TechnologySeptember 21, 2023
Reduce industrial CO2 emissions via increased motion efficiency
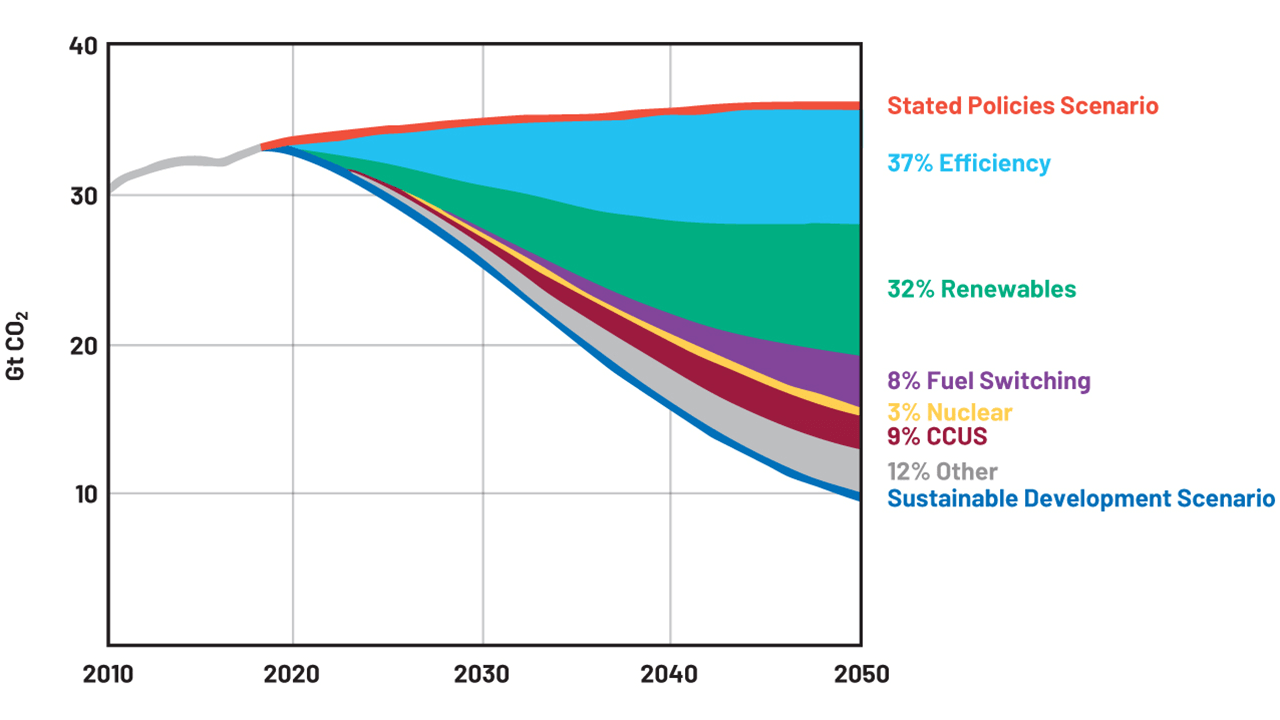
There is a great need to reduce industrial CO2 emissions. But the path to net zero will also create new opportunities for industrial manufacturing companies to embrace new technologies to accelerate lower carbon manufacturing. Increased industrial activity will also double the number of deployed motors in use by 2040.
Consumers today are looking for lower carbon products and services. Governments around the world are increasing regulations to reduce carbon emissions to meet their net zero greenhouse gas emissions targets.
Navigating the path to net zero will create new opportunities for industrial manufacturing companies to embrace new technologies to accelerate lower carbon manufacturing. This article will delve into two essential focal points to improve CO2 reduction in the industrial sector:
- Increased energy efficiency through increased deployment of motor drives
- The impact of digital transformation strategies to deliver increased manufacturing efficiency
The Paris Agreement in 2015 set out a plan to limit global warming to 1.5°C by 2050. Meeting the 1.5°C target in 2050 requires a >80% reduction in current CO2 emissions. The current trajectory is toward global warming of 1.9°C to 2.9°C, which will lead to a significant reduction in global GDP, displace up to 33% of the world population, and cost trillions of dollars in annual disaster-related losses.
