TechnologyMay 17, 2022
Single Pair Ethernet and Ethernet-APL moving ahead
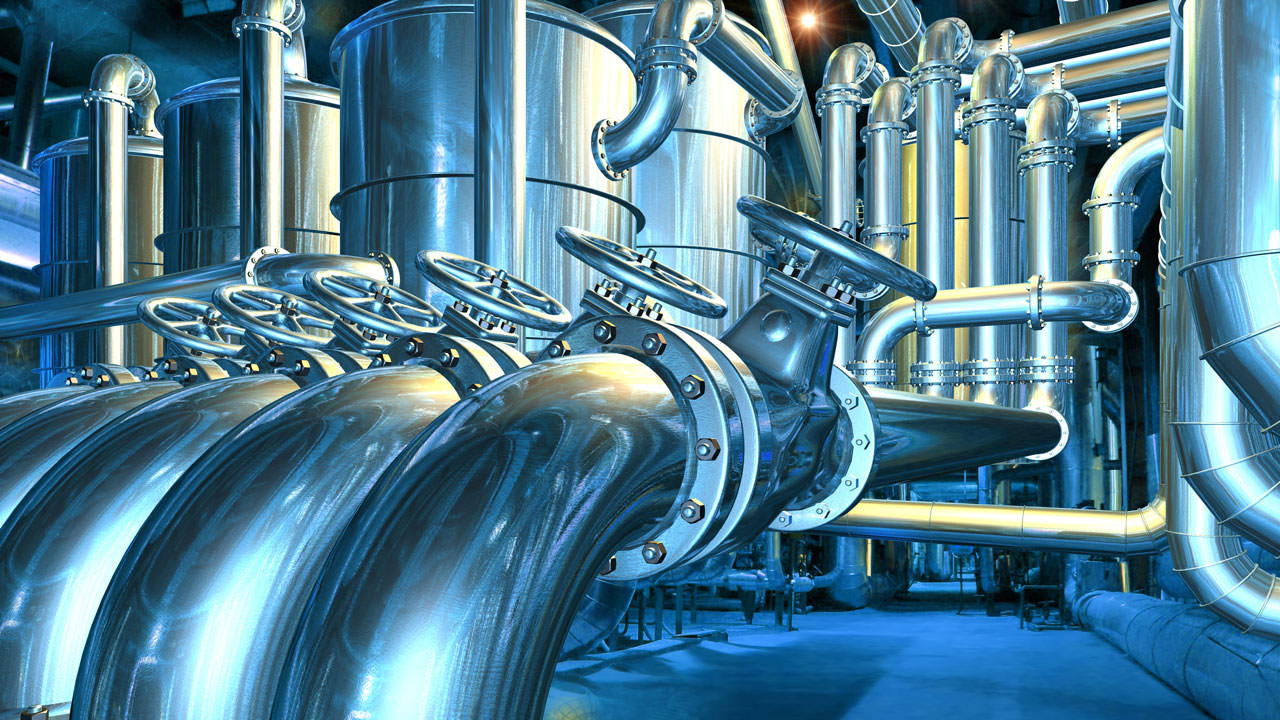
Industry experts provide their perspective on the development of Single Pair Ethernet and Ethernet-APL. Learn about the potential benefits and the work to be done to achieve what has become an ambitious vision that will ultimately shape the scope and future of Industrial Ethernet connectivity.
SINGLE PAIR ETHERNET and ETHERNET-APL are in the process of redefining Ethernet connectivity solutions. In this special report, IEB reached out to industry experts to get their insights into the development of SPE and Ethernet Advanced Physical Layer to gain their perspectives on the megatrends and applications shaping and enabling development of these important technologies.
The consensus of the group is that two-wire Ethernet solutions offer a broad set of benefits that are vital to achieving digital transformation and Industry 4.0 objectives.
SPE and Ethernet-APL are base technologies, for example, that offer possibilities for high speed data transfer compared to today’s analog or fieldbus solutions. Due to good transmission properties, even over longer distances, SPE optimally supports future-proof network communication. With the trend towards resource-saving, miniaturized devices, SPE offers more space for electronics thanks to space-saving cables.
Single Pair Ethernet (SPE) also allows for cost and size reductions in Ethernet PHYs, cable and connectors that enables cost effective connectivity for smaller devices. This opens up the possibility to connect simple devices to Ethernet that were previously only hardwired or controlled via fieldbus technology.
The list of potential benefits is long but there is still a lot of work to be done to achieve what has become an ambitious vision shaping the future of Ethernet connectivity.
