TechnologyMay 27, 2019
Selecting a partner for connectors and cable assemblies
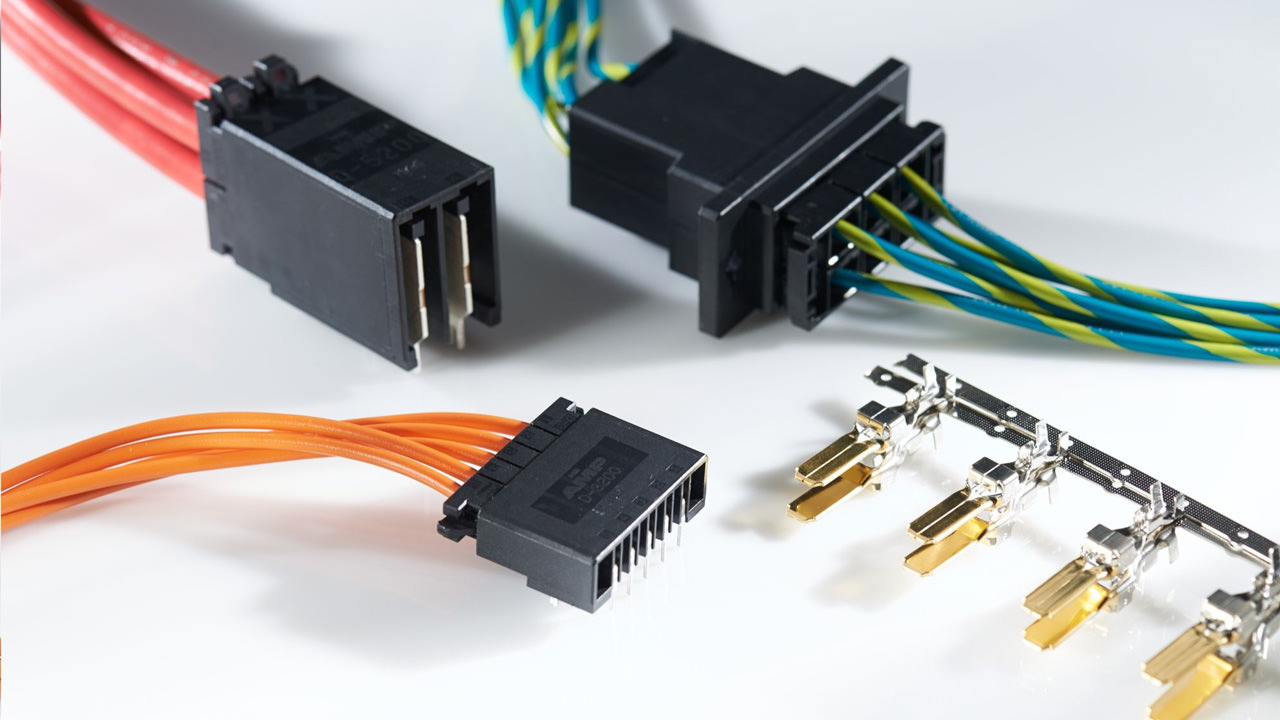
Development of cable assemblies is not as simple as would appear at first glance. However, it can be completed quickly and cost-efficiently by choosing the right partner. Early involvement of a partner during the design phase is essential, so the process can be optimized technically and from a sourcing perspective.
Many companies in the mechanical engineering industry, or even large OEMs in the equipment manufacture sector, follow a simple approach when it comes to deciding on cable assemblies. An interface is defined in engineering for data, power or signal applications at a connector level, with the decision often centering solely on technical factors (electricity, voltage, protection rating, etc.) as well as the availability of a connector in the company. This connector specification, together with the cable requirements, is then passed on to cable assembly manufacturers to create the cable assembly, or production takes place in-house. By choosing the right partner, this process can be optimized both technically and from a sourcing perspective.
Cable assembly requirements
Which requirements should a cable assembly manufacturer essentially fulfill? Apart from the basic market requirement of competitive and cost-optimized cable assembly, manufacturers should also offer the following features:
Speed: As the production landscape becomes increasingly automated, speed is a key factor along the entire process chain. This means that the faster a manufacturer can convert a customer’s requirements to finished products the better.
Accessibility: Accessibility and direct access to the relevant manufacturer’s engineering teams make it easier to process the technical queries and change requests that arise in the development process and in the product life cycle.
Quality: Full quality assurance of the complete cable assembly process is vital and virtually standard market practice meanwhile. This means that compliance with recognized ISO standards (EN ISO 9001 for quality management systems, etc.) is becoming a basic prerequisite, in addition to quality standards in specific sectors, such as the automotive, rail or aerospace, marine and defense industry, which are also required to a degree. Having an environment management system in place is therefore an advantage in this respect.