The world has warmed by 1.1°C and experts say that it is likely to breach 1.5°C in the 2030s. The challenge to meet the 1.5°C target is significant. It will require a shift in investment away from fossil fuels and toward energy efficiency, renewables, and nuclear power generation as well as carbon capture, utilization, and storage (CCUS) along with other low carbon areas. Figure 1 outlines a path to the 1.5°C target by reducing CO2 emissions to 6 Gt CO2, as covered in World Energy Outlook 2019. This study includes two major sections: the Stated Policies Scenario and the Sustainable Development Scenario.
The Stated Policies Scenario considers only specific policy initiatives that have already been announced. The Sustainable Development Scenario describes a pathway that enables the world to meet climate, energy access, and air quality goals, and is fully compliant with the Paris Agreement. At the same time, it maintains a strong focus on the reliability and affordability of energy for a growing global population. The largest reduction in CO2 emission identified as part of the Paris Agreement is efficiency at 37%. Global energy-related CO2 emissions grew by 0.9% in 2022, reaching a new high of over 36.8 Gt. Emissions from industry declined by 1.7% to 9.2 Gt in 2022. With 25% of CO2 emissions coming from industry in 2022, accelerating industrial energy efficiency investments will be a key part of the path to net zero emissions in 2050.
Higher efficiency motors can reduce industrial CO2 emissions
The global electricity supply in 2022 was 28,642 terawatt-hours, contributing 13.6 Gt of carbon emissions (36% of global CO2 emissions in 2022). Industry consumes 30% of global electricity, with electric motors making up 69% of power consumption. With ~450 Mu of motors installed in the industry and ~52 Mu new motors installed in 2022 (split between brownfield upgrades and greenfield developments), higher efficiency motion assets are reducing electricity consumption and CO2 emissions. Motors are used across industrial applications to drive pumps, fans, compressed air systems, material handling, processing systems, and more. It is estimated that if all deployed motor driven systems were operated at maximum efficiency, it would reduce global electricity demand by 10% and remove 2490 Mt of CO2 emission in 2030.
Increased energy efficiency with deployment of motor drives
The most basic and lowest efficiency motion solutions are based on a grid-connected or AC-powered, 3-phase motor that uses a switchgear to provide on/off control and protection circuitry. These basic motion solutions run at a relatively fixed speed, independent of any load variation.
Adjustments in output variables (such as fluid flow in pumps and fans) are implemented with mechanical controls such as throttles, dampers, and valves, and significant speed changes are implemented with gears. It is estimated that 70-80% of all deployed motors today are grid connected and would benefit from being connected to an inverter or variable speed drive to reduce energy consumption.
The addition of a rectifier, DC bus, and a 3-phase inverter stage creates an inverter with variable frequency and variable voltage output that is applied to the motor to enable variable speed control. This inverter driven motor significantly reduces energy consumption by running the motor at the optimum speed for the load and application. Examples include higher efficiency pumps and fans. When added to the existing motor of a pump, fan, or compressor, an inverter can typically reduce power consumption by ~25%.
For higher performance motion control applications, a VSD enables accurate torque, velocity, and position control. To achieve this, current and position measurement are added into the basic open-loop inverter drive. Conveyors, winding, printing, and extrusion machinery are typical examples of these applications. It is estimated that between 20% and 30% of all deployed motors in industry are inverter driven or connected to a VSD. By moving more deployed motion assets from grid-connected motors to inverter driven or VSDs, we can significantly reduce the energy consumption and CO2 emissions of the ~450 Mu of motors deployed in industry.
The important role of motor energy regulations
Intelligent motion control solutions are delivering and will continue to deliver significant reductions in energy consumption by moving more applications from fixed speed motors to high efficiency motors and VSDs, in part driven by energy efficiency regulations.
This reduction in energy consumption will enable more sustainable manufacturing with reduced CO2 emissions. To accelerate the deployment of higher efficiency motor driven systems, the International Electrotechnical Commission (IEC) has contributed to the definition of energy-efficient electric motor standards. This includes the IEC 60034-2-1 test standard for electric motors and the IEC 60034-30-1 classification scheme comprised of four levels of motor efficiency (IE1 through IE4). These standards have made it easier to compare efficiency levels between motor manufacturers.
