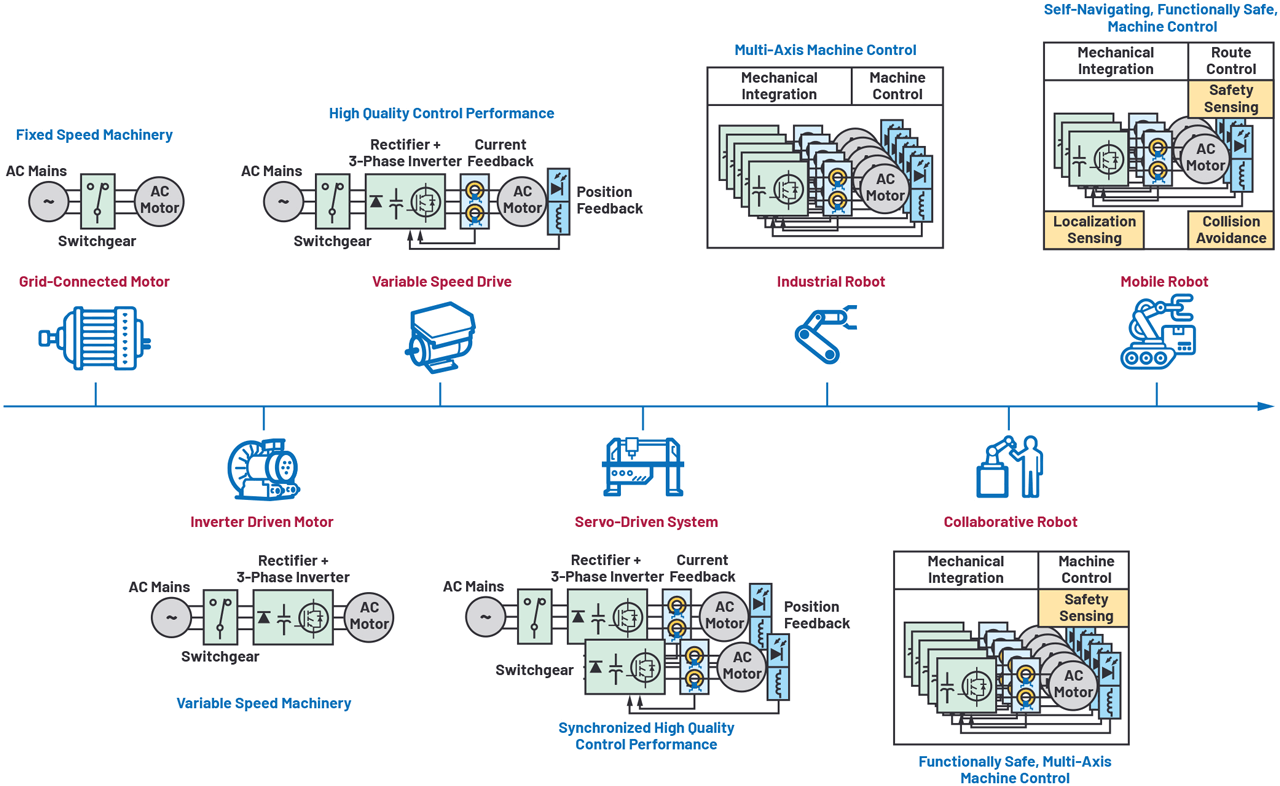
The evolution of intelligent, connected motion applications.
Intelligent motion solutions
Motion control has evolved over time, from simple grid connected motors to complex multi-axis servo drive solutions for machine tools and industrial robots. This evolution has been accelerated by the increasing complexity of automation required to deliver higher levels of productivity, flexibility, and autonomy in smart manufacturing.
Grid-connected motors
The most basic motion solutions are based on a grid-connected or AC-powered, 3-phase fixed speed motor that uses a switchgear to provide on/off control and protection circuitry. These basic motion solutions run at a relatively fixed speed, independent of any load variation. A reduction in output is implemented with mechanical controls—throttles, dampers, gears or valves, pumps, and fans are some typical asset examples.
Inverter-driven motors
The addition of a rectifier, DC bus, and a 3-phase inverter stage in effect creates a variable frequency and variable voltage source that is now applied to the motor to enable variable speed control.
