TechnologyJuly 18, 2025
IEB Special Report: industrial remote connectivity solutions
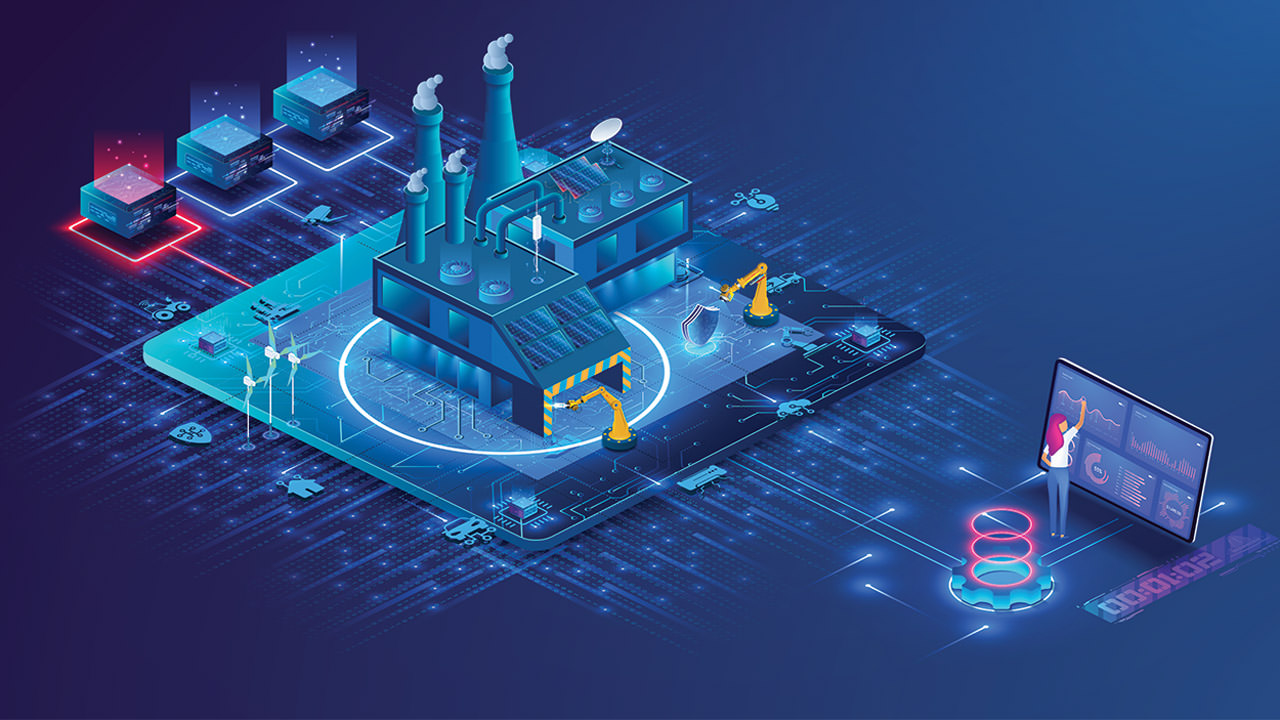
Industrial remote connectivity solutions enable machine builders and users to securely access industrial equipment from any location. These solutions facilitate seamless and secure Industrial Internet of Things (IIoT) functionality, allowing for remote maintenance, troubleshooting, and machine data visualization.
Industrial remote connectivity solutions enable secure access and management of industrial equipment and operations from remote locations, enhancing efficiency, reducing downtime, and improving safety.
Remote access enables quick troubleshooting and maintenance, minimizing production interruptions, and eliminates the need for on-site visits, saving travel expenses and time. Remote access allows personnel to operate and monitor equipment from a safe distance, particularly in hazardous environments.
For this special report, the Industrial Ethernet Book reached out to leading companies involved in developing remote connectivity solutions, asking them to discuss an Industrial Remote Connectivity technology solution they provide, and the specific technical benefits that this approach offers.
Reliable connectivity solutions
Robust industrial routing addresses evolving needs of modern industries.
“One key advantage of Cisco’s industrial routers is their modular design, featuring pluggable modules that allow businesses to adapt to varying connectivity requirements,” Emily Kasman, Industrial Security Product Marketing Specialist at Cisco told IEB recently. “Whether a location relies on 4G, 5G, fiber, or other technologies, Cisco’s portfolio provides the flexibility to support diverse backhaul options. Moreover, these backhaul options can be changed or upgraded over time without replacing the entire router, ensuring the ability to meet evolving needs and technology changes with unmatched long-term cost efficiency.”
