TechnologyJanuary 22, 2022
TwinCAT software solutions for networked machine control
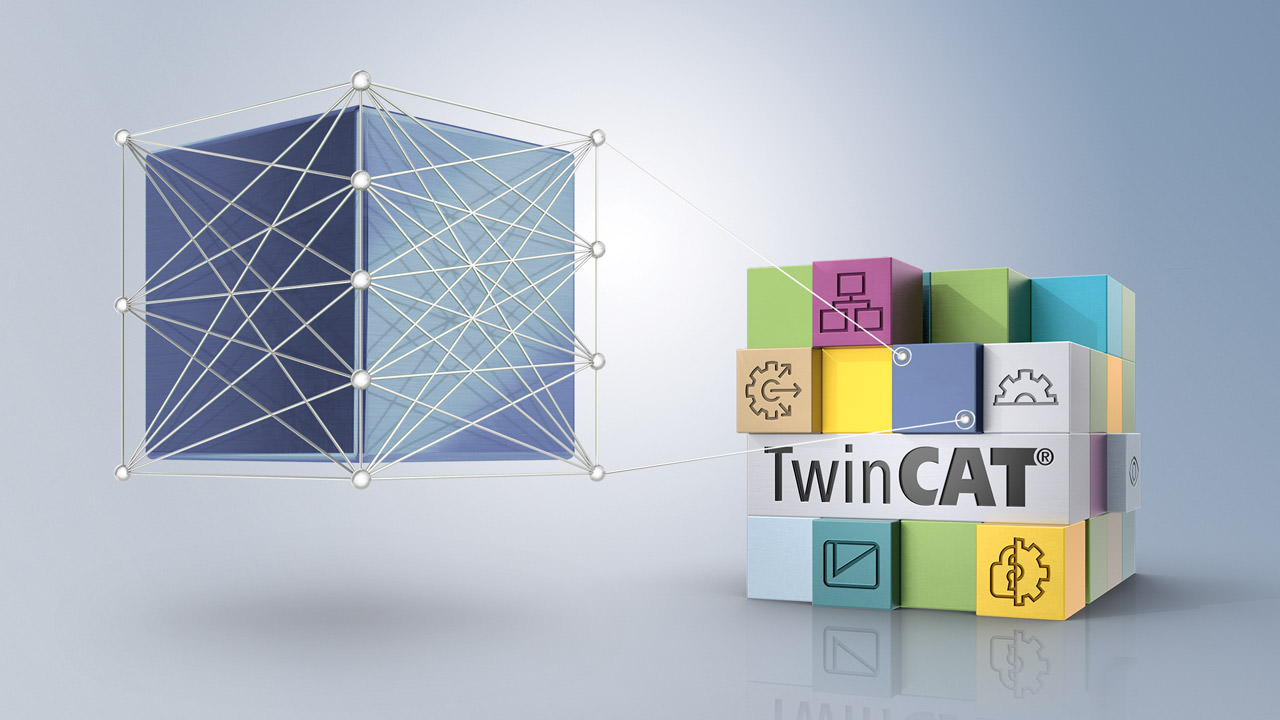
New automation and machine control networking solutions include direct integration of OPC UA Pub/Sub for real-time communication, a server inference engine for increasing machine learning requirements and a TwinCAT/BSD Hypervisor that increases availability through integrated virtual machine environments.
Software and hardware innovations are the heart of advances and new capabilities for automation and control applications. New TwinCAT solutions from Beckhoff including direct integration of OPC UA Pub/Sub, a server inference engine for increasing machine learning requirements and TwinCAT/BSD Hypervisor as a new system feature that increases availability through integrated virtual machine environments.
