TechnologyFebruary 2, 2021
System-integrated measurement simplifies power management
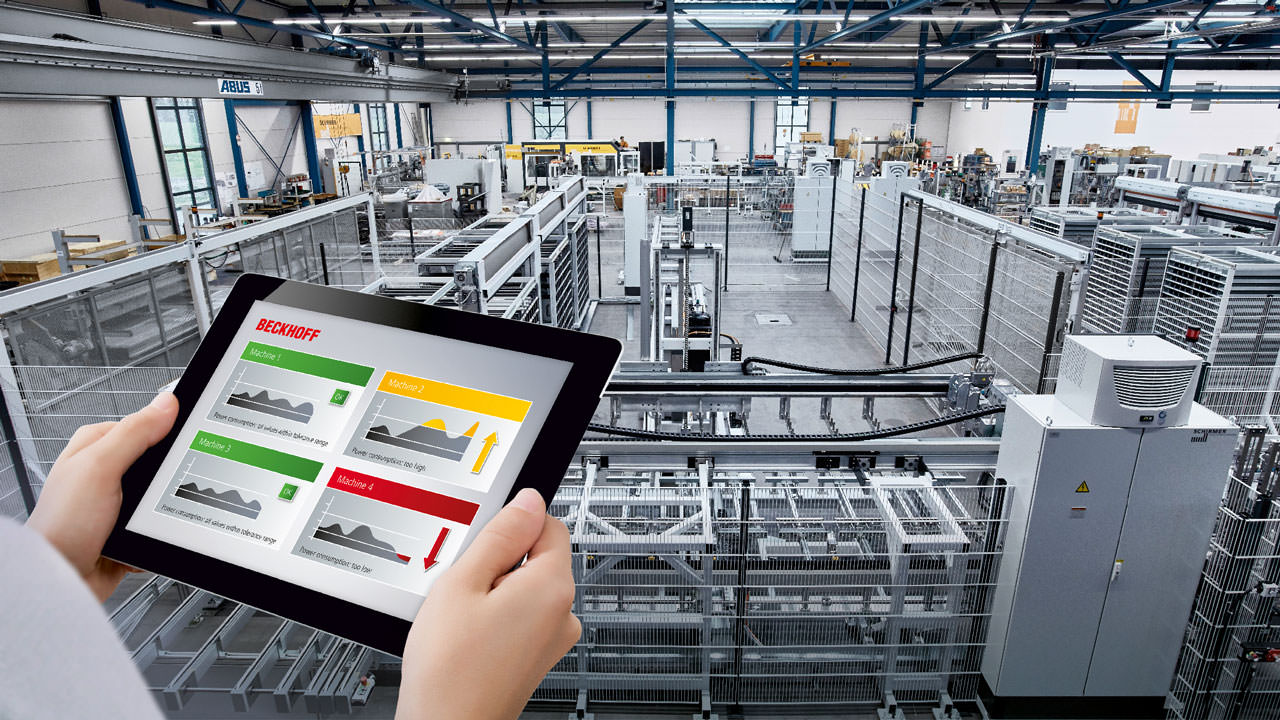
A highly efficient power measurement chain provides a range of solutions from the sensor to the cloud. These include capturing the physical value with new SCT current transformers, to the IoT Coupler and finally to cloud-based data analysis. A broad spectrum of power measurement terminals covers requirements.
An end-to-end power measurement chain that extends from the sensor to the cloud simplifies energy management, and improves the availability of machines and entire installations.
The solutions range from capturing the physical value with new SCT current transformers, to the IoT Coupler and finally to cloud-based data analysis. A broad spectrum of power measurement terminals covers all requirements, from a current input terminal to highly efficient distributed power measurement.
By having access to continuous and integrated power measurement tools, users can perform extensive inline analyses that allow them to detect deviations instantly in order to take quick corrective action and minimize downtime. For example, a steady increase in a machine’s power consumption may be an indicator of excessive wear on bearings, while a decrease may be a sign of quality problems.
