TechnologySeptember 1, 2020
TSN in manufacturing recovery and future-proofing of factories

TSN technology is already able to address the demands of Industry 4.0 that are emerging now by maximising the use of the increasingly common gigabit bandwidth. In addition, it holds the promise of being able to evolve accordingly to meet future demands while protecting existing investments.
As some global manufacturing sectors face unprecedented pressure, there has never been a more opportune time to implement game-changing automation technologies. Those businesses that have been adopting technologies able to provide greater transparency, higher productivity and better process management will be better placed to move forward and adapt to the new manufacturing landscape.
This article looks at how manufacturing companies can invest in key solutions that support current needs while also future-proofing their activities.Current production challenges mean that there is not just demand for factory automation solutions that can ensure continued manufacture and supply of goods, but that provide the transparency and productivity benefits promised by Industry 4.0 too.
Bearing in mind that the lifecycle times for automation hardware are as long as 20 years, there are many plants operating with aged production systems that could benefit from an update. This is where industry-leading open communication technologies can step in to deliver these necessary improvements in process transparency and productivity.
The case for TSN
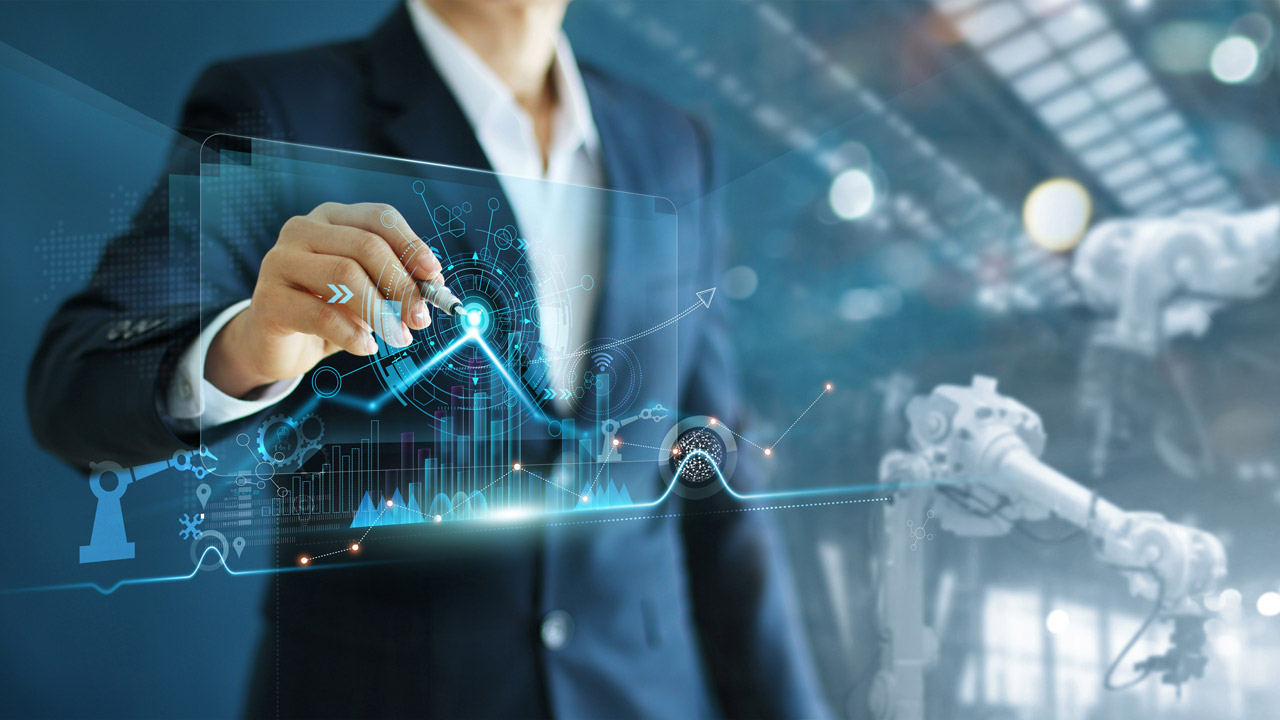
By removing the need for physical separation of critical and non-critical networks, TSN is helping to create a convergence between IT and OT systems in factories.
