TechnologySeptember 22, 2019
Single Pair Ethernet gears up to impact industrial automation
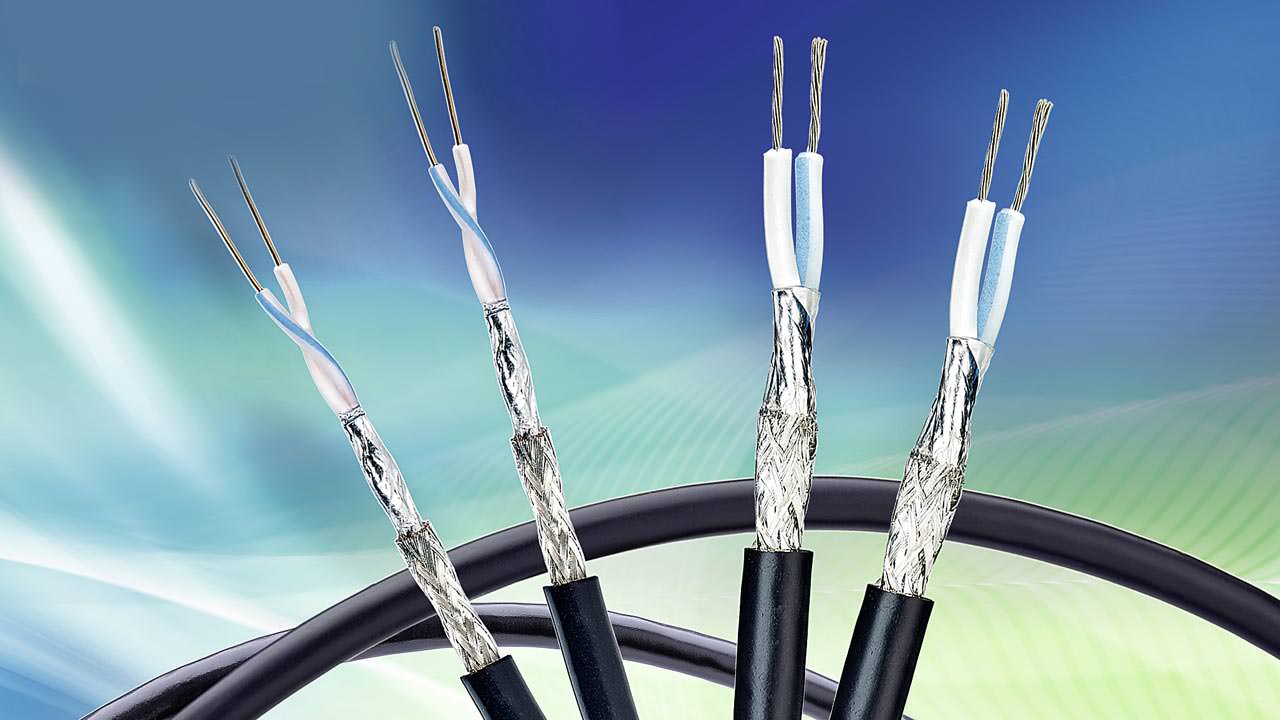
With Single Pair Ethernet technology and Time Sensitive Networking, industrial automation is poised for a leap forward in precision and productivity. With the new, unique SPE protocol for encoding and scrambling data, industrial networks will gain lower EMI, lower cost, reduced cabling weight and higher bandwidth.
In the worlds of industrial and process automation, and the networks that enable technology advances, tremendous progress has been made in recent decades. Over the years, more smart devices, more bandwidth, more determinism, along with more precision and sophistication, have been added to the work at hand – whether that work is automotive or semiconductor manufacturing, electrical power delivery or natural gas extraction.
Intelligent equipment uses sensors and actuators that can be connected over one common network. The data captured and conveyed to the data center for analysis and prediction is vital. But with this, many sensors and actuators that accommodate space, packing density, costs, infrastructure, and ease of installation and service, have become all the more important.