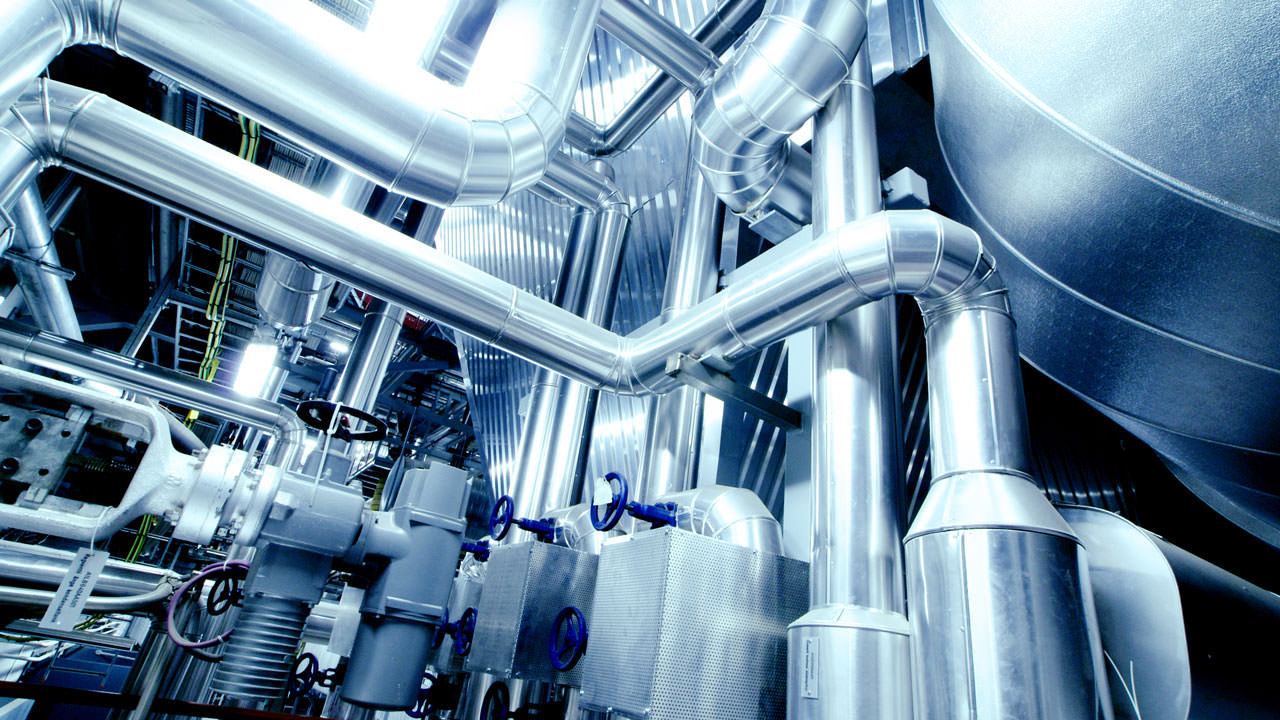
In process automation, many plants are equipped with 4-20 mA with HART or fieldbus installations. Both solutions have limited transmission speed and need conversion to be integrated into upper layers of the automation pyramid.
SPE and Ethernet-APL
High speed data transfers from the field
Today, everyone is talking about “Digitalization” and “Industry 4.0”. That means a lot of data from the field needs to be transferred to the upper layer of the automation pyramid in order to use digitalization for plant optimization and increasing productivity and efficiency.
“In order to digitally transform industry, adequate technologies should be in place to provide the amount of data from the field. SPE and Ethernet-APL are base technologies that give the possibilities to transfer data from the field in a very sufficient way with high speed compared to today’s Analog (4-29 mA) or fieldbus solutions,” Dr. Jörg Hähniche, project manager for the APL Project, told IEB recently.
From the process automation point of view, many plants are equipped with 4-20 mA with HART or fieldbus installations. Both solutions have limited transmission speed and need conversion to be integrated into upper layers of the automation pyramid.
“SPE and Ethernet-APL use the same easy installation technology as today; two wire for data transfer and power supply but with higher transmission speed and longer distances. In addition, because both are neutral Physical Layer solutions supporting Ethernet, any Ethernet based protocol can run on them. So, no conversion is necessary. SPE and Ethernet-APL now give the possibility to have access to data from the top to the field,” Hähniche said.
Networking impact
Hähniche said that both SPE and Ethernet-APL use switch technology. For Ethernet-APL in particular, two types of switches have been determined: both an APL Power Switch and APL Field Switch.
An APL Power Switch is able to provide the power for a segment that consists of APL Field Switches and up to 50 field devices. An APL Field Switch connects the field devices in the field. In Process Automation “field” means especially in hazardous, high explosive areas.
Because of the point-to-point connection between field devices and APL Field Switches, finding any problems in connectivity is easy since Field Switches are able to provide appropriate diagnosis information to the user.
Furthermore, Ethernet-APL uses existing cable specification – the so-called Fieldbus cable. That simplifies the introduction of Ethernet-APL because no specific cable needs to specified.
Focus on process industries
“Ethernet-APL has been developed specifically for the Process Automation industry. Standard Ethernet solutions cannot be used in the field of Chemical plants because of their specific requirements – protection against explosive atmosphere, long distance and 2-wire technology to connect field devices,” Hähniche added.
“Ethernet-APL meets these specific requirements and gives the possibility to bring all the advantages of Ethernet down to the field. Based on the high bandwidth (10 Mbit/s transmission speed) use cases can now be fulfilled that were not possible with fieldbus solutions. Since Ethernet-APL is a neutral Physical Layer any Ethernet-based protocol can run on it, also in parallel based on the high bandwidth.”
Based on the new technology, the access to the available information in the field is much easier than with today’s solutions. In addition, a further advantage is now the homogeneous network technology from top of the plant to the bottom (field). This makes the access to any information from anywhere very easy.
He added that, not only does Ethernet-APL offer advantages for the process automation industry, SPE in general brings a lot of advantages to building automation and factory automation. The 2-wire technology offers the possibility to decrease necessary space for connection equipment (smaller connectors, less space for connection interfaces) and the long distance (up to 1000m in non-hazardous areas) is useful for such industries.
“Sure, the new technology brings some challenges to the engineering. On the one hand the installation is very easy because of only two wires which needs to be connected to the field devices. Since the connectivity is polarity independent no special knowledge is necessary,” Hähniche said. “However, on the other hand the network needs to be planned. More effort is expected, e.g. number of devices per segment under consideration of power supply, different architectures (Star, Ring), redundancy and so on. For that reason, an Engineering Guideline has been developed for Ethernet-APL that helps to avoid mistakes during planning and installation of an Ethernet-APL network.”