This inverter driven motor enables significant reduction in energy consumption by running the motor at the optimum speed for the load and application. Examples include higher efficiency pumps and fans.
Variable speed drives
For higher performance motion control applications, a variable speed drive (VSD) enables accurate torque, velocity, and position control. To achieve this, current and position measurement are added into the basic open-loop inverter drive. More precise control of motor velocity, position, and torque is then possible. Conveyors, winding, printing, and extrusion machinery are typical examples of these applications.
Servo-driven systems
Synchronized, multi-axis servo-driven systems are used in more complex motion applications. Machine tools and CNC machines require synchronization of multiple axes, with extremely accurate position feedback. In CNC machining, 5-axis coordination is common, although there are applications that utilize up to 12 axes in which tools and workpieces are both being moved with respect to each other in space.
Collaborative and mobile robots
Industrial robots require multi-axis servo drives combined with mechanical integration and advanced machine control algorithms to achieve complex 3D spatial positioning. Robots typically have six axes that need to be controlled in a coordinated manner, and sometimes seven if the robot is moving along a rail.
Collaborative robots (cobots) build on industrial robotic solutions by adding power and force limiting (PFL) to deliver functionally safe, multi-axis machine control where an operator can work safely alongside the cobot. Finally, self-navigating, functionally safe machine control is deployed in mobile robots, with localization sensing and collision avoidance.
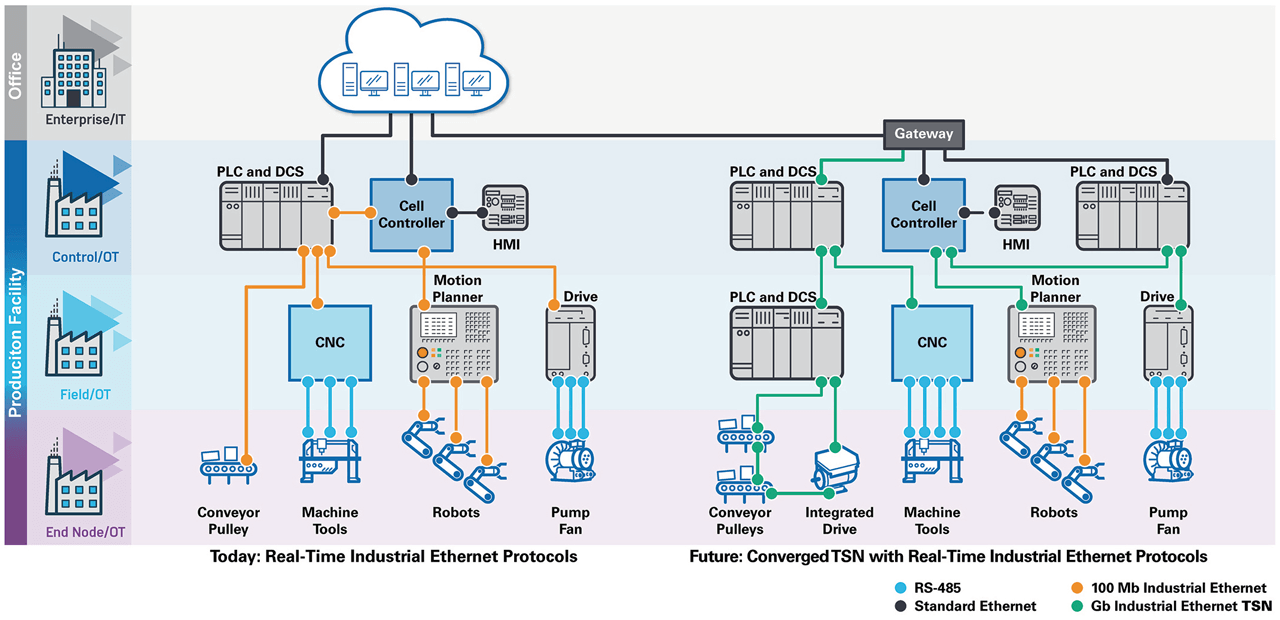
Digital transformation is being enabled by seamless Industrial Ethernet connectivity.