Proprietary and legacy fieldbus systems including Profibus, AS-Interface, Modbus, CANOpen, DeviceNet, CC-Link, and IO-Link are generally too bulky or resource-intensive for the best Industrial Process implementations. Remember, complexity breeds cost and space in control system layout is not unlimited. Order, structure and reliability with these legacy systems are not what it should be. But now, we are on the cusp of reversing that entropy. Two wires, a single twisted pair, are enough.
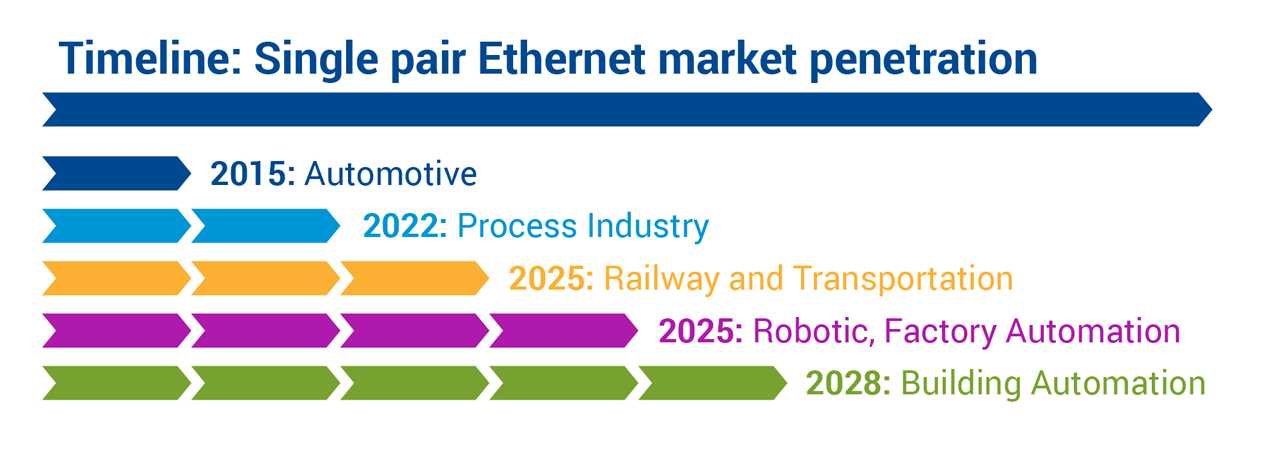
The benefits of Single Pair Ethernet is expected to gain wide market acceptance. One network from the sensor to the cloud guarantees control over all network components. Thinner, lighter cables enable more orderly, defined cabling.
Industrial Ethernet breakthrough
One Ethernet network in compliance with IEEE 802.3 from the sensor to the cloud is arriving. Now, with the coming of Single Pair Ethernet (SPE) technology in the Industrial Field together with Time Sensitive Networking (TSN) capability, our sector is poised for a leap forward in precision and productivity. With the new, unique SPE protocol for encoding and scrambling data, industrial and process networks gain lower electro-magnetic interference (EMI), lower cost, reduced cabling weight, and higher bandwidth.
One lighter, thinner cable that is still capable of Power over Data Lines (PoDL) and that will have a signal and power reach up to 1000 meters is arriving now. This will be one cable and one network type that any sensor or actuator can get power from, and any sensor or actuator can talk to.
Germany’s PI International Organization and ODVA (US) have begun their work to adopt the IEC single pair Ethernet cable and connector standards and the various IEEE 802.3 SPE protocols. With this development, “the stars are aligned,” as the saying goes. System integrators and field application engineers truly have a pathway to functionality gains without increases in their costs for installation, operation and repair.
With the right partners and the right application of these new standards and the engineering expertise it took to ratify them, there will very soon be one global common network type from the sensor through to I/O modules and switch devices, and up into the cloud backbone. All of this is possible if the right systems engineering is applied.