Up to now, such continuous monitoring was extraordinarily complex because it required external sensors to be installed at great cost and often using special parts. With power measurement terminals from Beckhoff Automation, this can now be accomplished with little effort using standard components, even in retrofits on existing machines and systems.
By measuring the power on an existing motor cable, for example, asymmetrical currents can now be detected within milliseconds and not only indirectly via an unusual rise in the motor’s temperature. And in case of vibrations, mechanical weak spots can be identified via an increase in harmonic content.
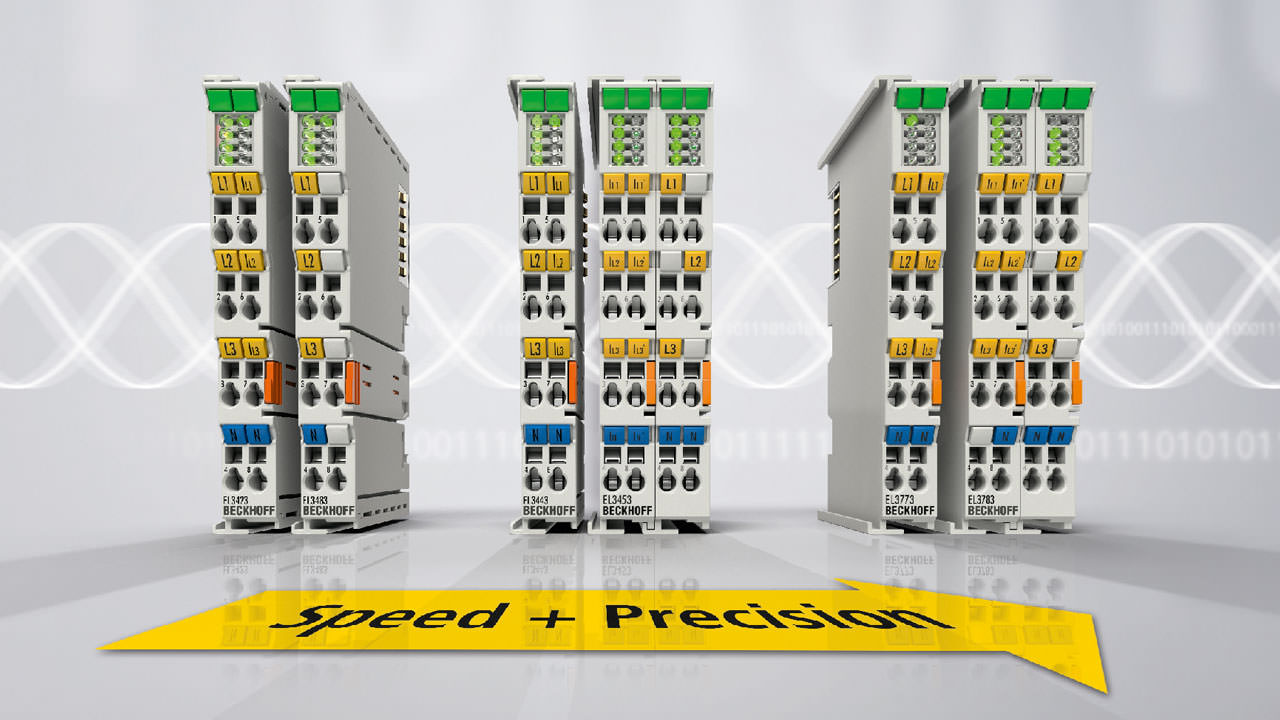
With the EtherCAT power management terminals, tasks with optimal scalability include power monitoring, process control, network control and maintenance.
Power transparency boosts efficiency
Machines and plants are dynamic systems that get expanded, modified, converted or otherwise adapted to new production requirements over the years. In order to obtain maximum transparency even for systems that have become unwieldy, it is recommendable to have an all-encompassing measurement system that collects all relevant power data reliably and makes it possible to analyze it quickly in the cloud, if necessary.
To make evaluation of measurement values as easy as possible, Beckhoff has developed the so-called power quality factor (PQF) which allows users to assess power quality for a machine or system based on a single number without having to analyze the frequency, voltage, harmonics or symmetry individually.