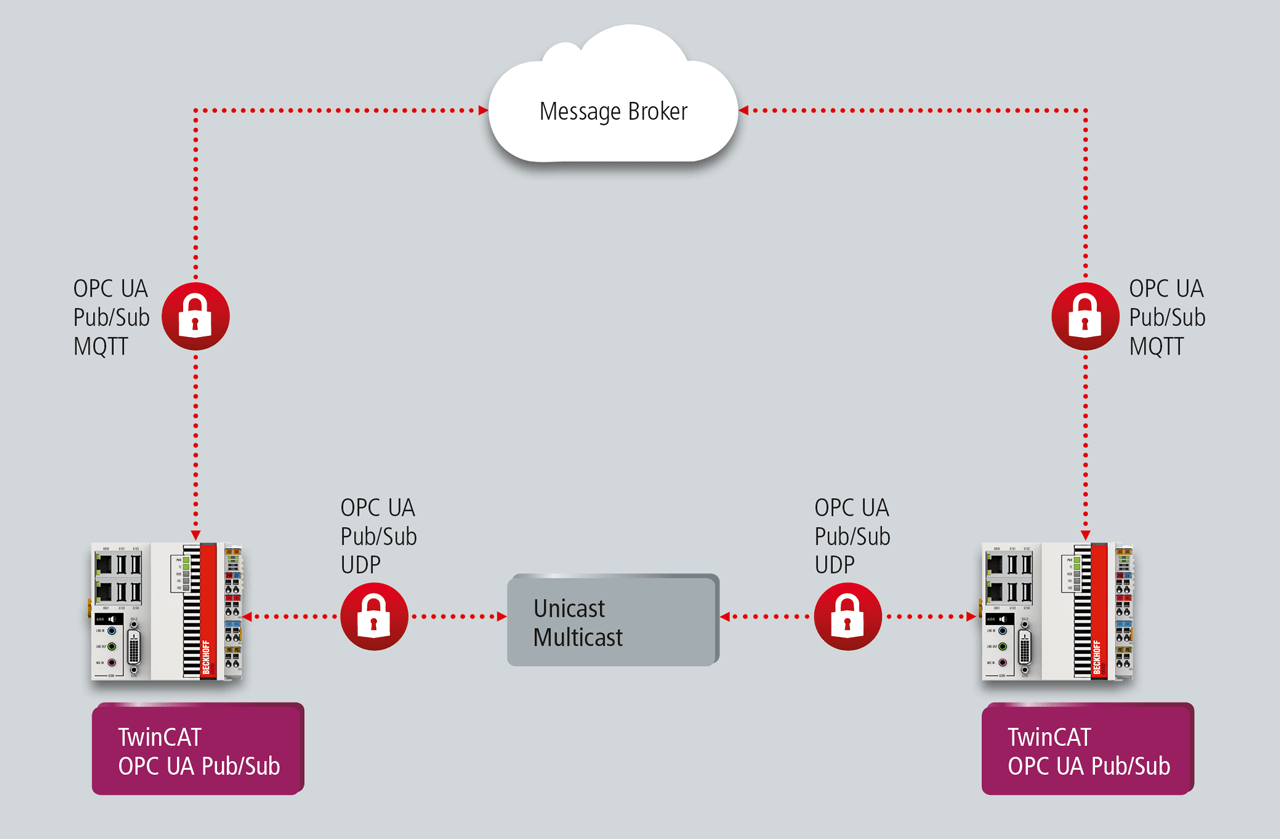
With PC-based control and TwinCAT 3, Beckhoff supports the extension of OPC UA to include publisher/subscriber communication.
PC UA Pub/Sub
Direct integration of OPC UA Pub/Sub communication into the TwinCAT 3 runtime paves the way for straightforward realization of machine-to-machine (M2M) and device-to-cloud (D2C) scenarios based on the OPC UA Pub/Sub specification.
With a new extension of the OPC UA specification, which Beckhoff played a prominent role in helping develop, the publisher/subscriber principle is being introduced into the established and standardized OPC UA communication protocol. Two different transport paths can be defined for data transmission: UDP and MQTT.
UDP enables efficient and real-time-capable data exchange in a local network between machines or machine components, whereas transport via an MQTT message broker primarily, but not exclusively, supports cloud scenarios. As an early adopter, Beckhoff implemented an initial prototype implementation of the UDP transport path back in 2016.
Now, the implementation of MQTT adds a second transport path. With the new TwinCAT 3 function OPC UA Pub/Sub (TF6105), Beckhoff provides a package that can be used to configure and use both OPC UA Pub/Sub UDP and MQTT Publisher and Subscriber directly in TwinCAT 3.
TwinCAT Machine Learning
With TwinCAT Machine Learning Server as an additional inference engine, TwinCAT Machine Learning also meets the increasingly growing requirements of machine learning (ML) or deep learning for industrial applications. This is because ML models are becoming more and more complex, the execution speed is expected to increase, and greater flexibility of inference engines is demanded with respect to ML models.
TwinCAT Machine Learning Server is a standard TwinCAT PLC library and a so-called near-real-time inference engine, i.e., in contrast to the two previous engines, it is not executed in hard real time, but in a separate process on the IPC. In return, basically all AI models can be executed in the server engine and this with full support of the standardized exchange format Open Neural Network Exchange (ONNX). Furthermore, there are AI-optimized hardware options for this TwinCAT product that enable scalable performance.