Automotive Ushered in SPE
Single Pair Ethernet is being used successfully in the automotive environment today. Vehicle harnessing systems and in-vehicle networks have greatly benefited from the work that key automotive engineering teams did in partnership with their cable and connector partners. That work included the time and energy put into getting the IEEE 802.3bw technology standard for 100BASE-T1 for Automotive in-vehicle networks published in 2015.
IEEE 802.3bw was driven primarily by the needs of the global automotive industry and it perfectly illustrates how Ethernet can expand into new application areas and bring about innovation. Advanced driver assistance systems and compute-intensive displays created the need for cost-effective, high-bandwidth connectivity. But, importantly, it fell to the component and cabling ecosystem to give automotive engineers a way to build that better network inside a very tight weight and space envelope. Enter, Single Pair Ethernet. Where once four wire pairs were necessary, now there can be just one.
Advanced automotive electronic systems require faster communication networks as today‘s vehicles share an enormous amount of real-time data, firmware and software between electronic control units (ECUs). IEEE 802.3bw (100BASE-T1) came to be because engineers developed a new physical layer (PHY) communication protocol that could make single pair work. This PHY was developed by automotive manufacturers in collaboration with leading integrated circuit (IC) manufacturers and the ecosystem of suppliers around them.
The 100BASE-T1 standard was based upon, and is interoperable with, the existing OPEN Alliance Broad-Reach automotive specification. 100BASE-T1 is the first in a family of Single Pair Ethernet standards to address new applications.
100BASE-T1-PHY performs all necessary scrambling and encoding prior to transmission over an unshielded twisted pair cable up to 15 meters. 100BASE-T1 is transparent from the media access control (MAC) device’s point of view, as the existing Media Independent Interface (MII) does not change.
100BASE-T1 is a physical full-duplex interface, which means that the data is sent and received on the same pair of conductors. The physical full-duplex transmission is achieved according to the principle of superposition.
100BASE-T1 PHYs have integrated hybrid circuits and use echo cancellation to remove their own transmitted signal and extract the information received from the remote station. In contrast, 10BASE-T and 100BASE-TX have their own pair of conductors for each transmission direction. This PHY approach was a true networking engineering breakthrough.
The use of one transmission medium for both directions reduces the total weight of the cables installed in the vehicle, so we have not only reduced material costs but also reduced fuel consumption. Using superposition and special coding and scrambling techniques, 100BASE-T1 reduces electro-magnetic interference (EMI), weight, cost and footprint compared to existing 10BASE-T and 100BASE-TX Ethernet standards.
100BASE-T1 enables the transmission of audio, video, connected car, firmware/software and calibration data in vehicles using Ethernet protocols for Audio Video Bridging (AVB) via unshielded single twisted-pair cable. The AVB protocols developed by the IEEE Time-Sensitive Networking Task Group offer low deterministic latency, synchronized nodes, and traffic shaping. These aspects are important for the communication of different types of information in automotive systems and give 100BASE-T1 the ability to transmit different types of data with different priorities (low data rate with high priority, or high data rate with low priority and time synchronization).
The Industrial and Process Automation world took note of automotive’s accomplishments with Single Pair Ethernet. Manufacturing and process engineers know that operational efficiencies will be gained with a common, higher bandwidth network encompassing much more of the power and data-carrying requirements manufacturing software calls for. The question was, “How do we get there?”
The 4th industrial revolution could be realized with the two-wire solution. So, the Ethernet standard IEEE P802.3cg, 10Mb/s Single Pair Ethernet Task Force group, formed. This group of companies and engineers took up the task of understanding everything that industrial fieldbus technologies do today to complete communication to the edge of the network, and they took up the task of building a unified Ethernet program that could replace them.
