TechnologyNovember 16, 2023
Software-driven, secure predictive maintenance for electric motors
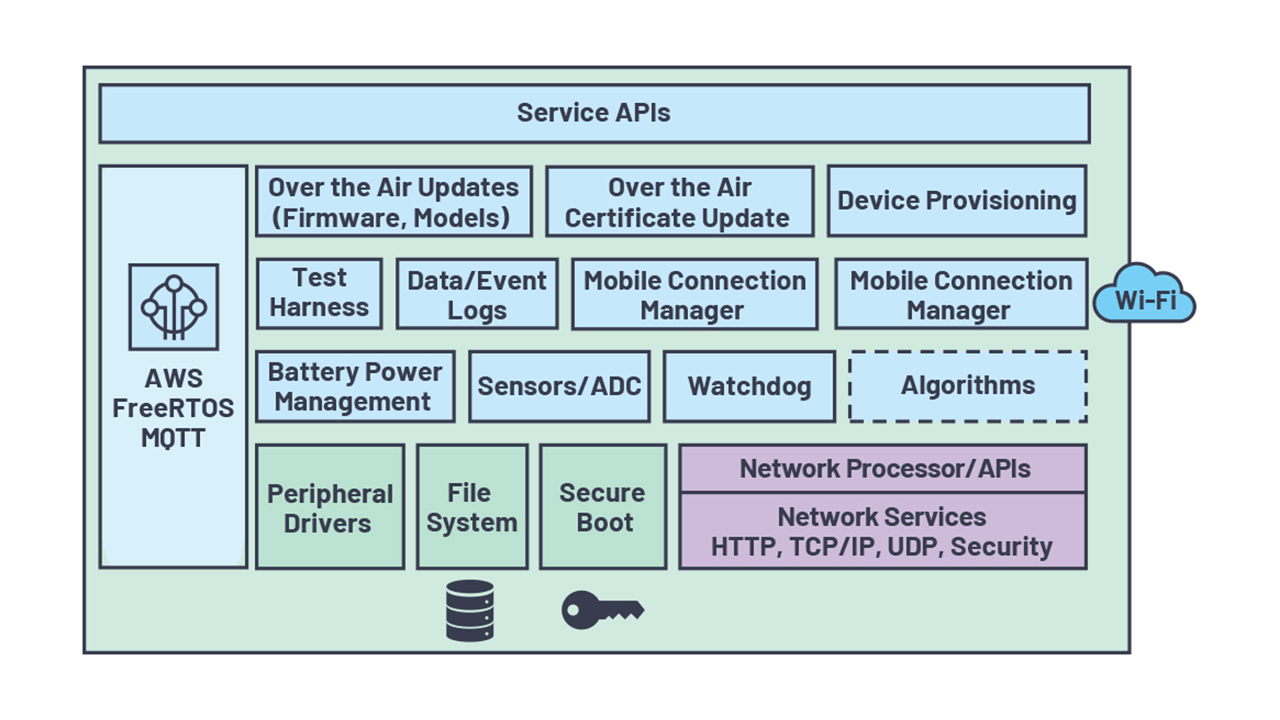
The Smart Motor Sensor (SMS) is a flexible, out-of-the-box, end-to-end secure wireless predictive maintenance (PdM) solution that combines software, hardware, and domain expertise in electric motors to create a secure scalable offering for the predictive maintenance of electric motors.
In today’s factories, 14 million hours of unplanned downtime happen due to system failures in the U.S. alone, resulting in the loss of billions of dollars.
In order to prevent such events, factories typically employ an expensive route-based approach where an expert gathers data to assess the health of the equipment or utilize a range of suboptimal sensing solutions that do not reliably detect all potential failures that could occur in these systems.
Now that the Industry 4.0 (also known as the Industrial Internet of Things or IIoT) wave is well under way, industrial customers are more focused on deploying solutions that increase equipment uptime, reduce operational cost, extend equipment lifetime, and improve worker productivity.
Predictive maintenance solutions combine sensing technologies to gather equipment data and employ advanced analytics and algorithms to draw actionable insights into the health of equipment. As a result, this approach is expected to increase overall industrial productivity by more than 30%.