Intelligent motion growth drivers
Intelligent motion control is being accelerated by four key growth drivers: reduced energy consumption, agile production, digital transformation, and the move toward new service-based business models based on reducing downtime and increasing asset utilization in smart manufacturing. Let’s look at each of these four key growth drivers in detail.
Reduced energy consumption
Almost 70% of electricity consumed by industry is used by electric motor systems. Intelligent motion solutions are delivering and will continue to deliver significant reductions in energy consumption by moving more applications from fixed speed motors to high efficiency motors and variable speed drives, in part driven by energy efficiency regulations. This reduction in energy consumption will enable more sustainable manufacturing. Access to motion insights that optimize a manufacturing flow will further reduce energy consumption in smart manufacturing.
Agile production
As industries are adapting to keep up with consumer demand and changing buyer behaviors, agile production, based on reconfigurable production lines, is required to deliver more customization and faster turn-around times. Consumer demand is driving a shift away from low mix, high volume manufacturing toward high mix, low volume manufacturing, which demands greater flexibility on the factory floor.
Complex, repetitive, and often dangerous tasks can now be performed by industrial robots, leading to higher throughput and increased productivity. Agile production increases resilience in a time of disruption and enables a faster response to changing customer demands.
Digital transformation
Global spending on digital transformation will reach $6.8 trillion globally by 2023.2 Variable speed drives and servo drives use data from voltages, currents, position, temperature, power, energy consumption combined with external sensors for monitoring vibration, and other process variables. With a converged information technology/operating technology (IT/OT) Ethernet network, motion applications are networked together communicating data and insights. Motion data and insights are now more accessible and can be analyzed by powerful cloud computing and AI to optimize manufacturing flows and monitor the current state of health of the assets across the entire installation.
Business models for deployed assets
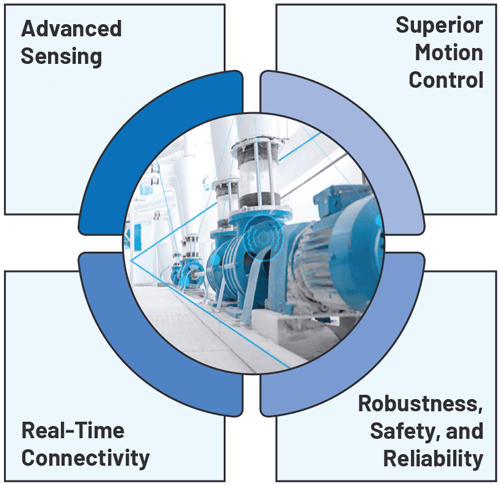
Intelligent motion requirements.
Asset manufacturers are looking to sell more than just assets—they want to expand their business models to include post-sales services contracts based on productivity and asset utilization. For example, a pump manufacturer wants to use new predictive maintenance service offerings to sell based on volume of liquid (for example, water or fuel) pumped and charge based on per cubic meter (m3) pumped rather than just sell pumps. 50% to 60% of the revenue of pump OEMs is expected to be generated from services-related activities in the next five years.
System integrators want to charge based on the uptime of the manufacturing capability they installed and not just charge based on the initial installation of the assets. New intelligent motion solutions are integrating condition monitoring capabilities to implement real-time monitoring of the assets’ health to plan maintenance schedules. This monitoring can eliminate unplanned asset downtime to deliver higher levels of productivity and asset utilization, which are the cornerstones of the new service-based contracts.
Intelligent motion requirements
To enable higher levels of productivity and sustainability in smart manufacturing, new advanced motion control solutions are required to deliver the benefits of the four growth drives outlined.
Superior motion control
Superior motion control reduces the time it takes to complete a manufacturing step, thereby increasing throughput and manufacturing productivity while reducing energy consumption. Examples include precise position and torque control for higher quality and faster machining, such as by reducing the number of steps and time to machine a complex component. The key requirements to deliver superior motion control include improved control loop performance, robust solutions for harsh industrial deployments, and high levels of integration to enable high reliability, small form factor solutions. These are in turn enabled by low latency, low drift, multiphase current and position sensing and signal chains with high transient robustness and highly integrated components.