With the new SPE technology, it is possible to connect devices over a full 1000 meters at 10 Megabits per second throughput and even have PoDL technology as an option. Any of the fieldbus technologies with data rates from hundreds of kilobits per second up to 10Mbps can be replaced. The long reach of 1000 meters is the key. Now, SPE can come into hazardous environments, because remote powering will be possible. And now, SPE can be used in power generation and transmission, in oil and gas exploration and extraction processes, in mining environments and in chemical and wastewater processing.
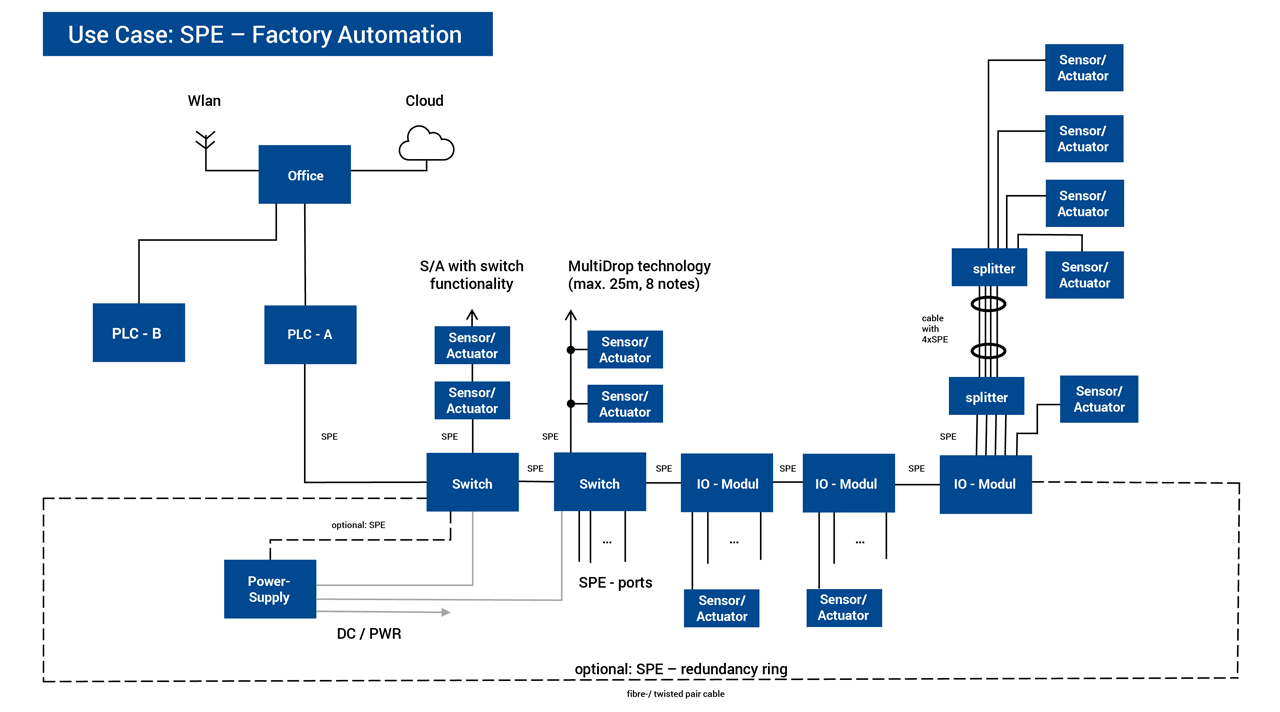
Single pair Ethernet technology in factory automation example application.
New cable standards from IEC
To be certain the long-distance applications come to be for these Industries, two new cable standards are currently being developed. The new cable standards, IEC 61156-13 and IEC 61156-14, describe symmetrical single pair cables with transmission characteristics up to 20 MHz over a distance up to 1 kilometer (km) to support 10Mbps for mainly industrial applications.
