TechnologyJanuary 18, 2024
Industrial networks playing key role in digital transformation
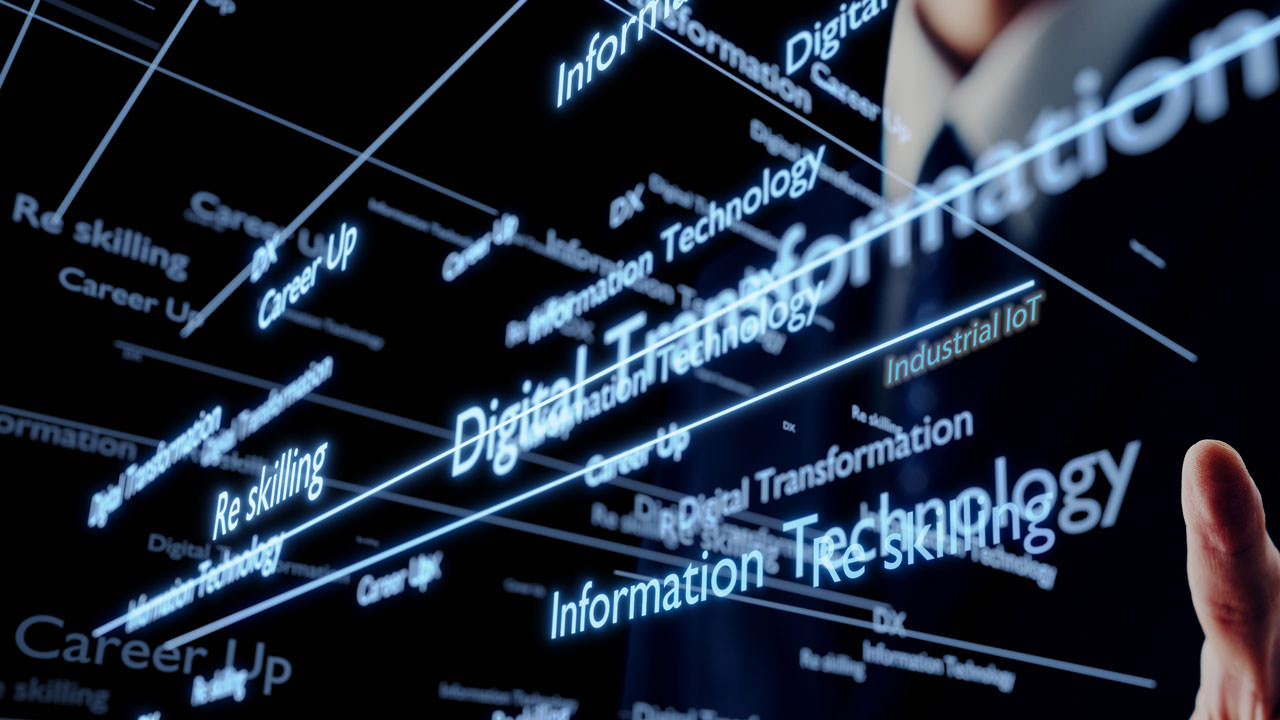
Digital Transformation (DX) is a goal for manufacturers with advances in artificial intelligence and machine learning, along with augmented and virtual reality, adding new possibilities. But the overall focus for industrial networks is still on speed of deployment, enhanced visibility and flexible, resilient software-defined operation.
Digital Transformation is an ongoing quest for manufacturers poised to harness advanced manufacturing networking and software solutions to create new avenues for continuous innovation, strategic success and long-term profitability.
In this special report, the Industrial Ethernet Book reached out to industry experts to gain their insights into the megatrends driving Digital Transformation (DX), and new fuel for the fire with recent advances in artificial intelligence, machine learning and more.
Effective management of networked assets
Fast, scalable and automated updates for network-enabled, operational technology (OT) and devices.
A team of industry experts from Phoenix Contact responded to our questions on what technologies and/or megatrends are shaping and enabling Digital Transformation in 2024 and beyond.
“One major topic for shaping and enabling future Digital Transformation is the development of solutions for fast, scalable and automated device and update management (DaUM) of network-enabled operational technology (OT) devices.” Dr.-Ing. Frank Possel-Dölken, Chief Digital Officer and Member of the Group Executive Board, told IEB. “This is largely motivated by increased activity of cyber criminals attacking not only classic IT infrastructure (for example, credential phishing for Microsoft, Apple or Google services) but also directly targeting operational technology (OT) systems.”
Possel-Dölken said that it is of high importance to understand the need for action at industrial enterprises. For cyber criminals, it is easy to gain access to OT systems because factories contain a variety of network-enabled devices from different manufacturers relying on different communication technologies and protocols. There is little holistic overview in terms of asset management; furthermore, there is no assurance that all security vulnerabilities have been addressed through software updates. Further exacerbation results from upcoming regulatory requirements.
“In the overall discussions on Digital Transformation, there is mostly a focus on developing new digital solutions/business models for gaining revenue – and partly the necessity of implementing new and more capable software systems for raising the potential out of digital transformation,” Possel-Dölken said. “Our main statement and remark to other companies, of course with regards to our own activities and experiences, is to emphasize the protection of both enablers for Digital Transformation as well as the basic infrastructure of industrial enterprises.”