If a machine malfunction occurs and the PQF simultaneously drops to zero, users can conclude that the might not lie in the machine itself but in the power supply. Based on this information, the causes and effects of faults can be identified and corrected much more quickly. The PQF can also function as an early-warning system and simplify the clarification of potential questions regarding liability.
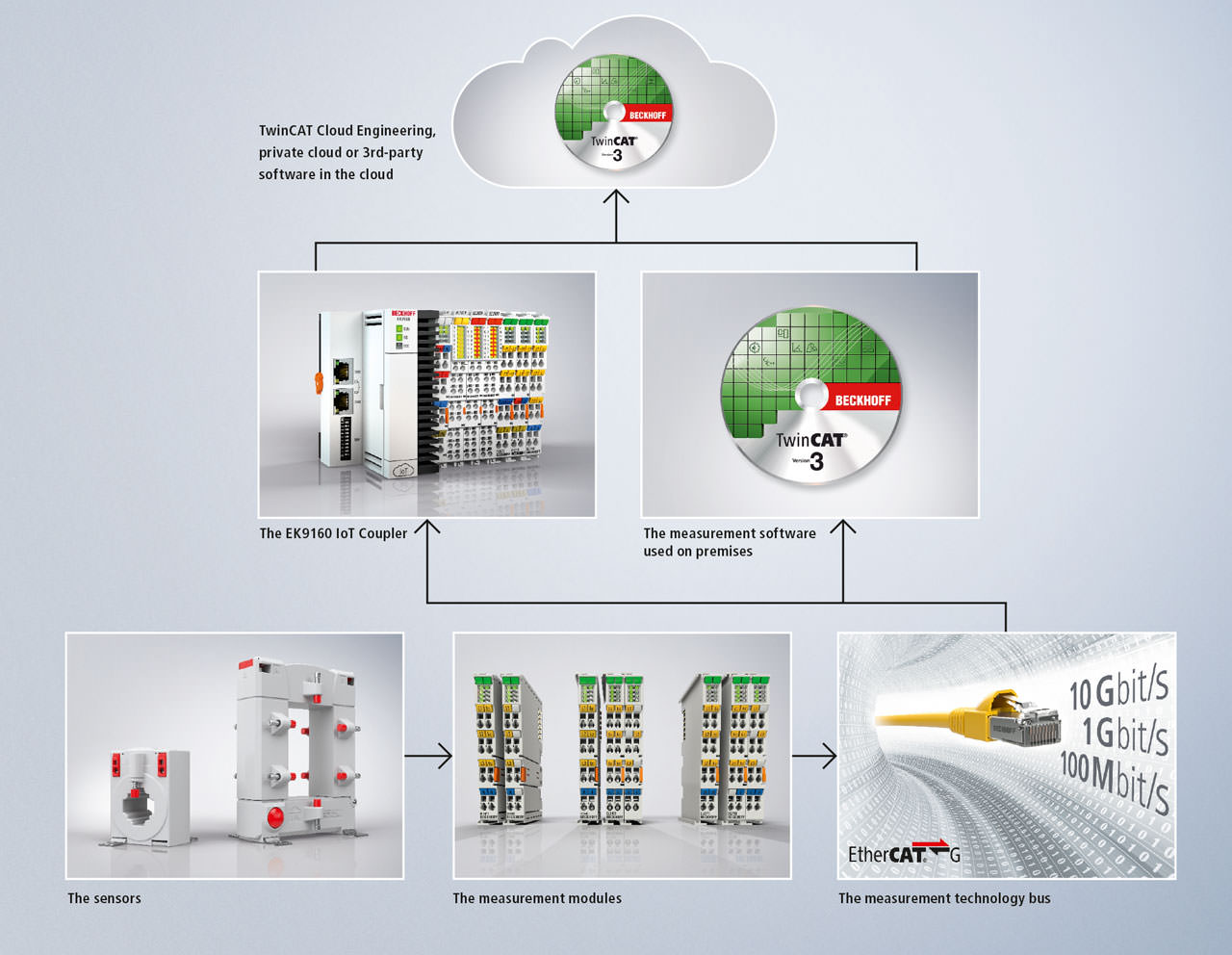
The end-to-end power measurement chain within PC-based control can be optimally adapted to requirements on both the software and the hardware sides.