The cable type is intended to be used for shielded channels, and they may also support remote powering. Part 13 can be used for horizontal floor wiring, thus the specification for it to have a solid, annealed copper conductor, and a nominal diameter between 0.64 and 1.7 mm. Part 14 is intended for work area wiring and stranded wire, so it is in flexible materials.
We see our role and our responsibility to customers as insuring the Single Pair Ethernet cables fulfill the standards. We are completing all of the necessary electrical and transmission characteristic documentation and tests, mechanical and dimensional documentation of requirements, and insuring the environmental characteristics are met for bending, elongation, and tensile strength. When these things are done, we will have the solution for SPE for remote and hazardous environment automation and instrumentation.
PROFIBUS & PROFINET International (PI), ODVA and the FieldCommGroup are working equally hard to support SPE for customers. They have specified an Advanced Physical Layer (APL) to connect power and data over a shielded twisted pair line to field devices and support the familiar trunk-and-spur-topology. With that, Ethernet in the Field really should be ready by 2021/2022.
APL is the ruggedized, two-wire, loop-powered Ethernet physical layer that uses 10BASE-T1L. It enables a direct connection of field devices to Ethernet-based systems in a way that process industries can benefit. With this, they can converge their IT and OT systems. Utilizing a switched architecture, the design intent is eliminating interference between devices connected to the same network.
Single Pair Ethernet in the field
With the success of SPE in Automotive, the advanced standardization work on IEEE 802.3cg for the process industry, and the first jointly developed specifications from the user organizations PI and ODVA culminating in the APL, Single Pair Ethernet will move into the Industrial markets and replace current fieldbus technology, we have talked about.
The benefits over current solutions are too big to ignore. In 2016, the IEEE 802.3bp standard 1000BASE-T1 for higher data rates and the SPE standard IEEE 802.3bu for Power over Data Lines (PoDL) of Single Balanced Twisted-Pair Ethernet were published. This was a watershed moment in SPE’s evolution.
“The IEEE 802.3bu project was initiated due to the increased utilization of Ethernet in automobiles in a single pair configuration. It also holds a good deal of promise for further applicability across a wide range of industries and within a rapidly growing Internet of Things ecosystem,” said Dan Dove, chair of the IEEE P802.3bu Task Force.
“The standard defines a power delivery protocol that supports multiple voltages, and multiple classes of power delivery at each voltage, with assured fault protection and detection capabilities for identifying device signatures, as well as communicating directly with devices to determine accurate and safe power delivery.“
As we have said, this remote and safe power delivery engineering is key. The question now moves to connectors.
Meanwhile, the standards for SPE cables and connectors have been pushed from international and national standardization groups. Now, cable standards for applications for long distances with transmission characteristics up to 20 MHz (IEC 61156-13 and -14) and also for applications with higher data rate and transmission characteristics up to 600 MHz and distances up to 40 m (IEC 61156-11 and -12) for both horizontal floor and work area wiring are on the way.
Six new proposal connector standards for the various applications are in progress. Four of these SPE connectors in accordance with IEC 63171 parts 1 to 4 are designed for the office environment (IP20), thus mechanical, ingress and protection, climatic and chemical and electromagnetic (abbreviated as “MICE”) level 1, or M1I1C1E1.
IEC 63171-5 and IEC 63171-6 are specified SPE connectors for the industrial environment (IP65/67). These 2-contact connector types can be used for levels 2 and 3, or M2I2C2E2/ M3I3C3E3 environmental conditions.
All of these connector variants have to fulfill the general requirements and tests for all shielded or unshielded free and fixed connectors for balanced single-pair data transmission with current carrying capacity. These connectors are intended to be used for Single Pair Ethernet according IEEE Ethernet standards: 10BaseT1 (IEEE802.3cg), 100Base-T1 (IEEE 802.3bw), 1000Base-T1 (IEEE 802.3bp) and PoDL (IEEE 802.3bu).