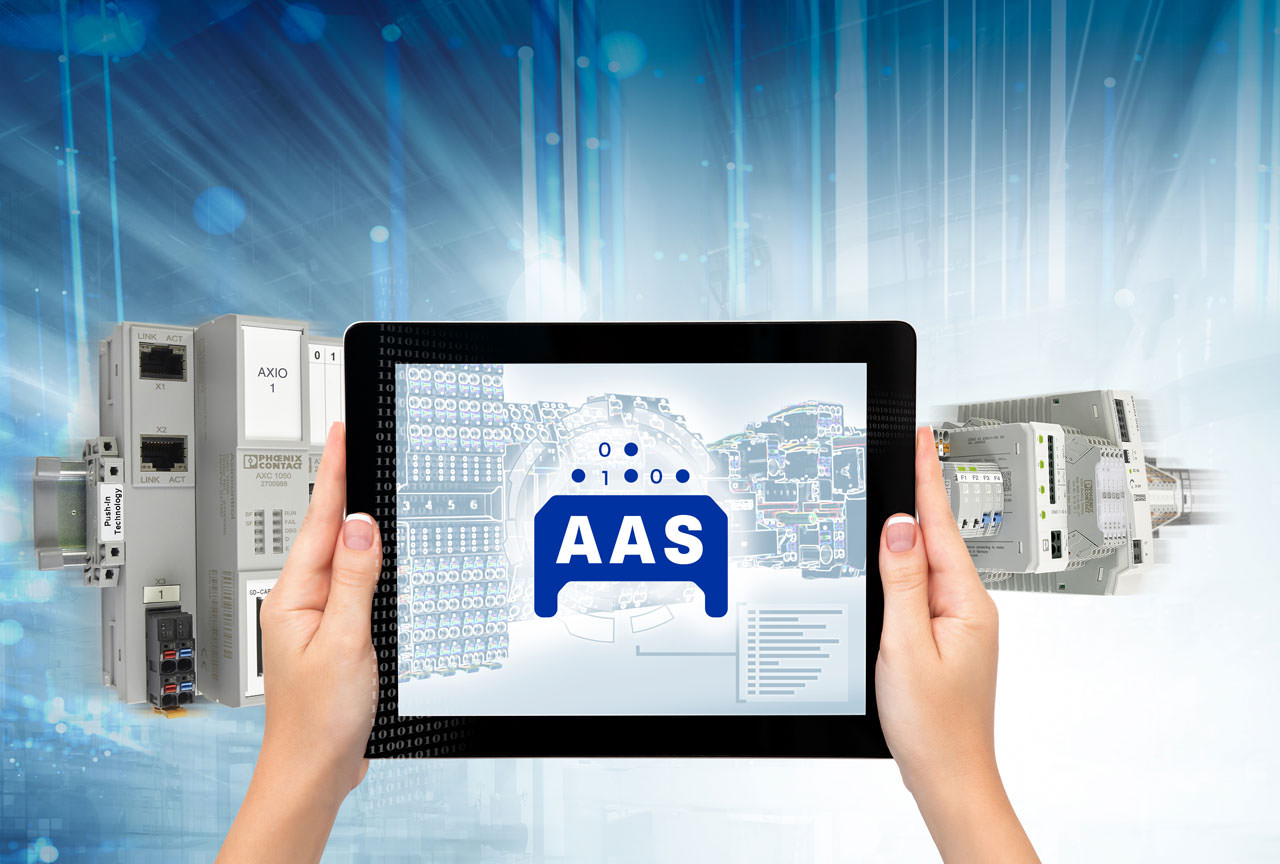
“Our main statement and remark to other companies, of course with regards to our own activities and experiences, is to emphasize the protection of both enablers for Digital Transformation as well as the basic infrastructure of industrial enterprises.” — Frank Possel-Dölken, Chief Digital Officer and Member of the Group Executive Board, Phoenix Contact.
Asset Administration Shell
Possel-Dölken added that the implementation of device and update management for networked OT devices requires seamless and barrier-free data logistics across manufacturer specific systems. The Asset Administration Shell (AAS) as a standardized technology for developing digital twins plays an essential role in establishing this solution. Why? The AAS operates as a data container and enables the standardized data transmission via common sub models, structure and security requirements. The big advantage: it is standardized! Both the transmitting and receiving enterprise understand and use the identical semantic (=semantic of AAS) for the information/data. The further processing of the received data, e.g. the integration into the internal PLM system of the receiving company, is executed fast.
“A good example that highly benefits from this solution is an internal machine building department, developing and building highly automated production equipment for production facilities,” said Dr.-Ing. Guido Hüttemann, Assistant to Chief Digital Officer. “Such machines usually consist of several hardware-software-devices from multiple vendors. During both development and maintenance phase, the availability of latest information is required – e.g. master data or information about software updates. The process of gathering all the information initially – most probably from the webpages of the numerous manufacturers – and keep them updated is costly, requiring both a lot of time and binding scarce human resources.”
He added that the chances that AAS is becoming at least one or even the standard for digital twins is high as a big consortium of international key players – under the umbrella of the Industrial Digital Twin Association (IDTA) – are continuously working on the development of the AAS and its implementation with their internal processes.
Another major driver for the operational implementation of data-driven use case such as device and update management is the cross-industry initiative called Manufacturing X. The overall goal of this initiative is to develop a sovereign data space for the entire industry. This is an enabler for exchanging data securely and confidentially along value chains without relinquishing control.
Currently, several consortia are awaiting the approval of their project proposals. The initiative is funded by the German Federal Ministry for Economic Affairs and Climate Action and lasts until mid of 2026.
Interoperability challenges
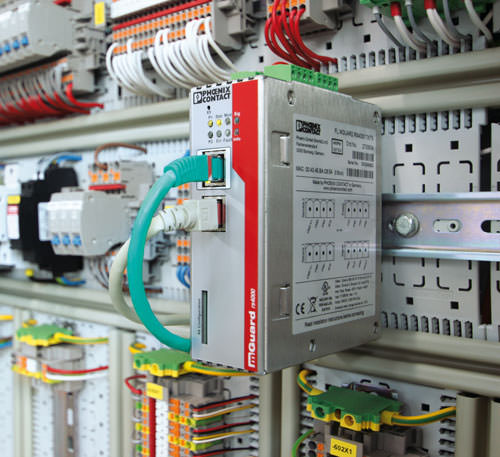
Machines usually consist of several hardware-software-devices from multiple vendors. During both development and maintenance phase, the availability of latest information is required – e.g. master data or information about software updates. The process of gathering all the information initially – most probably from the webpages of the numerous manufacturers – and keep them updated is costly.
Dr.-Ing. Christoph Kelzenberg, Director Digital Innovations said that, overall, the missing interoperability of software systems within one enterprise as well as between different enterprises is addressed by the technologies mentioned before. The consistency of data is not only required from customers (e.g. traceability as a customer requirement), it is also required by law (e.g. supply chain act in Germany).
“An exemplary customer benefit of the AAS technology is the ability to develop the real digital twin of an asset. To understand that, it is very important to distinct between an “As-Built” bill of material and an “As-Is” bill of material! Nowadays, the end customer receives a bill of material that includes all information of the factory state of an asset – meaning a status as built in the factory,” Kelzenberg said. “But this is not the exact digital representation of the physical good! Why is that? Alongside the different value creation steps – for example of a control cabinet – different entities add, configure and adjust components. They do parameter adjustments, apply software updates and perform other customizations. The consistent usage AAS technology allows to capture changes, such as a configuration of a power supply within a cabinet, and thus to develop the “real” digital twin of an asset.”