Robustness, safety and reliability
Robust, reliable solutions that extend assets’ usable lifetimes are key to more sustainable smart manufacturing. By extending asset lifetimes, we significantly reduce the consumption of raw material and energy to build replacement assets.
Power management solutions for both power regulation and power protection are key components to deliver more robust and reliable assets. Power management requirements include high-side power supplies for insulated gate bipolar transistors (IGBTs), high power density solutions for FPGA and processors, digital point of load (PoL) for power management telemetry, EMC robustness, high ambient temperature operation, and data and power isolation to protect users from high voltages.
Reliable use of new wide band gap power switches (made from silicon carbide (SiC) and gallium nitride (GaN)) puts new challenges and requirements to provide fast overcurrent protected systems and robust operation.
Real-time connectivity
In high performance, multi-axis, synchronized motion applications, control timing requirements are precise, deterministic, and time critical, with a requirement to minimize end-to-end latency, especially as control cycle times get shorter and control algorithm complexity increases. These high performance applications require real-time connectivity with sub-ms network cycle time to control complex motion applications.
Smart manufacturing uses vision systems alongside motion applications to monitor manufacturing quality and increase production safety. Industrial Ethernet networks must support the coexistence of both real-time deterministic motion control traffic and best-effort vision traffic on the same network up to Gb bandwidth.
The interoperability of devices and controllers connected to the networks is required to deliver seamless data flow throughout the manufacturing installation and ensures data transparency to the higher-level management systems while making these networks more flexible and scalable by reducing commissioning time. A converged (IT/OT) Ethernet network ensures seamless access of motion insights to the higher-level management software systems, for analysis, to optimize the manufacturing flow and accelerate digital transformation.
Advanced sensing
Advanced sensing solutions create motion insights that can be used to optimize the manufacturing flow and detect early signs of failure. Sensing modalities include position, current, voltage, magnetic field, temperature, vibration, and shock. New business models are being created by using advanced sensing to deploy real-time monitoring of an asset’s health to provide predictive maintenance services contracts based on increasing asset uptime. Advanced sensing requirements include robustness in harsh industrial environments (for example, those with a lot of dust), accurate position sensing, contactless high current sensing, high bandwidth current and vibration sensing, reduced calibration to ensure accuracy of the solutions, and small solution sizes for encoder type applications.
Technologies to accelerate higher value motion control solutions
A combination of technologies is required for the next generation of intelligent motion control solutions for smart manufacturing. These technologies when combined deliver robust, precise motion control for harsh industrial deployments with access to system insights from advanced sensing.
Precision measurement
Complex motion control requires precision converter technologies for high quality current feedback utilizing both isolated and non-isolated solutions to provide control loop performance that is both highly accurate and has fast transient response. Current feedback is the fundamental building block to enhancing drive performance and determines the overall control bandwidth and response time. Key requirements for current feedback include synchronized measurement with PWM cycle, isolated or high common-mode measurement, low offset drift to minimize torque ripple, and low latency simultaneous sampling at 14- to 18-bit resolution to measure phase currents. Precision converter technologies are also required for accurate position measurements in encoders and linear track applications that can deliver greater throughput and increase productivity.
Isolation and interface
Next-generation drives and motors that enable complex motion control require digital isolation technology to provide isolated data and isolated communications interfaces such as RS-485, USB, and LVDS. Isolated gate drivers are also needed to drive high- and low-side power semiconductors to provide robust, safety compliant, and high reliability assets.
Gate drivers convert the logic-level PWM signals to high-side referenced signals that control power transistors. High voltage inverter applications often use IGBTs, with a future trend toward SiC and GaN to increase switching frequency and/or lower switching losses. Low voltage applications typically use MOSFET-based switches.
The key requirements for gate drivers include high speed, low propagation delay, low delay skew, robustness and common-mode transient immunity, switch protection features (DESAT, Miller clamp, soft shutdown, UVLO), and controllable switching (variable slew rate switching).
Standard digital isolators play a role in many drives in transferring signals between high voltage power electronics domains and safety extra low voltage (SELV) domains for PWM and other signaling. Examples include isolated signaling for integrated power modules (IPM). Fully integrated isolated power solutions can also be combined with digital isolators or other isolated functions to provide significant solution size reduction compared to a discrete transformer solution.
