TechnologyJuly 16, 2024
Revolutionizing Precision: The Role of IoT in Modern CNC Technology
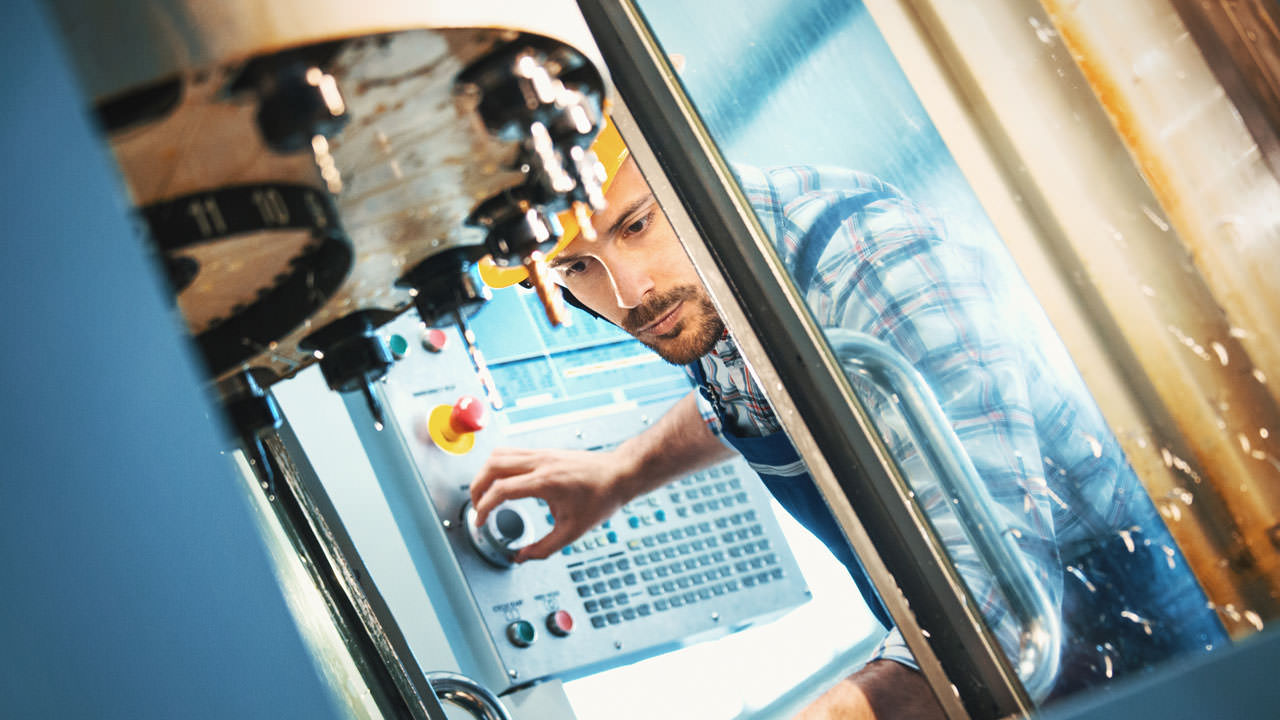
IoT's integration into CNC machines promises unprecedented levels of efficiency and precision, reshaping traditional manufacturing processes. This article delves into how IoT elevates CNC technology, detailing its benefits, applications, and the challenges it brings.
The fusion of the Internet of Things (IoT) and Computer Numerical Control (CNC) technology represents a transformative evolution in manufacturing, enhancing not only machine operations but also the entire production landscape.
What is IoT?
IoT refers to a network of interconnected devices that communicate and exchange data without human intervention. By embedding sensors and software in physical objects, IoT breathes intelligence into them, enabling automated and more efficient processes.
This technology is not limited to smart homes and consumer devices; it’s making significant inroads across various sectors, including manufacturing, healthcare, and transportation, by offering smarter, data-driven insights.
What is CNC technology?
Computer Numerical Control (CNC) technology brings automation to machining processes such as drilling, milling, and turning through precise computer directives. CNC machines are prized for their accuracy, reliability, and ability to produce complex geometries with minimal human oversight. As a staple in modern manufacturing, CNC technology’s adaptation to IoT is not just innovative but necessary for a competitive edge.