With regards to the automation and control engineers itself, Kelzenberg said the solutions allow them to focus on the essential, value-adding tasks during a typical workday. Time-consuming and barely value adding tasks – such as gathering information and data and putting them into a software system – will be obsolete as the described IoT technologies/solutions would be in place.
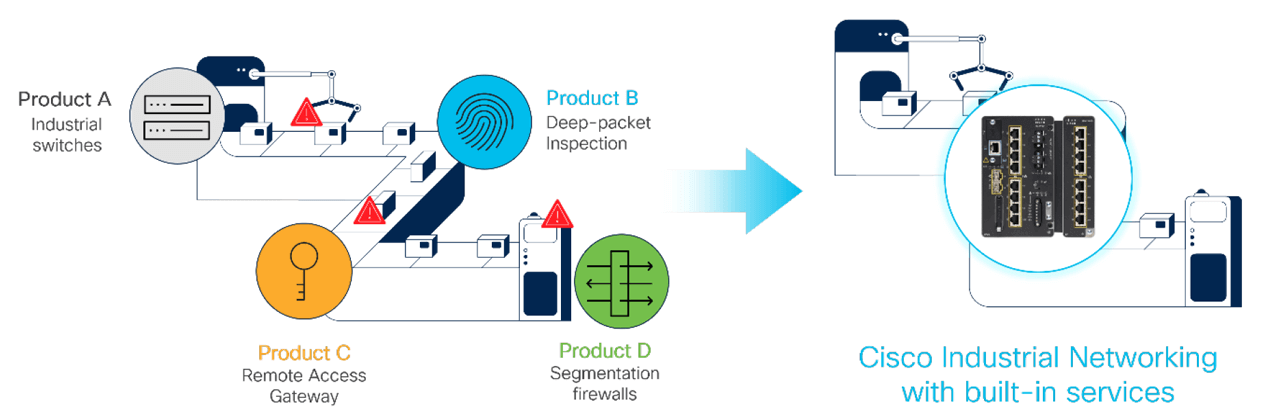
“An effective digitization solution not only relies on switches, routers, and wireless equipment to enable connectivity between assets, but this equipment must be supported by intelligent management and security systems. Together such a solution provides several technical benefits that enable new IIoT applications,” Carlos Rojas, Global Manufacturing Solutions Lead, Industries Group, Cisco.
Building more capable networks
Focus on speed of deployment, enhanced visibility and flexible, resilient software-defined operation.
Carlos Rojas, Global Manufacturing Solutions Lead, Industries Group, at Cisco said that there are a number of noteworthy trends continuing to push Digital Transformation forward.
“First, workforce shortages are fueling the demand for more automation and software-based decision making. Secondly, the desire for more flexibility in operations is driving greater investments in robotics, mobile systems, and wireless technologies. And finally, increasing number of cyberattacks is triggering a renewed focus on cybersecurity and the necessity of secure remote access into operations. And of course, ubiquitous connectivity is paramount to shaping and enabling a sustainable digital environment,” Rojas told IEB recently.
With these new requirements there is also a renewed need for simplifying deployments. The addition of single-function point solutions for each technology is only adding complexity and difficulty in scaling.
“A better answer lies in building a more capable network. Building such a network starts with equipment that is designed to withstand the most challenging of environments and can scale with your operations. Managed networking equipment such as switches and routers that are fit for use in industrial environments, that is, are ruggedized and designed in an environmentally friendly manner can enable digital transformation at scale,” Rojas said.
Look to equipment that’s faster to deploy and enhances visibility into the operations for managing planned and unplanned downtimes. They help build a scalable, flexible, resilient, software-defined network critical for success for any digitization initiative. Such a network can ease deployment of advanced future-ready AI/ML applications that avoid obsolescence and protect operations from becoming “brownfields of the future.”
Technical benefits
Rojas said that an effective digitization solution not only relies on switches, routers, and wireless equipment to enable connectivity between assets, but this equipment must be supported by intelligent management and security systems. Together such a solution provides several technical benefits that enable new IIoT applications.
These technical benefits start with the networking devices themselves. Today’s highly capable equipment is ruggedized to withstand extreme conditions, rivals enterprise equipment in performance, supports lossless resiliency protocols, all the while maintaining a high MTBF. Paired with an intelligent management system, networking tasks can be automated, reducing errors which saves time and costs. With proactive detection of network faults and guided remediation, the network can be relied on to be at its optimum performance. Such a system also lets you segment your operations for further protection.
Previously, a lot of advanced applications used to require additional hardware. With edge-computing capabilities, the network equipment can autonomously run these applications reducing complexity and costs.
One such applications performs DPI on network traffic to identify connected devices, their interactions, and vulnerabilities, providing you with deep visibility into your operations. Another application enables remote zero-trust network access to industrial assets avoiding more complex methodology. Yet another application collects real-time process data and transmits it to AI/ML aided analytical applications in the cloud that can help monitor product quality, maintenance needs, etc. These innovations would not be possible without advancements in industrial networking equipment.
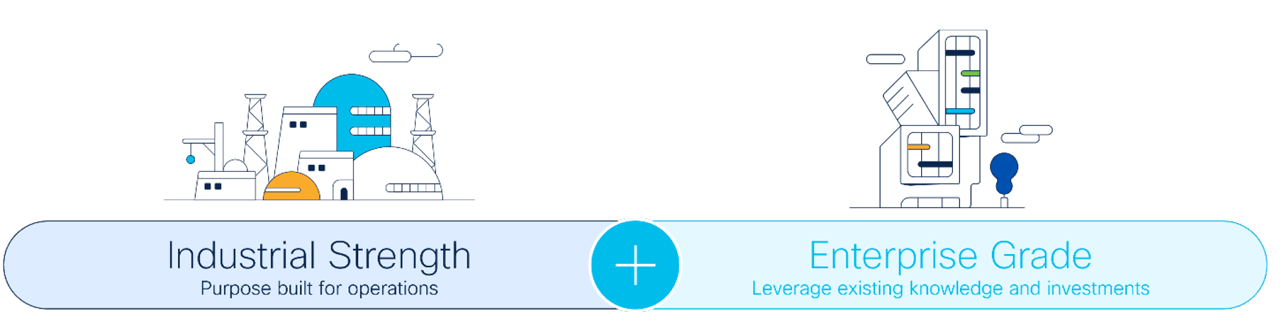
An industrial network that combines the best of two worlds eases control engineers’ jobs.