One common demand is for a full turnkey wireless solution that combines hardware and software and that is easy to install and use. Industries need a solution that does not require experts to manually gather data and/or install and maintain dedicated networks.
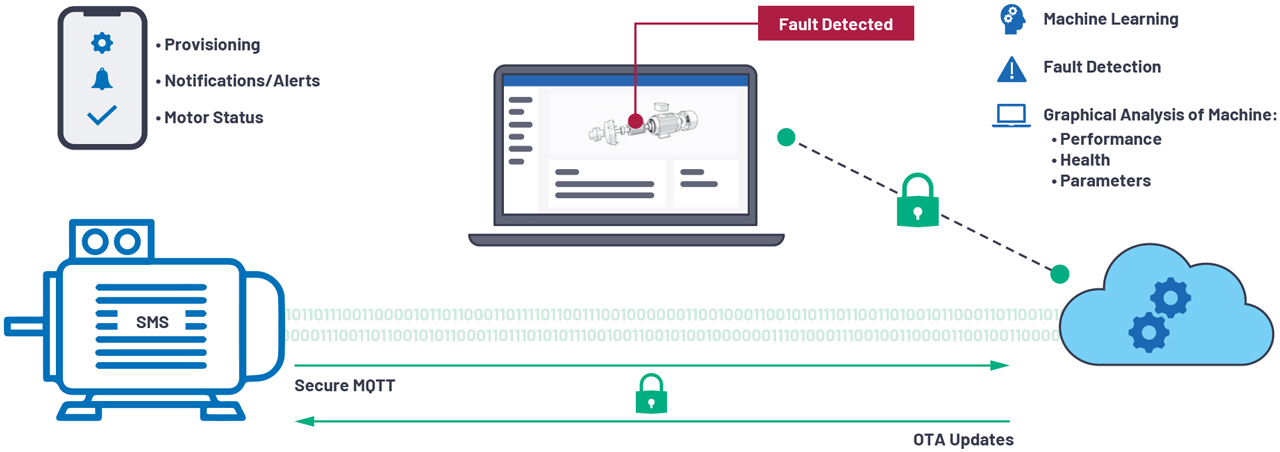
Figure 1. End-to-end predictive maintenance solution for electric motors.
Smart Motor Sensor (SMS) and how it works
The Smart Motor Sensor (SMS) is a flexible, out-of-the-box, end-to-end secure wireless predictive maintenance (PdM) solution that combines ADI software, hardware, and domain expertise in electric motors to create a secure scalable offering for the predictive maintenance of electric motors.
The Smart Motor Sensor (SMS) works with Android and iOS mobile applications for easy setup of the sensor, visibility on deployment data, and in-app notifications and alerts on critical events. A cloud hosted dashboard provides a complete overview of machine health diagnosis and fault detection with detailed information and visualization of each motor’s status along with AI-based analytics to detect commonly occurring faults in electric motors.
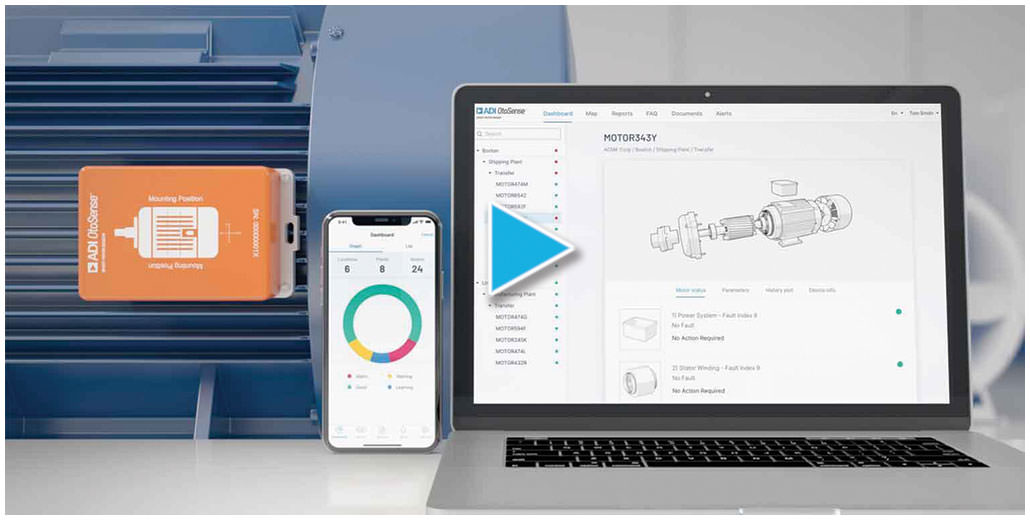
Figure 2. An overview of the ADI OtoSense™ Smart Motor Sensor.
