TechnologyMay 18, 2023
Universal I/O: a simpler path to smart process plants
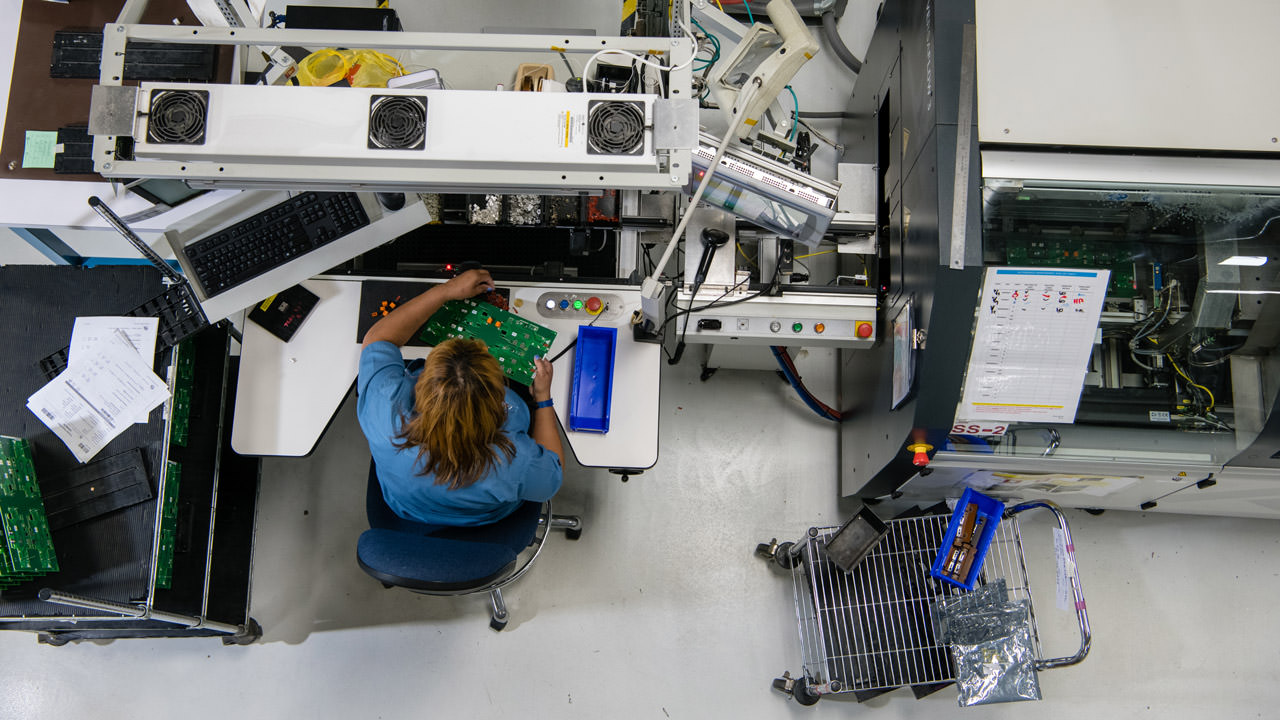
Universal I/O is a relatively young technology that will continue to deliver value to process operators. Advances combined with the benefits of universal I/O will mean process operators can expect more efficient workflows and fewer headaches when deploying new and smarter process applications.
Like everyone today, process operators are trying to reduce costs and project execution times. Smart manufacturing can help them do this in several ways, from digital engineering tools that can reduce cost and risk in the design stage, to smart sensors and instruments that can provide deeper insights into processes. But to deploy these capabilities, process operators are realizing they need to rethink how they manage the flow of data to and from their process devices.
Control systems in process operations have historically been designed and built with a set number and type of I/O modules. But these rigidly defined I/O layouts can be costly and difficult to change throughout a control system’s lifecycle.
During commissioning, for example, modifying an I/O layout to accommodate last-minute changes to the control system can throw a project off schedule and off budget. A seemingly simple change from analog input to digital input can require a new I/O module, potentially a new rack to house that module and a mess of wiring changes. And later, after a process is operational, new I/O cards can only be added if space is available for them in the enclosure.
These challenges are driving process operators to embrace universal I/O, which allows different I/O types to land on one I/O card. This greater flexibility can minimize the impact of late changes to the I/O and make projects overall more efficient, and make it easier for process operators to deploy smart devices throughout the life of a process.