Kasman added that Cisco’s industrial routers also serve as a unified platform, for both connectivity and cybersecurity. They embed comprehensive security capability including next generation firewalls (NGFW), OT visibility, ZTNA remote access and more, eliminating the need to source dedicated products for each function, simplifying deployments and reducing operational complexity. Combined with Cisco’s SD-WAN solution, organizations can centralize management, automate configurations, and enforce consistent security policies across the network.
“With these capabilities, Cisco delivers WAN infrastructure that is easy to manage, evolves with business needs, and supports a wide variety of connectivity scenarios, enabling cyber-resilient and efficient operations across industrial environments,” Kasman said.
Cisco is a global leader in IT networking, offering purpose-built rugged hardware specifically designed for the unique demands of Operational Technology (OT) environments. Cisco delivers secure, high-performance networking that withstands extreme conditions while enabling seamless IT and OT integration. Cisco’s industrial switches and routers are trusted worldwide for their reliability, advanced security features, and comprehensive management capabilities. Cisco’s industrial remote connectivity solution leverages its robust industrial routing portfolio to address the evolving needs of modern industries. Field assets in remote or challenging locations require reliable and secure connectivity, and Cisco’s routers are designed to meet this demand while simplifying network management.
Technology trends
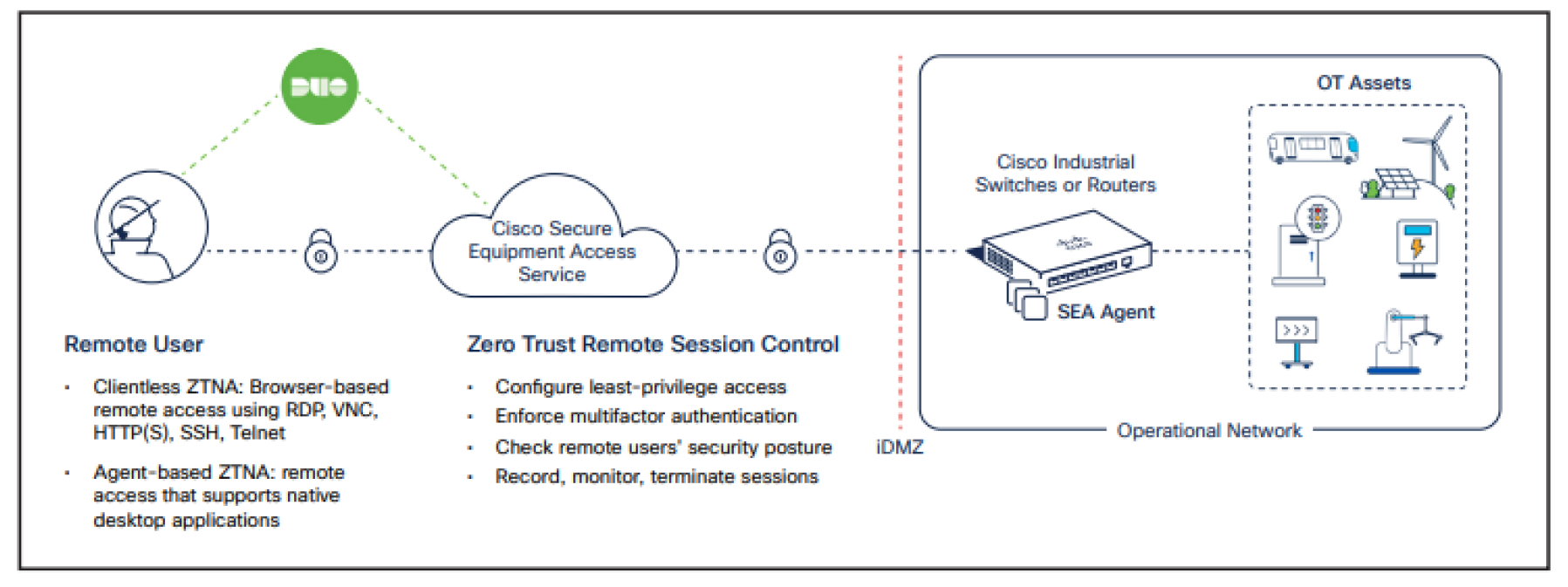
“The latest solutions for Industrial Remote Connectivity are driven by innovations that focus on simplifying infrastructure, enhancing security, and enabling centralized management, especially as there is exponential growth in new industrial assets coming online. Cisco industrial routers exemplify these trends by providing a modular, secure, all-in-one platform that consolidates multiple networking functions into a single device,” — Emily Kasman, Industrial Security Product Marketing Specialist, Cisco.