The battery-operated SMS device combines ADI’s MEMS sensors, precision converters, and signal chains. Firmware embedded in the SMS device captures various parameters of the motor (such as vibration, temperature, speed, and magnetic flux) and sends these data securely over a Wi-Fi connection to the back-end cloud for processing. An artificial intelligence (AI) engine that runs on the cloud and is integrated into the web application analyzes the data and monitors the health of the motors.
The system can predict nine different electrical and mechanical failures that commonly occur in motors and, upon detecting one, sends out push notifications or emails to inform the user about the appropriate action to take. The Smart Motor Sensor product suite is available direct to customers as an end-to-end solution or via a REST API.
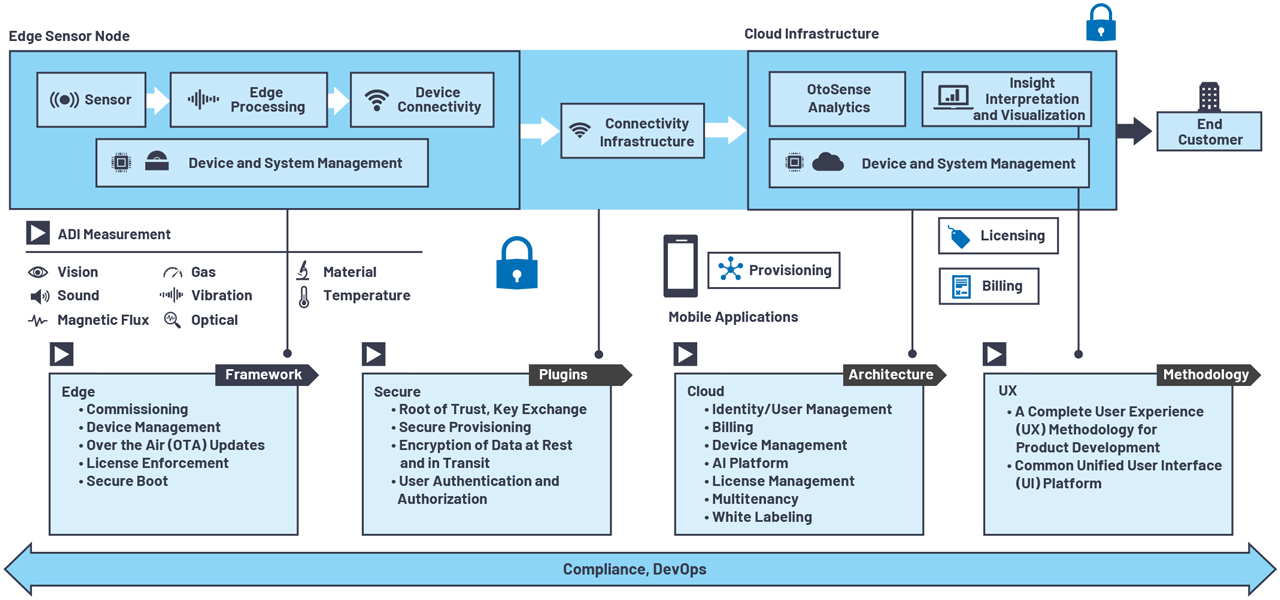
Figure 3. Sensor-to-cloud secure software framework.
Sensor-to-cloud software building blocks
Figure 3 above illustrates ADI’s sensor-to-cloud software framework, which was leveraged to build the necessary software for the SMS solution. The sensor-to-cloud secure software framework helps to meet the desire for complete solutions, without the frustration and complexity of putting together a full system to capture actionable insights from real-world data.