Distributed power measurement
The new concept of distributed power measurement offers a particularly efficient and cost-effective way to obtain accurate power data even from more complex systems. Its central element is the 6-channel EL3446 input terminal for measuring up to 1A of AC/DC current. It allows the user to determine precise power values even for physically separated voltage and current measurements.
What makes the EL3446 special is its ability as a current power measurement terminal to determine all relevant electrical data of the supply network, including all actual power measurement values. The voltage values required for the calculation of power data are transmitted to the terminal over EtherCAT by a 3-phase EL3443 power terminal (installed only once per network) and synchronized via the distributed clocks in EtherCAT.
The active power and energy consumption are computed for each of up to six connectable phases in the EL3446. This makes the effective voltage and current values as well as active, apparent and reactive power, frequency, phase shift angle and harmonics available for grid analysis and energy management.
This concept of distributed power measurement – with just one EL3443 and any number of EL3446s – minimizes the hardware and installation effort and eliminates the wiring requirements for the voltage distribution. In addition, the per-channel cost of the power measurement is reduced by almost 50%without having to reduce the scanning speed if the number of measurement points rises.
Another benefit is that only the EL3443 power measurement terminal must be protected with fuses. This eliminates the need for the downstream fuses required with conventional power measurement systems.
Broad spectrum of solutions
The SCT series current transformers serve as the starting point for the seamless power measurement chain within PC-based control. The broad portfolio of models covers all relevant applications from 1 to 5,000 A and from ring-type and split-core transformers to 3-phase transformers.
This allows the user to implement reliable power sensors as a standard component of the PC-based control system directly in the field with the option to choose between concepts that are highly scalable through a wide range of designs and performance classes.
The SCT portfolio is extremely broad, ranging from low-cost 3-phase transformer sets for building technology to standard industrial transformers for machines to solutions for inspection stations and test benches with extra-high precision requirements.
The choice of the appropriate product category depends on the type of usage, with ring-type transformers being particularly suitable for cost-effective and accurate data collection in new installations. Because of their easy installation, split-core transformers are predestined as an easy retrofit solution.
The EtherCAT power measurement terminals are also finely scalable and can be used for applications ranging from maintenance and closed-loop controlling to power monitoring. In terms of performance categories, they differ by their accuracy and speed in data acquisition with bandwidths ranging from seconds and milliseconds to microseconds for oscilloscope functionality.
For simple measurement tasks such as the monitoring of voltage, frequency and phases, Beckhoff offers the EL3483 as a network monitor and the EL3423 for power measurement.
Terminals in the EL34xx series handle measurements in the lower millisecond range, for example for closed-loop machine control applications.
Power monitoring with the momentary-value capture of current and voltage with microsecond accuracy, for example in test racks, can be implemented with the high-performance terminals in the EL37xx series. Their ability to access instantaneous values of current and voltage in the PLC makes a particularly thorough system integration possible.
Compared to the EL37xx series, the EL34xx series features much easier programming through pre-scaled SI units, statistical analysis directly from within the terminal, and a warning function when predefined upper and lower limit values are violated.
With their many special functions, the EtherCAT power measurement terminals offer other additional benefits. These include features such as min/max/average analysis, power total over preset intervals, user-controlled input signals, and harmonics analysis of current and voltage up to the 63rd harmonic. Also gaining importance is the measurement of fault or differential currents, which the EL3453 includes by default with its integrated 4-current measurement channel, which makes it possible, for example, to find insulation faults before the power supply to a machine is suddenly interrupted.