In addition, the Information Technology standard “Generic Cabling for Customer Premises ISO/IEC 3WD TR 11801 part 9906 – technical report: Balanced 1-pair cabling channels up to 600 MHz” describes balanced one-pair channels for the support of Single Pair Ethernet applications according the IEEE 802.3 SPE standards. This document clearly lays out that all of the standards – 1000 Mbps (IEEE 802.3bp) up to 40 m, 100Mbps (IEEE 802.3bw) with unshielded cable up to 15 m or 10Mbps (IEEE 802.3cg) up to 1000 m – are achievable, with cable design and wire diameter determining the reach that is possible.
With these standardization and specification activities for SPE in the Industrial field happening together and with them making the progress they have, we recently reached the point where “all of the oars were pulling the boat in the same direction.”
Now, a complete range of components, devices and applications for Single Pair Ethernet technology will bring Industry 4.0, the fourth industrial revolution, to the world with scalability, determinism and interoperability.
Thriving IEEE 802 ecosystem
To better address the needs of all of these areas, IEEE 802 standards are constantly evolving and expanding. The success of IEEE 802 standards – from their inception about 30 years ago through today – has been due to the fair, open and transparent IEEE 802.3 development process.
Now, a new IEEE P802.3ch task force group for Multi-Gig Automotive Ethernet has been founded and research projects are underway to make this standard suitable for the industrial and building sector, too.
Belden teams throughout Germany and around the world embody our core competence in physical, electrical and electronic network infrastructure. When we meet with customers and fellow suppliers in standardization groups, the exchange of ideas and the challenges we put to one another make the end products better.
We have found this process for single pair Ethernet technology in new Industrial applications has gone just the same. Our customers are already seeing the benefits from that and in the next three to five years, they definitely will see it.
One network from the production process at the field level up to the control level (in PLCs) and up to the process management (MES) and enterprise level (ERP) truly can be a reality: one network from the sensor to the cloud.
Single Pair Ethernet will become the backbone of the fully digitized factory. Cost-effective, reliable cables, connectors and active components adhering to SPE mean all factory subsystems can get smaller and the amount of space and accommodation for power and temperature control go down. Simpler cabling and installation of components are going to drive materials and labor costs out of new factory floor builds.
We believe that focus on these details, engineering for plug and play installation and repair, fast-connection technology between connector and wire and between connectors, low cable weight, and systems for monitoring the complete network are going to turbo-charge the deployment of the IIoT in the near future.
Think about how Single Pair Ethernet will look on the automated, connected factory floor:
- One network from the sensor to the cloud guarantees control over all network components.
- Thinner, lighter cables enable a more orderly, defined cable infrastructure, but with more Ethernet channels in existing cable ducts.
- Single Pair Ethernet connector standard for M2I2C2E2 /M3I3C3E3 industrial environmental with universally known M8 and M12 connector designs well-established in industrial environments (IP65/67).
- SPE standard enables cable sharing (four SPE channels in one cable) and allows simple and cost-effective passive line distribution.
- Possibility of connecting network components via multi-drop bus technology in which all components are connected to one cable for short distance.
- Higher reliability through simpler cable and connector designs because there is only one channel.
Further in the future, there will be a globally uniform Ethernet network for every market and application area. There may continue to be a heterogeneous network infrastructure for certain system requirements. But the common thread through them all will be Ethernet that global suppliers agree on.
Fiber cables for long transmission distances and shielded CAT 7 copper Ethernet cables for high data rates with 4-pair for 10 Gigabyte per second will continue to be required. Still, when sensor and actuator and PLC data can be gathered and passed up to these trunks without translators and without proprietary interfaces, the industry will benefit.
Now, new single pair Ethernet components as switches, IO modules, connectors, splitters, and cables are starting to be developed for future IIoT requirements.
Part of our expertise is doing that alongside the work of insuring compliance to the standards and directives of the various end-markets such as fire protection for buildings or low smoke, halogen free cable for railway applications.