Industry applications
“Manufacturers are rapidly modernizing their operations by introducing new data driven and software-controlled decision making. They are using these techniques to minimize unplanned downtimes, add production flexibility, improve security, and reduce costs,” Rojas said.
For example, a software driven, deterministic, resilient, and secure network is helping virtualize discrete hardware systems on a factory floor, replacing them with software functions that run in collocated hyper converged infrastructure. This is bringing huge benefits to manufacturers by reducing their maintenance costs, lowering the threat surface, and improving sustainability.
These solutions are also helping industries comply with increasing cybersecurity regulations. For example, European legislators are being asked to implement EU’s NIS2 directive. NIS2 aims to improve cybersecurity, enhance resilience, create a uniform standard, and foster better cooperation between member states. A unified industrial networking and security architecture with visibility, segmentation, and secure remote access is well positioned to easily meet these new requirements.
Responding to challenges
“A proven standardized network architecture removes risks for automation and control engineers and lets them focus on their jobs and bringing about innovation. Such a network can remove one of their biggest challenges of not having a connectivity solution that interoperates across multiple protocols, connects both legacy and modern equipment, and one that is easy to scale and troubleshoot,” Rojas added.
“A dependable network makes it easy for them to add new devices, expand their digitization initiatives, validate their POC efforts, and bring new technologies and solutions into their operations quickly and easily, knowing that the network has their back.”
Real-time data collection capability of the network helps them gain insights into their processes, allowing them to determine the changes necessary for optimization, improve yield and quality, or data needed for Digital Twin, AI and M/L.
Secure remote access to industrial assets allows engineers to configure, monitor, troubleshoot, or collect logs from these assets, helping them ensure that these assets are always running efficiently.
Leveraging edge IoT platforms
Technology facilitates real-time AI/ML applications through local processing.
Marian Hönsch, Product Manager – Industrial IoT at TTTech Industrial, said that “in 2024, key technologies shaping Digital Transformation include AI/ML integration, edge computing, and secure IoT connectivity. The importance of n flexible and secure edge IoT platform emphasizes the vitality of a secure collaboration between IO and OT. Edge computing enables data preprocessing locally, ensuring efficient use of bandwidth. In EU. the industry stakeholders will be confronted with the impact of the NIS2 Directive and the EU Cyber Resilience Act. The distinction of AI/ML into cloud and edge parts ensures flexibility and efficiency in processing and decision-making in real-time.”
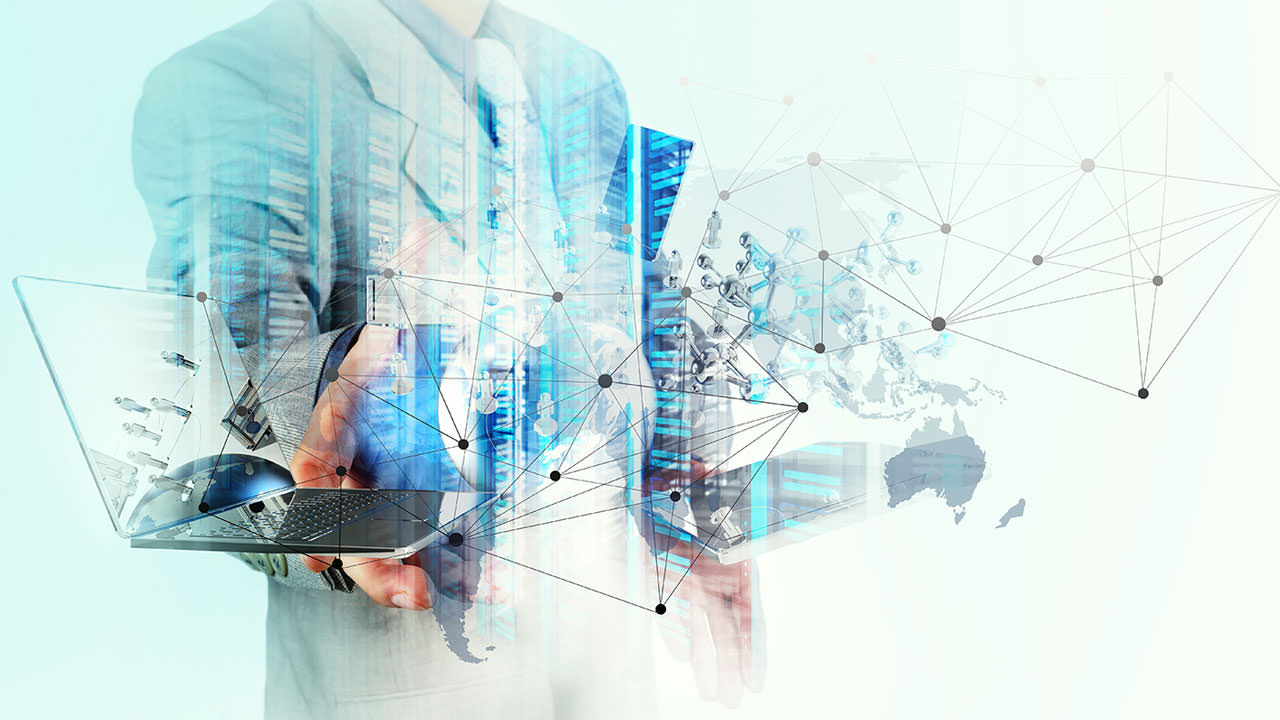
“The Digital Transformation landscape is significantly influenced by the capability of edge computing to facilitate real-time AI/ML applications through local processing. The distinct advantage lies in the ability to execute computations at the edge, ensuring real-time decision-making without solely relying on distant cloud resources. ,” Marian Hönsch, Product Manager – Industrial IoT at TTTech Industrial.
Hönsch said that secure edge IoT platforms provide local preprocessing, reducing data exposure and enhancing resilience against cyberthreats. Failure to incorporate robust security measures in the foundation of applications renders them incapable of being part of and connected to the IIoT, underlining the indispensable role of secure edge computing in shaping the digital future.