The universal I/O difference
Traditional I/O requires that process operators use separate I/O modules for analog-in, analog-out, digital-in and digital-out connections. And while four card types isn’t a lot, they can create some big challenges.
Just consider the typical process used to implement distributed control systems (DCS) in process plants. Activities like system sizing, enclosure and system design, system configuration, factory acceptance testing (FAT), installation, and site acceptance testing (SAT) and commissioning happen one after another. These serial workflows make projects inherently inefficient because teams can’t work in parallel.
An even bigger problem is that system changes can happen late in projects. This leads to teams having to redo activities and potentially make card and wiring changes to the physical I/O that’s already been installed in the enclosure. These physical changes are not only costly but can also push back project timelines.
Universal I/O can make DCS projects more efficient because now it doesn’t matter where signals are landing – they’re all going to a universal I/O module. Control engineers can configure a control systems’ logic and displays, while at the same time another team designs and builds the enclosures. This parallel work can make better use of people’s time and shorten project timelines. And because universal I/O allows devices to be swapped out without changing I/O cards or wiring, late project changes are easier to accommodate.
Universal I/O also simplifies long-term changes. Process operations are rarely static. New processes are added. Efforts like debottlenecking projects are made to improve processes. And new devices are installed to create smarter, more efficient operations.
With traditional I/O, process operators need to plan for these changes by not only leaving open I/O capacity in their control panels but also stocking up multiple different I/O modules. Universal I/O allows process operators to stock only one type of I/O module and even reuse I/O modules for different purposes.
It’s also important to remember that universal I/O is just one part of a DCS. And by using a modern DCS with digital engineering capabilities, even greater savings are possible.
For example, a DCS that uses virtual image templates, or virtual appliances, allows engineers to build system elements – like process automation system servers, historians, and operator and engineering workstations – in a virtual environment. This allows those system elements to be built and configured more quickly, because engineers don’t need to wait for physical hardware to be in place.
Design tools that are available in the cloud can also accelerate projects by allowing distributed teams to design, build and test control code from a browser.
Enabling smarter processes
Process operators can use universal I/O modules in many ways to support and ease digital transformation initiatives.
For starters, the modules can give plant personnel access to helpful, contextualized information about the devices themselves to help reduce downtime.
Today, engineers typically need to write special code to monitor I/O modules for issues. But universal I/O modules with built-in diagnostics can automatically provide information about device health and faults on specific I/O channels. This can help technicians not only know that something is wrong, but also identify what the specific issue is and where it’s happening so they can quickly address it.
Process operators can also use universal I/O to add smart devices more easily to their operations.
Today, smart sensors and instruments can provide deeper visibility into processes and advance warning of potential problems, both of which can help plant personnel optimize operations and reduce unplanned downtime. With universal I/O, all the work that needs to be done to add these devices, from adding a backplane, to installing and configuring the smart device, can be done while a process is running. This can help process operators create the smarter, data-driven processes they need to compete with minimal disruption to their daily operations.
Another activity that universal I/O modules can help simplify is adding redundancy to process operations. Specifically, high-availability modules can be deployed in duplex configurations, allowing engineers to land just one wire for both the standard and redundant modules. This can save time and effort compared to setting up two separate modules side by side and using special wiring and coding to create redundant I/O modules.
Of course, security is always top of mind when deploying smarter, data driven process operations. Universal I/O modules can support a defense-in-depth security strategy with security measures like firmware encryption, module vendor certificates and secure boot functionality.
What’s next?
Universal I/O is still a relatively young technology. It will only continue to evolve and expand in the coming months and years to deliver more value to process operators.
Soon, for example, integrated safety I/O and high-availability safety controllers will be available that allow integrated safety I/O and base process control I/O to be mounted in the same rack. This will help reduce hardware complexity and the overall system cost in DCS projects.
New options like smart junction boxes that can be used with universal I/O are also emerging. These prebuilt and prewired enclosures with field termination panels for I/O further simplify DCS projects by reducing engineering and minimizing the work that needs to be done to deploy DCS projects at a process plant.
These advances combined with the benefits of universal I/O mean process operators can expect more efficient workflows and fewer headaches when deploying new and smarter process applications.