ApplicationsMay 27, 2019
Wireless mesh networks in today’s petrochemical industry
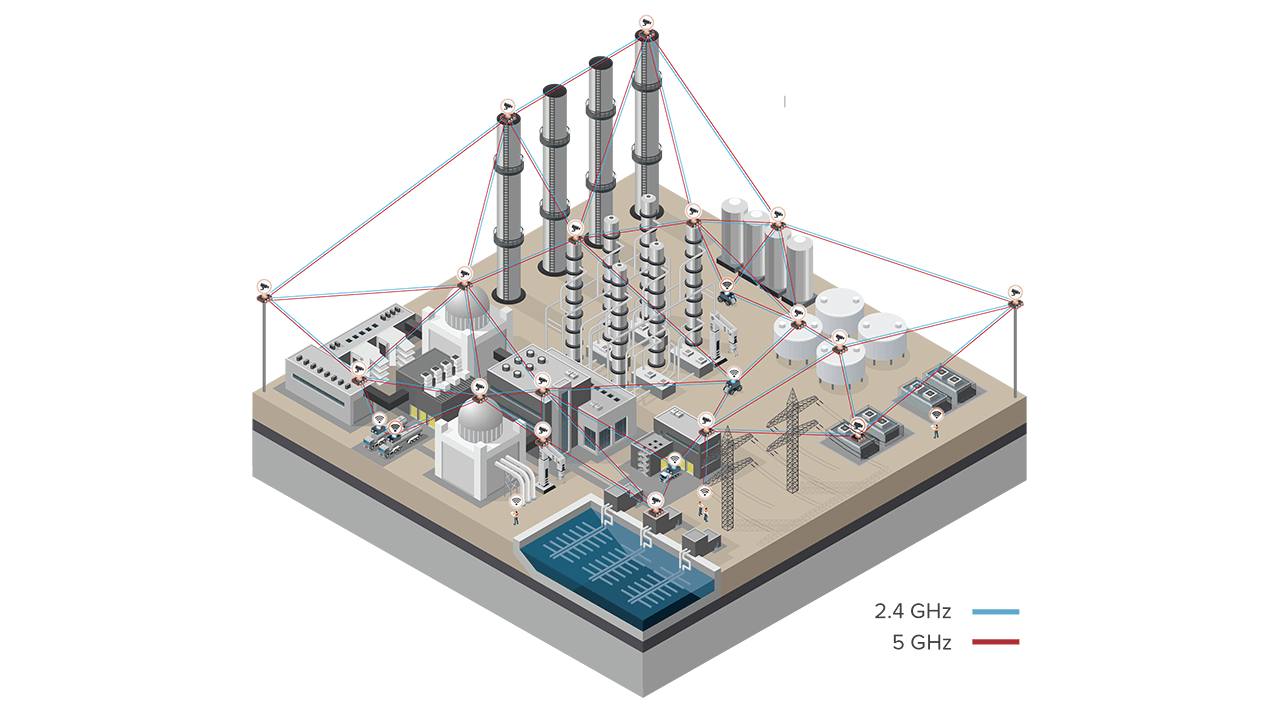
Scalable, high-bandwidth kinetic mesh networks are providing unmatched connectivity for upstream, midstream, and downstream applications in the petrochemical industry. IoT autonomy, advanced data analytics, and mobility are helping to significantly improve productivity and reduce operating costs.
The global petrochemical industry has continued to grow impressively, and it’s showing no signs of slowing down. Competitive pressure is pushing petrochemical plants to adopt new innovative technologies, whilst improving levels of safety during the chemical production process, to optimize production levels and stay ahead of its rivals.
Next generation solutions such as Augmented Reality (AR), autonomous robots, and real-time equipment analytics have taken centre-stage and are moving to Industry 4.0 which is emerging as the answer to overcoming challenges within plants such as personnel safety, whilst meeting the demands of plant operators for enhanced productivity. According to research from PWC, 60% of chemical companies state that Industry 4.0 data and analytics are of high importance today, while 88% believe they will be of high importance in five years.
To make this a reality, applications need IIoT connectivity in order to function and this is a requirement that Wi-Fi and two-way radio WAN alone cannot fulfill. The information network is the foundation of complex petrochemical operations and it is the cornerstone on which the productivity, safety, and profitability of an organization rely upon. Bandwidth and availability are precious, but downtime is intolerable and if plants are to take advantage of IIoT, their mission-critical applications need to run on a communications network that offers highly reliable, agile, and adaptable connectivity in a diverse and evolving mobility-driven environment.
Petrochemical plant connectivity
IIoT is a crucial part of establishing Industry 4.0 capabilities. Deploying a network to support these levels of connectivity demands in a dynamic and potentially hazardous environment can be extremely difficult. Balancing facility and production growth in the petrochemical industry, with employee safety, is of optimal importance.
Therefore, the network must keep up to pace with a number of demands. For instance, many petrochemical plants operate multiple networks in order to accomplish separate communications needs for employees. This often outweighs the burden of maintaining a Wi-Fi network for data and a two-way radio WAN for voice which can generate significant costs and can be a notable drain on resource demands for daily operations.