The TwinCAT Machine Learning Server can operate in classic parallelization on CPU kernels, either using the integrated GPU of the Beckhoff Industrial PCs or accessing dedicated GPUs, e.g., from NVIDIA. This provides an inference engine with maximum flexibility in terms of models and high performance in terms of hardware. Applications can be found in predictive and prescriptive models as well as in machine vision and robotics. Examples include image-based methods for sorting or evaluating products, for defect classification as well as defect or product localization, and for calculating gripping positions.
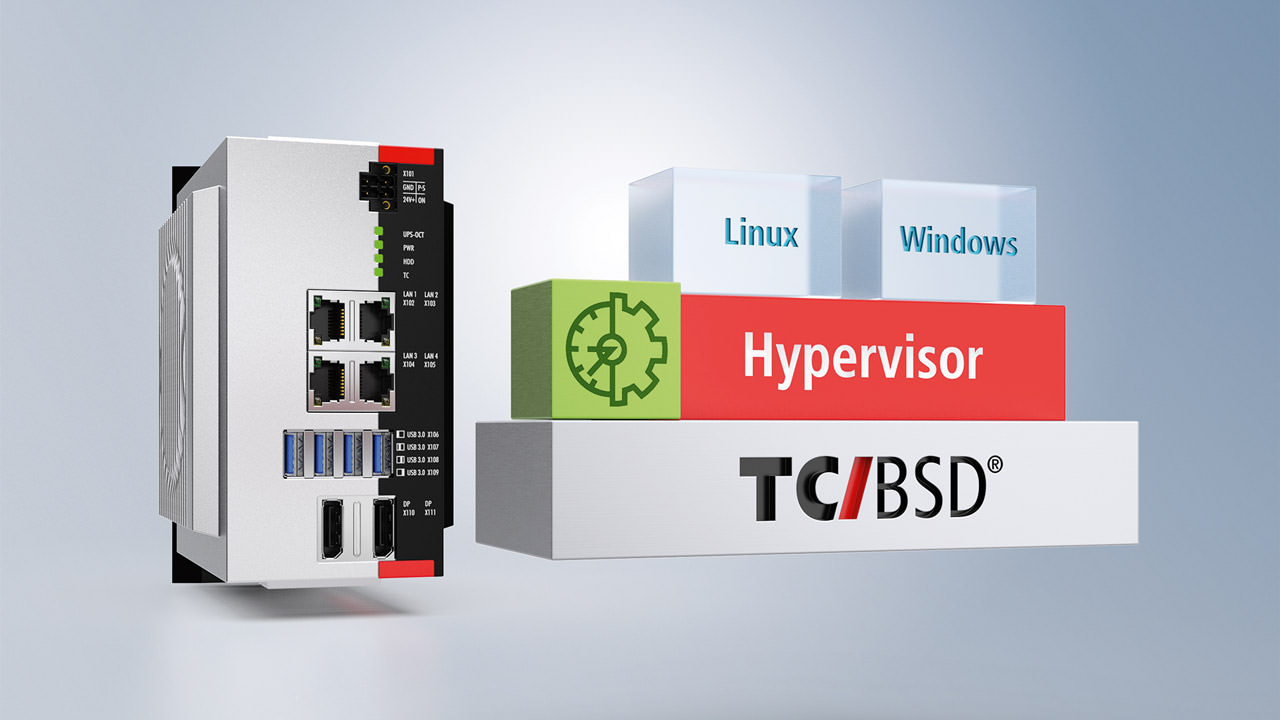
With PC-based control and TwinCAT 3, Beckhoff supports the extension of OPC UA to include publisher/subscriber communication.
Increased availability using integrated virtual machine
TwinCAT/BSD Hypervisor is new technology implemented in the TwinCAT/BSD operating system that enables the simultaneous execution of virtual machines (VM) and TwinCAT real-time applications on an Industrial PC. Optimized hypervisor integration in TwinCAT/BSD and matching configurations of Beckhoff software and hardware enable maximum performance of virtual machines while maintaining TwinCAT real-time properties.
The high-performance execution of virtual machines enables the strengths of different operating systems to be utilized on one Industrial PC and the security properties of the overall system to be improved by operating user environments in a modular and isolated manner.For example, TwinCAT real-time applications can be operated separately from a Windows desktop environment for machine operation on an Industrial PC. In this context, the Windows operating system is run in a virtual machine environment. Windows restarts, e.g., due to software updates, will therefore not interrupt machine control execution. This ensures machine availability since Windows is only restarted within the virtual machine environment and TwinCAT continues to run in the real-time context supported by the TwinCAT/BSD host.