Industrial Ethernet
Industrial Ethernet connectivity with sub-ms cycle times network performance is required for deterministic real-time communication in motion control applications (servos and drives). Robust physical layer devices at 100 Mb and Gb speeds combined with layer 2 Industrial Ethernet protocols such as EtherCAT, PROFINET, EtherNET/IP, and IEEE time sensitive networking (TSN) ensure deterministic Ethernet connectivity.
Next-generation designs are moving to Gb TSN on converged networks with multiple traffic types, cyclic communications for control, and acyclic communications for best effort traffic (for example, vision and monitoring traffic). Low latency Industrial Ethernet solutions are required to reduce cycle times in multi-axis applications. These deterministic motion solutions enable more complex motion applications that drive higher levels of manufacturing productivity and flexibility.
Magnetic sensing
Magnetic sensing based on anisotropic magnetoresistance (AMR) position sensor solutions enables robust and accurate position sensing for encoder applications. Position feedback is used for direct position control or for inferring rotational speed and implementing machine speed control in servo drives. Magnetic sensing provides a lower cost solution compared to optical encoders and a more robust solution in industrial applications that are subject to dust and vibration.
Power management
Intelligent motion applications are typically deployed in harsh industrial environments where high ambient temperature operation is required, along with immunity to conducted noise and high voltage transients. In some decentralized applications, drives are located closer to the motor in smaller enclosures and, in other applications, the drive is integrated with the motor. Higher power density power management solutions that operate at high ambient temperatures are required to enable these smaller form factor intelligent motion applications.
Machine health
Machine health uses vibration and shock sensors to enable real-time condition monitoring of an asset’s health to eliminate unplanned downtime, extending the asset’s useable lifetime while also reducing maintenance costs. By integrating machine health into motion applications, new revenue streams can be generated though digitization strategies that create new service-based business models based on guaranteed uptime to enable higher levels of manufacturing productivity. Asset health data based on vibration, shock, and temperature is transformed into asset health insights by edge AI, which are then communicated via wired or wireless solutions to the management control software where they provide real-time state of health of key assets.
Conclusion
Agile production is required to quickly respond to changing consumer demands and support efficient production, down to a batch size of 1. Agile production is enabled by intelligent, connected assets that can be reconfigured quickly. These connected assets share data in real time; this data is used to improve operational performance by identifying bottle necks in production and by monitoring the health of assets to eliminate unplanned downtime.
Smart manufacturing that is built on intelligent motion solutions consumes less energy and enables more complex motion to drive higher levels of flexibility, productivity, and sustainability.
Intelligent motion control solutions
Analog Devices technologies and system-level solutions for intelligent motion applications are enabling higher levels of performance while reducing energy consumption and downtime. A typical motor drive signal chain is comprised of six key blocks.
Power electronics
Power electronics provide the power conversion in a motor drive system. For high voltage systems (>100 V), an isolated gate driver is used to drive the power semiconductors. ADuM4122 is a single-gate isolated gate driver with 3 A short circuit (<3 Ω). It supports functional or reinforced isolation up to ~800 V DC bus with slew rate control for EMI/power loss optimization.
It also supports high common-mode transient immunity (CMTI) and low propagation delay for use with SiC and GaN power semiconductors.
ADuM160N multichannel digital isolators can be used to isolate PWM signals for use with integrated power modules (IPM) that integrate the gate driver with the power semiconductor. The ADuM6028 isolated power device can be used in conjunction with digital isolators, isolated transceivers, and isolated data converters to provide a very small 8-lead solution that is fully safety certified and ready to use.
For low voltage systems (<100 V), the LTC7060, a 100 V half-bridge driver with floating grounds and programmable dead time or the LTC7000, a 150 V protected high-side NMOS static switch driver with PassThru technology and adaptive shoot-through protection can be used to drive low voltage semiconductors.
LTC7000 also supports programmable dead time for efficiency optimization, enhanced current control, and slew rate control for EMI reduction.