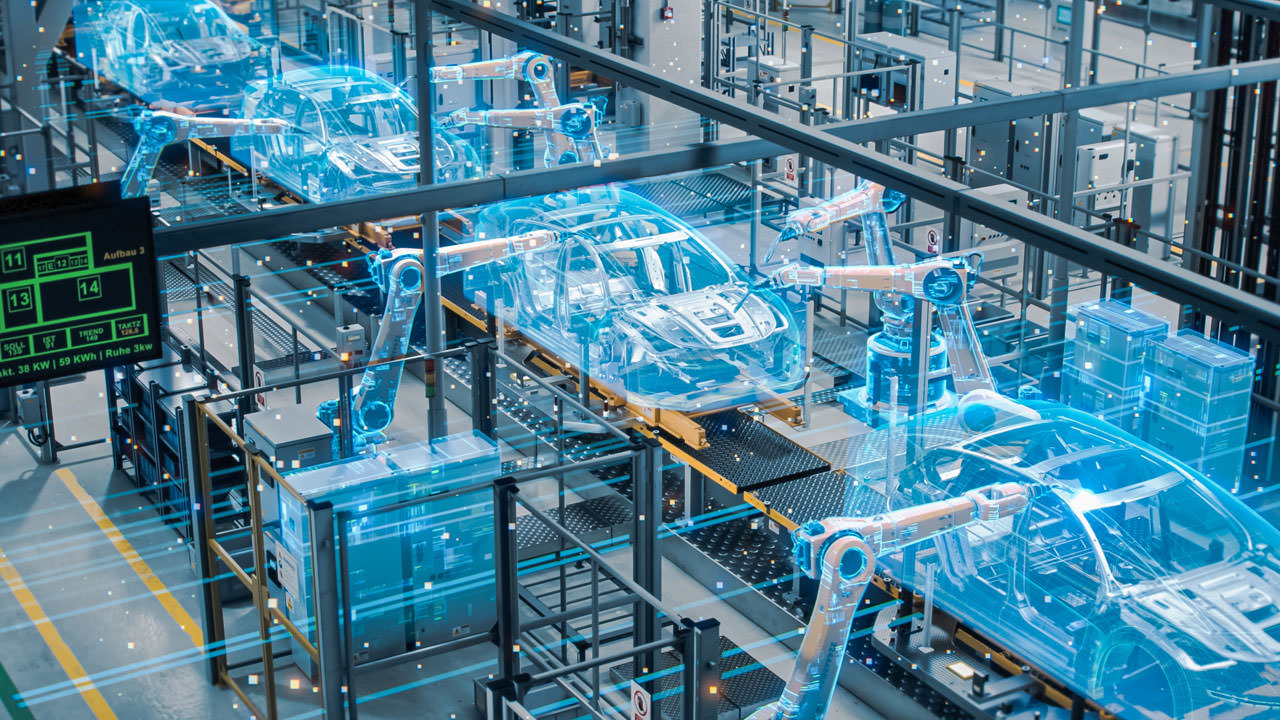
Automotive Ethernet simplifies cabling and saves weight. Many of these advantages can also be transferred to industrial applications.
Targeting industrial uses
Leveraging solutions in automotive Ethernet
According to Verena Neuhaus, Manager Product Management Data Connectors, Business Unit Field Device Connectors for Phoenix Contact, Single Pair Ethernet has already shown its strengths in the automotive sector. There they speak of automotive Ethernet and it was quickly recognized that a consistent communication protocol instead of many different fieldbus systems has many advantages.
On the one hand you save costs for gateways, on the other hand the Automotive Ethernet simplifies cabling and saves weight. Many of these advantages can also be transferred to industrial applications.
“The IIoT brings more and more communication participants who want to be networked with each other. And SPE brings many advantages in the field of industrial communication in this new networked world,” Neuhaus said. “On the one hand there is the miniaturization, the consistency of the communication protocol from the sensor to the cloud, the greater range of the Ethernet protocol of up to 1000m, but also the simplified cabling with only 2 wires and the possibility of energy transmission at the same time as the data.”
Technology trends
Neuhaus said that Single Pair Ethernet (SPE) can form the basis of all Ethernet-based communication. It opens up new fields of application and enables smart device communication.
“Due to its good transmission properties, even over longer distances, SPE optimally supports future-proof network communication. With the trend towards resource-saving, miniaturized devices, SPE offers you more space for your electronics thanks to space-saving cables,” Neuhaus said. “In the first step, the main incentives lie in the application area of sensor technology in order to close the gap in IP-based communication from the sensor to the cloud.”
She added that there are several different Ethernet standards that are being developed by different automation companies and the OSI layers need to be adapted to support real-time requirements. Some protocols are based on classic TCP/IP-based Ethernet, others modify layers 3 and 4, and still others require special hardware at the data link layer.
“All Ethernet variants are able to connect the shop floor in production environments the with the office networks and thus improve the performance, transparency and availability of the system. However, the complexity of Ethernet and the network topology as a daisy chain or switched network make it noticeably more difficult to integrate peripheral devices such as sensors and actuators. Single Pair Ethernet standardization efforts aim to close this gap and pave the way for a seamless, Ethernet-based IP network infrastructure,” Neuhaus said.
Application solutions
Neuhaus noted, as already mentioned, that Single Pair Ethernet has its origins in the automotive sector. With the many sensors installed in an automobile, the wiring harness became more and more complex and heavier due to the different fieldbus systems.
The advantages of a less complex cabling structure with single pair Ethernet and the resulting weight and cost savings as well as a consistent communication infrastructure can also be projected onto other areas of application.