Petrochemical plants can contain an abundance of explosive and flammable gases, such as ethylene, propylene, butadiene, and other vapours, which makes maintaining safety in danger zones a top priority. To prevent equipment from sparking and starting a fire, networking infrastructure must be kept in an explosion box as a precaution and this complicates installation further. Mission-critical operations carried out in petrochemical plants, from the first initial deployment to complex day-to-day plant operations require constant connectivity.
Losing signals for a short span of time can result in productivity loss and in the worst-case scenario put plant workers’ safety at risk. In essence, plants cannot afford to risk any loss of signal. With petrochemical plants undergoing significant expansion, choosing the wrong industrial network solution could mean a plant’s investment will be unable to adequately connect its operations.
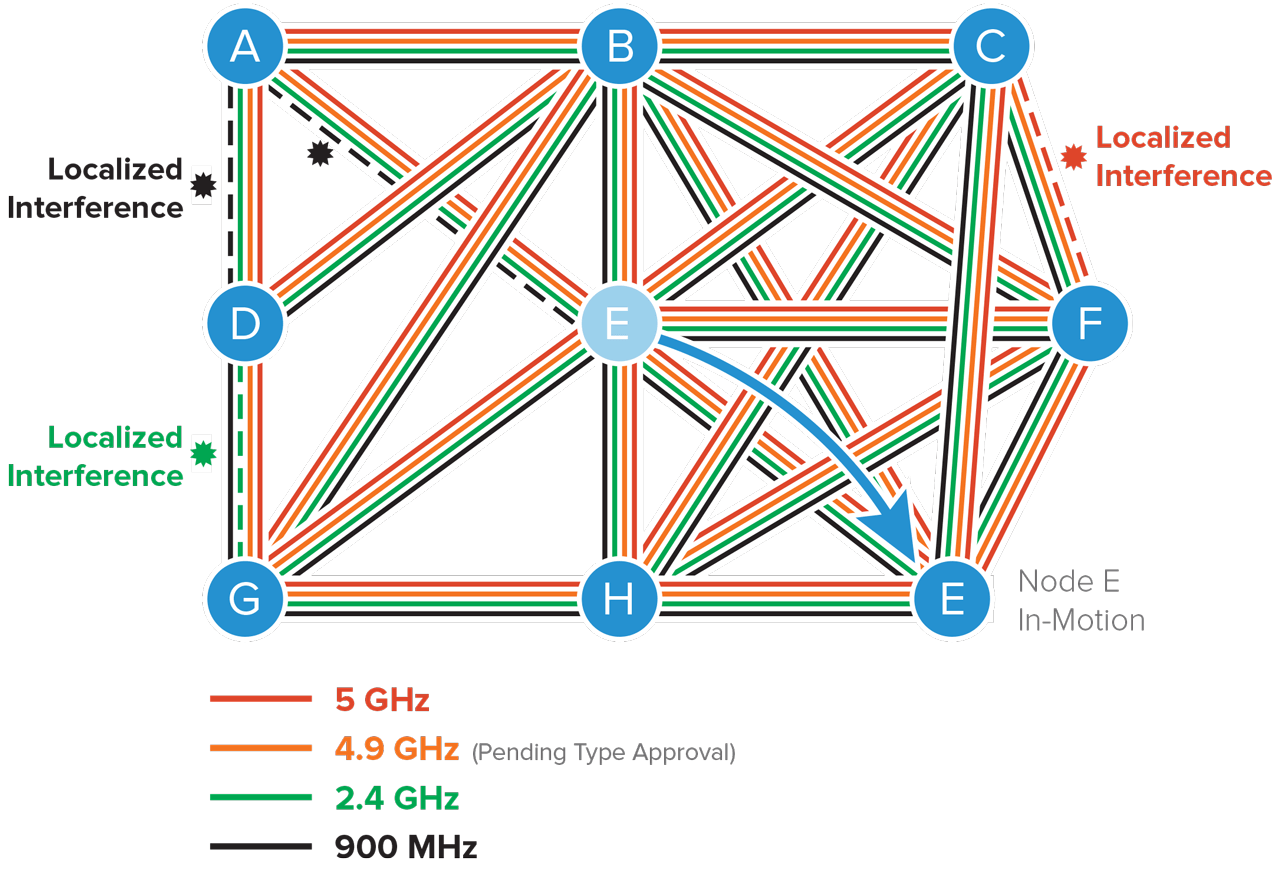
How a multi-frequency BreadCrumb network adapts to changes caused by the movement of BreadCrumb node E.
A new kind of network
To successfully fight through these obstacles and enable the capabilities that Industry 4.0 brings with it, petrochemical plants must utilize a different kind of network—an Internet of Things (IoT)-enabling network that is more dynamic than Wi-Fi networks or two-way radio WAN. Once this has been done, the petrochemical industry can take advantage of the innovative technologies that can maximize productivity, improve safety, and helps organizations survive in the midst of its petrochemical competition.