How does IoT enhance CNC technology?
IoT’s role in CNC operations unlocks several transformative features:
- Real-time data monitoring: Continuous feedback from CNC machines allows for immediate adjustments and enhanced monitoring of production activities.
- Predictive maintenance: IoT enables predictive analytics to forecast machine failures before they occur, reducing downtime and maintenance costs.
- Remote operation capabilities: Operators can manage and troubleshoot machines from remote locations, enhancing operational flexibility.
- Enhanced precision and automation: IoT integration facilitates finer control over CNC machines, increasing the precision of operations without additional human intervention.
Benefits of integrating IoT with CNC Machines?
Integrating IoT with CNC machines brings numerous advantages:
- Increased efficiency: Automated processes and optimized machine use reduce idle times and enhance throughput.
- Reduced operational costs: Efficient resource use and preventive maintenance cut down costs significantly.
- Improved safety: Enhanced monitoring helps in identifying and rectifying potential safety hazards, ensuring safer workplace environments.
- Enhanced data collection and analysis: IoT provides a wealth of data that can be used to refine processes and improve product quality.
Challenges integrating IoT with CNC?
While the integration of IoT with CNC technology offers extensive benefits, it also presents several challenges:
- Security risks: Increased connectivity exposes CNC machines to potential cybersecurity threats, necessitating robust security measures.
- Integration complexities: Merging IoT with existing CNC systems can be complex and costly, requiring significant technological adjustments.
IoT-enabled CNC applications in various industries
The application of IoT-enhanced CNC technology spans several industries, significantly impacting:
- Automotive: Streamlining production lines and improving component precision.
- Aerospace: Enabling the manufacture of complex, lightweight components critical for aerospace applications.
- Consumer Electronics: Enhancing the efficiency and precision of electronic component production.
- Healthcare: Improving the fabrication of medical devices and equipment with higher precision and control.
Case Studies: Success Stories of IoT in CNC
Several industries have seen remarkable success with IoT in CNC, including:
- Automotive: Major car manufacturers have integrated IoT to optimize their machining processes, resulting in reduced production times and improved quality.
- Aerospace: Aerospace giants use IoT for CNC machining in the aerospace industry to produce more reliable and precise components, pushing the boundaries of aviation technology.
Core components of IoT in CNC machines?
Key components of IoT in CNC include:
- Sensors and actuators: Collect data and act upon it to adjust operations in real-time.
- Data analytics platforms: Analyze the vast amounts of data generated to enhance decision-making.
- Network connections and protocols: Facilitate the seamless transfer and communication of data across devices.
- User interfaces and control systems: Allow operators to interact efficiently with IoT-enhanced CNC machines.
Future trends: where is IoT in CNC heading?
Emerging trends in the integration of IoT in CNC focus on:
- Increased adoption of AI and machine learning: These technologies are expected to further enhance automation, making CNC machines more intelligent and self-sufficient.
- Market growth: As industries continue to realize IoT’s potential benefits, its adoption in CNC processes is set to increase, driving significant market growth.
Step-by-step to implementing IoT in CNC technology
Implementing IoT in CNC involves:
- Assessment and planning: Evaluate current CNC capabilities and define IoT objectives.
- Choosing the right technology and partners: Select appropriate IoT technologies and collaborate with experienced partners.
- Implementation process: Integrate IoT devices and software into existing CNC systems.
- Monitoring and maintenance: Continuously monitor the system and perform regular maintenance to ensure optimal operation.
Best practices for IoT security in CNC?
To ensure safe IoT operations in CNC, consider:
- Robust authentication and encryption protocols: Secure all data exchanges to prevent unauthorized access.
- Regular security audits: Conduct frequent security checks to identify and mitigate potential vulnerabilities.
Conclusion
The integration of IoT into CNC technology is not just an enhancement—it’s a revolution. With its ability to bring real-time data, predictive analytics, and enhanced operational control, IoT is set to redefine the landscape of modern manufacturing. As this technology continues to evolve, its impact on CNC technology promises even greater efficiencies, pushing the boundaries of what’s possible in manufacturing.