“For industrial applications, the focus is on the areas of factory automation, building automation and process automation. Possible use cases in these areas can be found in applications such as mechanical engineering, robotics, sensor technology, but also in the building control of a smart building or in infrastructure applications such as traffic engineering,” Neuhaus stated.
She added that the Ethernet protocol has been established in the local data networks of the company and control levels for decades. With Single Pair Ethernet, data cabling is reduced to one pair of wires and the range is increased. This enables efficient transmission concepts at the field level – right down to the sensors. Corresponding switches and different sensors are currently being developed.
The high EMC requirements in the industrial environment and the implementation of simultaneous power transmission with PoDL (Power over Dataline) are challenges in the development process that should not be underestimated.
Even more network participants and components are required for the entire ecosystem of SPE. This is also the reason why Phoenix Contact is also promoting the topic of SPE holistically within the SPE System Alliance.
A worldwide association of almost 40 leading technology companies with the common goal of implementing and further developing the future-oriented Single Pair Ethernet technology.
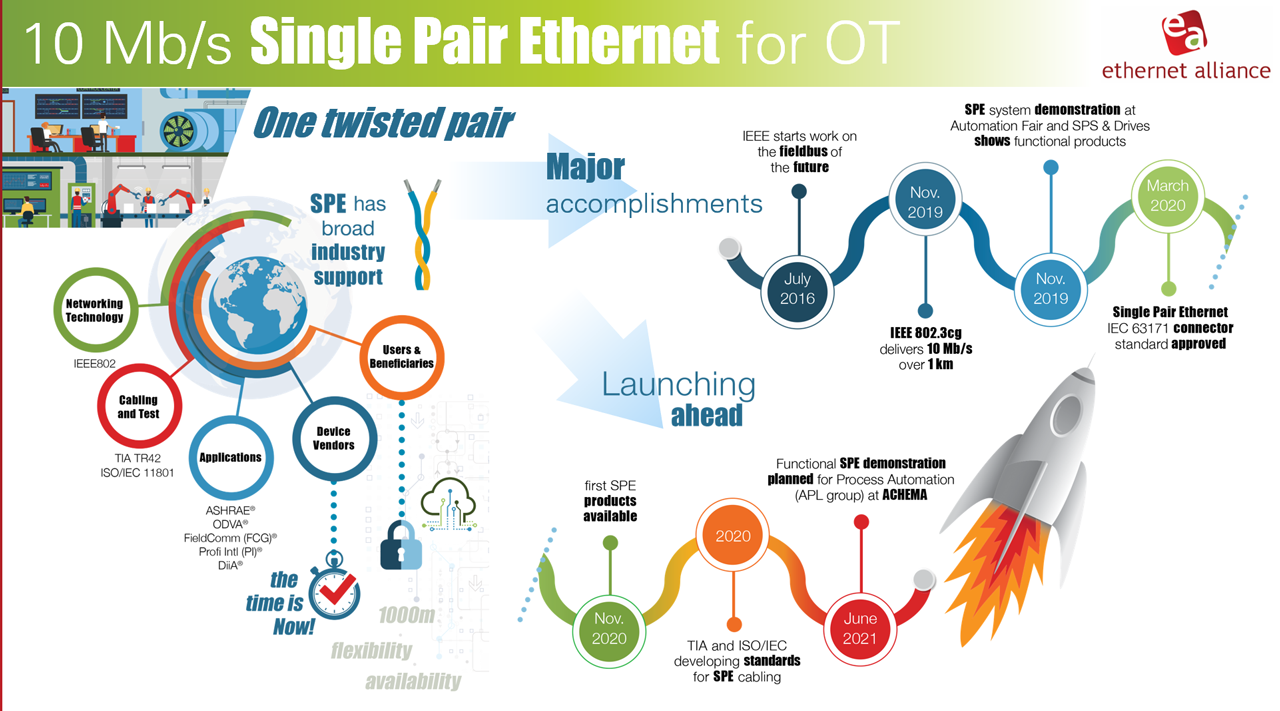
Single Pair Ethernet has been on a continuous development path but there is still more work to be done.
Uniform Physical Layer
Replacing legacy edge protocols
Bob Voss, Distinguished Engineer in PANDUIT Corporate Research and Development told IEB that Single Pair Ethernet (SPE) and Ethernet-APL are important technologies poised to advance automation and control networking solutions. While Ethernet-APL is a process industry optimized version of SPE, both Ethernet-APL and SPE are based on the formative IEEE 802.3cg standard.
“What both technologies do is create a uniform physical layer at the edge of industrial networks, capable of transporting all industrial Ethernet variants, nearly the ‘one ring to rule them all’ scenario,” Voss said. “When deploying SPE or Ethernet-APL, legacy edge protocols are replaced, upgrading the speed, performance, and security of the network edge. Also, as the network edge has become the final frontier for Ethernet, the ideal state of a single, seamless protocol from cloud to edge, is realized.”
Key technical benefits and trends are driving the move to Single Pair Ethernet and/or Ethernet APL technology, creating incentives that is influencing expected adoption rate among manufacturers.
“If you asked me the adoption rate question five years ago, I would tell you that Industrial networks have painfully slow refresh rates, often well more than 10 years. However, SPE and by extension Ethernet-APL, deliver important benefits,” Voss said. “As such, I expect the adoption rate to accelerate sharply. Coincident with gaining better cybersecurity, higher speed transmission, better data portability and ease of maintenance and deployment, SPE also addresses a serious business continuity risk for companies. The legacy protocols being replaced by SPE, and Ethernet-APL are old, slow and crabby like the engineers that support them. Kidding aside, the technical community that supports the non-Ethernet Industrial network edge today is old enough to retire. That factor alone puts the crosshairs on maintainability and reliability at the network edge and that should scare the heck out of businesses.”