“The Digital Transformation landscape is significantly influenced by the capability of edge computing to facilitate real-time AI/ML applications through local processing. The distinct advantage lies in the ability to execute computations at the edge, ensuring real-time decision-making without solely relying on distant cloud resources. This not only enhances the efficiency of IIoT applications but also addresses the critical aspect of cybersecurity and the fact that even the best Internet connection can be unavailable sometimes,” Hönsch said.
Anticipated impact
The application of cutting-edge solutions in 2024 involves not only the integration of secure edge IoT platforms but also a keen emphasis on swift responses to potential threats. The imperative lies in the need for a robust patch management system spanning all vertical levels of an IIoT application throughout the complete supply chain. This approach ensures a proactive stance against exploits and vulnerabilities as required by upcoming regulations. Specifically, in the realm of AI/ML applications integrated into real-time machine operation cycles, the agility to address emerging threats becomes even more critical.
According to Hönsch, the technologies under consideration address challenges for automation and control engineers by fortifying cybersecurity and optimizing data processing. They alleviate concerns related to bandwidth constraints and latency, providing local preprocessing capabilities.
Moreover, the need for secure edge IoT platforms, influenced by the NIS2 directive and the EU Cyber Resilience Act, plays a pivotal role in ensuring the integrity of automation systems.
“A notable challenge for engineers is the diversion of focus from their core value-added applications. As they are increasingly compelled to engage in infrastructure tasks and self-developed edge hosting maintenance, there’s a pressing need for regaining development capacity. To overcome this challenge, engineers can benefit from adopting cloud-managed edge solutions as products, enabling them to refocus on their company’s core competencies and innovative applications,” Hönsch said.
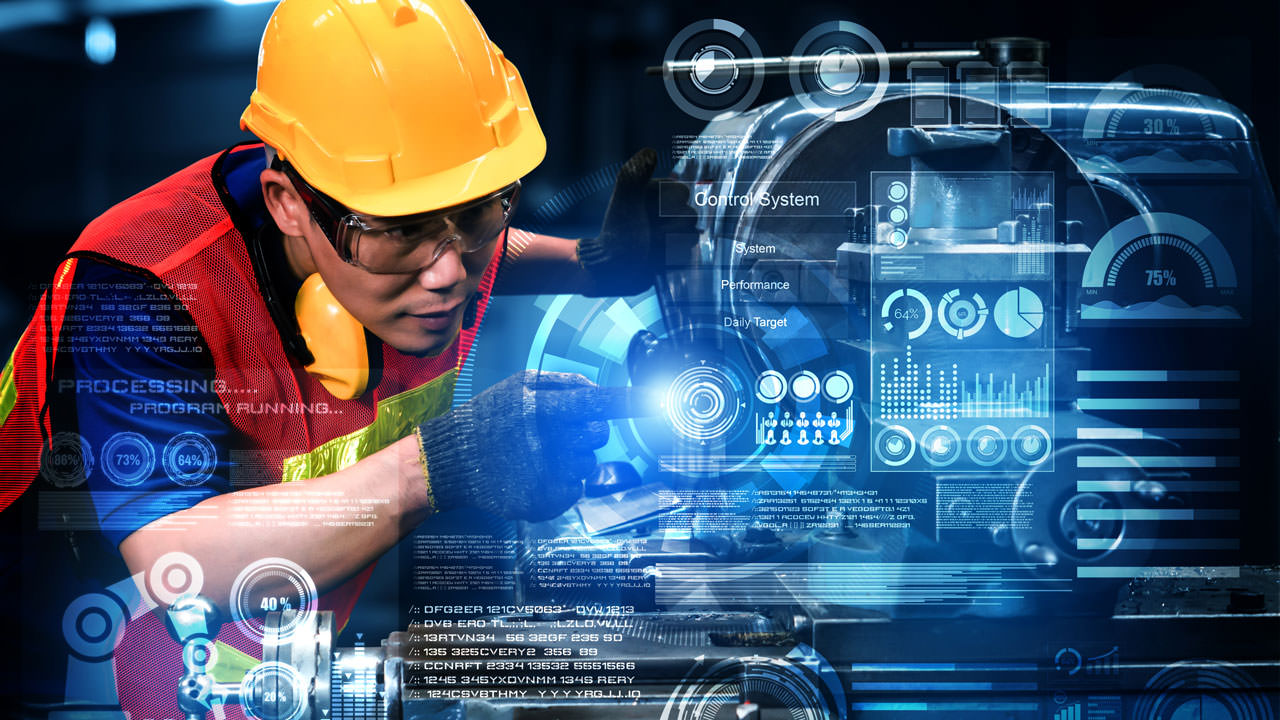
“AI and ML technologies allow broader and easier analysis of information. They can use more inputs and make decisions more quickly, without the bottleneck of requiring humans to interpret, understand, and act on information,” Andrew Stump, director of business development,” Rockwell Automation.
Impact of AI and ML technologies
Overall push is to access data, contextualize it and put it in front of employees to drive better decision making.
According to Andrew Stump, director of business development at Rockwell Automation, “we’ll likely continue to see industrial producers adopting digital technology at a faster pace in 2024. This is partially a continuation of the pandemic having forced companies to accelerate their digital transformation efforts to keep workers connected and mitigate risks like supply chain challenges.”
“But there’s another force driving the accelerated adoption – the technology itself. In 2023, ChatGPT burst onto the scene and thrust artificial intelligence (AI) and machine learning (ML) into the spotlight. This changed how work could be done almost overnight. And as ChatGPT and many new industrial tools have shown, these technologies can be used by nearly anyone. They don’t require specialized expertise in data science or coding.
Now, leadership teams are feeling an urgency to act and unleash the potential of these technologies, or risk falling behind,” Stump said.
Adoption of digital technologies
He added that the accelerated adoption of digital technologies is also driving another trend – the need for help. While pilot projects can demonstrate how technologies like AI and ML can deliver value, producers want to realize that value as soon as possible. Companies need partners who understand these technologies and can help craft a strategy to apply them efficiently, cost effectively and with intent.
Stump said that, for years, industrial producers have been working to access data from their operations, contextualize it and put it in front of employees to drive better decision making. Now, AI and ML technologies can help producers use data in new ways and unleash new possibilities in production.
