TechnologyNovember 12, 2019
IIoT benefits without heavy front-end investment
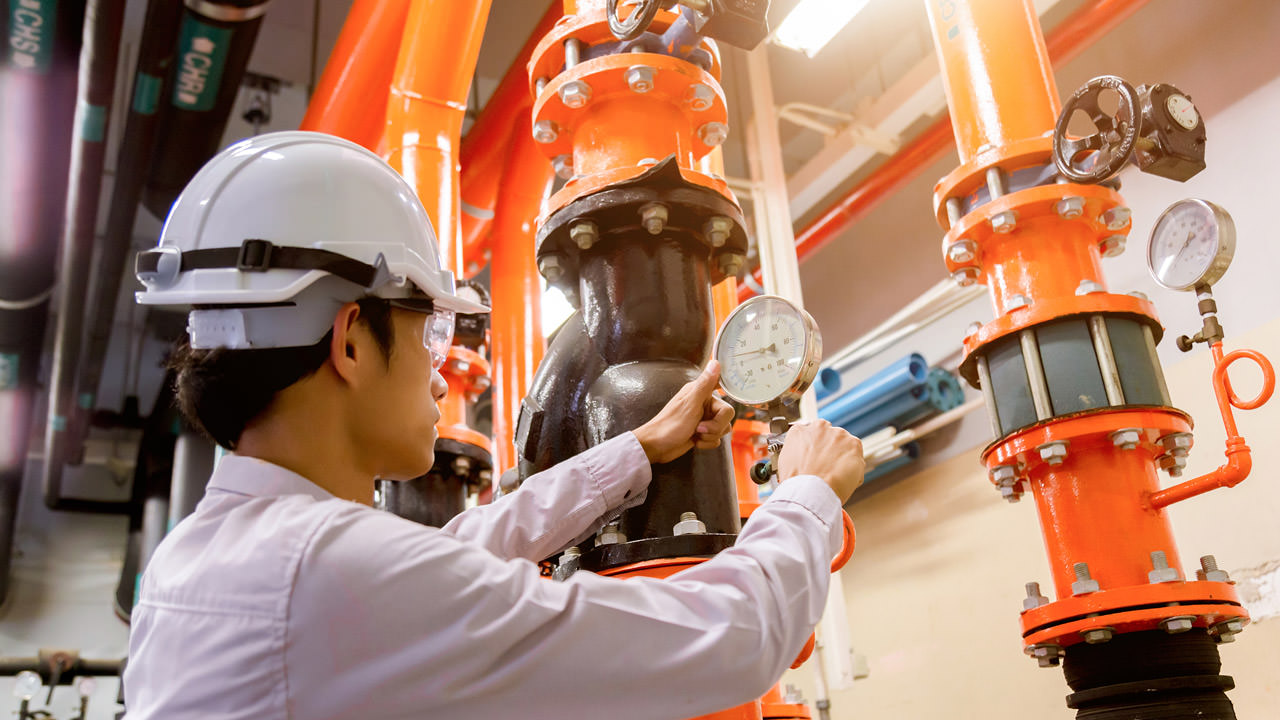
Taking process data from smart HART field devices and sharing it with higher level systems, no longer has to be difficult or expensive. Industrial Ethernet backbones and wireless networks, IIoT HART devices, open industry protocols and ease of programming provides a quick and seamless way to share process data.
Those who work in industrial process control and monitoring marvel at the newfound excitement and hype the commercial market revels in regarding IoT (Internet of Things). Sharing of data between devices and across platforms has been taking place for more than 35 years within our industry; we just referred to it as data exchange, distributed control or a host of other terms that described simple data sharing.
Nonetheless, advances are being made with open communication standards with smaller packet headers, agnostic platform requirements, exception-based reporting, minimizing network bandwidth and less expensive microprocessors that enable seamless exchange of data between all devices. And following suit, all we needed to do was to give it a new name – IIoT (Industrial Internet of Things).