“So, how do we accelerate the adoption rate? The control engineers I’ve just frightened need to make certain SPE and Ethernet-APL are on their favorite automation manufacturers’ development roadmaps. Progressive automation and IT companies are already doing so but don’t leave it to chance in your situation. Also, Ethernet-APL launched with a fair number of solutions and given its importance to the process industry, I expect solution development to ramp up sharply.”
Cabling and network topologies
Voss said that the development of single pair Ethernet (SPE) standards came from auspicious beginnings, in that the IEEE 802.3cg drew the attention and contribution of noted automation experts. Given the goal of replacing legacy protocols, physical layer topologies like long distance point-to-point links and trunk/spur links are accommodated in the standard. So, in some regard, its sort of “Back to the Future” in that we’re doing the old proven topologies with modern 10 Mb/s Ethernet.He added that Ethernet-APL is built for purpose. Part of the Ethernet-APL optimization of SPE includes optional PHY operating modes in the 802.3cg standard but it is also physically architected to permit operation in hazardous areas.
“Ethernet-APL uses the 10BASE-T1L PHY chip from the 802.3cg standard, retaining the ability to create links up to 1000 meters in length at 10 Mb/s. Power is handled differently than SPE, utilizing a separate power infrastructure to allow all the best safety methods to be included in device powering schemes,” Voss said. “Not to be repetitive but the chief advantage is a single, uniform physical layer that can support all Industrial Ethernet variants. Not too shabby …”
Impact on factory automation
Voss said that the target for SPE and Ethernet-APL is the edge of the network. That means sensors, drives, actuators, and the like. And fun fact for readers who don’t do Building Automation, but SPE solves the same problem in buildings that it does for industrial setting. It creates a high performing Ethernet edge. Remarkably, a lot of the same topologies appear in building edge networks that we use in industrial edge networks. It’s not designed to cannibalize 4-pair Ethernet applications elsewhere in the network.
By putting the whole network on Ethernet, there’s a single protocol across the entire enterprise, cloud to edge. That makes ALL data infinitely transportable. It makes federating a wide variety of data fast and easy. That augments decision speed and quality. And really IoT isn’t about getting all new data, its about getting the “nice to know” data in context with the mission critical data we already collect to make the business run better.
“Since I’ve already touched on IoT, SPE is also an IoT enabler. A number of pilot IoT applications proved their worth using battery-powered wireless sensors. A valuable means to quickly achieve a proof of concept but not a physical layer application that scales effectively. Enter SPE. Its simple to connect 2-wire cabling, 10 Mb/s transmission speed and ability to deliver device power make it an ideal IoT enabler that does scale,” Voss said.
He added that one drawback to legacy cabling is the lack of methodology to diagnose and debug problems in the physical layer without connecting and simultaneously debugging devices. This is a significant gap, since there is evidence that physical layer shortcomings make up a sizeable share of communication problems in serial networks. With SPE also comes standards and equipment that allows for validation of the installed system. This process has been well established for enterprise Ethernet connectivity, and provides confidence to end users that their installed cabling – which often make up the largest share of the cost – can support both short-term serial/analog applications as well as long-term APL and SPE upgrades.
What are the engineering challenges that the newest solutions are designed to address? Voss said that, first and foremost, there is an ability to support proven edge topologies.
“The value of a new technology diminishes rapidly if you must completely change the way you do the work. This objective also makes SPE a backwards compatible technology in that it may support the reuse of electrically healthy Fieldbus cables for SPE,” Voss said. “While not a certainty, it something that can quickly be determined with the help of test instrumentation. What we’re finding in laboratory testing at the Panduit Innovation Center is not all Fieldbus cable works. We have tested cable variants that, on paper, look like they’d work just fine for SPE but that assumption is not borne out by the performance testing.”
Secondarily, he added that SPE is lightweight. There’s not a lot of compute power required in the device for SPE. It operates happily with TCP/IP or UDP stacks. In fact, there are some excellent technical papers presented by ODVA in a category called “constrained devices” on the ability of SPE operating with UDP and supporting fully functional instantiations of EtherNet/IP.
“Finally, the creation of Ethernet-APL standing on the shoulders of SPE to bring Ethernet to edge industrial networks located in hazardous environments. That is a significant engineering challenge, elegantly overcome,” he concluded.
On the one hand you save costs for gateways, on the other hand the Automotive Ethernet simplifies cabling and saves weight. Many of these advantages can also be transferred to industrial applications.