Kasman said that the latest solutions for Industrial Remote Connectivity are driven by innovations that focus on simplifying infrastructure, enhancing security, and enabling centralized management, especially as there is exponential growth in new industrial assets coming online. Cisco industrial routers exemplify these trends by providing a modular, secure, all-in-one platform that consolidates multiple networking functions into a single device. This eliminates the need to source and deploy separate products for each function, saving costs and valuable space in industrial environments.
“With embedded cyber resilience and modular, future-ready connectivity, Cisco industrial routers enable you to connect and manage all your remote industrial assets and build a secure WAN infrastructure, even in harsh environments. Because they use the same technologies and management platform than Cisco’s enterprise networking solutions, they allow organizations to use existing skills and unify networking and security across IT and OT environments,” she added.
As industries generate massive amounts of data at remote sites and production facilities, the need for edge computing has never been greater. Processing data closer to its source reduces latency, minimizes bandwidth usage, and enables faster, smarter decision-making where it matters most.
Cisco addresses this need with Edge Intelligence running on its industrial routers, allowing businesses to securely collect, process, and act on data at the edge in real time. Beyond Edge Intelligence, Cisco’s industrial routers support a wide range of applications, including remote asset management, threat detection, and secure connectivity, empowering organizations to optimize operations and drive innovation across their industrial environments.
Technology innovations
Kasman said that Cisco industrial routers offer unparalleled functionality in a single, compact device. Unlike traditional solutions that require multiple products to handle various networking needs, Cisco industrial routers integrate advanced networking, modular capabilities, and advanced security into one platform. This streamlined approach not only reduces hardware costs and deployment complexity but also saves valuable space in industrial environments.
With Cisco’s SD-WAN Manager, businesses can centralize management and automate deployment and configuration tasks. Security policies are unified, meaning they are created in one location and automatically applied across the entire network, leaving no gaps and ensuring consistent protection everywhere.
Cisco industrial routers embed zero-trust network access (ZTNA) capabilities, enabling organizations to gain secure remote access to connected assets, for configuring and troubleshooting devices without dispatching technicians. Because ZTNA capabilities are built into the routers, there is no need to deploy additional hardware. This helps reduce costs and simplifies deployment, especially in remote locations where small cabinets might not have the space for additional hardware appliances.
“Using the same SD-WAN console, businesses can configure their networks and deploy security policies, creating a streamlined, cost-effective solution. Cisco Industrial Routers deliver efficiency, security, and scalability in a single solution, making them an invaluable asset for modern industrial networks,” Kasman said. “This is especially valuable for industries with widely distributed assets, as it eliminates the need for on-site visits, reducing operational expenses and downtime. This combination of security, flexibility, and centralized management makes Cisco industrial routers a standout choice for modern industrial networks.”
Remote connectivity solutions
Cisco Secure Equipment Access is designed to address the evolving needs of organizations across a variety of sectors by providing secure, seamless, and efficient remote connectivity to critical equipment and systems. In today’s increasingly connected world, these solutions are essential for supporting operations, reducing on-site visits, and enabling timely responses to system issues—all while maintaining robust security standards.
Kasman said that key applications include not only remote monitoring, troubleshooting, and configuration, but also secure firmware upgrades, software patch management, and real-time diagnostics of field devices.
Industries such as manufacturing, roadways infrastructure, public transportation, renewable energy, oil and gas, water utilities, and EV charging stations all benefit from these capabilities. For instance, in manufacturing, remote connectivity supports predictive maintenance and minimizes unplanned downtime. In energy and utilities, it allows operators to manage geographically dispersed assets and respond rapidly to outages or anomalies.
By delivering these advanced security features and connectivity options, Cisco Secure Equipment Access not only protects operational technology environments but also supports regulatory compliance, enhances productivity, and facilitates safe, scalable remote workforces. These benefits are indispensable for industries that rely on secure, always-available access to distributed or remote assets.
Addressing engineering challenges
“New Remote Connectivity solutions are designed to address several key engineering challenges faced by modern industrial organizations as they strive to maintain secure and efficient operations. Industrial enterprises increasingly rely on remote experts, contractors, and OEM partners to configure, troubleshoot, and support critical assets across geographically dispersed sites,” Kasman said. Traditional VPN solutions, however, are not ideal for OT environments. VPNs often provide broad, always-on access to the entire network, making it difficult to enforce least-privilege access policies. Managing granular permissions with VPNs is complex and often beyond the capabilities of most OT teams, especially at the scale required for industrial operations.”