However, even with advancements, the industrial and automation industry does not have the luxury of simply replacing existing instruments and control systems with new ones just because new capability or technology arises. All process facilities and their leadership are accountable for capital investment ROI, and that cannot be achieved by discarding perfectly good instruments and control systems. The ability to use existing industrial Ethernet and wireless networks in process manufacturing plants and automation facilities has made data exchange within a facility, and even throughout global corporate networks, easier than ever.
Today most process facilities have substantially invested in and utilize industrial Ethernet and wireless infrastructures to connect multitudes of devices to one another and to monitoring and control systems. These larger control systems often hold price tags of multiple millions of dollars. Additionally, each smart field instrument costs thousands of dollars each. With all of this investment in the control and monitoring system, network infrastructure and smart field instruments there are often remaining challenges with getting all of the data in one place in order to effectively perform data analytics.
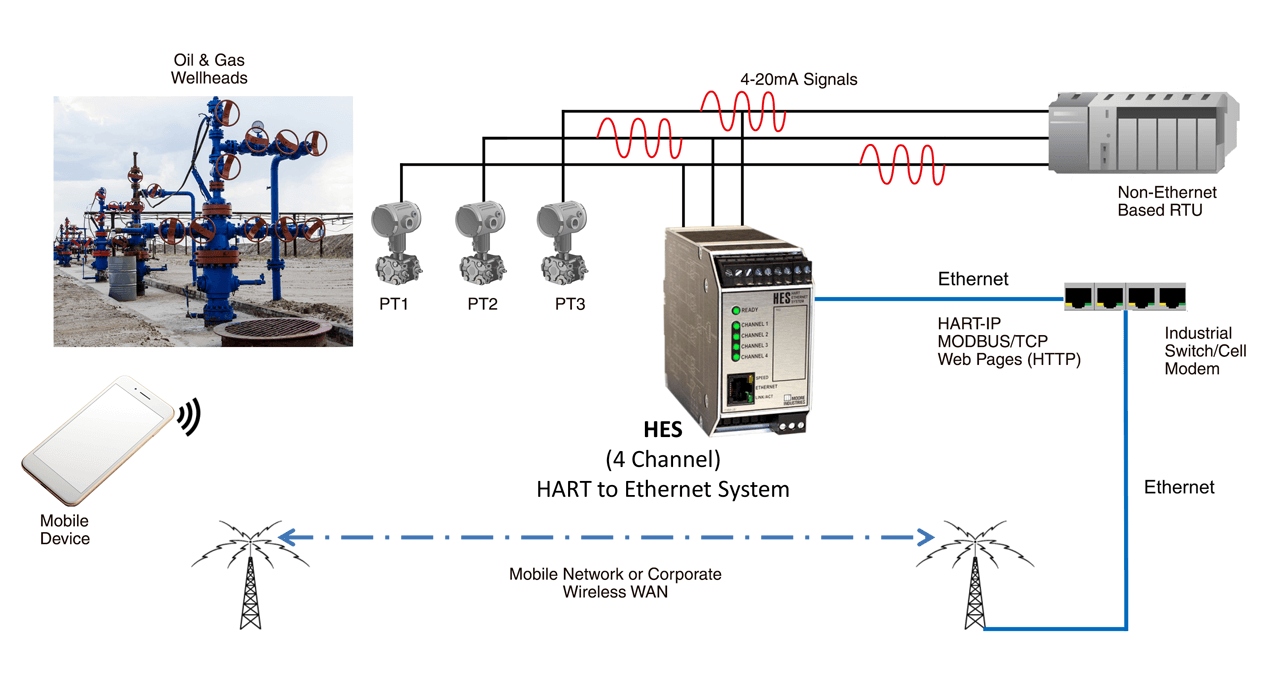
The HES gathers real time pressure and diagnostic data from insitu pressure transmitters at oil and gas wellhead and shares it via corporate wireless WAN and mobile devices.