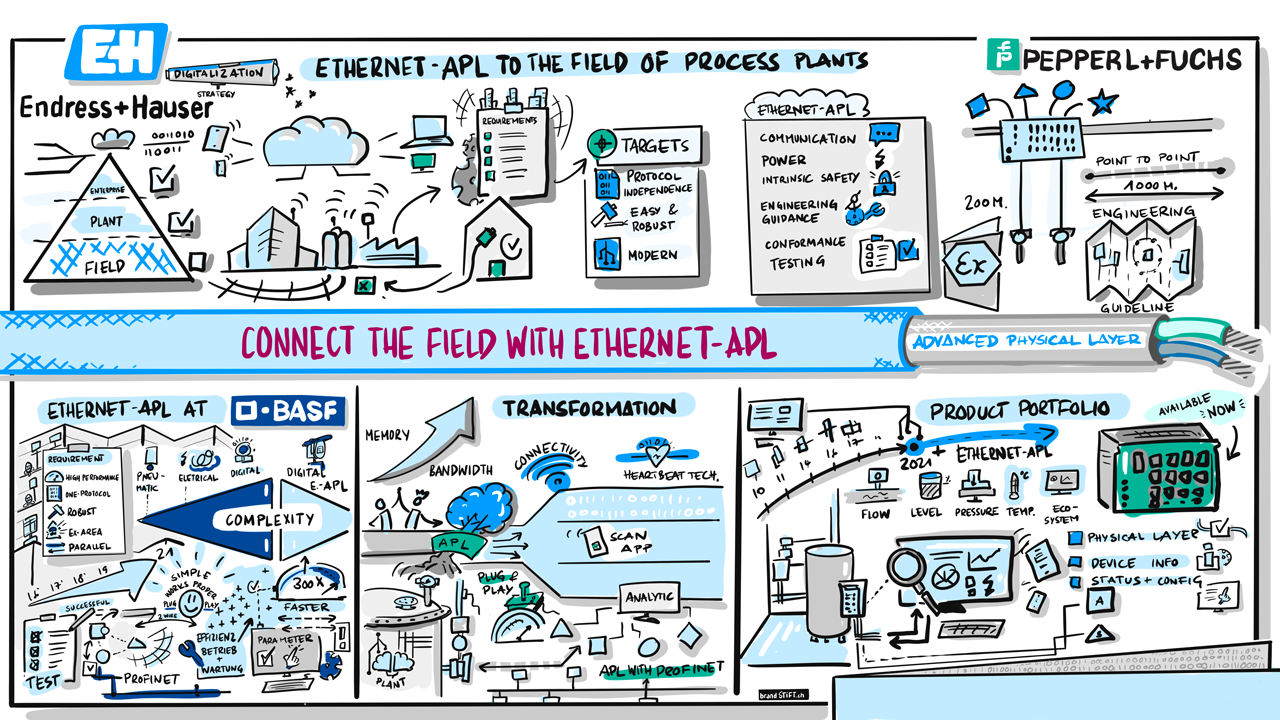
Single Pair Ethernet has been on a continuous development path but there is still more work to be done.
Ethernet in the field
Enabling digitalization and data-driven applications
According to Benedikt Spielmann, Marketing Manager Industrial Communication at Endress+Hauser Digital Solutions, Single Pair Ethernet and Ethernet-APL are important technologies advancing new solutions for automation and control networking.
“The field level is typically equipped with 4-20mA analogue technology for many decades. The HART protocol above is mostly used for configuration or troubleshooting only. Digital fieldbuses could never really replace the analogue technology due to complexity in engineering and troubleshooting, protocol conversions, difficult driver allocation, etc.,” Spielmann told IEB recently.
“In terms of digitalization and data-driven applications for Industry 4.0, a seamless data access for upper layer applications is crucial to unlock the data of smart instruments. Traditional technologies have limitations to meet this and have poor performance for transferring a large amount of data.”
Spielmann said that, in industries without hazardous areas, Ethernet-enabled 4-wire field devices have been successfully established for many years. With SPE technology, it will also be possible to provide typical 2-wire devices with Ethernet. This will make it feasible to integrate all field instruments into the Ethernet network, with full data access and without protocol conversions.
“For heavy industries with hazardous areas, a special adoption of SPE enables the use of Ethernet in the field level including intrinsic safety: The Advanced Physical Layer for Ethernet. Ethernet-APL brings Ethernet to the field level with power and data over the same 2-wire cable, enabling seamless data access and high performance for upper layer applications,” he added.
Technology benefits
Spielmann’s point of view is that two-wire Ethernet technology brings Ethernet to the field level, enabling one single network technology across all levels of the automation pyramid. And a major benefit of such a consistent network is the seamless data flow from the field level to upper layer applications.
“With traditional technologies we are always faced with complex protocol conversions through different infrastructure components of different vendors. This makes it nearly impossible to enable data-driven applications which are getting more important in the context of digitalization and Industry 4.0,” he said.
“Also standardized concepts and use cases as defined in NAMUR Open Architecture need the data flow from the field level and the appropriate performance for the data transfer. Daily work orders of maintenance personnel can be much more efficient. Just imagine a parameter upload or download in some seconds per device instead of several minutes as known from HART protocol today. By multiplying this increase in efficiency by hundreds of devices in a plant, a real cost benefit can be calculated.”
With the first APL field switches already available on the market, Endress+Hauser devices for all relevant measuring principles like flow, level, pressure, temperature but also actuators will be launched during 2022. This means that first real projects can start this year.
Impact of SPE
According to Spielmann, networks implementing Ethernet-APL or SPE are highly flexible and scalable. With Ethernet-APL for instance it is possible to set-up ring topologies with several APL Field switches. Thanks to features like the media redundancy protocol in the PROFINET context, a cable break between the APL field switches has no impact on the process as the communication will continue via the other way of the ring. Cables between the APL field switches can be selected depending on the application.
Either cheaper copper cables are possible with a maximum cable distance of up to 100 meters and 100Mbit/s or more expensive fiber optic can be chosen with cable distances of up to 2 kilometers and even higher data rates.
The connection between APL field switches and APL field instruments is always point-to-point which simplifies troubleshooting on the network, especially compared to fieldbus architectures. The preferred cable for these so-called spur lines is the Fieldbus cable type A which is specified in IEC 61158-2. With such a cable it is possible to reach maximum cable distances of up to 200 meters, even with intrinsic safety in all zones or divisions.
“Two-wire Ethernet fits to all applications in process industries with Ethernet-APL and discrete industries with SPE. It simplifies the network architecture, provides high-speed data communication, and enables the seamless data access for higher level applications,” Spielmann added.
Ethernet-APL and SPE meet the requirements of the industries in terms of easiness and robustness while bringing added-value by the connectivity to the smart instruments and their data. This data can be used in various types of applications. Probably the data will be collected in a central data hub first and will then be transferred to the appropriate application or service where it is needed. 2-wire Ethernet is just the enabler technology to connect the field level and to transfer the large amount of data via the data highway.”