Through the device passthrough feature of TwinCAT/BSD Hypervisor, hardware resources such as GPU, USB and/or network interfaces can be explicitly assigned to a virtual machine. In this way, access to the TwinCAT/BSD system by user and/or network interfaces can be limited, and the security of the control system can be improved. With TwinCAT/BSD Hypervisor, Linux distributions can be operated on the controller in addition to Windows, e.g., for running Linux containers. In this case, data communication between Linux containers and machine controller can be supported by host-only networks. This ensures that unencrypted network communication will take place exclusively locally between TwinCAT/BSD and the Linux container host, and confidential machine data will not leave the Industrial PC.
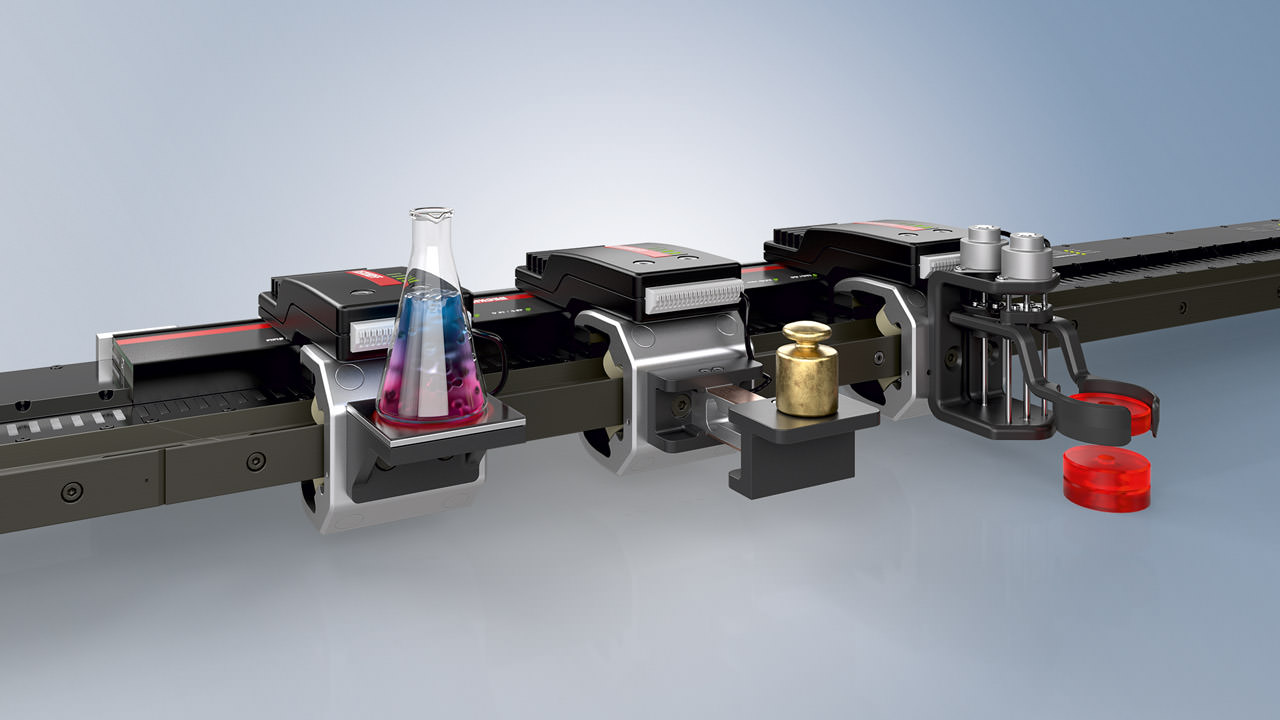
With the new No Cable Technology (NCT), XTS movers can become mobile handling or processing stations, thus expanding XTS into a highly flexible multi-robot system.
Contactless power and data transmission for movers
Contactless power supply and synchronous real-time data communication is now enabling individual XTS movers to be expanded into mobile handling and processing stations.
The modular XTS system has been expanded with NCT to include a special motor module as well as electronics that can be mounted on the movers. The hardware required for the transmission technology is fully integrated into the motor module, so that the existing functionalities and compact set-up are retained. No additional connections or supply lines are needed. The control of the hardware on the mover is fully implemented in TwinCAT. All known TwinCAT functionalities are available for simple project implementation.
For the first time, NCT makes it possible to process and check the quality of products on the mover while the process is running. Sufficient power and fast communication with the TwinCAT control system enable easy connection of sensors and actuators. The data communication is real-time capable and can synchronize system-wide events with µs accuracy in connection with EtherCAT. This opens up new solution options for the user, especially in the areas of product handling, machining and measuring in parallel with product transport, as well as adapting production machines for rapidly changing production lots.