The framework also enables greater reusability, which helps reduce time to market, and allows the software team to focus on delivering the domain-specific solution for any given product.
Along with functionality and scalability, prescriptive best practices and processes are a crucial part of the framework to ensure the most robust and secure solutions are delivered. The software framework is an embodiment of recommended best practices and proven processes, from approaching each new customer engagement from a user-centric perspective to automation of DevOps principles to achieve efficiency and compliance.
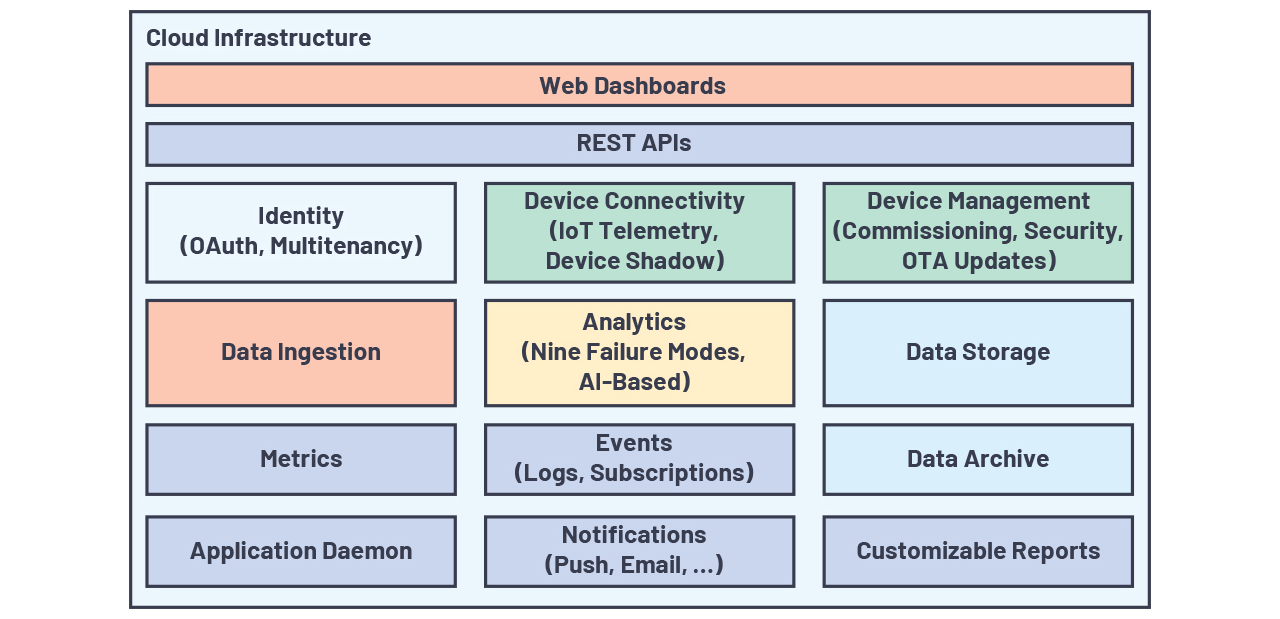
Figure 4. SMS cloud components from a secure software framework.
SMS cloud and web
The OtoSense SMS cloud back end is built on and extends the secure software framework. Figure 4 depicts the components of the cloud infrastructure. The application is multitenanted to support onboarding multiple customers and ensuring data segregation.
A unique custom label partner version also allows customers such as motor repair workshops, motor distributors, and others to easily add their logo and branding and sell SMS directly to their customers. Partners can seamlessly create new customer tenants with just a few clicks, and all the necessary architecture is automatically generated while the onboarding email invitations are sent to the customer.

Figure 5. Multitenancy ensuring customer data segregation.
SMS mobile applications
ADI OtoSense SMS mobile applications have been architected with code reuse as a priority. The core application consists of several modules, including an SMS communication module, API communication module, and a core application module (views and navigation).
These modules represent everything that can be reused across all custom label partner applications. For each new custom label application, a new configuration set is created that contains the partner’s branded UI components and API configuration. This software architecture enables the mobile applications development team to create new partner applications quickly and easily, as well as release new features and updates to all partner applications efficiently.