Cisco Secure Equipment Access (SEA) directly addresses these challenges by offering a secure, purpose-built remote access solution tailored for OT. Unlike traditional VPNs, SEA enables fine-grained, role-based access control, ensuring users only connect to the specific devices they are authorized to manage. This supports operational needs while dramatically reducing cybersecurity risks. Furthermore, SEA empowers OT engineers with a self-service portal that allows them to grant, monitor, and revoke remote access as needed—without requiring specialized IT expertise.
“This approach not only simplifies remote support and maintenance but also helps maintain high levels of uptime and operational continuity in critical industrial environments,” Kasman added. “SEA provides a single portal to manage access policies for all sites, making it simple to scale and empowering OT teams to independently manage users and assets, all while ensuring compliance with policies and controls defined by IT. By solving these engineering challenges, Cisco Secure Equipment Access empowers organizations to achieve secure, productive, and scalable remote connectivity while proactively mitigating risks in today’s evolving threat environment.”

“Key trends driving industrial remote connectivity include the convergence of IT and OT, edge computing and the adoption of cloud-native technologies. Innovations such as containerization, 5G and AI-driven analytics are changing the way remote systems are managed,” — Daniel Korte, Technology management PLCnext Technology, Phoenix Contact Electronics GmbH.
PLCnext technology
Robust remote connectivity options such as Proficloud.io is cloud agnostic using integrated MQTT and other communication technologies.
The PLCnext Technology Ecosystem from Phoenix Contact offers a comprehensive solution for industrial IoT applications. It combines robust remote connectivity options such as Proficloud.io, is cloud agnostic through integrated MQTT and other communication technologies and can be extended via the PLCnext Store with various remote connectivity options that provide secure VPN access to PLCnext controllers. These tools support remote diagnostics, programming and data collection, reducing on-site service and speeding up troubleshooting.
According to Daniel Korte, Technology management PLCnext Technology, Phoenix Contact Electronics GmbH, “Security functions such as encrypted communication, firewall protection and role-based access ensure reliable operation. The PLCnext Control platform enables real-time on-site data processing through edge computing and cloud services. Thanks to support for open source software and standard IT protocols, the platform is interoperable, flexible and ideal for modern industrial environments. It supports containerized applications and secure data exchange.”
Technology trends
“Key trends driving industrial remote connectivity include the convergence of IT and OT, edge computing and the adoption of cloud-native technologies. Innovations such as containerization, 5G and AI-driven analytics are changing the way remote systems are managed,” Korte said. “At Phoenix Contact, we see an increasing demand for platforms like PLCnext Technology that support open standards and enable integration with third-party tools and services. Cybersecurity is also a key focus, with secure booting, encrypted communications and identity management becoming standard. In addition, with the rise of the digital twin and predictive maintenance, the need for reliable remote access to machine data in real time is increasing. Together, these trends improve operational efficiency, reduce costs and enable new business models.”
What makes this technology unique?
Korte said that PLCnext Technology is characterized by its openness, flexibility and the integration of IT functions into industry automation. Unlike conventional PLCs, PLCnext supports high-level languages such as C++, Python and Java as well as IEC 61131-3 and allows developers to use familiar tools. The Linux-based architecture enables containerized applications and seamless cloud connectivity to any cloud, including Proficloud.io.
This hybrid approach bridges the gap between automation and digitalization, allowing users to implement advanced analytics, AI and remote services directly at the edge. The platform’s cybersecurity features, including secure boot and encrypted communication, ensure secure remote operations. This unique combination of openness, security and scalability makes PLCnext Technology the ideal solution for future-proof industrial connectivity.
Focus of remote connectivity solutions
Korte said that remote connectivity solutions are essential in industries such as manufacturing, energy, water/wastewater and transportation. Applications include remote monitoring of decentralized systems, predictive maintenance and centralized control of decentralized systems.
In the renewable energy sector, for example, operators use PLCnext Technology to monitor wind turbines and solar farms from central locations. In water management, remote access enables real-time control of pumping stations and wastewater treatment plants. OEMs benefit by offering remote diagnostics and updates for their machines, reducing service costs and increasing customer satisfaction. These solutions are particularly valuable in geographically dispersed or hazardous environments where on-site access is limited or costly.