AI and ML technologies allow broader and easier analysis of information. They can use more inputs and make decisions more quickly, without the bottleneck of requiring humans to interpret, understand, and act on information.
For example, add-on modules with built-in AI engines can be paired with industrial controllers to help optimize production in several ways. They can learn the baseline for a production process and detect anomalies against that baseline to help maintain quality levels. They can also create virtual sensors, which analyze variables from line assets and predict measurements that may otherwise be too difficult or costly to obtain using physical sensors.
“It’s important to note, however, that these technologies shouldn’t all simply be deployed in the cloud. Improving quality and optimizing processes requires being able to access and analyze data in real time. And that happens at the edge. This is why producers should have an edge-to-cloud strategy that allows them to use data and technologies like AI and ML tools where it best serves their applications’ needs,” Stump said.
Impact of new technology
“A top priority in the industrial world right now – and a key opportunity for AI and ML technologies – is to improve sustainability performance. The Eastern Municipal Water District (EMWD) in California provides a good example of what’s possible,” he added.
EMWD serves nearly 1 million people in Southern California and is the state’s sixth-largest retail water agency. Recently, it deployed an AI solution at its aeration operations, which is an energy-intensive process in water treatment. Installed on the existing plant automation network, the AI solution learns the current state of aeration operations and optimally adjusts PID response as conditions change – all with minimal staff intervention.
The solution has improved process control in the operation and delivered an estimated savings of 2,330 kWh of electricity per day – and more than $100,000 of cost savings per year.
Companies are also exploring how they can combine AI and machine vision to optimize quality through closed-loop control. Maintenance is another area of opportunity. An ML-based supervisory application, for instance, can alert technicians if a machine deviates from normal behavior that may signal maintenance is needed. And AI-based tools for CMMS software can help maintenance teams predict and prevent asset failures before they happen.
Addressing challenges for automation and control engineers
Stump said that, for industrial engineers, production optimization is a never-ending quest. As we’ve discussed, AI and ML have great potential to help engineers improve KPIs like quality, throughput and uptime in their operations.
These technologies can also improve worker effectiveness in a tight labor market. They can capture the knowledge of long-time workers and pass it on to newer, less-experienced workers. They can also provide important context – like which alarms require the most urgent attention.
“The current focus on creating simpler tools can also help workers take advantage of technologies like AI and ML without having specialized knowledge in them. In some cases, workers can simply point AI-enabled tools toward the data points that are most relevant to what they’re trying to solve, and the tool will create a model for them,” he said.
“And it’s not just in technologies like AI and ML where greater simplicity is making a difference. There’s a growing demand for industrial robotics to help lighten the loads for operators. Through eased integration between robot and machine control systems, vendors are making it easier to configure, operate and maintain these technologies without having specialized knowledge in robot programming.”
Pervasive connectivity
From unconnected components into a unified group of devices focused on specific results.
According to Dr. Al Beydoun, President and Executive Director at ODVA, “pervasive connectivity is positioned to transform industrial automation in 2024 and beyond. The combination of new technologies including Single Pair Ethernet (SPE), wireless 5G, and Artificial Intelligence (AI) will enable more devices than ever before to be connected to the network while also allowing for continuous feedback loop optimization based on real world input being fed into data models and back onto the production floor. SPE will enable low cost, remotely located devices – such as those positioned far away on a warehouse conveying system, constrained devices in cabinets, and process devices in hazardous areas – to all become a part of the Ethernet plant network.”
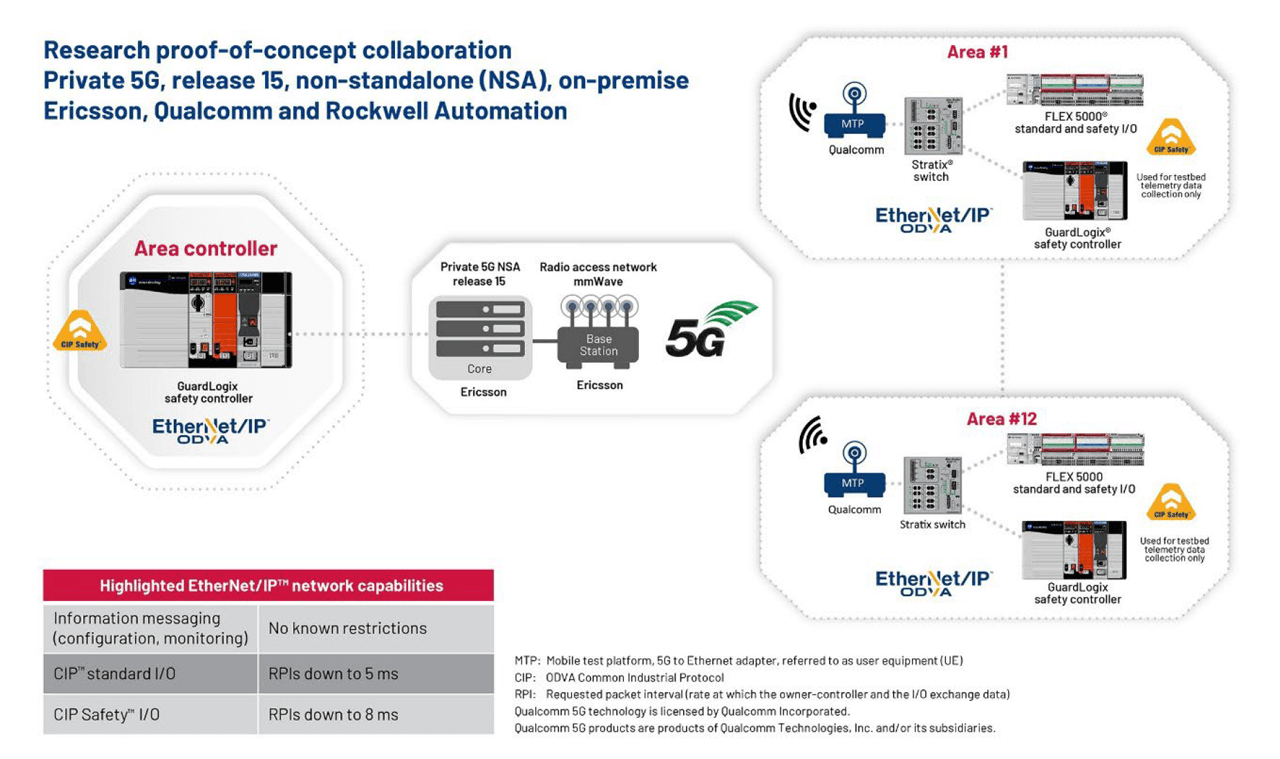
“Pervasive connectivity will help transform plant operations from being an assortment of unconnected components that operate in an opaque manner into a unified group of devices across the network with readily available insights that point to actions that lead to results,” Dr. Al Beydoun, President and Executive Director at ODVA.