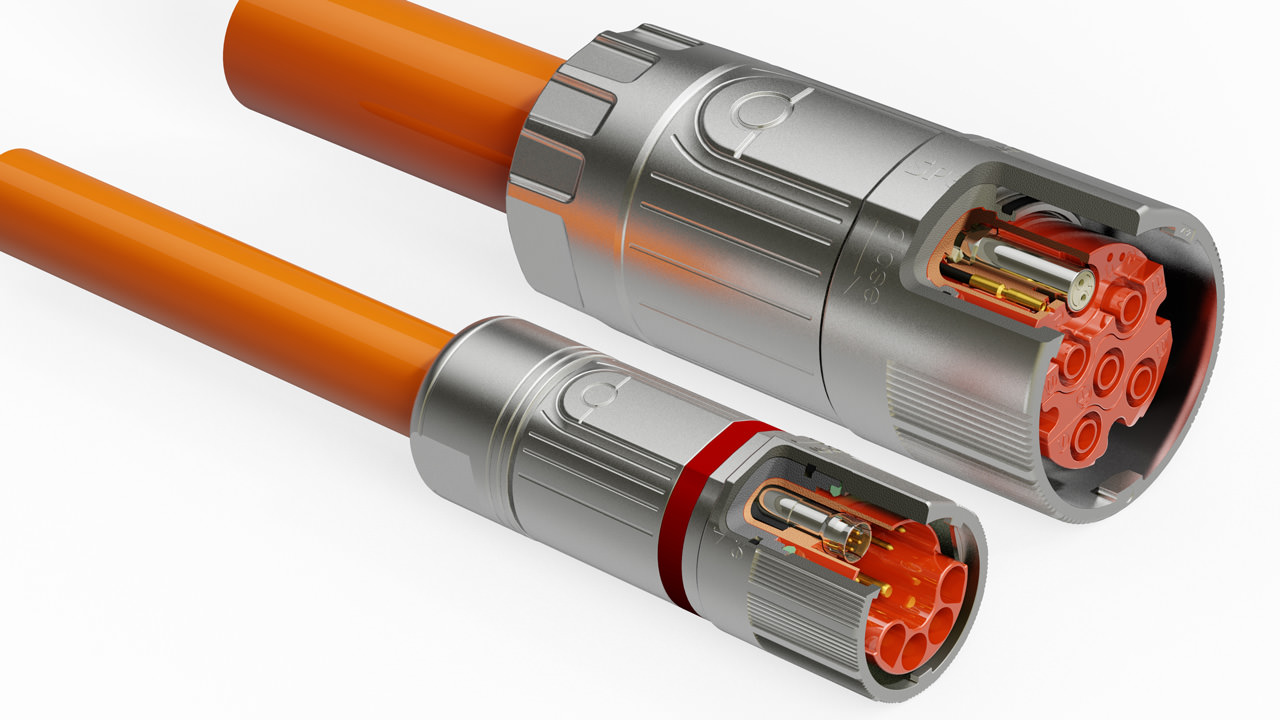
Connector and cable assemblies.
Advantages with cable assemblies
One of the advantages of large connector companies that also offer cable assembly lies in the product portfolio. An extensive connector portfolio allows a broadly diversified solution offering of cable assemblies, without having to fall back on components from competitors. This often offers availability and cost benefits for end customers.
Another aspect in this regard is that connector manufacturers are able to incorporate custom connector solutions into the cable assembly, because they possess the engineering capabilities. Connector customization is therefore another option to improve the performance of cable assembly and helps to create tailored solutions for practically any customer application. Examples would include adding (over) molding, and changing material to improve technical features or even designing and developing a completely new connector.
The solution expertise for developing technical and cost-efficient cable assemblies is closely linked with a level of engineering know-how. It is only possible to design cable assemblies for the long term with a suitable pricing structure, if the engineers have a deep knowledge of the right connection technology and electromechanics, as well as a broad understanding of cable design and design-to-cost.
One aspect that should not be neglected in this respect is the financial security offered by a cable assembly manufacturer. Should it happen, despite all the quality assurance measures mentioned above, that a product recall is necessary because an installed cable assembly is faulty, the importance of a good financial standing on the part of the cable assembly manufacturer quickly becomes evident.
Small companies may only be able to absorb the high costs associated with a global recall to a limited extent, and these costs can sometimes even lead to the financial collapse of the company. Costs may continue to arise for the manufacturer, however, after such a collapse, which can then no longer be passed on to the cable assembly manufacturer. The probability of such a scenario arising with a financially strong global player in the connector industry is very low.
In addition, the one-stop-shop approach described (connector supplier is also the cable assembly manufacturer) offers advantages in terms of price negotiations for purchasing. The increased sales volume as a result of the centralization improves the negotiating position for the customer and offers the opportunity to negotiate better terms and conditions for overall packages with just one supplier.