Predictive modeling, historical analytics, process optimization and proactive preventative maintenance are just a few of the latest trends being implemented to reduce cost and improve overall performance. But in order to achieve these results, data must not only already exist but flow easily from the plant floor to higher level control, MES (Manufacturing Execution Systems) and ERP (Enterprise Resource Planning) systems.
The challenge remains for the slower adopting process industries: how do they get the benefits of what IIoT is promising without the heavy front end investment? Obviously, the answer to that question lies with exploring ways to take advantage of existing infrastructure investments.
One of the most efficient ways to capitalize on such investments is to take advantage of the digital HART data in your smart HART devices, convert it to a widely used digital communications protocol such as MODBUS/TCP, and transmit it using the existing Ethernet and wireless networks.
HART Protocol
With over 40 million installed HART devices worldwide, HART continues to get updated revisions that continually enhance data exchange capacity, speed, number of devices on a network, support over Ethernet, and wireless capability. It enables end users to have unfettered access to process and diagnostic data that can be shared with all areas of the new Smart Factory that supports IIoT endeavors. In many cases, HART instruments were installed simply because they could be configured and diagnosed easily with a HART handheld communicator (HHC). However, the HART digital signal often contains additional process measurements and other variables that may include instrument status, diagnostic data, alarms, calibration values and alert messages.
A simple and cost-effective solution for gathering HART information is to use a HART interface device. These HART interface devices make acquiring HART data a fairly simple proposition. This HART data can then be made available to the control system, asset manager or plant Ethernet backbone where it can then be shared with higher level systems or corporate WANs (Wide Area Network).
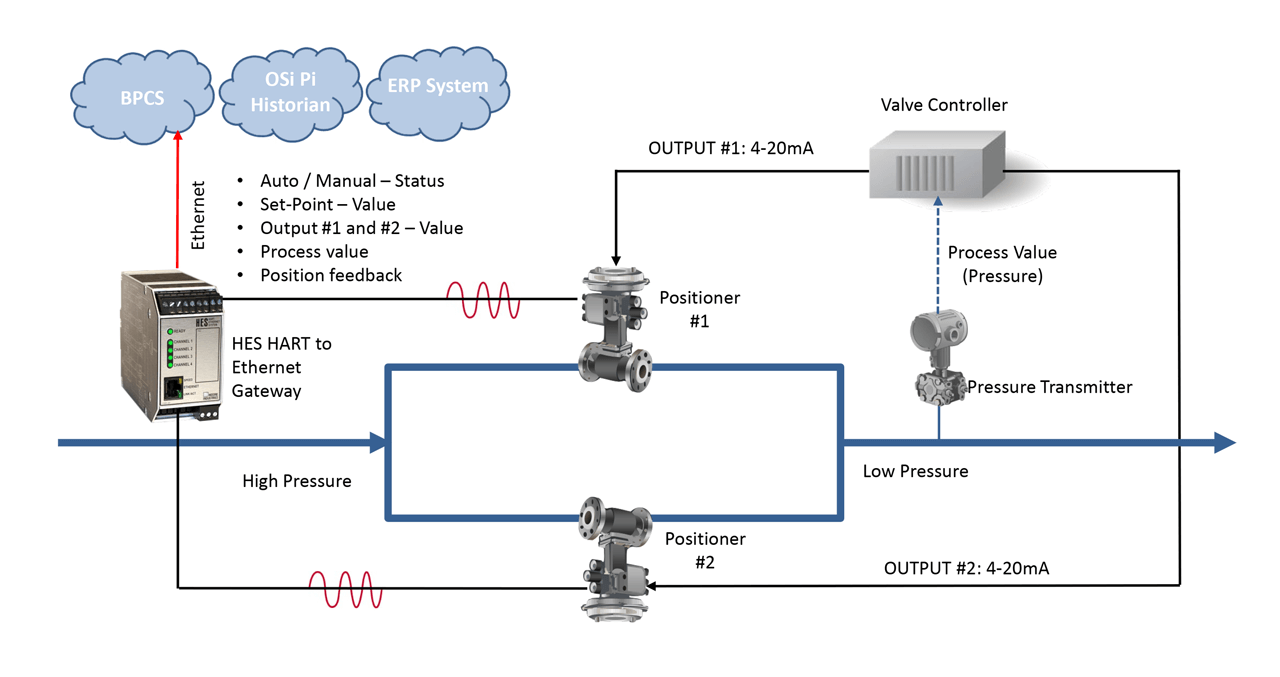
Using the HES HART to Ethernet Gateway to stream precise positioning data from electronic valve positioners.