A feasible solution is for petrochemical plants to implement a mesh network topology, a resilient architecture constructed of nodes which allows a multitude of devices to wirelessly connect to each other; each node is capable of communicating data across the network until it reaches its target destination. This technology is gaining increased interest due to its skill set in handling the surge of data that comes in conjunction with the enhanced number of IoT connected devices.
Petrochemical operations rely on a variety of vehicles, equipment, heavy machinery, and personnel, dispersed across a large, rugged terrain and all of which require reliable, high bandwidth, and mobile communications. Every aspect of exploration, extraction, and production must always be carefully monitored and managed to ensure continuous operations and cost efficiency. A mesh network can provide real-time, site-wide communications for employees, vehicles, drills, wellheads, video cameras, smart meters, sensors, laptops, smartphones, and other assets.
However, not all mesh networks offer the same benefits. Some can be arduous to install. Some need continuous, labour-intensive maintenance. Plants need mobile wireless broadband connectivity that can meet their demands and is simple, instantaneous, and robust in any application.
Ensuring critical connectivity
This is possible through a combination of wireless network nodes and networking software, which utilizes any-node to any-node capabilities to continuously route data via the best available traffic path and frequency for a number of nodes with extremely low overhead. Greater mesh networks can connect with any Wi-Fi or Ethernet-connected device to deliver low-latency, high-throughput data, voice, and video applications.
The right mesh network can prove to be a secure and converged solution for plants, reducing the need to maintain multiple networks by supporting data, voice, and video. This solution reduces the total cost of ownership and simplifies the work demands of employees by allowing them to centralize their communications to a single device. Depending on the mesh network provider, certain nodes are beneficial to deploy in any corner of a petrochemical plant without the need for mounting in explosion boxes.
Look for wireless network nodes that can be attached to both fixed and mobile assets including equipment, vehicles, and facility infrastructure and they can maintain multiple immediate connections between peers whilst sending and receiving data on multiple frequency bands. They need never break connections to form new ones, meaning the connections are maintained until they are no longer needed. With high-bandwidth speeds across multiple mesh node hops, a mesh network offers extremely low latency for real-time, plant-wide connectivity, even at the network edge—making it the perfect solution for mission-critical operations which require ubiquitous connectivity.
Mesh networking software can direct traffic over all meshed connections by dynamically load balancing and routing data around signal blockage from moving assets and potential interferences. This ensures that data packets get to their destination via the fastest path available. This eliminates the need for a controller node and therefore the network will have no single point of failure.
As petrochemical plants are dispersed over widespread areas, they are regularly adding new bandwidth-intensive applications to support continued growth. A superior mesh network topology can rapidly evolve as a plant expands. In fact, as more nodes are added, more paths to direct mission-critical data are naturally formed – and, with more paths, the network becomes more resilient.
Petrochemical plants require military-grade data security as they are potential targets for high-risk network security attacks. A mesh network can protect a plant from security breaches thanks to multi-layered, military-grade security for network traffic, making it incredibly difficult to penetrate. It boasts multiple cryptographic options, configurable data and MAC address encryption, and configurable per-hop, per-packet authentication between nodes.
IIoT using mesh networks
A mesh network is an effective alternative to prevailing limiting technologies like Wi-Fi and two-way radio WAN. Once a petrochemical plant has enabled IIoT connectivity, there are a multitude of applications that can be implemented to drive optimized production and increase safety. It means a plant can stay ahead of its competition and can immediately exploit advantages such as RFID tracking of personnel and contractors, which is enabled through everywhere connectivity and provides real-time tracking of workers across a plant. This not only allows operators to monitor personnel’s ongoing safety status but also aids in emergency extraction in case of an incident.
Mesh networks also support bandwidth-intensive applications such as asset tracking and optimization, enabling monitoring of a plant’s assets in real-time as well as predict equipment maintenance needs and maximize efficient machine movements on the production line. Plants can lay the groundwork for applications, such as 24/7/365 equipment autonomy, with plant-wide asset mobilization, which increases petrochemical output while keeping employees out of dangerous areas.
Furthermore, products and equipment can be protected from theft with real-time video surveillance. With round-the-clock views into operations, a plant can also gain insights into plant performance and events on the production floor. And thanks to AR, the productivity of employees can be enhanced, while also removing them from potentially hazardous petrochemical environments.
This highlights the benefits of wireless mesh networks for the petrochemicals market, which can deliver secure, reliable broadband coverage anywhere and at any time.
Mesh networking in the new age
Although the numbers are not overwhelming, it does highlight how an IIoT-enabling mesh networking solution can make operations smarter and employees safer. It goes a long way in showing that this new kind of network is intended to provide continuous wireless connectivity to support numerous applications.
A key upside of deploying mesh networks is the speed at which a complete IIoT solution can be deployed very quickly and cost-effectively as there are no cables to run. This means petrochemical plants can maximize this sector of industrialisation much sooner than they think.