TechnologySeptember 1, 2020
SPE in industrial applications offers IP-protected solutions
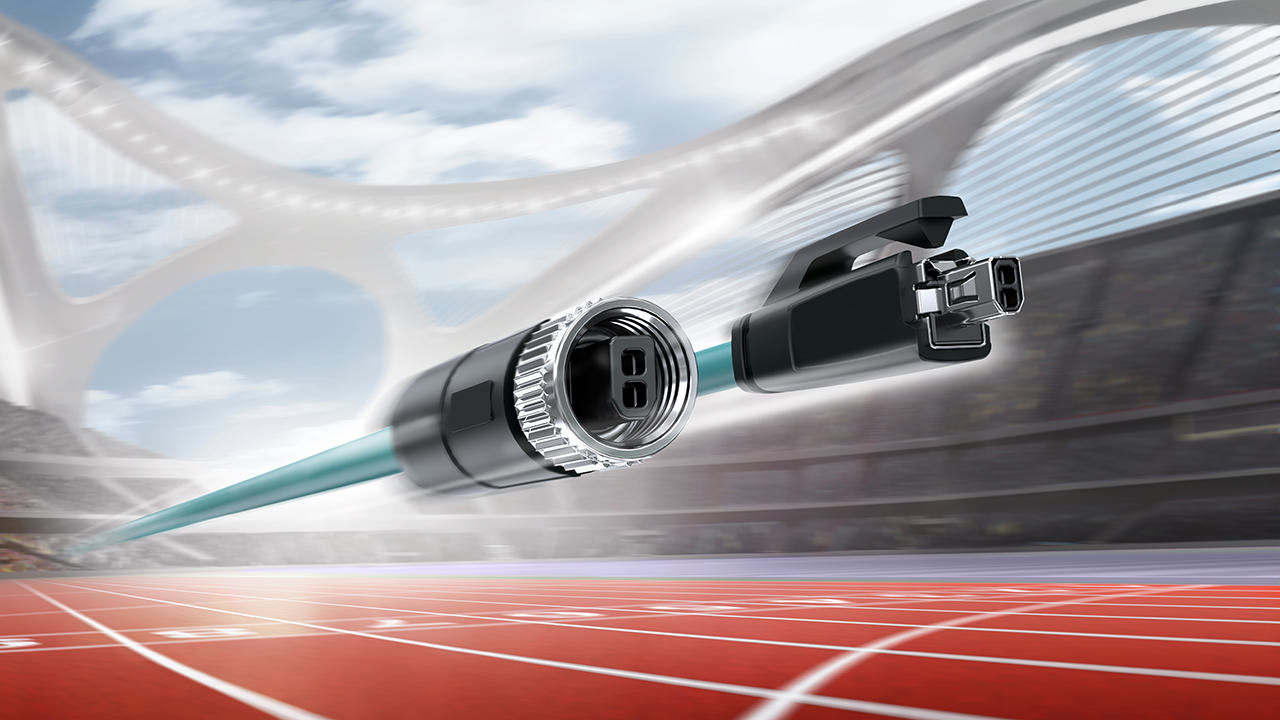
Single Pair Ethernet work continues with the aim of toughening up this evolutionary new technology for as many application scenarios as possible. But reduced cable weight, miniaturization and simplification of the connection technology will only come into play with achieving continuity with the overall infrastructure.
There can be no doubt that Single Pair Ethernet (SPE) is the future of industrial communication. In addition to the safety that a standardized solution offers users, application-specific customer requirements play a significant role.
The prevailing trends and innovations in the age of the IIoT (Industrial Internet of Things) all strive to bring product functions and solution requirements more in line with each other against the backdrop of digital transformations. When examining SPE more closely from this perspective, the following key features are readily mentioned: range of up to 1000 m, high data transmission rates over twisted pair, miniaturization at the device and in the field along with, last but not least, significant cost savings.
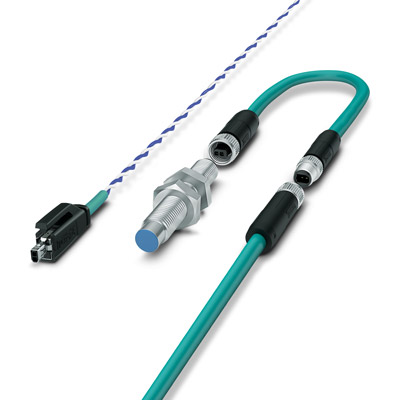
The little brother of M12: with full IP20 compatibility, M8 connectors are also suitable for fast servicing.
All of these aspects present many advantages, providing further support for the extensive and future-proof use of SPE. And behind all these advantages, there are countless customer and application requirements. The true skill of a component provider now lies in their ability to reconcile all of these aspects. If they do not succeed, because specific customer requirements cannot be met, a connector standard gradually develops over time, which the world does not actually want or need. This is why numerous large and small companies are working on the expedient implementation of this technology.