“Modern solutions for remote connectivity face several technical challenges: secure data transmission, interoperability, scalability and real-time responsiveness. Traditional systems often lacked flexibility and required proprietary tools. PLCnext Technology overcomes this problem by supporting open standards and IT protocols that enable seamless integration into existing infrastructure,” Korte said.
He added that cybersecurity is a major concern, and the Phoenix Contact platform includes a secure launch, encrypted communications and user authentication to protect against threats. Another challenge is managing large amounts of data at the edge – PLCnext Technology enables local processing to reduce latency and bandwidth usage. Finally, remote updates and diagnostics reduce downtime and maintenance costs, addressing the need for efficient lifecycle management in industrial environments.
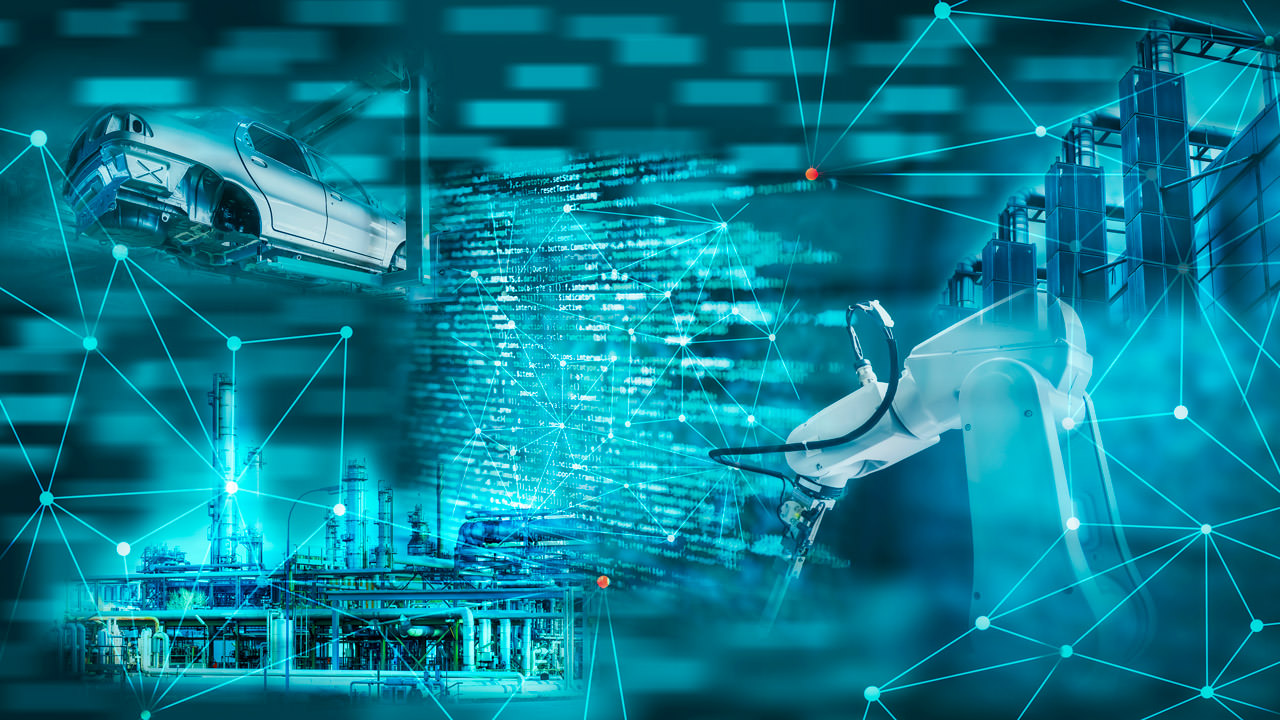
“One of the biggest shifts is the adoption of MQTT Sparkplug B. It’s changed how industrial systems move data by replacing the traditional poll-response model with a publish-subscribe approach that’s faster, more efficient, and firewall-friendly. Devices push updates only when something changes, reducing bandwidth and simplifying connectivity across networks,” — Dan White, Director of Technical Marketing, Opto 22.
Encrypted tunnels
Utilizing dual Ethernet network interfaces, zero-trust user authentication, OpenVPN client and granular firewall control..
“Opto 22’s groov devices—groov EPIC and groov RIO—are designed from the ground up for secure, reliable remote connectivity. With dual Ethernet network interfaces, zero-trust user authentication, a built-in OpenVPN client, and granular firewall control, they let engineers connect to remote systems over encrypted tunnels without exposing the control network to the public internet,” Dan White, Director of Technical Marketing at Opto 22 told IEB.