HART Interface options
There are several ways to interface with HART smart field devices in order to acquire the digital process and diagnostic information. They vary from HART enabled 4-20mA input cards, HART multiplexer (Mux) systems, slide-in PLC gateway cards, custom coded software interfaces for asset management and MES/ERP systems and standalone gateways that typically convert the HART data to some other proprietary or open industry format.
HART multiplexers are common and typically their interface is a custom RS-422, RS- 485 or RS-232 serial connection and is custom configured for a particular vendor’s hardware interface, asset management system or control system. Each of these options is quite costly and often avoided. The most expensive but also most specific HART interface to have is one written by a programmer which can then be customized to exact user and hardware specifications.
Standalone HART gateways, such as the Moore Industries HES HART to Ethernet Gateway System, often provide the most economical pathway to extracting HART data from field devices, making the data readily available to higher level systems. These products usually offer one to four channels or ports that allow several HART devices to be multidropped for maximum data concentration
Application of HART Interfaces
These highly flexible HART gateways have been applied in multiple ways that have allowed the users to collect, convert and transmit the process and diagnostic data to systems that can perform the needed analytics while avoiding expensive system upgrades and extensive additional wiring.
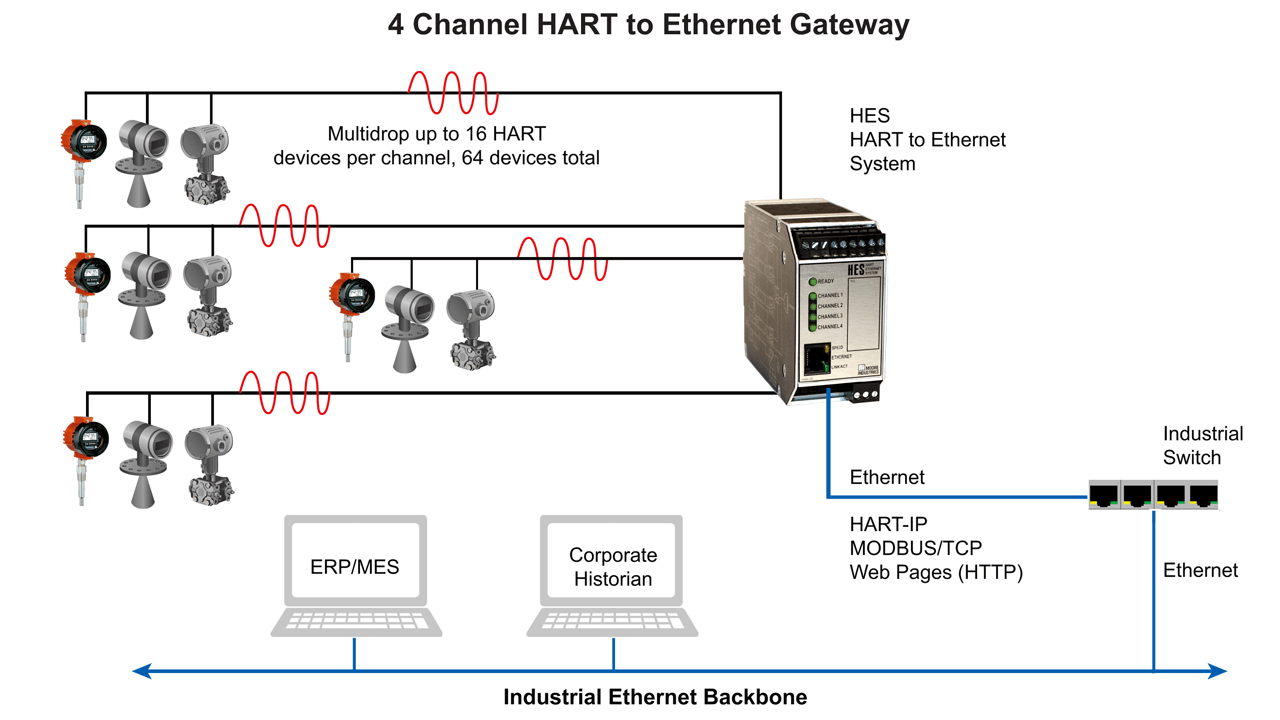
HART to Ethernet Gateways offer a quick and economical way of sharing critical HART data with higher level systems.