Beydoun said that 5G has already started to enable the emerging use of Automated Guided Vehicles (AGVs) and Autonomous Mobile Robots (AMRs) to move freely throughout the factory floor to allow processes to become more flexible and to allow workers to focus on higher value-added tasks instead of being tied up making sure that parts are loaded into a machine, for example. AI is a powerful tool that is able to analyze current production data relative to data models based on operating information over a much longer timeframe to be able to deliver both automated production optimization as well as actionable recommendations for operators in much less time than previously possible.
Focus on technology solutions
“Pervasive connectivity will help transform plant operations from being an assortment of unconnected components that operate in an opaque manner into a unified group of devices across the network with readily available insights that point to actions that lead to results. In the current paradigm, it takes a significant amount of time to collect data from different sources, to clean the data to remove blank or erroneous entries, to collate all of the information, to conduct a manual data analysis, and to finally create an action plan,” Beydoun added.
He said that solutions like SPE and 5G will allow for data to be more easily collected both saving time and providing a more complete picture of operations. Additionally, AI will allow for a reusable optimization model to be built, allowing for multiple analyses going forward based on the existing operations data that indicates what ideal performance is, as well as what conditions such as imminent failure or maintenance needed look like.
The use of Ethernet at the device level and beyond also enables powerful tools like SQL to be taken advantage of. The unmodified, standard Ethernet foundation of EtherNet/IP along with its ease of use is one of the reasons that it’s possible today to push factory floor data from CIP objects into powerful tools like SQL for analysis and action. ODVA Members such as Softing help enable the seamless transfer of CIP object data from EtherNet/IP into SQL databases.
Application implementations
Many experienced workers are also transitioning into retirement, leaving a large knowledge gap behind in the companies and industries that they are departing, including within industrial automation. Additionally, since productivity gains are often tied to increases in wages, there is further incentive across companies to find novel ways to accomplish more with fewer resources.
Utilizing SPE to connect additional devices to the Ethernet network enables benefits such as remote commissioning, standardized diagnostic alarms, and even prognostic forecasting made possible by edge and cloud appliances running optimization models enabled by AI. Additionally, the latest 5G technology releases are enabling low latency and sufficiently high bandwidth for many automation applications including AGVs and AMRs.
Additional benefits of 5G include not having to manage physical access points that will require upgrading over time. 5G has recently been demonstrated by multiple ODVA Members, including Rockwell Automation and HMS Networks to be capable of powering EtherNet/IP devices, including those utilizing the CIP Safety network extension.
“It’s also important to note that while technology can develop in an exponential way, many times organizations progress linearly due to the time it takes to diffuse new information across culture and processes. That means that although SPE, 5G, and AI may be technically ready for use, it will still take time to see widespread adoption across industrial automation,” Beydoun said.
Leveraging remote connectivity powered by SPE
He added that automation and controls engineers can leverage remote connectivity powered by SPE to help reduce time needed for plant and machine startup and troubleshooting. Instead of spending a day chasing down a line break, an offline device can indicate the problem in short order. Wireless 5G as an all-encompassing plant wide network can also make it much easier to add additional devices over time for additional diagnostics information. 5G can also easily accommodate modifications to the production line flow.
Additionally, AI will help what were stressful and time-consuming projects to identify production bottlenecks and quality problems to become much more manageable daily tasks after the work of developing a comprehensive model is completed. While today AI model creation typically requires a highly trained data scientist, there are efforts in the works to develop more user-friendly tools to allow existing IT/OT networking and operations workers to be able to handle the tasks with the aid of standardized software tools. Removing the requirements for specialized skills to fully utilize AI will be a key driver in the next phase of significant productivity improvements in automation.
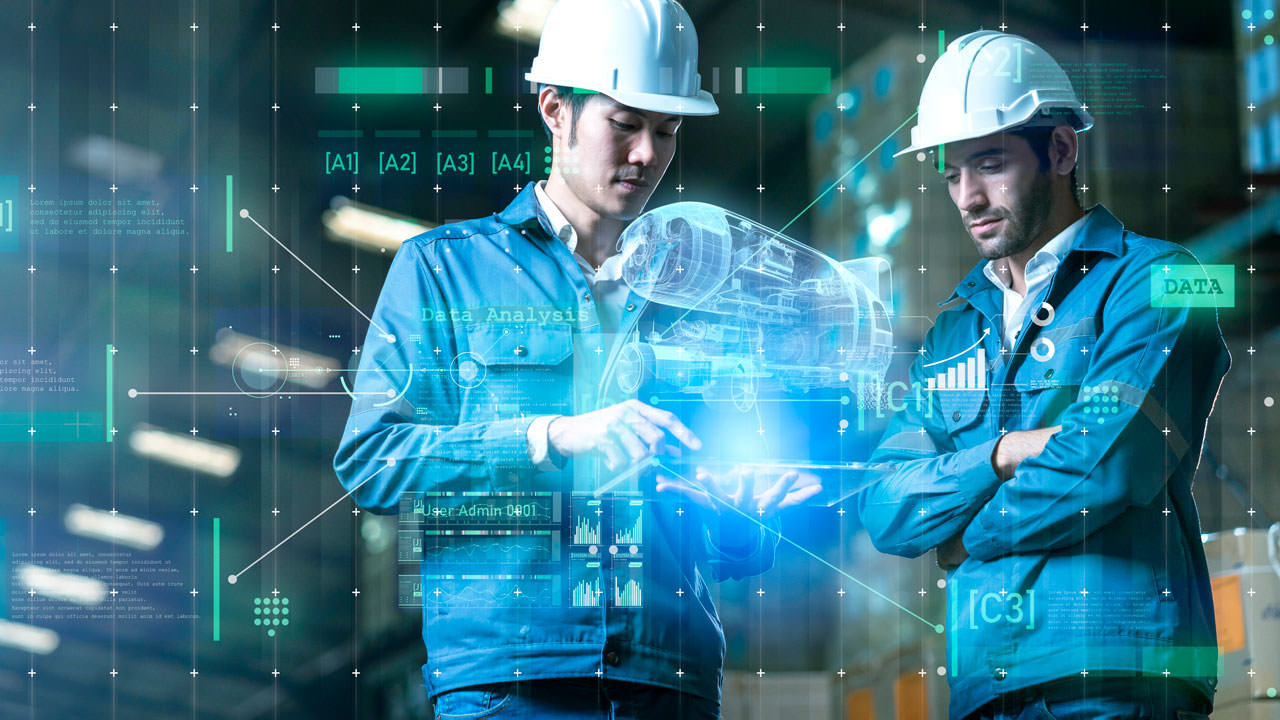
“The changing workforce is also a place where the impact of the industrial metaverse will be seen. The next gen workforce has advanced expectations of working and collaborating in the digital world with AR/VR and AI,” Dale Tutt, VP Industry Strategy at Siemens Digital Industries Software.