The basic framework for the future of industrial communication technology is emerging in parallel in various committees and projects. New communication standards such as the Open Platform Communications Unified Architecture (OPC UA), Time-Sensitive Networking (TSN), and 5G form the basis for integrated networking from the sensor through the machine and higher-level systems to the cloud. The new standards will far outperform existing protocols and interfaces in terms of cost, data throughput, latency, and deterministic aspects. As a technology leader with more than 30 years of experience in industrial communication, Phoenix Contact is therefore actively involved in all of the relevant standardization committees. The goal: nothing less than a new, cross-manufacturer communication standard for industrial automation.
OPC UA is already used as the higher-level communication standard in systems. OPC UA is now being gradually extended with standardized application profiles in the field for I/O, safety or drive applications, for example. Furthermore, standardized device models are being defined for the uniform configuration and diagnostics of devices in the network.
It starts at the sensor…
The overarching goal of consistent Ethernet communication will always be the IP-based integration of all components into a communication system. Many of the sensors that are currently used are not IP-capable.They have to be integrated into the communication system using other systems such as IO-Link. With regard to Industry 4.0 and predictive maintenance, a consistent Ethernet communication system offers significant advantages over existing stand-alone solutions.
M8 and M12 connectors are a widely used connection technology in industrial automation. The Ethernet system codings that are used for circular connectors are proof of this with D- and X-codings used for M12 and D-coding used for M8. In this context, the focus is on easy integration into standard sensor housings together with maximum possible robustness. Due to the significantly cheaper integration of pin contacts and an external thread on the sensor side, it makes sense to equip the SPE field side with socket contacts. Retaining this connection provides sensor manufacturers with an option for easy integration into the sensor.
Male and female connectors
Retaining the sensor connection does not just provide advantages for the relevant manufacturer, there are also clear advantages when it comes to cabling in the field. In the context of modern M8 and M12 installations, there is a lot of talk about flying leads or even field coupling. This is why modern sensor/actuator cabling is chiefly designed as a male/female connector version. One end is fitted with pin contacts and the other end with socket contacts. This also means that one end must be equipped with an external thread and the other end with an internal thread. Cables can then be extended without having to use a female/female or male/male adapter, as is typically the case with RJ45. This type of cabling topology provides a high degree of flexibility for users in the field as well as SPE integrators. Full compatibility with SPE connectors with IP20 degree of protection also ensures fast servicing.
Miniaturization – not at any cost
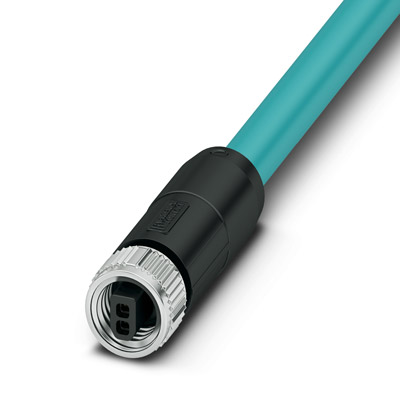
For external thread and male contact on the sensor side: female contacts in the field cabling simplify integration into the sensor infrastructure.
The M8 version of the popular M12 connector has become established as the standard for compact connections: One third smaller than the M12, the M8 is still suitable for industrial use and is easy to handle. The M8 is already widely accepted and is being used successfully in many fields – especially for the connection of compact sensors in machines to obtain process-related information or to supply power to small devices. Although miniaturization is also one of the megatrends in industrial cabling, it must be determined exactly how and where this can be implemented effectively.
While most of the cables used in industrial automation are between AWG (American Wire Gauge) 22 and 26, things are quite different in process automation. Due to the longer distances that have to be covered here, much thicker cables are used that range from AWG 16 to 18. A cable in a process application can therefore quickly reach an outside diameter of 7.5 to 8.5 mm. In this case, the cable easily matches the outside diameter of the connector. There are many reasons why it would not make sense to connect a miniaturized connector to such a cable.
This not only applies to protected connectors, but also connectors in IP20 applications. Considering the aforementioned conditions, it likewise does not make sense to implement the smallest possible footprint on the printed circuit board or significantly increase the port density compared to RJ45. This is why the product launch is initially focusing on pre-assembled cables in the AWG 22 range.
IP20 versions as well as IP65/IP67 versions are available for device integration. The continuous development of the product range ensures consistent use in all fields of application. The aim of the Single Pair Ethernet System Alliance is to combine continuity with practical implementation.
Size M8 – in the shadow of M12?
When it comes to connectors for sensor/actuator cabling or data transmission, talk usually turns to popular M12 connectors. As the technological shift to SPE continues, along with the demand for miniaturization, the M8 size will achieve further significant growth rates in the market. This growth will be further boosted by male/female connector versions for the field and device side. The advantages of M8 with regard to SPE:
- Cabling structure remains unchanged
- Full connection compatibility with the IP20 pin connector pattern for fast servicing
- Wide range of applications due to the modular layout of the pin connector pattern in various housing forms
Summary
Work continues steadfastly on SPE with the aim of toughening up this evolutionary new technology for as many application scenarios as possible. The advantages namely the reduced cable weight, miniaturization, and simplification of the connection technology only come into play with the continuity of the overall infrastructure. This innovation will influence the network structure in all fields of application from building automation through factory automation to process automation. In this context, no one should lose sight of the fact that decisions made today will determine where Ethernet will go in the future.
Manuel Rüter, Product Manager for Industrial Field Connectivity, Phoenix Contact.