Stream precise positioning data
It is common for customers to upgrade the top works of their valves with smart HART positioners. However, as stated above, upgrading valve controllers or control systems to read back HART positioning and diagnostic data from these new positioners can be quite an expensive proposition. In a recent application, a customer needed to control two valves which had smart HART positioners installed and had a further requirement to communicate actual valve position over Ethernet using MODBUS/TCP to their higher-level systems.
Originally the customer wanted to use a ¼ DIN PID Controller to control the two valves in order to balance and/or limit each valve’s travel to maintain final pressure through the system, but they realized that the remote controller’s communication capability did not support MODBUS/TCP as their BPCS and Historian required.
Moreover, the higher-level monitoring systems needed to monitor and record where actual stem positions currently were, not where the valve controller was driving them via the 4-20mA signal – which was what the BPCS was currently recording. This could only be obtained by reading the HART data from the smart positioners.
The HES HART to Ethernet gateway, 4-channel model, was utilized to pick up the actual stem position HART data from the smart positioners and send it directly to the higher-level systems – no longer requiring the valve controller to communicate the CV (Controlled Variable), or desired stem position, output. The HES was an effective and economical solution that enabled the customer to take advantage of existing HART data from the positioners and share that critical data with their higher-level systems on their existing Ethernet infrastructure.
From flowmeters to Ethernet
A water treatment facility in Texas is saving the cost of an expensive host system upgrade by using a HART to Ethernet gateway to pull in totalizer values from magnetic flowmeters. Updated local and state laws required that totalized flow values at various effluent locations be historically archived and simultaneously shared with higher level municipal corporate systems.
Since the original SCADA system used for monitoring and control included PLCs that were incapable of reading HART data, expensive flowmeter upgrades were going to be required. This entailed purchasing new flowmeters with pulse output options. In addition new PLC input cards with pulse-counting capability would need to be procured; not to mention the new wire that had to be pulled for the pulse output signals.
By utilizing existing wiring, existing smart HART flowmeters and the existing PLC that had Ethernet communication capability along with the HES HART to Ethernet gateway, the municipal treatment facility saved tens of thousands of dollars. Now the local SCADA system is able to historically archive the totalized effluent flow data, along with other flow diagnostics and readings, locally and share this data over the municipal WAN (Wide Area Network) to other higher-level systems to meet reporting requirements.