Addressing engineering challenges
Process plants are one area that are typically equipped with 4-20mA analogue technology. Such topologies are typically designed by either a central IO with marshalling rack from where a multi-wire bulk cable goes out to the field or with remote IOs in the field level which are connected via fieldbus interfaces or standard industrial Ethernet to the controller.
Spielmann said that these topologies require either huge cable effort within the cable trays or expensive remote IOs. In addition, remote IOs are not standardized in terms of upper protocol integration which makes it nearly impossible to route through all the different components of different vendors for data access of upper layer applications.
“A major advantage of Ethernet technology is the transparent routing through the infrastructure components which decreases complexity compared to 4-20mA technology a lot. Same applies to intrinsic safety calculations which are quite time-consuming with 4-20mA architectures but built-in into APL devices via the IEC specification 2-WISE,” he said. “With Ethernet technologies, necessary redundancy concepts can be realized which are supported by the well-established industrial Ethernet protocols like PROFINET or EtherNet/IP. This increases plant availability which is a key performance indicator of process plants.”
Connectivity for smaller devices
Cost and size reductions
Dr. Al Beydoun, President and Executive Director at ODVA, said that Single Pair Ethernet (SPE) allows for cost and size reductions in Ethernet PHYs, cable and connectors that enables cost effective connectivity for smaller devices.
“This opens up the possibility to connect simple devices to Ethernet that were previously only hardwired or controlled via fieldbus technology,” Beydoun said, “and SPE also reduces the overall labor for panel installations and provides information for concepts such as prognostics. ODVA’s in-cabinet resource-constrained device solution is a case in point as it enables contactors and push buttons to be connected to EtherNet/IPTM via a SPE multidrop flat cable.”
“It’s important to note that SPE encompasses 10BASE-T1L General Purpose SPE applications, 10BASE-T1S in-cabinet applications, and 10BASE-T1L Ethernet-APL applications. Furthermore, there are multiple IEEE SPE standards in addition those mentioned.”
Emergence of Ethernet-APL
Ethernet-APL is an intrinsically safe (IEC TS 60079-47), two-wire extension of 10BASE-T1L SPE (IEEE 802.3cg-2019) that meets the requirements of the process industries. Ethernet-APL allows for power to field instrumentation, long cable runs of up to 1,000 meters as well as potential reuse of type A fieldbus cable (IEC 61158-2), and up to 10 Mbit/s communication speeds. As another physical layer for Ethernet, Ethernet-APL provides seamless connectivity from field instrumentation to the plant-wide Ethernet. Additionally, process instrumentation can easily communicate multiple variables such as temperature, level, and flow from one instrument via the increased bandwidth of Ethernet-APL.
Beydoun said that EtherNet/IP will be able to expand precise, efficient Ethernet-based control and commissioning across process field instrumentation via the Ethernet-APL physical layer. The full use of EtherNet/IP in process automation will enable concurrent seamless connectivity from the field devices to the controllers, to Industrial IoT applications, as well as the edge and cloud for prognostic analysis.
Technology trends
Beydoun said that the drive to digitalize the enterprise will be a key catalyst in adopting Single Pair Ethernet and Ethernet-APL technology on the plant floor to connect more and more field devices.
Key incentives to adding devices to Ethernet networks include remote commissioning, digital troubleshooting enabled by diagnostics, analytics and edge and/or cloud enabled prognostics. The cost savings from being able to quickly and easily add a new device to the network and to identify a malfunctioning device without having to physically test for failures adds up quickly between labor savings and downtime reduction.
The overall SPE adoption rate among manufacturers is likely to reach the majority quickly as digitalization, the Industrial Internet of Things (IIoT), and Industry 4.0 are used to reduce the impact of significant labor shortages that are being experienced across multiple sectors, as well as to contain increasing cost pressures to stabilize margins.
“The functionality in EtherNet/IP for in-cabinet resource-constrained device connectivity powered by SPE allows for the usage of a flat cable to reduce material cost, space used, and installation time,” Beydoun said. “The flat cable includes both switched power, network power, SPE, and a select line to enable multi device connectivity at a low cost. This compact low-cost flat cable allows devices to be easily attached via a safe and simple piercing connection.”
He added that Ethernet-APL supports trunk and spur, line, and star topologies as well as Type A fieldbus cable to meet the requirements of the process industries. The trunk and spur topology will be seen in the vast majority of instances for powered and intrinsic safety applications, but a ring topology is possible for non-powered and non-IS applications to enable redundancy for critical applications in sectors such as Water Treatment Plants. Ethernet-APL also enables the use of Parallel Redundancy Protocol (PRP) for network technology that have this as an option, as EtherNet/IP does.
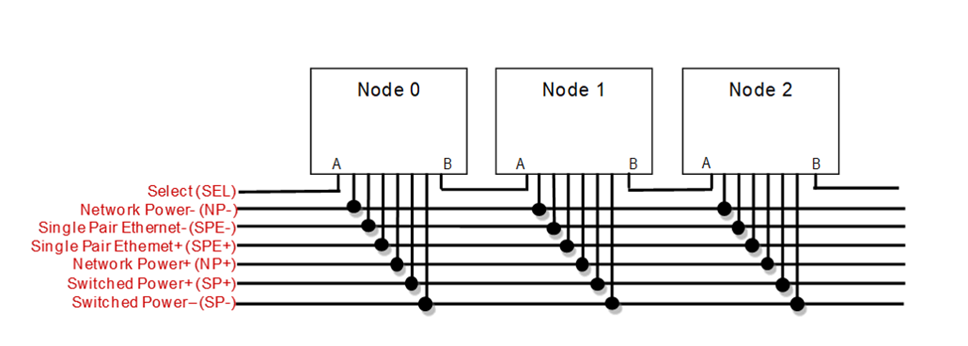
EtherNet/IP In-Cabinet 10BASE-T1S SPE Multidrop Flat Cable with Select Line.