White said that, with tight, built-in firewall controls, users choose which services are exposed. In many cases they don’t need to open any ports at all, because groov devices can publish data outbound using MQTT with Sparkplug. This publish/subscribe model avoids polling and sends updates only when something changes. With TLS encryption and client-authenticated certificates, it’s a secure, efficient way to move data across networks without exposing the system.
For diagnostics and visualization, there are options. Browser-based HMI software groov View is built in for control, trending, and status screens, and is accessible from any device with proper credentials. If user standardize on Inductive Automation’s Ignition, groov devices also support Ignition Edge to provide tag access, alarming, and mobile-friendly visualization.
“And because groov devices combine control, I/O, networking, and data services in one platform, there’s no need for separate gateways or PCs to enable remote support. It’s all built-in. This setup reduces complexity, improves security, and gives engineers practical tools to monitor and support systems from wherever they are,” White said.
Technology trends
White said that one of the biggest shifts is the adoption of MQTT Sparkplug B. It’s changed how industrial systems move data by replacing the traditional poll-response model with a publish-subscribe approach that’s faster, more efficient, and firewall-friendly. Devices push updates only when something changes, reducing bandwidth and simplifying connectivity across networks.
“Security is no longer something you have to add—it’s baked in. Modern systems include built-in VPN clients, use TLS encryption by default, and support certificate-based authentication. Many are designed with outbound-only communication in mind, so there’s no need to open inbound ports. That aligns well with IT security policies and makes deployment much easier in remote or cloud-connected applications,” White said.
He added that cloud integration is another major trend. Edge devices can now publish data safely and securely to cloud platforms for monitoring, analytics, and long-term storage—without middleware or external gateways.
“Scalability is a major differentiator. Remote connectivity today isn’t limited to large, centralized systems. It can start with a single device in the field and scale to hundreds across multiple sites, all managed with consistent tools, protocols, and security policies,” White added.
Traditional industrial systems have been isolated or hard to integrate. Now, edge devices are designed to speak both OT and IT languages:
Modbus/TCP, serial RS232/485, OPC UA, analog, and digital I/O on one side; MQTT Sparkplug B, REST API, and SSL/TLS security on the other. That makes it easier to move data securely among machines, cloud platforms, and enterprise systems.
These platforms are also self-contained. Instead of piecing together PLCs, gateways, and third-party VPN appliances, everything you need for control, visualization, remote access, and data communication is in one small box.
Applications solutions
“Remote connectivity is a natural fit for industries with widely distributed assets or critical infrastructure,” White said.
In water, wastewater, and utility systems, remote access reduces the need for site visits and allows operators to monitor tanks, pumps, and generators across large service areas. It’s essential for catching issues early and reducing response time.
Oil and gas, along with broader energy markets, rely on remote systems to manage wellheads, substations, and other unmanned locations. With secure access to live data, teams can make informed decisions without having to be on-site, or to wait for someone who is.
Machine builders and OEMs benefit from staying connected to the systems they ship. Remote diagnostics help them support customers in the field, track equipment usage, and even push updates after deployment. It’s a huge win for uptime and customer satisfaction.
Building automation and smart facility applications also depend on remote connectivity—especially when managing HVAC, lighting, and power systems across multiple buildings, campuses, or regions.
Engineering challenges
White added that security has always been one of the biggest barriers to remote access. Older systems often required opening inbound ports or punching through firewalls—something most IT teams rightly pushed back on. Modern solutions are designed with outbound-only communication, TLS encryption, and certificate-based authentication, making secure access possible without compromising the network.
Complexity in older setups was another challenge. Engineers used to need a mix of PLCs, modems, remote desktop software, and custom scripts just to access a remote site. New platforms integrate all of that—control, networking, remote access, and visualization—in one box.
Data loss was also common in remote systems. If the network went down, data just disappeared. Today’s solutions buffer and store data locally, then publish it when the connection is restored. You keep a complete record, even across outages.
Finally, updates used to be painful. Making changes to logic, firmware, or configuration meant being on-site or walking someone else through it. Now, secure remote updates are built-in, so engineers can support systems across sites or time zones without leaving their desks.

“As industries become increasingly digitized, three trends are shaping the transformation of remote connectivity: stronger cybersecurity requirements, hybrid infrastructure integration (legacy and Ethernet-based devices), and the need for scalable, resilient remote access,” — Philipp Jauch, Integrated Marketing Manager, Moxa Europe GmbH.