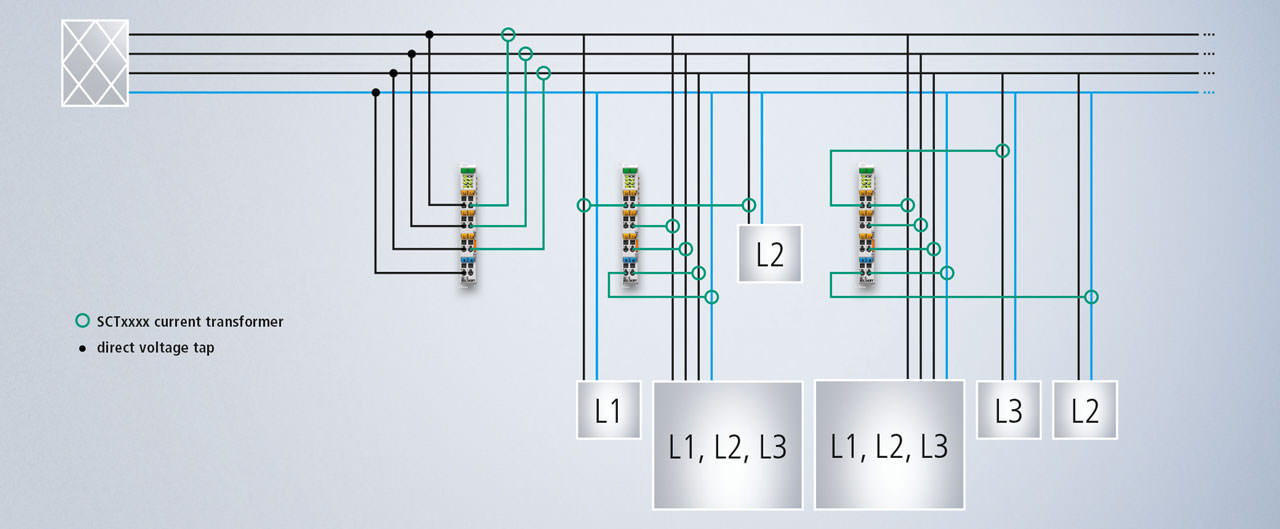
With distributed power measurement, a single voltage measurement can be connected digitally to any number of current measurements, making it easy to capture exact power values at each metering point.
Cloud communication & data analysis
The power measurement data can be transmitted to the cloud either via the local control PC or the EK9160 IoT Coupler. With the help of TwinCAT automation software, all machine functions ranging from engineering, PLC, motion control, safety management, visualization and measurement technology to communication are governed by the local control PC.
In addition, TwinCAT Power Monitoring provides special network analysis functions. With the IoT Coupler, power data can be transferred safely and easily via communication protocols such as OPC UA PubSub or MQTT to the desired cloud environment enabling functions such as cloud-based engineering, centralized data analysis and easy integration with storage services of various public cloud platforms.
The special feature of the EK9160 IoT Bus Coupler is its ability to connect EtherCAT I/O directly to the IoT with no need for a specific control program. By transferring the E-bus signal representations to various IoT communication protocols, the EK9160 makes it possible to integrate I/O data into cloud-based communication and data services easily and in a standardized manner. It requires neither a controller nor programming, i.e. users can parameterize the I/O data via any browser via a simple configuration dialog with the integrated web server.
The respective cloud service and security functions such as authentication, encryption, a.o., can also be easily configured via a browser. Once the parameters have been set, the bus coupler sends digital or analog I/O values, including the associated timestamps, to the selected cloud service. If the internet connection is interrupted, the I/O data to be transmitted can be buffered locally.
Users can optimize their power management by performing fast, cloud-based analysis of their power data. As the ideal solution for this purpose, TwinCAT Analytics allows for selective or continuous data analysis depending on the user’s needs. While the TwinCAT Analytics Service Tool improves and simplifies the commissioning processes for technicians, for example, the Analytics Workbench features enhanced capabilities and supports the automatic generation of program code.
And with 24/7 runtime deployment, the Analytics Workbench makes consistent and seamless data analytics possible. In this way, machine manufacturers can offer their customers individual data analytics solutions and become themselves providers of new predictive maintenance concepts.