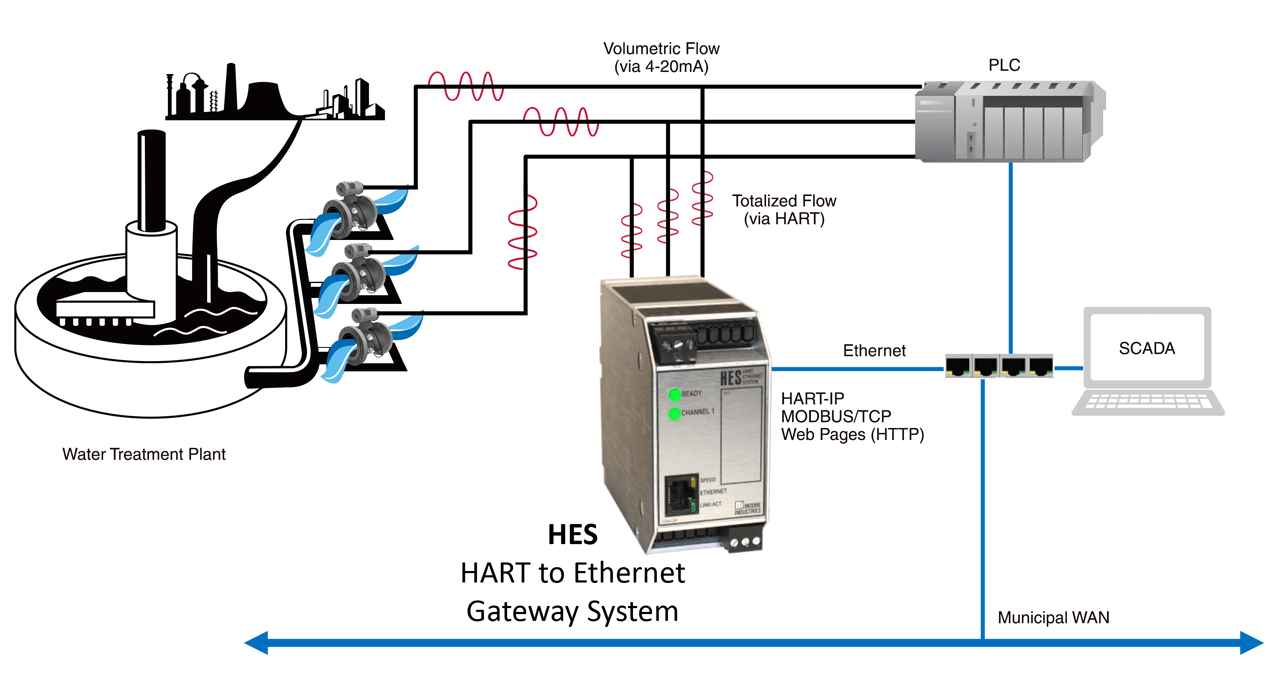
HART Totalized Flow Data converted to MODBUS/TCP and transmitted over Ethernet and a Municipal WAN.
Archive & display critical pressures
Fracking technology has presented boundless opportunities with extracting oil and gas in West Texas and other regions. However, as supplies and inventories of oil and gas increase, this obviously presents new pricing pressures within the market as the price per barrel of oil and per cubic foot of gas declines. These pricing pressures immediately evolve into the need to lower operational, maintenance and monitoring costs of upstream wells.
Since most of these wells are remote, Wireless WAN infrastructures have been put in place to cost effectively remotely control, report and monitor upstream assets. Unfortunately, many existing RTUs (Remote Terminal Units) don’t have smart HART communication capability or Ethernet capability. Upgrading these RTUs across several hundred oil and gas sites can be costly and downright time consuming.
An oil and gas company had a new requirement to locally and remotely continuously monitor wellhead pressure for production, and for safety of personnel and equipment. The HES HART to Ethernet gateway enabled a quick and cost-effective retrofit solution for all of their remote wellheads. The HES can capture direct pressure data from insitu smart HART pressure sensors and immediately make that available over Ethernet to the Wireless WAN system, which included Ethernet based modems. Moreover, this also allowed for the HES to offer direct viewing of pressure to local Ethernet based HMIs and quickly gave the company access to any other critical measurement variables from installed smart HART transmitters or valves to any remote or mobile phone monitoring apps.
Conclusion
Taking critical process data from smart HART field devices and sharing it with higher level control and information systems, whether in a manufacturing facility or between remote locations, no longer has to be difficult or expensive.
With the acceptance of industrial Ethernet backbones and wireless networks, IIoT HART interface devices, open industry protocols and ease of programming provides a quick and seamless way to share process data with the entire corporate infrastructure.