Remote Connect
Securely bridge field devices, service engineers and application servers over the internet.
According to Philipp Jauch, Integrated Marketing Manager, Moxa Europe GmbH, Moxa’s Remote Connectivity solution is designed to securely bridge field devices, service engineers, and application servers over the internet. At the heart of this solution is Moxa Remote Connect (MRC), a platform that offers an easy-to-deploy, cybersecure approach to industrial remote access.
The solution combines three key components: the MRC Server, MRC Gateway, and MRC Client. The MRC Server acts as a centralized connection management platform that defines relationships between gateways and clients. The MRC Gateway connects Ethernet-ready devices at remote sites to the internet securely, while the MRC Client, installed on an engineer’s laptop, provides intuitive access to remote devices.
Administrators can define access schedules and set permissions through the MRC Server, offering full control over when and how devices are accessed remotely. To further simplify deployment, MRC Quick Link, a Moxa-hosted remote connection service, minimizes maintenance overhead by handling the setup and connection process for users.
Latest remote connectivity solutions
“As industries become increasingly digitized, three trends are shaping the transformation of remote connectivity: stronger cybersecurity requirements, hybrid infrastructure integration (legacy and Ethernet-based devices), and the need for scalable, resilient remote access,” Jauch said. “With cybersecurity taking center stage, regulatory initiatives such as the EU Cyber Resilience Act (CRA) are setting the bar for mandatory product-level security. In parallel, technical standards like IEC 62443 provide a structured framework for securing industrial systems, from development to deployment. Together, these pressures are prompting manufacturers and operators to reassess how they manage secure remote access to field equipment. Meanwhile, digital transformation initiatives are expanding the number and diversity of connected devices, requiring both compatibility and manageability.”
In this context, Jauch said that industrial connectivity solutions must deliver secure-by-design architectures, support for both brownfield and greenfield deployments, and fail-safe network performance in increasingly remote and unmanned environments.
Moxa’s OnCell G4300 Series cellular routers were developed with these exact challenges in mind. Built in compliance with IEC 62443-4-2 and developed under IEC 62443-4-1 secure development practices, the series offers future-ready security alongside flexible networking options. The routers also support legacy serial devices and modern Ethernet-based systems, enabling a smoother transition for operators modernizing their infrastructure.
Cellular routers
Moxa’s OnCell G4300 Series cellular routers combine advanced cybersecurity, reliable connectivity, and broad interoperability, making them uniquely suited for industrial remote access.
Security features include Secure Boot, which ensures only authenticated firmware and software are executed during startup, and Deep Packet Inspection (DPI), which inspects OT protocol traffic to control exactly which devices are allowed to read or write data. An integrated firewall provides granular control over services and ports, reducing the attack surface of connected systems.
To support both modern and legacy infrastructure, the routers include built-in RS-232/422/485 ports, enabling secure connectivity to older serial devices without additional hardware. For Ethernet-based setups, a model with an integrated 8-port Ethernet switch simplifies network deployment at remote sites.
Connectivity stability is enhanced through GuaranLink, which continuously monitors link status and triggers automatic failover or reconnection mechanisms when needed. The feature is highly configurable, allowing adaptation to diverse use cases and environments.
Finally, with global LTE band support, a single device model can be used across multiple regions, streamlining logistics, reducing the bill of materials, and simplifying international deployments.
Applications and industries
“Industrial remote connectivity solutions are essential across various sectors—unified by the need to connect and manage equipment in the field. These applications often involve machines with long life cycles (~15 years), deployed in remote areas, where sending service engineers on-site is costly and time-consuming,” Jauch said.
Jauch said that factory automation is a prime use case, where machine builders often provide service contracts that require fast response times in the event of downtime. However, restrictive IT policies at manufacturing sites can complicate remote access. By using Moxa’s remote connectivity solution, machine builders retain secure, direct access to their machines without depending on third-party IT configurations.
In oil and gas, the need for explosion-proof and certified equipment is critical. The OnCell G4300 Series meets international standards including IECEx, ATEX, and CID2, enabling secure remote monitoring of pipelines and other critical assets.
The rise of electric vehicle (EV) infrastructure also demands scalable and robust connectivity solutions. Harsh outdoor environments, a high volume of deployed charging stations, and the risk of communication loss all necessitate a solution that can maintain reliable and secure connections over long distances.
Engineering challenges
“Managing a growing number of remote connections across globally deployed machines and applications poses significant challenges. Engineers need secure, scalable, and easy-to-deploy connectivity—especially as regulatory expectations increase,” Jauch said.