Targeted application areas
10BASE-T1L SPE is geared more toward discrete and hybrid industrial automation applications to reach low-cost sensors and actuators within sectors such as automotive, tire, electronics, distribution and packaging. However, the EtherNet/IP functionality for in-cabinet 10BASE-T1S resource-constrained devices can be implemented in discrete, hybrid and process industries.
Ethernet-APL is purpose-built to meet the needs of the process industries, including placement in Zones 0/1/2 for flammable liquid/gas in sectors such as oil & gas and chemical. Ethernet-APL may also have some applications within hybrid industries that require intrinsic safety such as food/beverage and pharmaceutical.
“SPE and Ethernet-APL both allow devices to be connected to Ethernet that were previously hardwired or connected via point-to-point or multidrop fieldbus solutions. A vast number of new possibilities are opened up via additional network connectivity including fast identification of failures via standard diagnostics or monitoring of devices for out-of-range operation to both predict premature failure and reduce negative impacts on quality. OEE can also be positively impacted by adding new device metrics to automated KPI models that can help identify and remove bottlenecks via improved visibility to improve overall throughput,” Beydoun said.
Engineering challenges
His view is that in-cabinet resource-constrained device solutions will address the challenge of cabinet space being some of the highest cost real estate in the world. SPE can dramatically reduce the amount of space that the wiring takes up within the cabinet, allowing for either smaller cabinets or fewer cabinets to be installed. The savings can add up quickly in factories and plants with thousands of nodes.
The simple and quick installation enabled by SPE cabling can also help to address labor shortages, enable quick problem identification and resolution during validation processes during plant commissioning, and can enable last minute design changes with dramatically lower impact on production schedules.
“Ethernet-APL meets the ruggedness, simplicity, and security expected by the process industries for a control network. Ethernet-APL leverages the same Type A fieldbus cable that is currently installed in process plants today. In fact, existing Type A cable may be reused if the cable integrity is verified and resistance standards of 100 ohms with +/- 20 ohms tolerances are met,” Beydoun said.
“A screwdriver and related wire preparation tools are all that is needed to physically connect field devices. Since it is just a physical layer, Ethernet-APL allows end users to access standard safety and security services built on IEC 61508 and ISA/IEC 62443 from the leading industrial automation standards bodies. This includes CIP SafetyTM and CIP SecurityTM capabilities for EtherNet/IP.”
Extending the reach of Ethernet
Addressing new application areas
According to Michael Clark, Director of OPC Foundation North America, SPE and Ethernet-APL extend the reach of Ethernet to support additional industrial use cases at the field level, including discrete, process, and hazardous applications.
“High-speed Ethernet connectivity to field devices (sensors and actuators) provides the ability to make data directly available from the source seamlessly to the edge or even to cloud applications. These technologies, thus, make an elementary contribution to the digital transformation of the industry,” Clark told IEB recently. “In addition, SPE and Ethernet-APL bring significant advantages with regard to wiring & installation: cable lengths of up to 1000 meters, minimal space requirements, easy installation, and the possibility to transmit data and power over a single twisted pair cable.”
Clark said that SPE and Ethernet-APL help to overcome many of the limitations that analogue interfaces or fieldbuses have imposed in industrial applications over recent decades. This is why SPE and Ethernet-APL, together with other IEEE standards such as Ethernet Time-Sensitive Networking (TSN), are key technologies for the OPC Foundation to further develop OPC UA (IEC 62541) as a communication solution that fully scales from the field to the cloud, with the support of all major IT & OT companies across the world. OPC UA then serves as the standard for semantic interoperability, which is key for exchanging data with an unambiguous, shared meaning across IT & OT systems.
Impact of networking technology
“The industrial networking environment today is often diverse with a variety of different communication interfaces (proprietary, analogue, or fieldbus types), with Ethernet as the backbone network to IT enterprise systems. With SPE and Ethernet-APL, Ethernet is extending its reach into the field level, thus becoming the single networking technology for IT & OT; greatly simplifying network infrastructure complexities and costs,” Clark said.
He added that this architecture enables uniform operation, based on higher-layer protocols within Ethernet, i.e. parameterization, initialization, and programming. Operation and maintenance/troubleshooting of large and generally heterogeneous network structures are sustainably simplified. With this approach, the field level is as easy to operate and manage with SPE and Ethernet-APL as IT networks are with SNMP.
Targeted applications
Clark said that SPE and Ethernet-APL are ideal but, at the same time, not limited across a broad range of applications in discrete manufacturing and the process industry, including hazardous areas. Field devices, including sensors and actuators, can be easily integrated into an existing Ethernet environment, without the need for additional gateways or interfaces.
This is improving connectivity and, therefore, supports the digital transformation across different use cases, such as condition monitoring, predictive maintenance, energy optimization, and increased productivity and flexibility.
Some of the engineering challenges that companies implementing these solutions are related to physical layer conformance, along with safety and power requirements.
“Testing the physical layer is essential to ensuring correct operations of the products, including conformance to the physical layer, according to IEEE, as well as intrinsic safety and power requirements, according to IEC,” Clark said.
“Cross-organization recognition of test results is required to avoid the need for device manufacturers to do physical testing, multiple times, in cases where they are supporting multiple industrial protocols.”