If the cable assembly manufacturer is also active internationally in this scenario, further advantages can be generated. Such advantages are attributable, for example, to global supply chain solutions. A globally active company can offer warehousing on every continent and therefore a high level of failsafe reliability as well as a standard delivery time practically anywhere in the world.
If the global footprint not only extends to warehousing then, rather also includes production and engineering, the added value increases additionally if the customer is likewise globally active. Engineers can therefore develop the solution locally in real time on the object itself. The local content, which is often required especially in rail applications or prescribed in part in the project context, can then be generated more easily.
In addition to the hard technical facts and the price, other factors are also increasingly playing an important role in deciding which cable assembly manufacturer to choose. Economical resource management together with consideration of health and safety aspects at the workplace can be a swift indicator of which companies take their social obligations seriously. As attention focuses increasingly on the points mentioned above, it goes without saying that these requirements have to be fulfilled by all production locations around the globe.
Achieving process improvements
How can the previously mentioned advantages of large connector manufacturers, which also supply cable assemblies, be utilized in order to improve the existing procedure for introducing cable assemblage? There are three main points of note here, which allow a positive result to be achieved:
Early integration of the cable assembly manufacturer’s engineering department in the development process allows solutions to be found quickly based on the latest connector and production technologies.
If it is possible to discuss interfaces openly, then the manufacturer’s entire portfolio can be used without restricting the potential performance of the assembly owing to any pre-screening.
And if it is then also possible to abolish restrictions in the bill of materials (BOM) and have 1:1 alternatives on the part of the manufacturer considered in the design-in, a best possible design-to-cost is ensured, since the manufacturers can take account of cost advantages of own products in the cable assemblage offer.
Products: generalist vs specialist?
The product portfolio can be used as a decision-making aid to ensure the right choice of partner long term in the area of cable assembly. It helps in this context to answer the question as to whether the connector manufacturer is more of a generalist, so a provider of connectors in the most varied applications, or a specialist that focuses on one market segment / application. The ideal partner for manufacturing cable assemblies combines both attributes in one.
Generalist:
- Broad portfolio of connectors for the widest range of applications. Example: circuit board connectors through to heavy-duty industrial connectors or hybrid circular connectors.
- Extensive product and engineering know-how allows solutions to be developed for a variety of applications without limiting attention to specific segments or predefined technical solutions.
Specialist:
- Specific portfolio of connectors for “one” application. Example would be a clean room connector.
- Expert know-how in terms of the application and identifying solutions at connector level as well as cable assembly.
From standard assembly to customer-specific harness?
Another aspect to be considered when choosing the right partner is the range of solutions offered in the area of cable assemblies, since there are different levels of complexity in this regard too:
Standard assemblies: An assembly is based on a standardized interface (e.g. RJ45 or M12 connector) and is offered in different lengths as standard (partly ex stock). These standard assemblies are offered by any number of manufacturers and the effort involved in sourcing as well as in engineering is negligible.
Point-to-point assemblies: A point-to-point connection is manufactured with a cable assembly in this case, though it is important to know which connector and which cable is used. The coordination effort in engineering is higher since clear specifications that describe the assembly uniquely have to be exchanged.
Harness: The cable assembly consists of three or more connectors (same or different design), which are assembled to form a harness. The engineering effort is considerably higher since apart from the unique specifications, increased effort is required for testing and release. Increased effort is also required on the part of purchasing, since it is more difficult to compare different competitor offers owing to the increased complexity.
Value-added assemblies: This is the supreme discipline in the area of cable assembly, since subsystems are created here for machines and equipment. For example, a complete drag chain can be assembled by the cable assembly manufacturer for use in a machine.
This means that it is no longer only cables and connectors being used, rather also numerous additional components such as the drag chain, hoses for coolant or compressed air with a host of interfaces. The significantly increased complexity of these assemblies requires close and effective collaboration between the participating engineering departments as well as support in sourcing in order to achieve the best possible technical solution at the right price.
Cable assemblies are possible for practically every industrial application, with an entire array of connectors available in the portfolio. TE is also in a position to install products from other market players in its assemblies. These products are either procured directly from the manufacturer through special contractual arrangements or acquired through distribution channels. Practically every interface can therefore be linked with assembly work by TE Connectivity. This means the best possible service from a single source with the advantage of only having to deal with one partner for solutions in the area of connection technology.
Conclusion
Development of cable assemblies is not as simple as would appear at first glance, however it can be completed quickly and cost-efficiently by choosing the right partner. Early involvement of the cable assembly partner during the design phase of the equipment is essential. This ensures the design happens according the latest available connectivity solutions in the most cost-effective way.
Partners must fulfill a number of requirements in this respect in order to ensure that both the development and the procurement process function right down the line. The following checklist is provided to assist with the selection process and should provide support when reviewing your current suppliers or when choosing new business partners.