Current Sense
For isolated current sense measurement, the ADuM7701 is a high performance, second-order, sigma-delta modulator that converts an analog input signal into a high speed, single-bit data stream with on-chip digital isolation based on Analog Devices iCoupler® technology.
ADuM7703’s low offset drift (0.6 μV/°C max) reduces torque ripple and is packaged in a compact 8-lead package with integrated LDO to simplify power supply design and reduce board area. Its 150 V/ns min CMTI rating enables use with GaN and SiC power electronics.
AD8410 high voltage, current sense amplifiers provide a high gain (20 V/V, 50 V/V, 100 V/V) and low offset drift (~1 μV/°C) with high bandwidth (2 MHz) for optimum current control. AD8410 also includes bidirectional current measurement input up to 100 V common-mode input. The LTC6102 precision zero-drift current sense amplifier ensures accuracy across a wide range of operating conditions and can be powered from high-side voltages up to 100 V in shunt-based current sensing applications.
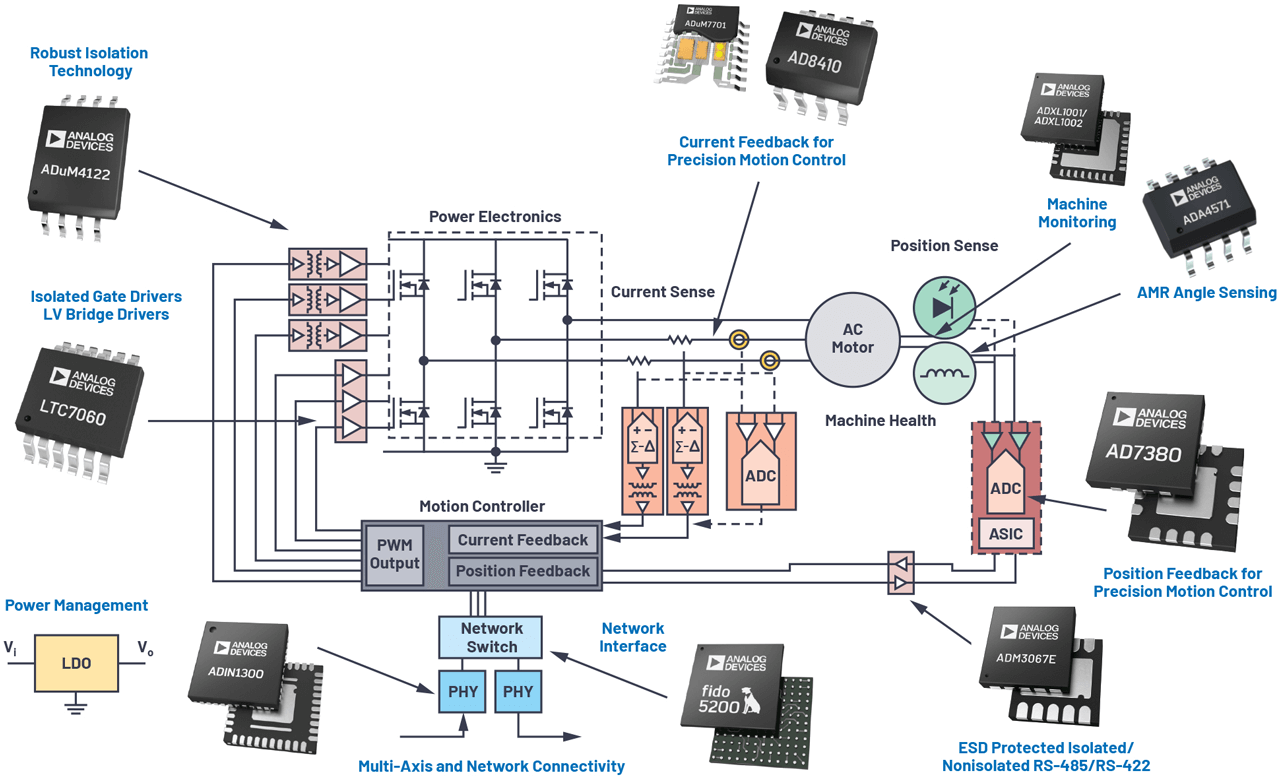
Analog Devices solutions for intelligent motion applications.
