TechnologyNovember 18, 2021
Long Distance Positioning System (LDPS)
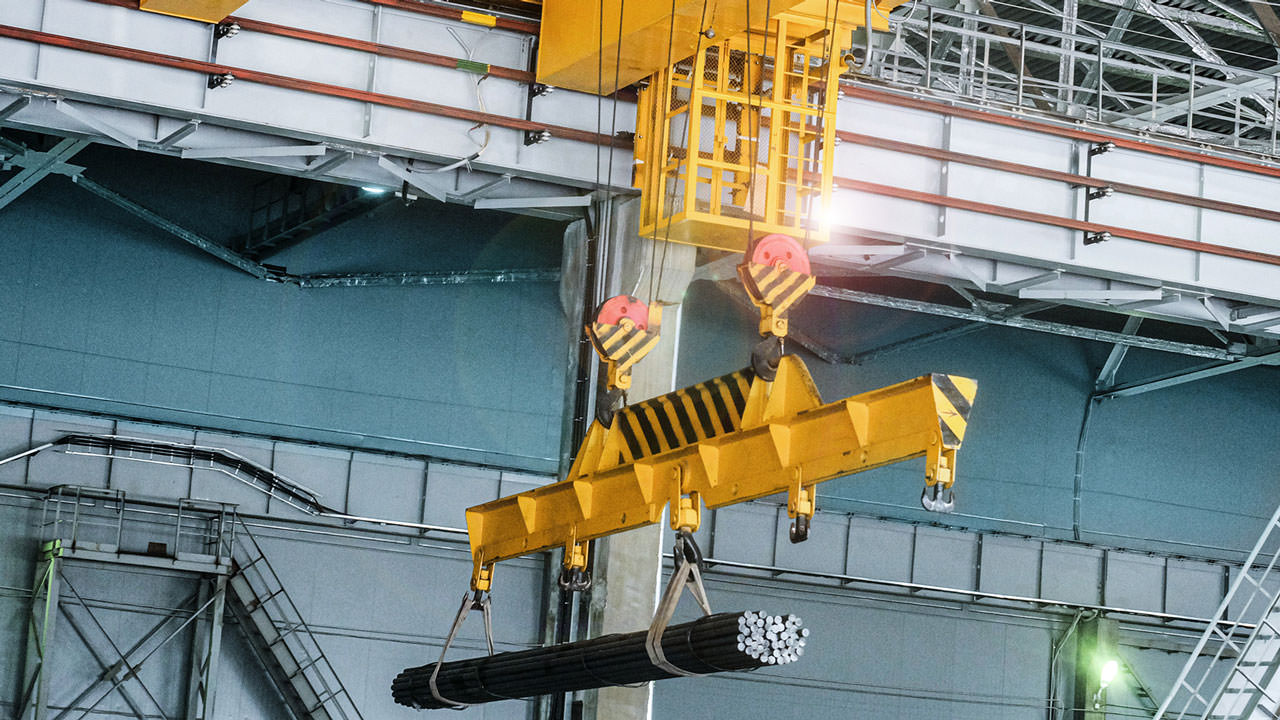
New technology provides reliable, intelligent and adaptable position measurement over several hundred meters in harsh environmental conditions.
Long distances are no longer an obstacle for the intelligent BTL magnetostrictive position measuring system. Where the highest precision in position and speed measurement is required, Balluff offers an absolute measuring displacement encoder that can determine positions over distances of several hundred meters with a repeat accuracy of 0.5 mm. This makes the system ideally suited for applications on overhead traveling cranes, loading bridges, gantry cranes, reversing controls, and for crane and trolley travel, which turns process cranes into large-scale robots.