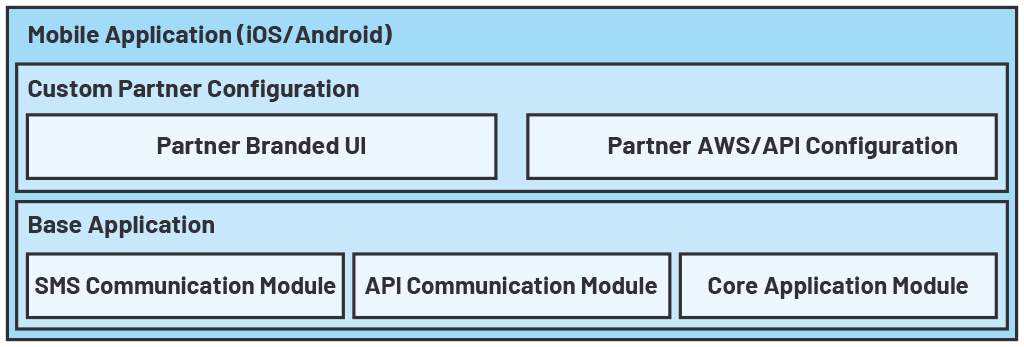
Figure 6. Mobile applications architecture.
SMS AI engine
The OtoSense AI platform can address any sensing interpretation challenge. This platform has been leveraged to implement the machine learning components of the Smart Motor Sensor solution. ADI’s in-depth knowledge in electric motors has been used to create a digital blueprint of an electric motor’s optimal behavior, across all ranges of loads, rotation speeds, and temperatures. However, each motor once sold deviates from this initial model. Its environment, usage, and maintenance operations make it unique.
After installation on a motor, ADI OtoSense SMS initially acquires data to learn how this motor differs from the blueprint and creates a unique digital twin for the motor the SMS edge device is attached to. From there, OtoSense SMS compares the data coming from this motor to its digital twin running in the exact same operating conditions. If there is a substantial difference in behavior between the physical motor and its digital twin, OtoSense SMS analyzes this difference to determine the most probable root cause of this discrepancy and informs the user about the existence of a fault, its origin, and the action to perform to resolve it.
The system is capable of detecting the following nine commonly occurring issues:
- Faults in the motor power system that can cause an asymmetry in the motor currents.
- Machine rotor unbalance as a consequence of the gravity center displacement of any of the motor rotating parts.
- Loss of alignment between motor and motor load.
- Faults caused in the motor stator, leading to asymmetry in the motor currents.
- Malfunction of the motor when the concentricity between the stator and the rotor is not maintained.
- Problems in the motor cooling system, such as obstruction of the ventilation outlet or the fan stop, in case of independent ventilation of the motor.
• Rotor failures such as discontinuities in the active part of the rotor, such as rotor bars or short-circuit ring, or problems in the welds of the copper rotor.
• Bearing failures such as lack of lubrication or defects in the inner and outer race, the cages, or the rolling elements.
• Problems in the fixing system of the motor to the operating bench, like soft/ loose foot.
SMS firmware
The firmware embedded in the SMS captures various parameters of the motor (vibration, temperature, speed, magnetic flux) that it is attached to and sends this data securely over a Wi-Fi connection to the back-end cloud for processing.
The SMS firmware connects with an iOS or Android smartphone via the Wi-Fi interface to enable device installation and provisioning. The firmware provides diagnostics information for troubleshooting the device during and after deployment and can be updated securely over the air.