Impact of artificial intelligence
AI looks to provide valuable insights, predictive capabilities, and automation to ensure business resiliency.
According to Dale Tutt, VP Industry Strategy at Siemens Digital Industries Software, “while there are several technologies and/or megatrends that I think will shape and enable digital transformation in 2024 and beyond, the one that has everyone talking these days is artificial intelligence (AI). It is already changing how businesses work and can be transformative in ways that we are not even predicting yet. As companies continue to face growing pressures to innovate faster, manage costs, navigate supply chain disruptions more effectively, fill open positions and produce more sustainable products, AI’s impact will continue to grow.”
Tutt said that companies are looking for technologies like AI to provide valuable insights, predictive capabilities, and automation to ensure business resiliency. For example, this could help navigate supply chain disruptions caused by pandemics, natural disasters or political conflict.
And, on the shop floor, AI can help automate mundane tasks to allow engineers more time to focus on solving design challenges. It is important to note that in this scenario, AI will not take away jobs but instead enable workers to focus on innovation. These are just a few examples. I expect AI’s capabilities will prove to be even more impactful and help provide the foundation for the highest level of digital transformation.
“We are also going to continue to see an increase in the use of augmented reality (AR) and virtual reality (VR) to create a truly immersive engineering environment. With digital solutions, we are always looking for enhanced ways to present data to the user in a way that enables them to increase their efficiency. The same immersive environments being used for design and design reviews can also be used to augment how people work, how they build, and how they maintain products. The more companies can present in virtual and augmented reality, the more effective they are going to make their technicians and engineers,” Tutt said.
He added that advances in AI and AR/VR will set the stage for the industrial metaverse to play a significant role in enabling digital transformation this year. The industrial metaverse can be thought of as a virtual world that is almost indistinguishable from reality, a similar concept to a digital twin. But to reach its full potential, the industrial metaverse must become more than a visualized version of the digital twin. On the manufacturing floor, every movement and action must be accounted for precisely, demanding real-world physics.
“Some may think it is overhyped, but the foundational technology of the industrial metaverse is still going to be in demand for customers: the greater computing power, the ability to do faster, real-time, high-definition visualizations, and access to cloud-based computing, which will support the industrial metaverse with the necessary computational power,” he added.
When combined with AI, the industrial metaverse will enable companies to instantaneously work together to address real-world challenges. Companies will be empowered to adopt new technologies faster to accelerate innovation and enhance sustainability. The industrial metaverse has the power to transform entire industries.
The changing workforce is also a place where the impact of the industrial metaverse will be seen. The next gen workforce has advanced expectations of working and collaborating in the digital world with AR/VR and AI.
“Finally, I expect the digital thread itself to be even more impactful in 2024. Companies are interested in the connectivity they can get when they are moving from one application to another. The digital thread and digital transformation are the foundation and key to leveraging these new digital trends, including AI and the industrial metaverse,” Tutt said.
Technology payoff
The technical benefits these solutions provide are how they can optimize production processes and connect factories. A factory with increased connectivity can bring data from the production floor anywhere, at any time, analyze it, and find and optimize interactions that might not have been previously available or would have taken significantly longer to find with typical applications. The data has always been there but now you can see it in real-time and visualize it differently. Today, companies have significantly more options to integrate their solutions and manage and optimize their production processes.
“Connectivity and additional computing power are something that we are doing a lot with the executable digital twin. IIoT is bringing all of the data together in a big data lake and doing data analytics, but at the same time it is also moving some of that computation to the machine and feeding it into the digital twin to enable even further optimization,” Tutt said.
He added that “one of our customers is a battery supplier and they have been using Insights Hub, our solution that drives smart manufacturing through IIoT. This customer uses Insights Hub to gain actionable insights from their asset and operational data. They are using this to optimize their production processes and help improve the yield of their battery production. This is a great example of how to bring data and data analytics together in a way that could not have been done five or 10 years ago, maybe even two or three years ago. Companies are seeing a significant improvement in the yield and the impact of that is how it affects the bottom line.”
Another customer is doing the same thing in their new production facility for engine blade production. They are getting a much more holistic view of their factory operations because they have more data available to them, enabling them to improve their yield. This goes back to the convergence of IT and OT, which provides manufacturers with greater flexibility and visibility and encourages collaboration across planning, scheduling, and factory performance, leading to superior efficiency. “We are seeing these successes and I know of customers who are experiencing production increases of 15 to 20 percent,” Tutt said.
Process optimization
These technologies help automation and control engineers optimize their production lines faster and in a more controlled way, especially when they are managing their data and their applications with good configuration control. They can now track changes much more effectively over time.
“Digital transformation enables companies to combine the real and digital worlds and unlocks a critical resource, data, the flow of which can now be shared between all stakeholders involved in a project. Using digitalization in this manner can also guide and support companies on their sustainability journeys, facilitating energy and resource efficiency and decarbonization by using fewer resources to achieve results,” Tutt said.
“While digital transformation can help companies address the more immediate pressures coming in 2024, it can offer much more to companies that build a plan to evolve beyond connecting data into higher level functions such as automation of data management and eventually the closed-loop optimization of products and processes. It is not a short-term fix but instead a long-term strategy for smart companies,” he added.