Intelligent sensor technology
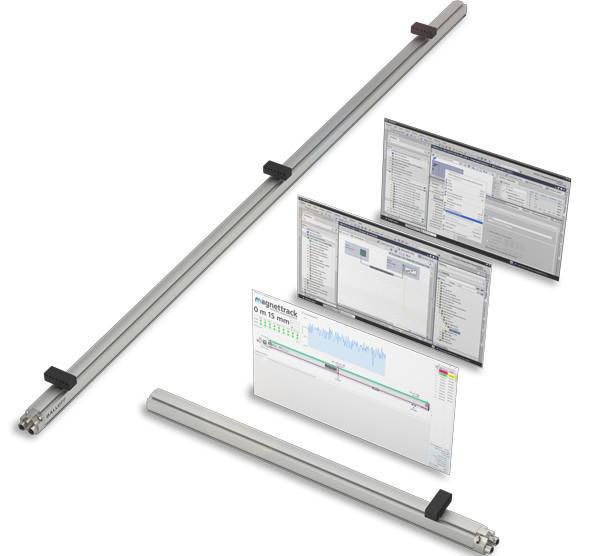
Long Distance Positioning System
The Long Distance Positioning System (LDPS) consists of a magnetostrictive position measuring system, with a Profinet interface, and several position encoders installed along the travel path of a crane, whose position is read by the magnetostrictive sensor mounted on the crane. This information is transmitted to the controller, which calculates the absolute coordinates of the crane position with high accuracy. In addition, you receive a software function block for easy integration into your control system. The S.C.A.D.A. visualization software is also included in the system.
The measuring system is also available with a fail-safe operating option with redundant markings along the travel path, which further increases the efficiency, reliability and quality of your application. The system is wear- and maintenance-free and is insensitive to shock, vibration and contamination.
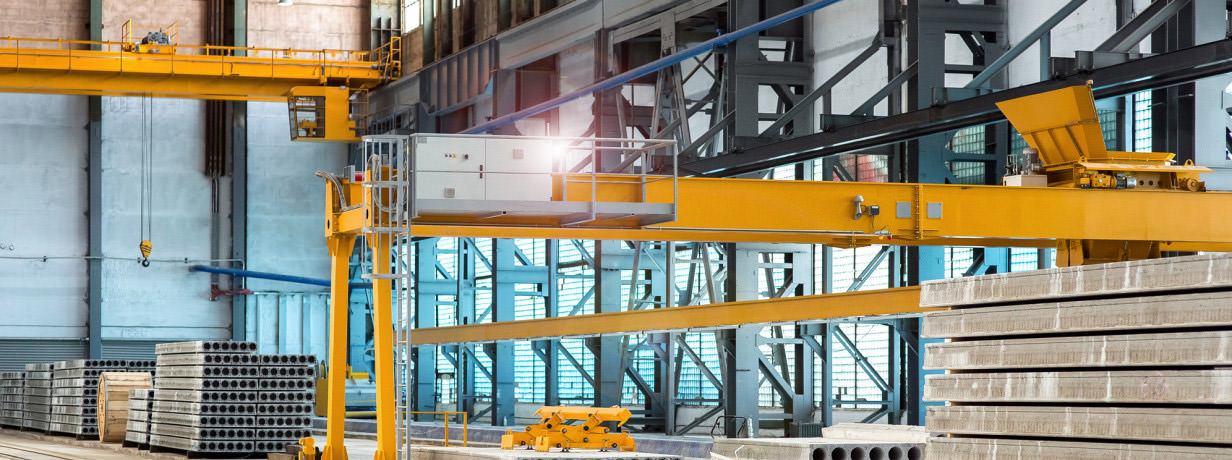
Long Distance Positioning System Overview
Long Distance Positioning System
Crane systems are used worldwide and across industries for transporting goods in intralogistics, in warehouse management or in various production processes. The loads here are often very high and the environment also places enormous demands on the sensor technology. In addition, the operator must always be aware of the absolute position of the crane or the control system.
This applies all the more if there are two or more cranes on one runway. For correct positioning and to avoid collisions of cranes, laser sensors are usually used, which meet common performance requirements under normal ambient conditions. However, if the level of contamination in a hall is high or if the cranes are operated outdoors, laser-based systems reach their limits.
Bang Kransysteme has put Balluff’s Long Distance Positioning System through its paces: “The distance measuring system, which travels with the crane and is approx. four meters long, detects the position sensors which are mounted along the travel path according to a predefined scheme and calculates the absolute crane position from this. If knowledge of this position is indispensable even under adverse conditions, the system is ideally suited,” summarised David Böttiger, Head of Automation.
Most important features and advantages at a glance
- Absolute linear position measuring system with a measuring range of up to several hundred meters
- Simple mounting
- The measuring section does not require a continuous rail, thus highest flexibility guaranteed
- High accuracy and reliability
- Low maintenance due to a non-contact and wear-free operating principle
- Resistance in harsh industrial environments (IP67)
- Automatic adaptation of the system to the magnetic marking
- Repeat accuracy up to ±0.5 mm
- Includes software function blocks for the Siemens PLC (required)