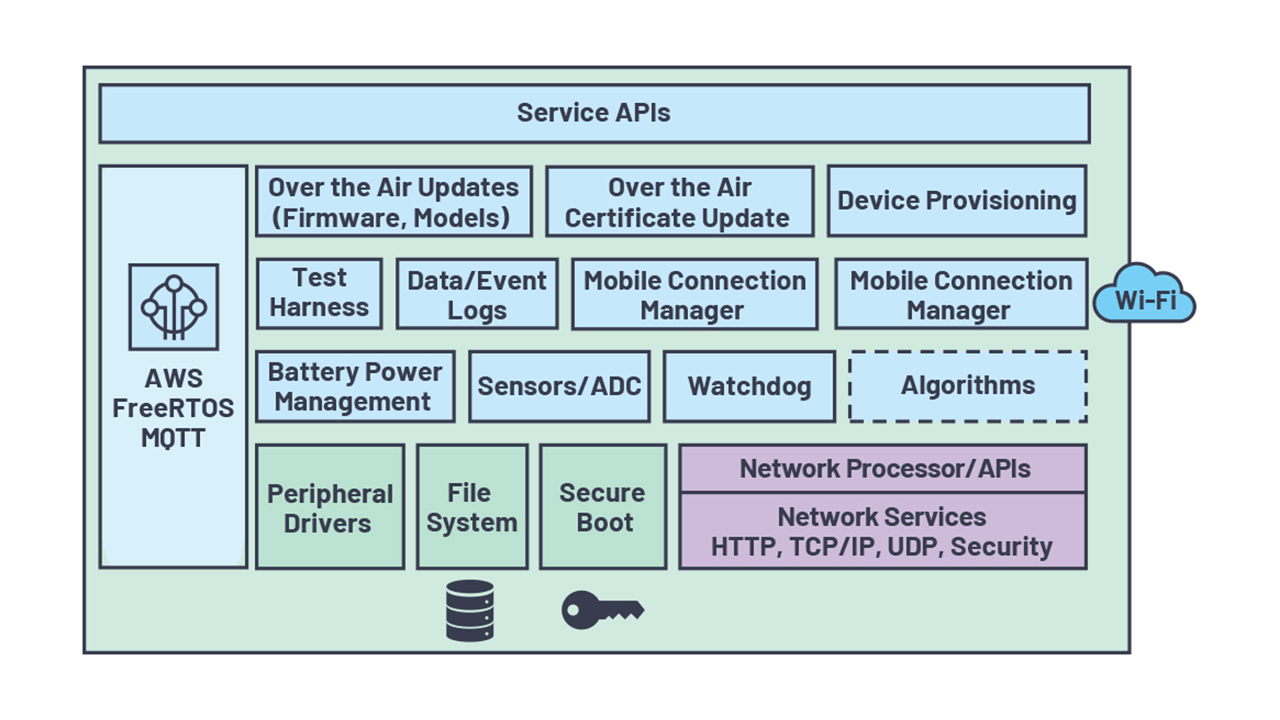
Figure 7. Secure firmware framework functional blocks.
The SMS firmware was built leveraging a portable service oriented architecture-based framework. This framework consists of modular, reusable functional blocks wrapped in application agnostic service APIs to enable reuse for other IoT applications. It also enables application developers to easily integrate application-specific signal processing functions and algorithms along with service APIs into the product. Figure 7 shows the functional blocks of the framework.
End-to-end security
ADI OtoSense SMS is designed from end to end with industry-best security protocols and controls, which ensure that SMS data and insights maintain their accuracy and precision, are reliably processed, are transmitted with no interruptions, and are always and only accessible by authorized OtoSense SMS users.
Each SMS customer has a dedicated account on the OtoSense Cloud, and all data (sensor data, insights, account information, etc.) are partitioned using the customer ID as the top-level partition key. Access to customer data is restricted to members of the customer account, and access authorization is enforced via identity and access management services offered by premier cloud services providers.
User account creation, management, and username/password login security (including password reset functionality) leverage trusted user management and authentication services from premier identity and login service providers, which ensures safe and secure user login from both the mobile application and web dashboard.
Sessions between the SMS device and the web application are exclusively established via mutually authenticated TLS. All data to or from the SMS device is encrypted and transmitted via the MQTT-over-TLS protocol. This includes sensor data, commands sent to the SMS device, and over-the-air updates transmitted to deployed SMS devices.
Conclusion
All the software building blocks, combined with ADI’s advanced technologies like MEMS sensors, precision converters, and signal chains and expertise in electric motors, make for a complete out-of-the box solution for the predictive maintenance of electric motors.
The end-to-end secure solution is designed to provide trusted insights to increase equipment uptime, reduce operational cost, extend equipment lifetime, and improve worker productivity.