Position sense
Position feedback is used for direct position control or for inferring rotational speed and implementing machine speed control. ADA4570 and ADA4571 integrated AMR angle sensors with integrated signal conditioners enable higher absolute accuracy position sensing for motor drive and servo applications (<0.1° error, <0.5° over life/temperature).
They are robust in magnetically harsh environments, support wide air gap tolerances without degradation of angular error (unlike Hall/GMR/TMR), and simplify system design considerations.
The ADA4570 and ADA4571 are not affected by dust or dirt when compared with optical sensors in industrial applications, and they have very low latency compared to digital output solutions on the market with built-in calibration engines.
ADA4571 produces two single-ended analog outputs (sine and cosine) that indicate the angular position of the surrounding magnetic field, while the ADA4570 produces two differential analog output pairs. A dual version of the ADA4571 (ADA4571-2) is also available where full redundancy is needed in safety critical applications.
The AD7380 is a 4 MSPS dual simultaneous sampling, 16-bit SAR ADC that provides precision, throughput, and minimal size for encoder applications. AD7380 is in a small package size (3 mm × 3 mm) for miniaturization of the encoder with 4 MSPS throughput for minimal latency and fast control loop transient response. The AD7380 oversampling engine allows higher accuracy for slower operating conditions.
Machine health
Vibration and shock sensors are being integrated into the encoder or the motor to provide asset health insights. The ADXL1002 ultralow noise (25 μg/√Hz in ±50 g range), high frequency, ±50 g MEMS accelerometer provides high data bandwidth vibration sensing up to 11 kHz (3 dB point) with a resonant frequency of 21 kHz. ADXL1002 provides a lower cost and lower power alternative to piezoelectric sensors.
ADXL1002 enables monitoring of slow rotating equipment down to DC while also reducing calibration requirements when compared to piezo sensors. ADXL354 is a low noise, low power, 3-axis MEMS accelerometer in a small (3 mm × 5 mm) package with a digital interface, SPI (3- and 4-wire), and I2C to provide a compact solution for vibration sensing integration in encoders.
The ADI OtoSense Smart Motor Sensor is an AI-based, full turnkey hardware and software solution for condition monitoring of electric motors, combining best-in-class sensing technologies with leading-edge data analysis. Agnostic of motor type, ADI OtoSense SMS covers the most critical diagnostics, translating data into actionable insight that enables you to forecast maintenance cycles and avoid unplanned downtime.
Network interface
Smart manufacturing is based on a network of intelligent motion applications sharing data between the assets and the higher-level control and management network. ADI’s robust, low power, and low latency PHYs include the ADIN1200 (10/100) PHY and the ADIN1300 (10/100/1000) PHY. Both these Industrial Ethernet PHYs were developed for industrial applications that require operating ambient temperature up to 105°C and have been extensively tested to EMC and robustness standards to operate in harsh industrial applications.
Low latency PHYs enable a lower cycle time network that can support more devices connected to the network and meet the timing requirements for complex, high performance deterministic motion applications. For deterministic Industrial Ethernet connectivity, ADI’s layer 2 Industrial Ethernet embedded 2-port switches. fido5100 and fido5200 support PROFINET, Ethernet/IP, EtherCAT, Modbus TCP, and Ethernet POWERLINK Industrial Ethernet protocols with any processor, any protocol, any stack.
Motion controller
The motion controller provides the processing engine to generates the PWM signals to drive the power semiconductors and receives the current and position feedback signals to control the motors speed and torque. Robust, high ambient, high power density power management solutions are required to power the controller, which is often an FPGA or a processor with optional power supply sequencing and power telemetry capabilities. Analog Devices’ Power by Linear power management ICs and power modules provide the foundation for powering today’s and tomorrow’s intelligent motion applications.
The motion controller is often located in a central rack that needs to communicate over a large distance to the encoder. This is where ADI’s isolated and non-isolated RS-485 transceivers are used for serial communication of the encoder position feedback information to the motion controller. The ADM3066E, a ±12 kV IEC ESD protected, full-duplex 50 Mbps RS-485 transceiver, provides a high bandwidth, high ambient (125°C), robust communications solution in a small 3 mm × 3 mm package size for encoder applications.