As automation plant lifecycles typically last many years, it is essential to know what technologies show the most promise of longevity, rapid return on investment (ROI) and clear technical benefits. It is clear to most automation specialists that one of these will be Time-Sensitive Networking (TSN).
This is a set of Ethernet sub-standards for the OSI-Layer 2 defined by IEEE 802.1. These aim to improve determinism and reliability in industrial Ethernet-based communications by creating accurate time synchronisation across a network, in addition to technology for traffic prioritisation.
Therefore, businesses can combine multiple types of traffic on a single network, with no loss of performance for critical control-related tasks. The end result is an industrial Ethernet infrastructure that permits all kinds of traffic to coexist, regardless of whether it is critical safety or motion control-related data, general control information, video frames from inspection systems, periodic shift logs or even emails.
This consequently delivers several technical benefits. Networks are able to fully leverage the benefits of gigabit bandwidth, their infrastructure is simpler and therefore less costly to design, implement and maintain. Ultimately, systems can be rolled out and start their operations in a shorter time.
By removing the need for physical separation of critical and non-critical networks, TSN also creates a convergence between information technology (IT) and industrial operational technology (OT).
This convergence directly addresses the competitive pressure of Industry 4.0 in order to deliver corresponding business benefits. Key results include better transparency and management of processes, product quality improvements, increase in output as well as reduced downtime. In addition, the enterprise can become more responsive to customer demands and better able to support its business.
An evolving solution
While many of the IEEE 802.1 standards are now complete, some are still under development. Moreover, the IEC/IEEE 60802 working group is still standardising TSN profiles for industrial automation. Hence, TSN is still evolving. The counterpoint to this is that projects have to be done now, and TSN’s maturity level is such that vendors have already started to market solutions. As with most technologies, TSN will continue to evolve over time.
However, any risk of moving forward now is mitigated by the fact that the organisations involved have a strong track record of ensuring backwards compatibility. So while TSN will continue to evolve, future iterations will be compatible with what is available today. TSN, as it stands today, can deliver all the benefits outlined earlier, and hence this creates a compelling case for using it to maintain a competitive advantage now.
Specific examples of applications that can benefit from TSN include those that would profit from combining several types of control on one network. For example, a converting application such as a printing press could combine high precision motion control for registration with visual inspection of the process, along with systems related to operator safety. TSN allows them all to coexist on a single network, simplifying system design, reducing cost and increasing uptime.
Time to implement TSN
Plant lifecycles are typically measured in decades. With this in mind, current TSN solutions are a safe bet. The technology is already able to address the demands of Industry 4.0 that are emerging now by maximising the use of the increasingly common gigabit bandwidth. In addition, it holds the promise of being able to evolve accordingly to meet future demands while protecting existing investments.
Its base technology, Ethernet, was first conceived in the early 1970s and has already proved its ability to remain relevant over time. Hence, TSN will likely continue to benefit from this ability and offer advantages during the current plant lifecycles and beyond.
TSN can act as a powerful ally to support businesses to address current manufacturing challenges. The technologies that offer TSN functionalities now are also providing migration capabilities for the future.
To support advanced industrial communications, the CLPA organisation has recently developed CC-Link IE TSN technology, the first open industrial Ethernet to combine 1Gbit bandwidth with TSN functionalities. Thanks to these key features, it offers an effective migration solution that can address current manufacturing needs while acting as a gateway to the future of connected industries. By implementing this technology businesses are enabled to handle the large volume of traffic associated with Industry 4.0 data-driven manufacturing. As a result, they will not only optimise their current operations, but also future-proof them.