New regulations such as the EU Radio Equipment Directive Delegated Act (RED-DA) aim to improve cybersecurity for wireless and internet-connected products. While not yet in force, it is already shaping design priorities by encouraging manufacturers to implement more secure communication practices from the start.
In parallel, initiatives like the Cyber Resilience Act (CRA) and standards such as IEC 62443 highlight the importance of secure development lifecycles and device-level protections.
Moxa addresses these needs by offering industrial connectivity products that are easy to deploy and comply with modern security expectations. Our solutions can also be integrated with MXview One, Moxa’s network management software, which simplifies device monitoring, visualises bandwidth usage, alerts engineers to unusual activity or rogue devices, and accelerates documentation processes.

“The increasing demand for IoT and IIoT devices necessitates robust connectivity solutions for seamless integration. The latest AI and machine learning technologies enable predictive maintenance and process optimization, while software-defined networking (SDN) allows flexible, centralized network management, enhancing scalability and adaptability in industrial environments,” — Lars Walpurgis, Product Owner – Sinema Remote Connect, Siemens.
Sinema remote connect
Server application facilitates simple, secure remote access to widely distributed machinery and plants, such as remote maintenance.
Siemens offers the SCALANCE M series of industrial routers, which provide secure remote access to machines and plants. This solution supports VPNs, 5G, firewall functionalities, and various mobile and broadband connections, ensuring reliable and secure communication. Key benefits include reduced downtime, efficient maintenance, and enhanced data security.
According to Lars Walpurgis, Product Owner Sinema Remote Connect at Siemens, SINEMA Remote Connect, the Siemens management platform for remote networks, is a server application which facilitates simple, secure remote access to widely distributed machinery and plants, such as remote maintenance. SINEMA Remote Connect ensures the secure administration of VPN tunnel connections between the control centers, the service engineers, and the installed systems. Secure remote maintenance can then be carried out via the TIA Portal, for example.
“This avoids direct access to the corporate network in which the machine to be maintained is integrated,” Walpurgis said. “The stations that are to communicate with one another “meet” at a neutral location, the SINEMA Remote Connect Server, also known as a rendezvous server. This then verifies the identity of the individual stations by an exchange of certificates before access to the machine via the corporate network or cellular network, and the dedicated SCALANCE industrial router becomes possible.”
Trends and innovations
“The latest solutions for industrial remote connectivity are driven by several key technology trends. For instance, 5G integration offers high bandwidth and low latency for real-time data transfer,” Walpurgis added. “Edge computing brings processing power closer to data sources, reducing latency and improving efficiency. Also, advanced cybersecurity measures ensure data integrity and secure remote operations. A key for that is a unified Identity and Access Management (IAM) to securely authenticate and maintain users and machines.”
Walpurgis added that the increasing demand for IoT and IIoT devices necessitates robust connectivity solutions for seamless integration. The latest AI and machine learning technologies enable predictive maintenance and process optimization, while software-defined networking (SDN) allows flexible, centralized network management, enhancing scalability and adaptability in industrial environments.
“Industrial remote connectivity technology is unique due to its comprehensive security measures, such as advanced encryption and multi-layer firewall protection, which ensure data integrity and secure remote operations,” Walpurgis said. “Its high reliability and seamless integration with various existing systems and network protocols make it adaptable and versatile for different industrial needs. In that sense, SINEMA Remote Connect is an easy-to-use tool for Operational Technology (OT) on the shop floor.”
He said that remote connectivity solutions are predominantly focused on industries like manufacturing, process industries, energy, and public infrastructure. These solutions are critical for applications such as remote monitoring, which allows for the observation of industrial processes from a distance; predictive maintenance, which uses data analytics to predict equipment failures and schedule timely maintenance; decentralized control systems, which distribute control functions across various devices for increased reliability and efficiency; and real-time data processing, which enables immediate analysis and response to data collected from industrial operations.
“Automation engineers face several challenges, including ensuring secure remote access to sensitive industrial systems, managing the complexity of network configurations, and minimizing system downtime,” Walpurgis said. “Particularly for OT remote connectivity Layer-2 access is a challenge.
Modern remote connectivity solutions address these challenges by providing secure and encrypted communication channels that protect against unauthorized access and cyber threats. They also offer user-friendly configuration tools that simplify network management and setup. Upcoming European security regulations like Cyber Resilience Act (CRA) and NIS-2 are additional challenges.”