They also provide a reference for governments to specify the efficiency levels for their minimum energy performance standards (MEPS), helping countries to meet their energy efficiency and carbon dioxide emissions targets.
IEC 60034-1 Efficiency Classes:
- IE1 Standard Efficiency
- IE2 High Efficiency
- IE3 Premium Efficiency
- IE4 Super Premium Efficiency
Significant progress has been made by governments worldwide to set MEPS for motors. Since 2020, countries consuming 76% of global electric motor system electricity have introduced MEPS for motors at either the IE2 or IE3 level, contributing to reduced industrial electricity consumption. In the EU, since July 1, 2021, a minimum efficiency class of IE3 (Premium Efficiency) is required for motors from 0.75 kW to 1000 kW. A minimum of IE2 (High Efficiency) is required for smaller motors from 0.12 kW to 0.75 kW. Starting July 1, 2023, the MEPS will increase to IE4 (Super Premium Efficiency) for motors between 75 kW and 200 kW in the EU.
When we look at the total cost of ownership of a motor driven system over the life of its deployment, 70% of the total cost is electricity compared to 5% for the purchase of the motor and 20% for the maintenance of the motors. Therefore, by deploying more efficient motion driven systems, we can significantly reduce the operation cost of industrial motors while also reducing CO2 emissions.
Digital transformation strategies deliver manufacturing efficiencies
VSDs use data from voltages, currents, position, temperature, power, and energy consumption combined with external sensors for monitoring vibration, and other process variables. With a converged information technology/operating technology (IT/OT) Ethernet network, motion applications are networked together communicating data and motion insights to cloud-based data storage or on-premises storage.
Motion data and insights are more accessible and can be analyzed by powerful cloud computing and artificial intelligence to optimize manufacturing flows, reducing the energy consumption and CO2 emissions created in manufacturing. Access to motion insights extends equipment lifespans, improves manufacturing quality, and reduces unplanned downtime and material wastage while increasing safety in plants.
Motor driven systems are now integrating advanced sensing, signal processing, edge AI, and connectivity solutions to create motion data and insights at the Intelligent Edge. These new insights are communicated to the manufacturing execution system (MES). The MES can then identify deployed motors that are being operated significantly below their nominal rated output, resulting in underutilization and increased electricity consumption. Another critical capability is identifying deployed motors that operate too near to or slightly above their rated output, which also results in increased electricity consumption and potential lifetime issues. In a large manufacturing installation with several hundred to several thousand motors deployed, digital transformation strategies are especially crucial to reducing electricity consumption and CO2.
World Economic Forum— Sustainable Lighthouse Network
The World Economic Forum’s Shaping the Future of Advanced Manufacturing and Value Chains platform has set up the Global Lighthouse Network, which recognizes top leaders in manufacturing as lighthouses. The World Economic Forum’s Global Lighthouse Network showcases real-world examples of how digital transformation strategies are accelerating the reduction of CO2 emissions in industry. It is a community of manufacturers using advanced technologies to drive new innovations in smart manufacturing to increase productivity and sustainability. As of January 2023, the Global Lighthouse Network comprises 132 manufacturing sites worldwide, including 13 sustainability lighthouses. Schneider Electric’s Le Vaudreuil factory is one of the sustainability lighthouses at the forefront of digital transformation. The Le Vaudreuil facility has demonstrated the impact of data-driven insights to catalyze more sustainable manufacturing by:
- Reducing power use by 25%
- Reducing material waste by 17%
- Reducing CO2 emissions by 25%
Conclusion
The path to net zero will create new opportunities for industrial manufacturing companies to embrace new technologies to accelerate lower carbon manufacturing. Increased industrial activity (almost half of which occurs in China and India) will double the number of deployed motors in use by 2040.
Therefore, the CO2 reduction impact and the business opportunity size for new higher efficiency motor driven systems will increase significantly. At Analog Devices, we are fully dedicated to driving automation toward a more sustainable and efficient future. Our advanced technologies and solutions are designed to support the next generation of manufacturing systems, focusing on improving every level of efficiency from precise motion control and seamless connectivity to enhanced insights and analytics at the edge.